Boron Nitride(BN) Ceramics
HIgn Quality Boron Nitride(BN) Manufacturer
- Four Decades of Unwavering Dedication to Excellence
- Personalized Service to Fulfill Specific Needs
- Competitive Pricing through Direct Manufacturing
- Fast Turnaround Times and Seamless Global Delivery
Get a Quote Today
Trusted Boron Nitride(BN) Ceramic Components Manufacturer
WHy Yomua Boron Nitride(BN) Ceramics
- Precision Manufacturing Excellence: Our state-of-the-art machinery and equipment, coupled with our commitment to leveraging the latest technologies ensure every Boron Nitride(BN) Ceramics component we produce.
- Transparent Pricing: Benefit from our transparent pricing and upfront cost structures, providing you with budget certainty and peace of mind.
- Tailored Solutions: End-to-end solutions, guiding you through every stage of the manufacturing process – from initial design and prototyping to full-scale production.
- Quality Assurance: Comprised of highly skilled technicians, meticulously inspects every component at each stage of the manufacturing process.
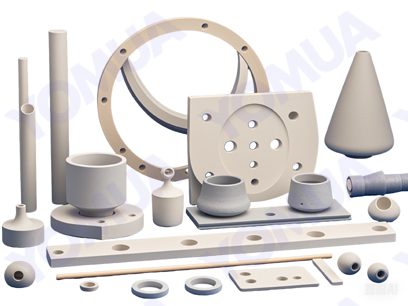
Custom Boron Nitride(BN) Ceramics Parts
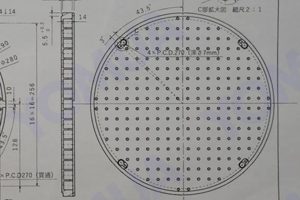
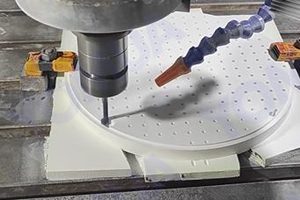
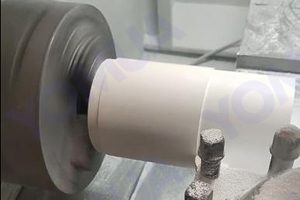
- Exceptional Customer Support:Yomua provide exceptional after-sales support, including expert technical guidance, prompt issue resolution, and ongoing assistance to maximize the performance of your BN components throughout their lifecycle.
Boron Nitride(BN) Ceramics Properties
Grade | Unit | BN-99 | BN-99.5 |
Chemical structure(BN% ) | % | 99 | 99.5 |
Other components | no | no | |
Density | g/cm3 | 1.9-2.0 | 1.55-1.65 |
Hardness | HL | 300-400 | 200.-300 |
Flexural Strength | Mpa | 35 | 33 |
Coefficient of thermal expansion(25℃-1200℃) | (10-6/K) | -1~2.5 | -1~2 |
Thermal conductivity at 20℃ | W/mk | 40 | 60 |
MAX-Temperature of use | oxidizing | 900℃ | 900℃ |
vacuum | 1800℃ | 1800℃ | |
inert | 2200℃ | 2200℃ | |
RT Resistivity | Ω.cm | >1014 | >1014 |
Note: The material property data provided is for general design guidance and may vary depending on specific product variations. For accurate and precise information pertaining to your specific application, please contact Yomua directly.
Boron Nitride(BN) Ceramics Products
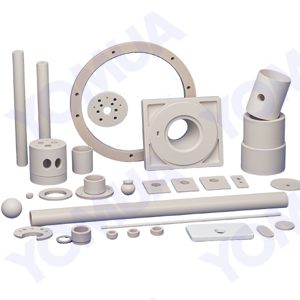
Customized Boron Nitride(BN) Ceramic Parts
Solutions manufactured for your unique needs, featuring precisely shaped components with tailored properties.

Boron Nitride(BN) Ceramic Crucible
Offer good features ,ideal for melting, casting, and processing high-temperature materials such as metals, alloys, and ceramics
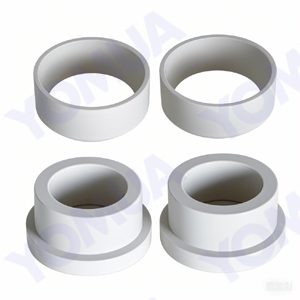
Boron Nitride(BN) Ceramic insulation sleeve
Provide excellent thermal and electrical insulation at high temperatures for protecting sensitive components.
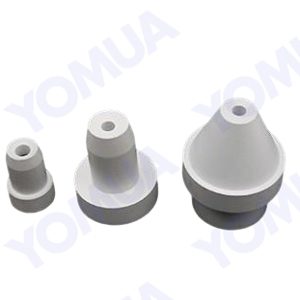
Boron Nitride(BN) Ceramic Nozzle
Boron Nitride (BN) ceramic nozzles are used in high-temperature applications like metal spraying and powder injection molding.
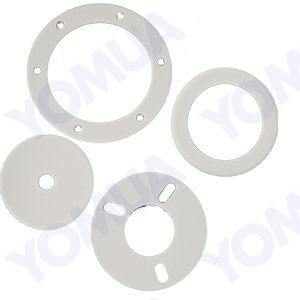
Boron Nitride(BN) Ceramic washer
Used as electrical insulators and thermal conductors in high-temperature applications. They offer excellent wear resistance and chemical stability.
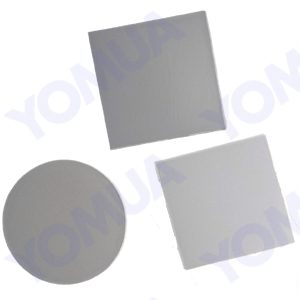
Boron Nitride(BN) Ceramic Plate
BN plates offer excellent thermal conductivity, chemical inertness, and high-temperature stability.Used in Structural components etc.,
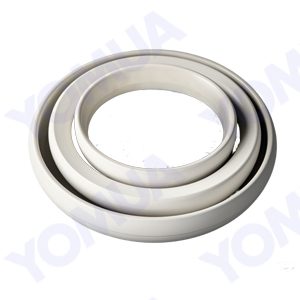
Boron Nitride(BN) Ceramic Seal Ring
Boron Nitride(BN) Ceramic Seal Ring is for excellent heat – resistance and sealing in tough conditions to prevent leakage of gases or fluids.
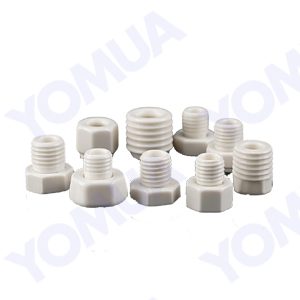
Boron Nitride(BN) Ceramic Screw Bolt Nut
Offer exceptional thermal stability, electrical insulation, and chemical resistance, ideal for high-temperature and corrosive environments.
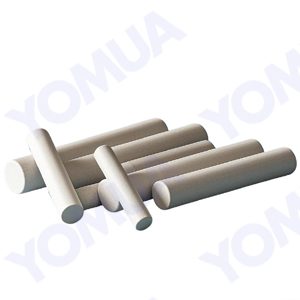
Boron Nitride(BN) Ceramic Rod
The Boron Nitride (BN) ceramic rod stands out as a highly specialized and versatile component. Its unique combination of properties makes it invaluable across multiple industries.
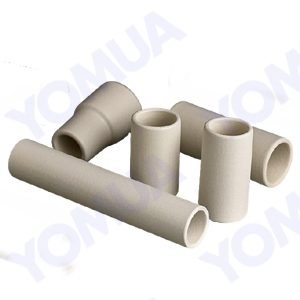
Boron Nitride(BN) Ceramic Tube
Boron Nitride ceramic tube is an essential part in many advanced industrial and scientific setups, enabling reliable operations in challenging conditions.
Customer Testimonials for Boron Nitride(BN) Ceramics ...

Yomua: Dedicated to Customer Success.



Boron Nitride(BN) Ceramics Related Products
Aluminum oxide ceramic, precision-engineered components on request.
Crystalline zirconium oxide ceramic offers outstanding resistance to crack propagation
High thermal conductivity aluminum nitride ceramic is available in any quantity.
Carborundum: High hardness, high thermal conductivity. Meets specific requests.
Si₃N₄ ceramic. Ideal for high-temperature bearings, cutting tools, and engine components.
Boron Nitride(BN) Ceramics Components Guide
Boron nitride (BN) is a refractory compound composed of boron and nitrogen. It has the chemical formula BN and exhibits remarkable thermal and chemical stability, making it suitable for various industrial applications. The compound exists in multiple crystalline forms, each with distinct properties, which allows it to be utilized in diverse fields ranging from lubricants to advanced nanotechnology.
Chemical Formula: BN
CAS Registry Number: 10043-11-5
PubChem Compound ID: 6321
SMILES Identifier: B(N)=N
Appearance: Boron nitride can appear in several forms, including hexagonal boron nitride (h-BN), which is a white powder, and cubic boron nitride (c-BN), which resembles diamond and is typically colorless or light yellow.
Density: The density of boron nitride varies depending on its allotrope. For hexagonal boron nitride, the density is approximately 2.1 g/cm³, while for cubic boron nitride, it is around 3.48 g/cm³.
Melting Point: The melting point of hexagonal boron nitride is about 2,973 °C (5,363 °F), whereas cubic boron nitride has a melting point of approximately 2,500 °C (4,532 °F).
Crystal Structure: Boron nitride exists in several crystal structures:
- Hexagonal Boron Nitride (h-BN): This structure is similar to graphite and consists of layers of hexagonally arranged boron and nitrogen atoms.
- Cubic Boron Nitride (c-BN): This structure resembles diamond and has a face-centered cubic lattice.
- Wurtzite Boron Nitride (w-BN): This structure has a hexagonal arrangement but differs from h-BN in its three-dimensional arrangement.
The different allotropes of boron nitride exhibit unique properties that make them suitable for various applications, such as lubricants, thermal insulators, and cutting tools.
- Main Types
- Hexagonal Boron Nitride (h – BN): It has a layered structure similar to graphite and is also known as “white graphite”. It has good lubricity, high temperature resistance, chemical stability and electrical insulation.
- Cubic Boron Nitride (c – BN): It has a crystal structure similar to that of diamond. Its hardness is second only to that of diamond, and it has extremely high wear resistance, thermal conductivity and chemical stability.
- Characteristics
- High Hardness: Cubic boron nitride has extremely high hardness and can be used to manufacture cutting tools, abrasives, etc., which can efficiently process hard and brittle materials.
- High Temperature Resistance: It can still maintain good stability in high temperature environment. Hexagonal boron nitride can be used at high temperatures above 1000°C for a long time, and cubic boron nitride also has excellent heat resistance and can withstand higher temperatures.
- Good Chemical Stability: It has strong tolerance to most chemical substances and is not easily corroded by chemicals such as acids and alkalis. It can be used for components in harsh environments such as the chemical and metallurgical industries.
- High Insulation: It is an excellent electrical insulating material and can be used for insulating components in electronic devices to ensure the safe operation of electronic equipment.
- High Thermal Conductivity: It has good thermal conductivity and can conduct heat quickly, which is helpful for the heat dissipation of electronic devices and improves the performance and stability of the equipment.
Boron nitride (BN) ceramics possess a unique combination of properties that make them exceptionally versatile across a wide range of industrial applications, including electronics, aerospace, metallurgy, and more. These properties can be broadly categorized as mechanical, thermal, chemical, and electrical.
Mechanical Properties:
- Extreme Hardness (c-BN): Cubic boron nitride (c-BN) is second only to diamond in hardness, making it ideal for cutting tools and abrasives used in machining hard materials.
- Excellent Lubricity (h-BN): Hexagonal boron nitride (h-BN), with its layered structure similar to graphite, provides outstanding lubrication, even in extreme temperatures and pressures. This makes it a valuable solid lubricant.
- High Strength and Toughness: Optimized BN ceramics exhibit high strength and toughness, enabling them to withstand significant mechanical stress.
Thermal Properties:
- High Thermal Stability: BN ceramics maintain their structural integrity at high temperatures. h-BN can withstand temperatures above 1000°C for extended periods, while c-BN can endure even higher temperatures.
- High Thermal Conductivity: Efficient heat dissipation is facilitated by BN’s good thermal conductivity, crucial for applications like electronics and aerospace components.
- Low Thermal Expansion: Minimal dimensional changes with temperature variations contribute to the stability and accuracy of components in thermal cycling environments.
Chemical Properties:
- Excellent Chemical Stability: BN ceramics are highly resistant to corrosion from most chemicals, including acids and alkalis, making them suitable for harsh chemical environments.
- Good Oxidation Resistance: Resistance to oxidation at high temperatures extends their lifespan in oxidizing atmospheres.
- Non-Wetting: BN’s non-wetting properties with most molten metals and glasses are crucial in applications like crucibles, preventing contamination.
Eectrical Properties:
- High Electrical Insulation: BN ceramics are excellent electrical insulators with high resistivity and dielectric strength, ensuring safe and reliable operation in electronic devices.
- High Dielectric Constant: Certain forms of BN have a high dielectric constant, useful in capacitors and high-frequency electronics.
Other Notable Properties:
- Low Density: BN’s lightweight nature is advantageous in aerospace and other weight-sensitive applications.
- Neutron Absorption: BN’s ability to absorb neutrons expands its use in nuclear applications.
- Good Machinability: BN can be easily machined into various shapes, allowing for customization.
- Excellent Thermal Shock Resistance: BN can withstand rapid temperature changes without cracking.
In summary, the unique combination of these properties makes boron nitride a highly versatile material suitable for a wide range of demanding applications.
Boron nitride (BN) exists in several crystalline forms, each with unique structures and properties, contributing to its versatility across various fields. The primary forms are summarized in the table below:
Crystalline Form | Structure | Key Properties | Applications |
---|---|---|---|
Hexagonal Boron Nitride (h-BN) | Layered (graphite-like) | High thermal stability, excellent electrical insulation, lubricity | Thermal management, electrical insulation, lubricants, cosmetics |
Cubic Boron Nitride (c-BN) | Diamond-like (sphalerite) | Extreme hardness, high thermal and chemical stability | Cutting tools, abrasives |
Wurtzite Boron Nitride (w-BN) | Lonsdaleite-like | Predicted ultra-high strength | Research, potential future applications |
Amorphous Boron Nitride (a-BN) | Non-crystalline | Properties similar to amorphous carbon | Coatings, thin films |
AAh Boron Nitride (AAh BN) | Orthorhombic (helical nanotubes) | Unique nanotube structures | Research, potential future applications in nanotechnology |
Hexagonal Boron Nitride (h-BN): The most common and stable form, h-BN has a layered structure similar to graphite. Strong covalent bonds within the layers and weak van der Waals forces between them give h-BN properties like high thermal stability and excellent electrical insulation. It’s often called “white graphene” due to its structural similarities.
Cubic Boron Nitride (c-BN): With a diamond-like (sphalerite) structure, c-BN is less stable than h-BN at room temperature but boasts superior thermal and chemical stability compared to diamond. Its extreme hardness makes it invaluable for cutting tools and abrasives.
Wurtzite Boron Nitride (w-BN): Featuring a structure similar to lonsdaleite, w-BN’s tetrahedral arrangement of boron and nitrogen atoms within 6-membered rings suggests it could be even stronger than diamond. However, its rarity limits experimental verification.
Amorphous Boron Nitride (a-BN): Unlike the crystalline forms, a-BN lacks long-range order. Its non-crystalline structure gives it properties similar to amorphous carbon.
AAh Boron Nitride (AAh BN): This recently discovered orthorhombic form exhibits unique helical structures in its derived nanotubes, further expanding our understanding of BN’s structural diversity.
These diverse crystalline structures are key to BN’s wide-ranging applications in nanotechnology, materials science, and high-temperature engineering.
BN ceramics are often engineered with specific compositions and manufacturing processes to optimize them for particular applications. Here’s a breakdown of common types:
1. Hot-Pressed Boron Nitride (HPBN)
- Manufacturing: This is a common method where BN powder is compacted under high pressure and temperature. This results in a dense, strong ceramic.
- Properties: Generally good thermal conductivity, high electrical resistivity, and excellent thermal shock resistance.
- Uses: A wide range of applications, including crucibles, insulators, heat sinks, and components in high-temperature equipment.
2. Pyrolytic Boron Nitride (PBN)
- Manufacturing: PBN is produced by chemical vapor deposition (CVD). This results in a highly pure, anisotropic material with a layered structure.
- Properties: Exceptional purity, high thermal conductivity in one direction, excellent chemical inertness, and good high-temperature performance.
- Uses: Specialized applications such as crucibles for semiconductor crystal growth, components in vacuum systems, and insulators in high-frequency electronics.
3. Composite Boron Nitride Ceramics
- Concept: These ceramics combine BN with other materials to enhance specific properties.
- Examples:
- ZSBN: A composite of BN, silicon carbide, and zirconia. This material is known for its increased hardness and wear resistance, often used in nozzles.
- BN-AlN: Combines boron nitride and aluminum nitride for high thermal conductivity and good machinability, suitable for electronics and thermal management.
- BN-BO: A composite with boron oxide, offering high thermal conductivity and excellent thermal shock resistance.
- ZSBN: A composite of BN, silicon carbide, and zirconia. This material is known for its increased hardness and wear resistance, often used in nozzles.
4. Other Types
- Reaction-Bonded Boron Nitride: Made by reacting boron oxide with nitrogen at high temperatures. This can produce complex shapes.
- Sintered Boron Nitride: Similar to HPBN but may involve different sintering aids and conditions.
Type of BN Ceramic | Manufacturing Method | Key Properties | Typical Applications |
---|---|---|---|
Hot-Pressed BN (HPBN) | Compacting BN powder under high pressure and temperature | High density, good thermal conductivity, high electrical resistivity, excellent thermal shock resistance | Crucibles, insulators, heat sinks, high-temperature components |
Pyrolytic BN (PBN) | Chemical vapor deposition (CVD) | High purity, anisotropic (high thermal conductivity in one direction), excellent chemical inertness, good high-temperature performance | Crucibles for semiconductor crystal growth, vacuum system components, high-frequency electronic insulators |
Composite BN Ceramics | Combining BN with other materials (e.g., SiC, AlN, BO) | Tailored properties depending on the composite; generally enhanced hardness, wear resistance, thermal conductivity, or other specific characteristics | ZSBN (BN/SiC/ZrO2): Nozzles; BN-AlN: Electronics, thermal management; BN-BO: High thermal conductivity, thermal shock resistance |
Reaction-Bonded BN | Reacting boron oxide with nitrogen at high temperatures | Can produce complex shapes | Specialized components |
Sintered BN | Similar to HPBN, but may involve different sintering aids and conditions | Varies depending on the specific process | General-purpose BN ceramic applications |
Boron nitride (BN) ceramics offer a compelling combination of mechanical, thermal, chemical, and electrical advantages, making them highly versatile for a wide range of applications.
Mechanical Advantages:
- Extreme Hardness (c-BN): Cubic boron nitride is exceptionally hard, second only to diamond. This makes it ideal for cutting tools and abrasives used on hard materials like hardened steels and ceramics.
- Excellent Lubricity (h-BN): The layered structure of hexagonal boron nitride provides excellent lubrication, reducing friction and wear even in high-temperature and high-pressure environments.
- High Strength and Toughness: Well-designed microstructures give BN ceramics high strength and toughness, enabling them to withstand significant mechanical stresses and impacts.
Thermal Advantages:
- Outstanding Thermal Stability: BN ceramics can withstand high temperatures without significant property degradation. h-BN can be used above 1000°C for extended periods, and c-BN even higher.
- High Thermal Conductivity: Efficient heat dissipation is facilitated by good thermal conductivity, crucial for thermal management in electronics and power systems.
- Low Thermal Expansion: Minimal dimensional changes with temperature variations ensure accuracy and stability in thermal cycling environments, important for precision instruments.
Chemical Advantages:
- Excellent Chemical Stability: BN ceramics resist corrosion from most chemicals, including strong acids and alkalis, making them suitable for harsh chemical environments.
- Good Oxidation Resistance: They maintain their integrity in oxidizing atmospheres at high temperatures, extending their lifespan in applications like furnaces.
- Non-Wetting: BN does not wet easily with molten metals and glasses, preventing contamination in crucible applications.
Electrical Advantages:
- High Electrical Insulation: BN ceramics are excellent electrical insulators with high resistivity and dielectric strength, ensuring safe operation in electronic devices and power systems.
- Tailorable Electrical Properties: Electrical properties can be adjusted through manufacturing processes and doping for specific applications like capacitors.
Other Advantages:
- Low Density: BN’s lightweight nature is advantageous in aerospace and automotive applications.
- Good Neutron Absorption: Effective neutron absorption makes BN ceramics suitable for nuclear reactors.
- High Purity: Low impurity content ensures consistent and reliable performance.
- Good Machinability: BN can be machined into complex shapes despite its hardness.
- Excellent Thermal Shock Resistance: BN can withstand rapid temperature changes without cracking.
- Low Friction Coefficient: BN’s low and stable friction coefficient makes it superior to traditional lubricants in extreme conditions.
In summary, the unique combination of these properties—high heat resistance, excellent thermal conductivity, low thermal expansion, superior electrical insulation, good corrosion resistance, low friction, high purity, and machinability—makes boron nitride ceramics a highly versatile material for a wide range of demanding industrial applications.
While boron nitride (BN) ceramics offer a remarkable range of advantages, they also present certain disadvantages that can limit their applicability in some situations.
Here’s a table summarizing the disadvantages of Boron Nitride (BN) ceramics:
Disadvantage | Description | Impact |
---|---|---|
Manufacturing Challenges | ||
High-Pressure/High-Temperature Requirements (c-BN) | Cubic BN synthesis requires extreme conditions. | Increased costs, limits large-scale production |
Strict Purity Demands | High-performance BN needs high-purity raw materials. | Complex and costly purification, difficult quality control |
Mechanical Limitations | ||
Brittleness | Low fracture toughness. | Prone to cracking under impact or stress, limits use in high-vibration environments |
Poor Thermal Shock Resistance | Susceptible to cracking from rapid temperature changes. | Restricted use in fluctuating temperature environments |
Cost Considerations | ||
High Raw Material Costs | BN raw materials are expensive. | Increased overall cost |
High Production Costs | Complex processes and specialized equipment. | Higher prices compared to other ceramics |
Property Limitations | ||
Limited Electrical Conductivity Tuning | Difficult to precisely control conductivity. | Limits use in applications needing adjustable conductivity |
Anisotropic Thermal Conductivity (h-BN) | Thermal conductivity varies by direction. | Uneven heat distribution, complex design considerations |
Hygroscopic Nature (certain grades) | Some BN grades absorb moisture. | Performance degradation if not properly handled |
Limited Wear Resistance | May not be sufficient for some abrasive applications. | Restricted use in high-wear environments |
Limited Availability of High-Purity Grades | Ultra-pure BN can be hard to find. | Limits options for applications requiring highest purity |
Manufacturing Challenges:
- High-Pressure/High-Temperature Requirements (c-BN): Producing cubic BN requires extremely high pressure and temperature, demanding specialized, expensive equipment and complex processes, which increases costs and hinders large-scale production.
- Strict Purity Demands: High-performance BN ceramics require high-purity raw materials. Purification is complex and costly, and the synthesis process is sensitive to impurities, making quality control challenging.
Mechanical Limitations:
- Brittleness: Despite good hardness and strength, BN ceramics have low fracture toughness, making them prone to cracking under impact or stress. This limits their use in applications requiring high impact and vibration resistance.
- Poor Thermal Shock Resistance: Brittleness also leads to poor thermal shock resistance. Rapid temperature changes can cause cracking, limiting use in environments with fluctuating temperatures.
Cost Considerations:
- High Raw Material Costs: BN raw materials are relatively expensive, especially the high-purity grades needed for high-performance ceramics.
- High Production Costs: The complex manufacturing processes, specialized equipment, and purification steps contribute to high production costs, making BN ceramics less cost-effective than other materials in some applications.
Property Limitations:
- Limited Electrical Conductivity Tuning: While generally excellent insulators, precisely controlling electrical conductivity within a wide range can be challenging, limiting use in applications needing adjustable conductivity.
- Anisotropic Thermal Conductivity (h-BN): Hexagonal BN’s thermal conductivity varies depending on direction, which can lead to uneven heat distribution and requires careful design considerations for thermal management.
- Hygroscopic Nature (certain grades): Some h-BN grades, especially those with B2O3 binders, absorb moisture, which can degrade performance if not properly handled.
- Limited Wear Resistance: While hard, BN ceramics may not offer sufficient wear resistance in some applications compared to materials like diamond or metal matrix composites.
- Limited Availability of High-Purity Grades: Ultra-pure BN grades can be difficult to obtain, restricting options for applications needing the highest purity.
In conclusion, while BN ceramics possess many desirable properties, their cost, brittleness, manufacturing challenges, and specific property limitations must be carefully considered when selecting materials for particular applications
Boron nitride (BN) ceramics, prized for their unique blend of physical and chemical properties, find wide application across diverse fields.
Here’s a table summarizing the applications of Boron Nitride (BN) ceramics across different industries:
Industry | Application | BN Type/Property Used | Benefit |
---|---|---|---|
Aerospace | Thermal protection tiles | High melting point, low density, high thermal conductivity | Protects spacecraft during re-entry |
Engine components (combustion chambers, turbine blades) | High-temperature stability, wear resistance | Improved engine efficiency and reliability | |
Mechanical Processing | Cutting tools | Cubic BN (c-BN) hardness | Efficient machining of hard materials |
Lubricants and wear-resistant coatings | Hexagonal BN (h-BN) lubricity | Reduced friction and wear, extended equipment life | |
Electronics & Semiconductor | Substrates for integrated circuits | Electrical insulation, high thermal conductivity, low thermal expansion | Improved device stability and heat dissipation |
Semiconductor manufacturing components (crucibles, fixtures) | Chemical stability, high-temperature resistance | Ensures quality and yield in production | |
Optical & Optoelectronic | Optical windows | Optical transparency, hardness, chemical stability | Protects optical components |
Optoelectronic devices (LEDs, laser diodes) | Material properties tailored for specific device needs | Improved device performance and efficiency | |
Nuclear | Neutron shielding | Neutron absorption | Radiation protection |
Reactor components | High-temperature resistance, chemical stability, low thermal expansion | Reliable operation in reactor environment | |
Biomedical | Biomedical implants | Biocompatibility (certain BN forms) | Potential for tissue engineering and implants |
Drug delivery carriers | Functionalizable BN materials | Improved drug efficacy and targeting | |
Other Industrial Uses | High-temperature furnace insulation | Thermal stability | Efficient insulation at high temperatures |
Vacuum system electrical insulators | Electrical insulation | Safe operation in vacuum environments | |
Microwave transparent windows | Microwave transparency | Use in telecommunications and radar | |
Sealing material in electronics | Sealing properties, electrical insulation | Protects electronic components | |
Glass melting gaskets | Non-wetting, thermal stability | Prevents contamination and aids in temperature control | |
Crystal growth crucibles | Non-wetting | Cleaner crystal growth | |
Metal casting components | Wear resistance, thermal stability | Efficient metal casting | |
High-voltage equipment feedthroughs | Electrical insulation, high-temperature resistance | Reliable operation in high-voltage applications | |
Ion implantation equipment parts | Durability, wear resistance | Reliable operation in harsh conditions | |
Electrostatic printing/laser printer components | Charge leakage barrier properties | Enhanced print quality | |
Automotive oxygen sensor seals | High-temperature resistance, chemical inertness | Improved engine efficiency and emissions control |
Aerospace & High-Temperature Applications:
- Thermal Protection: BN’s high melting point, low density, and high thermal conductivity make it ideal for thermal shielding in spacecraft re-entry, protecting internal structures from extreme heat.
- Engine Components: BN ceramics are used in manufacturing combustion chambers and turbine blades, enhancing engine efficiency and reliability due to their high-temperature stability and wear resistance.
Mechanical Processing:
- Cutting Tools: Cubic BN (c-BN), second only to diamond in hardness, is crucial for cutting tools used to machine hard materials like hardened steel and carbide alloys.
- Lubricants & Coatings: Hexagonal BN (h-BN) provides excellent lubrication, used as an additive or in wear-resistant coatings to reduce friction and extend equipment life.
Electronics & Semiconductor Industry:
- Substrates: BN’s electrical insulation, high thermal conductivity, and low thermal expansion make it suitable for integrated circuit substrates, improving device stability and reliability.
- Semiconductor Manufacturing: BN is used for crucibles, fixtures, and reaction chambers due to its chemical stability and high-temperature resistance, ensuring quality in semiconductor production.
Optical & Optoelectronic Fields:
- Optical Windows: BN’s optical transparency in certain wavelengths allows for use in optical windows, with its hardness and chemical stability protecting optical components.
- Optoelectronic Devices: BN-based materials show promise in LEDs and laser diodes, potentially improving device performance.
Nuclear Industry:
- Neutron Shielding: BN’s strong neutron absorption capability makes it valuable for shielding in nuclear applications.
- Reactor Components: High-temperature resistance, chemical stability, and low thermal expansion make BN suitable for certain reactor components.
Biomedical Field:
- Biomedical Implants: BN, particularly in nanotube form, exhibits biocompatibility, suggesting potential for implants and tissue engineering.
- Drug Delivery: Functionalized BN materials can serve as drug delivery carriers, improving drug efficacy and targeting.
Other Applications:
- High-Temperature Furnace Insulators: BN’s thermal stability makes it ideal for insulating high-temperature furnaces.
- Vacuum System Electrical Insulators: BN ensures safe operation in vacuum systems by preventing electrical discharge.
- Microwave Transparent Windows: BN’s transparency to microwaves makes it useful in telecommnications and radar.
- Sealing Material: BN protects sensitive electronic components from environmental factors.
- Glass Melting Gaskets: BN gaskets aid in temperature control and prevent contamination in glass melting.
- Crystal Growth Crucibles: BN’s non-wetting properties are ideal for crucibles in crystal growth.
- Metal Casting Components: BN is used in continuous casting machines.
- High-Voltage Equipment Feedthroughs: BN’s insulation and high-temperature resistance make it suitable for high-voltage equipment.
- Ion Implantation Parts: BN provides durability and wear resistance in ion implantation equipment
- Electrostatic Printing/Laser Printers: BN serves as a charge leakage barrier in printing drums.
- Automotive Oxygen Sensor Seals: BN-based seals enhance engine efficiency and emissions control in automobiles.
This diverse range of applications underscores the versatility of boron nitride ceramics across a wide spectrum of industries.
Silicon nitride (Si₃N₄) and boron nitride (BN) ceramics, while both offering valuable properties, differ significantly in their composition, structure, and resulting characteristics, leading to distinct applications.
Composition and Structure:
- Silicon Nitride: Composed of silicon and nitrogen, forming a strong covalent bond network structure. Exists primarily in α and β crystalline forms.
- Boron Nitride: Composed of boron and nitrogen. Exists in several forms, including hexagonal (h-BN), with a layered structure similar to graphite, and cubic (c-BN), with a diamond-like structure.
Physical Properties:
Property | Silicon Nitride (Si₃N₄) | Boron Nitride (BN) |
---|---|---|
Hardness | High (15-30 GPa Vickers) | h-BN: Relatively low; c-BN: Extremely high (>50 GPa Vickers, second only to diamond) |
Thermal Conductivity | Good (20-30 W/m·K) | h-BN: Excellent, anisotropic (up to 300 W/m·K); c-BN: High |
Density | ~3.2 g/cm³ | h-BN: ~2.27 g/cm³; c-BN: ~3.48 g/cm³ |
Chemical Properties:
- Silicon Nitride: Good chemical stability, resistant to many acids and alkalis, but can react with strong oxidizing agents at high temperatures. Forms a protective silica layer at high temperatures in air.
- Boron Nitride: Excellent chemical stability, inert to most chemicals, withstands harsh environments. h-BN stable in air up to ~1000°C; c-BN even higher. h-BN can be oxidized at higher temperatures.
Applications:
Silicon Nitride:
- Mechanical Engineering: Engine components, bearings, cutting tools (due to high strength and wear resistance).
- Electronics: Substrates, packaging (good electrical insulation and thermal conductivity).
- Mechanical Engineering: Engine components, bearings, cutting tools (due to high strength and wear resistance).
Boron Nitride:
- High-Temperature Applications: Thermal insulation, crucibles.
- Semiconductor Industry: c-BN for cutting/grinding/polishing; h-BN as a lubricant and release agent.
- Aerospace: Thermal protection, engine parts.
- Other: Lubricants, electrical insulators, etc.
- High-Temperature Applications: Thermal insulation, crucibles.
Key Differences Summarized:
- Strength and Hardness: Silicon nitride excels in mechanical strength and hardness (except c-BN).
- Thermal Properties: Boron nitride, especially h-BN, offers superior thermal conductivity and thermal shock resistance.
- Electrical Properties: Boron nitride is a superior electrical insulator.
- Chemical Resistance: Boron nitride exhibits generally better chemical inertness
- Applications: Silicon nitride is favored for high-stress mechanical parts, while boron nitride is preferred for thermal management, high-temperature applications, and chemically harsh environments.
Here’s a table summarizing the key differences between Silicon Nitride (Si₃N₄) and Boron Nitride (BN) ceramics:
Property | Silicon Nitride (Si₃N₄) | Boron Nitride (BN) |
---|---|---|
Composition | Silicon and Nitrogen | Boron and Nitrogen |
Structure | Covalent network | Layered (h-BN), Diamond-like (c-BN) |
Hardness | High (15-30 GPa) | h-BN: Relatively low; c-BN: Extremely high (>50 GPa) |
Thermal Conductivity | Good (20-30 W/m·K) | h-BN: Excellent, anisotropic (up to 300 W/m·K); c-BN: High |
Thermal Shock Resistance | Good, but less than h-BN | Excellent (h-BN) |
Electrical Insulation | Good | Excellent |
Chemical Stability | Good, but reacts with some strong oxidizers | Excellent, inert to most chemicals |
Density | ~3.2 g/cm³ | h-BN: ~2.27 g/cm³; c-BN: ~3.48 g/cm³ |
Primary Applications | Mechanical parts (bearings, cutting tools), Electronic substrates | Thermal management, High-temperature applications (crucibles), Semiconductors, Lubricants |
Boron nitride (BN), with its unique properties, can often replace other materials in various industrial applications. Here are some key examples:
1. Replacing Graphite:
- High-Temperature Crucibles: While graphite crucibles are common, BN offers superior chemical stability and corrosion resistance, especially when working with reactive metals like titanium and zirconium. BN crucibles minimize contamination and provide a more stable environment.
- Lubricants and Release Agents: Hexagonal BN (h-BN) excels as a lubricant and release agent, often surpassing graphite’s performance. Its lubricity reduces wear and improves processing efficiency, particularly in precision part molding where BN ensures better release and product quality.
2. Replacing Diamond:
- Cutting and Grinding Tools: Cubic BN (c-BN), nearly as hard as diamond, offers a cost-effective alternative for cutting and grinding hard, brittle materials. It’s particularly useful for machining hardened steel, providing high cutting efficiency and a long tool life.
- High-Pressure/High-Temperature Environments: While diamond is used in HPHT applications, c-BN can serve as a replacement in some cases. Its similar stability under pressure and temperature offers an alternative where diamond may be less practical or cost-prohibitive.
3. Replacing Alumina Ceramics:
- Electronic Substrate Materials: Although alumina is widely used, BN offers better thermal conductivity and a lower thermal expansion coefficient. This makes BN preferable for high-performance electronics where heat dissipation and thermal stability are critical, such as in high-power ICs and microwave devices.
- High-Temperature Insulation: BN’s high melting point and excellent thermal insulation properties make it a superior alternative to alumina in some high-temperature insulation applications, such as within furnaces and thermal processing equipment.
4. Replacing Tungsten Carbide:
- Wear-Resistant Parts: Cubic BN’s hardness and wear resistance make it a viable replacement for tungsten carbide in certain wear-resistant parts, such as abrasive spraying nozzles where c-BN extends nozzle lifespan.
- Metal Forming Tools: BN-based materials can be used in some metal forming applications. For example, h-BN coatings or lubricants on tungsten carbide tools reduce friction and improve metal forming quality.
Key Considerations When Choosing a Replacement:
- Specific Application Needs: The best material choice hinges on the specific application requirements, including temperature, chemical environment, mechanical stress, and cost.
- Performance Trade-offs: Switching materials may involve trade-offs in performance. Each material has its strengths and weaknesses.
- Cost-Effectiveness: Material and processing costs are crucial factors in material selection.
Here’s a table summarizing the materials that Boron Nitride (BN) can replace in various applications:
Application | Material Replaced by BN | Reason for Replacement | Advantages of BN |
---|---|---|---|
High-Temperature Crucibles | Graphite | Chemical instability of graphite with some metals | Better chemical stability, corrosion resistance with reactive metals |
Lubricants & Release Agents | Graphite | Lower lubricity in some applications | Superior lubricity, especially in precision molding |
Cutting & Grinding Tools | Diamond (in some cases) | Cost of diamond | Cost-effective alternative for certain applications |
High-Pressure/High-Temperature Applications | Diamond (in some cases) | Cost and availability of diamond | Comparable stability in some HPHT uses |
Electronic Substrates | Alumina | Lower thermal conductivity, higher thermal expansion of alumina | Better thermal conductivity, lower thermal expansion for high-performance electronics |
High-Temperature Insulation | Alumina | Lower melting point, lower thermal insulation in some cases | Higher melting point, superior thermal insulation |
Wear-Resistant Parts | Tungsten Carbide (in some cases) | Lower wear resistance in specific applications | Superior wear resistance in certain uses |
Metal Forming Tools | Tungsten Carbide (coatings/lubricants) | Higher friction in some metal forming processes | Reduced friction, improved metal forming quality (as a coating/lubricant) |
Careful evaluation of potential replacements and consultation with materials experts are essential for choosing the most suitable material for a given application.
Boron nitride (BN) ceramics are produced through several specialized manufacturing processes, each designed to optimize the material’s unique properties. Here’s a breakdown of the key methods:
1. Powder Synthesis:
- Chemical Vapor Deposition (CVD): Gaseous boron and nitrogen precursors react at high temperatures in a reactor, forming high-purity BN powder. CVD allows for precise control over the process, resulting in tailored powder characteristics.
- Solid-State Reaction: Boron and nitrogen compounds are mixed and reacted under controlled conditions to produce BN powder.
2. Forming Techniques (after powder synthesis):
- Hot Pressing: BN powder is compacted under high temperature and pressure, creating dense shapes with excellent mechanical properties.
- Hot Isostatic Pressing (HIP): Similar to hot pressing, but with uniform pressure applied from all directions, resulting in even higher density and reduced porosity.
- Spark Plasma Sintering (SPS): Pulsed electric current rapidly heats and densifies the BN powder, minimizing grain growth and improving mechanical properties.
3. Manufacturing Methods (combining synthesis and forming):
Hot Pressing (Detailed):
- Raw Material Preparation: High-purity BN powder (often from CVD or solid-state reaction) is selected and sieved.
- Molding: The powder is placed in a graphite or other suitable mold.
- Hot Pressing: High temperature (1600-2200°C) and pressure (20-50 MPa) are applied, sintering and densifying the powder.
- Post-Processing: Machining, grinding, and polishing are used to achieve final dimensions and surface finish.
Chemical Vapor Deposition (CVD) (Detailed):
- Substrate Preparation: A substrate (e.g., silicon wafer, metal surface) is cleaned and prepared.
- Gas Introduction: Gaseous reactants (e.g., BCl₃ and NH₃) are introduced into a reaction chamber.
- Deposition Reaction: At high temperatures (800-1200°C), the gases react, and BN deposits onto the substrate, forming a film or coating. (BCl₃ + 3NH₃ → BN + 3HCl)
- Thickness Control: The thickness of the BN layer is controlled by adjusting process parameters.
Spark Plasma Sintering (SPS) (Detailed):
- Powder Preparation: High-purity BN powder is prepared.
- Loading: The powder is placed in a graphite die within the SPS apparatus.
- Sintering: Pulsed electric current and pressure are applied simultaneously, rapidly heating and densifying the powder.
- Cooling and Ejection: The sintered ceramic is cooled and removed from the die.
Reaction Sintering:
- Raw Material Mixing: Boron powder and nitrogen-containing substances are mixed.
- Pre-Molding: The mixture is shaped into a “green body.”
- Reaction Sintering: The green body is heated in a nitrogen atmosphere, causing boron to react with nitrogen and form BN, densifying the material.
- Post-Treatment: Further processing (heat treatment, machining) may be required.
4. Post-Processing and Quality Control:
All methods may involve post-processing steps like machining and surface finishing. Rigorous quality control measures are implemented throughout the entire manufacturing process to ensure the final BN ceramic meets required specifications.
Here’s a table summarizing the Boron Nitride (BN) ceramic manufacturing methods:
Method | Raw Materials | Process | Key Features | Advantages | Disadvantages |
---|---|---|---|---|---|
Powder Synthesis | |||||
Chemical Vapor Deposition (CVD) | Gaseous boron & nitrogen precursors (e.g., BCl₃, NH₃) | High-temperature reaction in a reactor | Precise control over process parameters | High purity BN powder, tailored properties | Complex, can be expensive |
Solid-State Reaction | Boron & nitrogen compounds | Controlled reaction at high temperatures | Simpler than CVD | Can be less expensive | Powder purity may be lower |
Forming Techniques | BN Powder (from above) | ||||
Hot Pressing (HP) | BN powder | Compaction under high temperature & pressure | High density | Good mechanical properties | Can be expensive |
Hot Isostatic Pressing (HIP) | BN powder | Compaction under uniform pressure at high temperature | Very high density, reduced porosity | Excellent mechanical properties | More expensive than HP |
Spark Plasma Sintering (SPS) | BN powder | Pulsed electric current and pressure | Rapid heating & densification | Improved mechanical properties, minimal grain growth | Specialized equipment |
Combined Methods | |||||
Hot Pressing (Detailed) | BN powder | See detailed description | High density | Good mechanical properties, widely used | Can be expensive |
Chemical Vapor Deposition (CVD) (Detailed) | Gaseous precursors | See detailed description | High purity BN films/coatings | Precise control, specialized applications | Complex, expensive |
Spark Plasma Sintering (SPS) (Detailed) | BN Powder | See detailed description | Rapid sintering | Improved mechanical properties | Specialized equipment, cost |
Reaction Sintering | Boron powder, nitrogen source | Reaction at high temperature | Simpler, can produce complex shapes | Cost-effective for some applications | Lower density, may require post-treatment |
Pyrolytic boron nitride (PBN), also known as pyrolytic BN, is a high-purity ceramic material made of boron and nitrogen. It’s created through chemical vapor deposition (CVD), a process where boron halides and ammonia are pyrolyzed at high temperatures. This CVD process allows for exceptionally high purity levels, often exceeding 99.999%.
Structure:
PBN’s structure is hexagonal and layered, similar to graphite, earning it the nickname “white graphite.” Boron and nitrogen atoms alternate in layers, with a closer spacing within the layers (1.45 Angstroms) than between them (3.33 Angstroms). This layered structure leads to anisotropic thermal conductivity (different thermal properties in different directions).
Key Properties:
- Ultra-High Purity: Typically greater than 99.999%, making it ideal for sensitive applications.
- Excellent Chemical Resistance: Inert to most acids, alkalis, and salts at room temperature. It can be slightly corroded by strong bases and oxidizes above 1273 K.
- High Thermal Stability & Shock Resistance: Withstands rapid temperature changes without cracking.
- Excellent Electrical Insulation: High dielectric strength (56 kV/mm at room temperature).
- Good Mechanical Strength: Tensile strength up to 153.84 N/mm² and an elastic modulus of approximately 235690 N/mm².
Applications:
PBN’s unique combination of properties makes it valuable in various industries:
- Semiconductor Manufacturing: Crucibles for growing compound semiconductors (GaAs, InP).
- Aerospace & Aviation: Components requiring high-temperature stability and chemical inertness.
- Electronics: Electrical insulators in electronic devices.
In short, PBN is a highly specialized and versatile material prized for its exceptional purity, layered structure, thermal stability, and electrical insulation capabilities.
Boron carbide (B₄C) and boron nitride (BN) are both boron-containing compounds, but they differ significantly in their composition, structure, properties, and applications.
1. Composition and Structure:
- Boron Carbide (B₄C): Composed of boron and carbon atoms in a complex, three-dimensional network of B₁₂ icosahedra linked by C-B-C chains.
- Boron Nitride (BN): Composed of boron and nitrogen atoms. Exists in various forms, including hexagonal BN (h-BN), which has a layered, graphite-like structure, and cubic BN (c-BN), which has a diamond-like structure.
2. Physical Properties:
Property | Boron Carbide (B₄C) | Boron Nitride (BN) |
---|---|---|
Hardness | Extremely high (Mohs ~9.3) | h-BN: Relatively soft; c-BN: Extremely high (second to diamond) |
Color | Typically gray-black | h-BN: White or colorless; c-BN: Colorless or light yellow |
Thermal Properties | High melting point (2350°C), good thermal stability | High-temperature resistance (up to 2800°C in inert atmosphere), high thermal conductivity (h-BN) |
Density | ~2.5 g/cm³ | h-BN: ~2.27 g/cm³; c-BN: ~3.48 g/cm³ |
3. Chemical Properties:
- Boron Carbide: Resistant to corrosion by hydrofluoric and nitric acids at high temperatures; insoluble in water and acids, soluble in molten alkalis.
- Boron Nitride: Highly chemically inert, resistant to many chemicals, not easily wetted by molten substances.
4. Neutron Absorption:
- Boron Carbide: Excellent neutron absorber, widely used in nuclear applications.
- Boron Nitride: Relatively weak neutron absorption.
5. Manufacturing Process:
- Boron Carbide: Usually produced by reducing boron trioxide with carbon in an electric furnace.
- Boron Nitride: h-BN synthesized by reacting borax with ammonium chloride or urea; c-BN from h-BN under high temperature and pressure with a catalyst.
6. Applications:
- Boron Carbide:
- Abrasives and cutting tools
- Armor (due to its hardness and neutron absorption)
- Nuclear reactor control rods
- Abrasives and cutting tools
- Boron Nitride:
- h-BN: Lubricants, high-temperature coatings, electrical insulators
- c-BN: Cutting tools, abrasives (for extremely hard materials)
- Semiconductor industry (crucibles, insulators)
- Aerospace (thermal management)
- h-BN: Lubricants, high-temperature coatings, electrical insulators
In summary: Boron carbide is known for its extreme hardness and neutron absorption, making it suitable for cutting tools, armor, and nuclear applications. Boron nitride, in its various forms, excels in thermal management, electrical insulation, and high-temperature lubrication, serving critical roles in electronics, aerospace, and other advanced industries.
Pricing for boron nitride (BN) ceramic parts is highly variable due to several key factors:
- BN Type: Hexagonal BN (h-BN) is generally the most affordable, followed by cubic BN (c-BN). Wurtzite BN (w-BN) is the rarest and thus, likely the most expensive.
- Purity: Higher purity BN requires more complex purification processes, significantly increasing the cost.
- Manufacturing Process: Advanced manufacturing techniques like hot isostatic pressing (HIP) or chemical vapor deposition (CVD) often result in higher prices compared to simpler methods like hot pressing.
- Part Complexity & Size: Custom-designed and complex shapes, as well as larger parts, will be more expensive due to increased design, tooling, and manufacturing costs.
- Order Volume: Bulk orders typically qualify for discounts, reducing the per-unit price.
General Price Indications (These are rough estimates and should not be used for purchasing decisions):
h-BN Powder:
- Low Purity (lubricants, coatings): $20-$80/kg
- Medium Purity (general industrial use): $80-$200/kg
- High Purity (electronics, specialized uses): $200-$500+/kg
Hot-Pressed BN Parts:
- Simple Shapes (discs, washers): $5-$50/piece
- Complex Shapes (crucibles, insulators): $50-$500+/piece
- Larger Parts (tiles, tubes): $100-$1000+/kg
c-BN Abrasives/Cutting Tools:
- Grinding Wheels: $50-$500+/wheel (size, grit, bond dependent)
- Cutting Inserts: $10-$100+/insert
- c-BN Powder (specialized applications): $200-$1000+/kg
Key Considerations:
- These prices are estimates only. Actual prices will vary significantly depending on the specific supplier, order volume, and product requirements.
- Custom parts always incur a premium due to design, tooling, and specialized manufacturing.
- High-purity BN is considerably more expensive due to the added purification steps.
- Market fluctuations in raw material availability and demand can influence pricing.
To get an accurate quote, be prepared to provide the following information to Yomua,you can send email [email protected] directly:
- Type of BN: (e.g., hexagonal BN (h-BN), cubic BN (c-BN), or a specific grade)
- Purity level: (e.g., percentage of BN content)
- Desired properties: (e.g., thermal conductivity, electrical resistivity, density, etc.)
- Form and dimensions: (e.g., powder, solid part with specific dimensions and tolerances, thin film, etc.)
- Quantity: (how much material you need)
- Application: (what you intend to use the BN ceramic for)
- Customization: (if you need a custom-designed part, provide drawings or detailed specifications)
Be Clear and Specific:
- The more details you provide, the more accurate the quote will be.
- If you have any specific requirements or preferences (e.g., manufacturing process, surface finish, packaging), be sure to mention them.
When it comes to ordering custom-made boron nitride (BN) ceramic components, the lead time for Yomua can vary significantly based on several factors. The typical lead time for these components is generally around 3 to 15 days for standard orders by Yomua. However, this timeframe can extend considerably depending on specific requirements such as the complexity of the design, the size of the order, and the current workload of the manufacturing facility.
For custom orders that require specialized tooling or unique specifications, lead times may increase. In cases where new die press or injection molding tooling is necessary, preparation for these tools alone can take 1 to2 months before production of the actual parts begins. Therefore, if you are in a prototype phase where testing and adjustments are needed, it is not uncommon for a ceramic project to stretch out to 2 to 6 months before receiving production quantities.
In summary, while standard lead times for custom-made BN ceramic components can be as short as 3 days , more complex orders requiring additional tooling or modifications may result in much longer timelines.
Yes, technical support is readily available for boron nitride (BN) ceramics. Yomua recognize the complexity of working with this material and offer a range of services to assist customers. Here’s a breakdown:
Understanding BN Ceramics:
BN ceramics are valued for their unique combination of properties: high thermal conductivity, excellent electrical insulation, and high-temperature resistance. This makes them applicable across diverse industries like semiconductor processing, aerospace, and high-temperature insulation.
Types of Technical Support Offered:
- Consultations: Experts work with clients to understand their project requirements and discuss how BN ceramics can best be utilized.
- Material Selection: Given the various types of BN ceramics (e.g., hexagonal, cubic, composites), guidance is provided to choose the optimal material for the specific application.
- Processing Advice: Support may include recommendations on appropriate processing techniques (hot pressing, spark plasma sintering, etc.) to achieve desired material properties and performance.
- Application Development: Experts can assist in developing tailored applications that leverage BN’s unique characteristics for specific industry needs. 1
- Troubleshooting & Problem Solving: Technical support teams are available to help resolve any issues that may arise during the use or implementation of BN ceramics. They can draw on their experience to suggest solutions and help users overcome challenges.
In short: Whether you’re exploring the use of BN ceramics for the first time or are an experienced user, technical support is available from Yomua to help you succeed.Yomua can provide valuable expertise and guidance throughout the entire process, from material selection to application development and troubleshooting.
Yomua does not have a stock of Boron Nitride BN ceramics.Yomua operate on a made-to-order basis or require specific requests for production.
Production Time and Stock Availability: The production time for Boron Nitride ceramics generally depends on various factors such as materials, production methods, tolerances, and quantity. If stock material is available, the typical production time ranges from 3 to 20 days. However, if the required materials are not in stock, it may take longer, approximately 30 to 40 days.
Custom Orders: It is also noted that most orders for Boron Nitride products are custom-made. This indicates that while there may be standard offerings or stock items available, many clients opt for tailored solutions based on specific requirements.
Free Samples and Trial Orders: The company offers free samples if they have them in stock and if the cost is manageable. This suggests that there might be some level of inventory for evaluation purposes.