Alumina Ceramic Components
By Yomua:Top Manufacturer
- 40+ Years Manufacturing Alumina Ceramic Components!
- Top Quality Alumina Powder Material .
- Rigorous Quality Control System Management.
- Understanding and Meet Customers’need .
- Own Factory have Competitive Price.
Get a Quote Today
Alumina Al2O3 Ceramic Components Manufacturing Leader
Why Yomua Alumina Al2O3 Ceramic Components
Precision Engineered, Customer-Centric Solutions
For over four decades, we’ve been at the forefront of alumina part manufacturing. Our commitment to quality and customer satisfaction has earned us a reputation as a trusted partner for businesses worldwide.
Unmatched Quality and Precision
- Premium Materials: We source only the highest quality alumina powder materials to ensure optimal performance and durability.
- State-of-the-Art Technology: Our advanced manufacturing processes allow us to achieve maximum surface accuracy, up to RA0.01μm.
- Rigorous Quality Control: Our stringent quality control system guarantees that every part meets or exceeds industry standards.
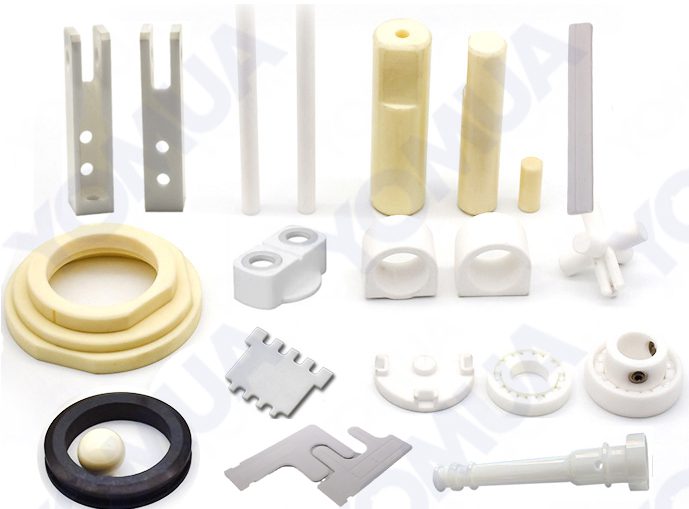
Custom Manufacturing Alumina Ceramics
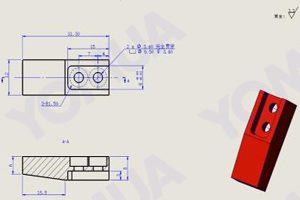
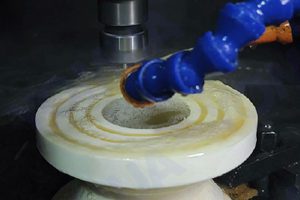
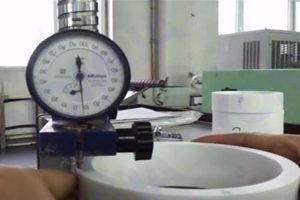
Alimina Aluminum Oxide Properties
Properties | Units | 99.99% Al₂O₃ | 99.7% Al₂O₃ | 99.5% Al₂O₃ | 99% Al₂O₃ | 97% Al₂O₃ | 95% Al₂O₃ |
---|---|---|---|---|---|---|---|
Color | – | White | Ivory | Ivory | Ivory | White | White |
Permeability | – | Gas-tight | Gas-tight | Gas-tight | Gas-tight | Gas-tight | Gas-tight |
Density | g/cm³ | 3.95 | 3.94 | 3.9 | 3.8 | 3.75 | 3.7 |
Straightness | % | 1 | 1 | 1 | 1 | 1 | 1 |
Hardness | Mohs Scale | 9 | 9 | 9 | 9 | 8.9 | 8.8 |
Water Absorption | % | ≤0.2 | ≤0.2 | ≤0.2 | ≤0.2 | ≤0.2 | ≤0.2 |
Bending Strength (Typical 20°C) | MPa | 375 | 375 | 370 | 340 | 320 | 304 |
Compressive Strength (Typical 20°C) | MPa | 2300 | 2300 | 2300 | 2210 | 2100 | 1910 |
Max Working Temperature | °C | 1750 | 1750 | 1750 | 1700 | 1650 | 1500 |
Coefficient of Thermal Expansion (25°C to 800°C) | 10⁻⁶/°C | 8 | 7.8 | 7.8 | 7.7 | 7.6 | 7.5 |
Fracture Toughness | MPa•m¹/² | 4.4 | 4.3 | 4.3 | 4.2 | 4 | 3.8 |
Dielectric Strength (5mm Thickness) | AC-kV/mm | 9 | 8.7 | 8.7 | 8.7 | 8.5 | 8.3 |
Dielectric Loss (25°C @ 1MHz) | – | <0.0001 | <0.0001 | <0.0001 | 0.0001 | 0.0002 | 0.0002 |
Dielectric Constant (25°C @ 1MHz) | – | 9.8 | 9.7 | 9.7 | 9.5 | 9.3 | 9.2 |
Electrical Resistivity (25°C) | Ω•mm²/m | >10¹⁴ | >10¹⁴ | >10¹⁴ | >10¹⁴ | >10¹⁴ | >10¹⁴ |
Thermal Conductivity (25°C) | W/m•K | 30 | 30 | 30 | 29 | 27.5 | 25 |
Note: The data presented in this table is intended for general design guidance and may not reflect the exact properties of specific products. Actual properties may vary depending on factors such as composition, processing techniques, and specific applications. For precise information, please consult with the material supplier or refer to relevant technical documentation.
Trusted Alumina Al2O3 Ceramic Components Partner
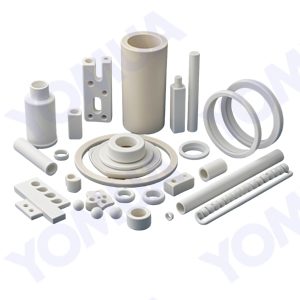
Customized Alumina Ceramics Parts
Alumina ceramic parts based on customers’ needs including shape, size, performance, etc ., No MOQ required, Competitive price, fast delivery……
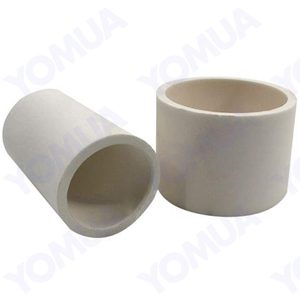
Alumina Crucible
High purity (alumina exceeds 95%), high temperature resistance (≤1800℃), chemical resistance, resistance to rapid cold and heat, etc.
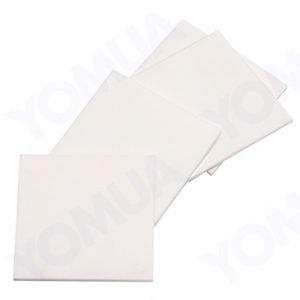
Alumina Substrate
Alumina ceramic substrates play an important role in the fields of electronic packaging, circuit substrates, power electronic devices and sensors.
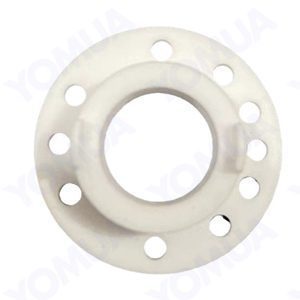
Alumina Flange
Ceramic flanges are superior to metal flanges in many aspects, especially in wear resistance, high temperature resistance and corrosion resistance.
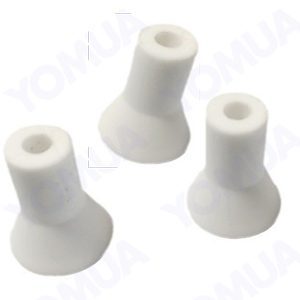
Alumina Nozzle
Used in flue gas desulfurization, dust removal, flow cleaning, fire extinguishing spraying, dust removal and cooling, waste gas washing, defoaming, etc.
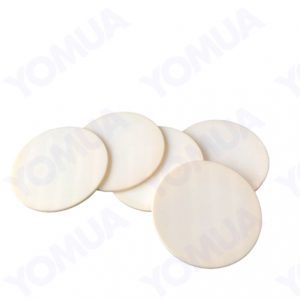
Alumina Plate
Good electrical insulation, chemical resistance, corrosion resistance,wear resistance, heat resistance and thermal conductivity etc., Used in many industries.
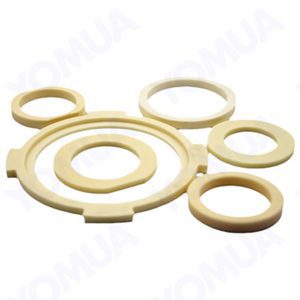
Alumina Ring
High Al2O3 materials, widely used in electronics, machinery, chemical industry and other fields such as seal rings,insulators,heating furnace components .
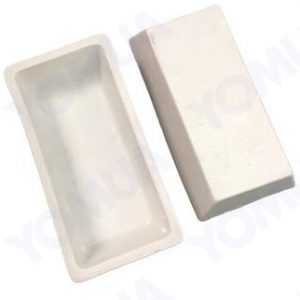
Alumina boat
High temperature, excellent refractoriness, high purity and corrosion resistance.Used in
electronics industry, heat treatment,metal smelting industry etc.,
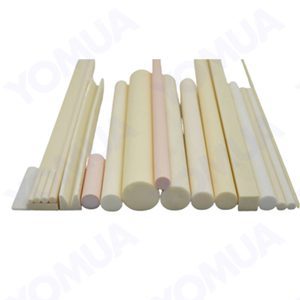
Alumina Rod
Known as alumina bar,used in industrial precision ceramic parts, electronic and other fields, such as knife sharpeners, ceramic plungers, industrial shaft rods etc.,
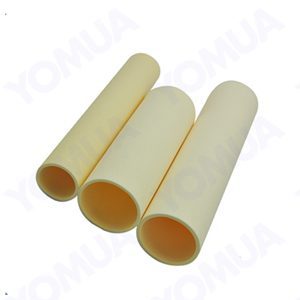
Alumina Tube
See What Our Customers Has To Say about Alumina Ceramic....

99.9% Satisfaction Made Yomua Strong



Alumina Ceramics Related Products
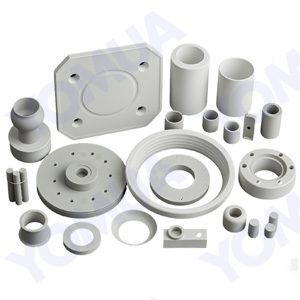
Yomua Boron Nitride(BN) Ceramics
with excellent heat – resistance and insulation.
Alumina Ceramic Components FAQ Guide
This FAQ guide has explored the multifaceted world of alumina ceramics, offering insights into their properties, applications, and manufacturing processes. By understanding the unique characteristics of alumina, such as its exceptional strength, thermal stability, and electrical insulation, you can harness its potential to create innovative and high-performance solutions.
Frequently Asked Questions
What is Alumina or Aluminium Oxide or Al2O3 ?
Alumina, also known as aluminium oxide (Al2O3), is a widely used compound formed by aluminum and oxygen. It’s not an amorphous powder, but rather a crystalline solid that can exist in different crystal structures.
Key characteristics of alumina include:
- High hardness: This makes it a valuable abrasive material for grinding and polishing.
- High melting point (2054°C) and boiling point (2980°C): This allows it to withstand extreme temperatures, making it useful in refractory applications like furnace linings.
- Chemical stability: Alumina is resistant to many chemicals, making it versatile in various industrial settings.
While alumina isn’t typically considered an “ionized crystal,” it can exhibit some ionic character due to the attraction between positively charged aluminum ions and negatively charged oxide ions.
Here’s a breakdown of the information:
- Atomic crystal: This description isn’t quite accurate. Alumina has a crystalline structure, but not all crystals are atomic crystals.
- Ionized crystal at high temperatures: This needs clarification. While the bond between aluminum and oxygen has some ionic character, it’s not a purely ionic bond. Additionally, alumina doesn’t become fully ionized at high temperatures.
What is Alumina Ceramic or Aluminium Oxide Ceramic?
Alumina ceramic is a widely used ceramic material primarily composed of aluminum oxide (Al2O3).
It is a highly durable industrial ceramic renowned for its exceptional hardness. It’s derived from bauxite, a clay-like material rich in aluminum.It’s a popular choice among oxide ceramics due to its versatility and favorable balance of properties, including high strength, excellent thermal shock resistance, and good electrical insulation.
Key Features of Alumina Ceramic:
- Exceptional Hardness: Alumina is renowned for its extreme hardness, making it ideal for applications requiring superior wear resistance.
- High Thermal Conductivity: It efficiently conducts heat, enabling effective heat dissipation in demanding thermal environments.
- Excellent Electrical Insulation: Alumina serves as an excellent electrical insulator, with its insulating properties improving with increasing purity.
- Superior Corrosion Resistance: It exhibits remarkable resistance to chemical corrosion, particularly against strong acids and alkalis, even at elevated temperatures.
- High Melting Point: Alumina boasts a very high melting point of approximately 2050 degrees Celsius, allowing it to withstand extreme heat.
- Thermal Shock Resistance: While alumina can tolerate significant temperature fluctuations, its thermal shock resistance can be compromised at extremely high temperatures due to variations in thermal expansion coefficients.
What are the Characteristics of Alumina Ceramic ?
Alumina ceramics, primarily composed of aluminum oxide (Al2O3), offer a unique blend of properties that make them suitable for a wide range of applications:
Physical Properties:
- High Hardness: Alumina ceramics are known for their exceptional hardness, making them highly resistant to wear and abrasion.
- Light Weight: Despite their strength, alumina ceramics are relatively lightweight, reducing the weight of components and improving efficiency.
- Excellent Wear Resistance: They exhibit superior wear resistance, significantly extending the lifespan of components in harsh environments.
- Good Thermal Conductivity: Alumina ceramics efficiently conduct heat, enabling effective heat dissipation.
- High Temperature Resistance: They can withstand high temperatures without significant degradation in their properties.
- Electrical Insulation: Alumina ceramics are excellent electrical insulators, making them ideal for electrical components.
- Chemical Resistance: They are resistant to a wide range of chemicals, including acids and alkalis.
- Biocompatibility: Alumina ceramics are biocompatible, making them suitable for medical and dental applications.
Mechanical Properties:
- High Strength: Alumina ceramics possess high mechanical strength, allowing them to withstand significant loads.
- Good Thermal Shock Resistance: They can tolerate rapid temperature changes without fracturing.
Property | Description |
---|---|
Hardness | Exceptionally hard, resistant to wear and abrasion |
Weight | Relatively lightweight, improving efficiency |
Wear Resistance | Superior wear resistance, extending component lifespan |
Thermal Conductivity | Efficient heat conduction, enabling effective heat dissipation |
Temperature Resistance | High temperature tolerance, maintaining properties at high temperatures |
Electrical Insulation | Excellent electrical insulator, ideal for electrical components |
Chemical Resistance | Resistant to a wide range of chemicals, including acids and alkalis |
Biocompatibility | Safe for medical and dental applications |
Mechanical Strength | High strength, capable of withstanding significant loads |
Thermal Shock Resistance | Tolerant to rapid temperature changes, reducing risk of fracture |
Are Alumina Ceramics Suitable for Strong Magnetic Field Environments?
Alumina ceramic is an insulating material characterized by its very low magnetic permeability, which is significantly lower than that of metallic materials like steel. In the presence of strong magnetic fields, alumina ceramics do not exhibit notable magnetic effects as metals do; therefore, they are minimally influenced by magnetic fields. This property allows alumina ceramics to maintain stability even in environments with intense magnetic fields, making them resistant to interference or damage caused by such fields.
Key Characteristics:
- Low Magnetic Permeability: Alumina exhibits negligible magnetic susceptibility, making it highly resistant to magnetic forces. Unlike metals, it does not experience significant magnetic effects, ensuring its stability in intense magnetic environments.
- Excellent Insulation: As an exceptional electrical insulator, alumina maintains its insulating properties even in the presence of strong magnetic fields, preventing electrical short circuits and ensuring safe operation.
- High Hardness and Wear Resistance: Alumina’s inherent hardness and durability make it highly resistant to wear and tear, extending its lifespan in demanding magnetic field applications.
Applications in Strong Magnetic Fields:
- Electronic Components: Alumina’s stability and insulating properties make it ideal for various electronic components, including substrates for integrated circuits, capacitors, and resistors.
- Magnetic Materials: While not magnetic itself, alumina serves as a stable substrate for the deposition of magnetic thin films, enabling the development of advanced magnetic devices.
- Scientific Research: Alumina’s inert nature and resistance to magnetic interference make it a valuable material for scientific research, particularly in experiments involving strong magnetic fields.
By leveraging these properties, alumina ceramics provide a reliable and efficient solution for a wide range of applications in strong magnetic field environments.
What are the Crystalline Structures of Alumina and Their Applications?
The crystalline form of alumina has various forms such as α, γ, η, δ, θ, κ, χ, etc.Their density, specific surface area, porosity, and acidity vary due to different dehydration conditions, and initial alumina hydroxide. The crystalline form will be transformed when the external conditions change.Except for α phase which is thermodynamically stable, all other sub-stable transition crystalline phases will be transformed into α phase with the increase of temperature, for example, γ alumina can be transformed into α alumina after calcination, while significant volume contraction occurs (γ alumina density is 3.65 g/cm3, α alumina density is 3.99 g/cm3).
Alumina exists in various crystalline forms, including α, γ, η, δ, θ, κ, and χ. Each of these phases exhibits distinct properties such as density, specific surface area, porosity, and acidity. These variations arise from different dehydration conditions and the initial form of alumina hydroxide used in their formation.
The transformation between these crystalline forms is influenced by external conditions. Notably, while the α phase is thermodynamically stable at elevated temperatures, all other sub-stable transition phases will eventually convert to α alumina when subjected to increased temperature. For instance, γ alumina can undergo a transformation into α alumina upon calcination. This process is accompanied by a significant volume contraction; specifically, the density of γ alumina is approximately 3.65 g/cm³, whereas that of α alumina is about 3.99 g/cm³.

Key Alumina Phases and Their Properties:
1.α-Al₂O₃ (Alpha Alumina):
Alpha Alumina (α-Al₂O₃), also known as corundum, is the most stable phase of aluminum oxide. It features a tripartite crystal structure and exhibits several remarkable properties that make it highly valuable in various industrial applications.
Property | Description |
---|---|
Melting Point | Approximately 2054 °C (3729 °F), suitable for high-temperature applications. |
Hardness | Ranks 9 on the Mohs scale, making it one of the hardest known substances. |
Wear Resistance | Excellent wear resistance due to its hardness and structural integrity. |
Mechanical Strength | Significant mechanical strength allows it to withstand substantial stress. |
Electrical Insulation | Effective electrical insulator, useful in electronic applications. |
Corrosion Resistance | Strong resistance to chemical corrosion enhances durability in harsh environments. |
Applications
Given these properties, alpha-Al2O3 serves as an ideal raw material for manufacturing:
- Ceramics: Widely used in the production of pure aluminum ceramics due to its stability and mechanical properties.
- Abrasives: Preferred choice for abrasives used in grinding and cutting tools because of its hardness.
- Refractory Materials: Utilized in refractory materials that can withstand extreme temperatures without degrading.
In summary, alpha-Al2O3 stands out as a versatile material with exceptional properties that support its use across various industries, particularly in ceramics, abrasives, and refractory applications.
2. β-Al2O3:
Beta alumina(β-Al2O3) is not classified as an isomer of alumina; rather, it is categorized as an aluminate. The general chemical formula for β-Al2O3 can be expressed as M2O·xAl2O3, where M represents a monovalent cation. This structure allows for the potential substitution of M with divalent or trivalent cations, providing versatility in its applications.
Crystal Structure and Physical Properties:β-Al2O3 crystallizes in a hexagonal crystal system. It exhibits several notable physical properties:
Property | Value |
---|---|
Density | ~3.5 g/cm³ |
Porosity | Low (typically < 5%) |
Mechanical Strength | High (compressive strength > 200 MPa) |
Thermal Impact Resistance | Excellent (up to 1000°C) |
Ionic Conductivity | ~10^-4 S/cm at room temperature |
Particle Size Distribution | Uniform and fine |
Grain Boundary Resistance | Low |
- High Density: This characteristic contributes to its structural integrity.
- Low Porosity: Low porosity enhances its durability and resistance to environmental factors.
- High Mechanical Strength: This makes β-Al2O3 suitable for demanding applications where structural stability is crucial.
- Good Thermal Impact Resistance: It can withstand rapid temperature changes without significant degradation.
- High Ionic Conductivity: This property is particularly important for its role in electrochemical applications.
- Uniform and Fine Particle Size Distribution: This feature aids in achieving consistent performance across various uses.
- Low Resistance to Grain Boundaries: This characteristic facilitates ionic movement, enhancing its conductivity.
Applications of β-Al2O3
Due to its unique properties, β-Al2O3 finds application in several fields:
- Solid Electrolyte Film in Sodium-Sulfur (Na/S) Batteries: In this context, it serves dual functions as both an ion conductor and a separator that isolates the sodium cathode from the sodium anode. This role is critical for maintaining battery efficiency and safety.
- Room Temperature Batteries: Its ionic conductivity makes it suitable for use in batteries that operate at ambient temperatures.
- Sodium Thermal Components: The material’s thermal stability allows it to be used effectively in components that experience high temperatures.
- Raw Materials for Glass Production: Its chemical properties make it a valuable ingredient in glass manufacturing processes.
- Refractory Materials and Ceramics: The high mechanical strength and thermal resistance of β-Al2O3 make it ideal for use in refractory applications where materials must withstand extreme conditions.
In summary, β-Al2O3 is a versatile aluminate with significant industrial relevance due to its exceptional physical properties and broad range of applications.
3. γ-Al2O3:
Gamma alumina is a crystalline form of aluminum oxide (Al₂O₃) produced by calcining soft alumina monohydrate at relatively low temperatures (500-750°C). It possesses a cubic crystal structure, high porosity, and a large specific surface area. These properties endow it with excellent adsorption and catalytic capabilities.
Key Properties:
- Cubic crystal structure
- High porosity
- Large specific surface area
- Strong adsorption capacity
- High catalytic activity
Property | Value |
---|---|
Crystal Structure | Cubic |
Color | White |
Density | 3.65 g/cm³ |
Melting Point | 2072 °C |
Specific Surface Area | High |
Porosity | High |
Adsorption Capacity | High |
Catalytic Activity | High |
Applications:
Due to its unique properties, gamma alumina finds applications across various industries:
- Catalysis:
- Catalyst support for numerous reactions, including refining and hydrogenation processes in the petrochemical industry.
- Adsorption and Desiccation:
- Effective adsorbent for removing impurities and moisture from gases and liquids.
- Widely used as a desiccant in industrial processes.
- Materials Science:
- Raw material for producing advanced materials like ceramics, refractories, and abrasives.
- Used in the manufacturing of aerospace components, electronic devices, and military hardware.
- Chemical Mechanical Polishing (CMP):
- Nano-sized gamma alumina particles are employed in CMP slurries to polish the surfaces of semiconductor wafers, optical lenses, and other precision components.
Gamma alumina’s versatility and excellent performance make it a valuable material in a wide range of applications.
4. δ-Al2O3
Delta alumina is a crystalline form of aluminum oxide (Al₂O₃) produced by calcining soft alumina monohydrate at temperatures between 800 and 1050°C. This thermal treatment process transforms the monohydrate into a more stable, crystalline structure.
Key Properties:
- Tetragonal crystal structure
- Strong adsorption capacity
- High catalytic activity
Property | Value |
---|---|
Crystal Structure | Tetragonal |
Color | White |
Density | 3.65 g/cm³ |
Melting Point | 2072 °C |
Specific Surface Area | High |
Porosity | High |
Adsorption Capacity | High |
Catalytic Activity | High |
Applications:
Due to its unique properties, delta alumina finds applications in various industries:
- Adsorbent: It can absorb and retain various molecules, making it useful for gas purification, water treatment, and other separation processes.
- Desiccant: It can effectively remove moisture from gases and liquids, making it suitable for drying applications.
- Catalyst: It can accelerate chemical reactions without being consumed, finding applications in various catalytic processes.
- Catalyst Support: It can provide a stable support for active catalytic components, enhancing their performance and durability.
Delta alumina’s versatility and excellent performance make it a valuable material in a wide range of industrial applications.
5. η-Al2O3
Eta alumina (η-Al2O3) is a crystalline form of aluminum oxide (Al₂O₃) produced by calcining aluminum hydroxide derived from the Bayer process. This transformation occurs at temperatures between 400 and 750°C, with a specific heating rate influencing the final product’s properties.
Key Properties:
- Cubic crystal structure
- High pore capacity
- High specific surface area
Property | Value |
---|---|
Crystal Structure | Cubic |
Color | White |
Density | 3.65 g/cm³ |
Melting Point | 2072 °C |
Specific Surface Area | High |
Porosity | High |
Applications:
- Catalyst Support: Due to its high surface area and porosity, η-Al₂O₃ is widely used as a catalyst support in various chemical reactions. It provides a stable platform for active catalytic components, enhancing their performance and durability.
Eta alumina’s specific properties make it a valuable material in the field of catalysis, contributing to the efficiency and effectiveness of numerous industrial processes.
6. θ-Al2O3
Theta alumina(θ-Al2O3) is a crystalline form of aluminum oxide (Al₂O₃) that forms during the calcination of aluminum hydroxide (Al(OH)₃) at specific temperatures and heating rates. It is a transitional phase between the less stable gamma alumina (γ-Al₂O₃) and the more stable alpha alumina (α-Al₂O₃).
Formation Process
- Starting Material: The process begins with aluminum hydroxide, which is derived from bauxite ore through the Bayer process.
- Calcination: The aluminum hydroxide is heated to high temperatures, typically between 900°C and 1100°C. This thermal treatment process is known as calcination.
- Phase Transition: During calcination, aluminum hydroxide undergoes dehydration and transforms into various alumina phases. At lower temperatures (around 500-800°C), gamma alumina (γ-Al₂O₃) may form. As the temperature increases, the structure transforms into theta alumina.
Crystalline Structure and Properties
- Crystal System: Theta alumina crystallizes in a monoclinic system.
- Intermediate Properties: Its properties lie between gamma and alpha alumina:
- Moderate surface area: Lower than gamma alumina but higher than alpha alumina.
- Moderate thermal stability: Higher than gamma alumina but lower than alpha alumina.
Property | Value |
---|---|
Crystal Structure | Monoclinic |
Thermal Stability | Intermediate (between γ-Al₂O₃ and α-Al₂O₃) |
Surface Area | Moderate |
Porosity | Moderate |
Applications | Catalyst supports, refractory materials, ceramics |
Applications
Due to its unique properties, theta alumina is used in various applications:
- Catalyst Supports: It provides a stable platform for catalysts, enhancing their performance.
- Refractory Materials: It is used in high-temperature applications due to its thermal stability.
- Ceramics: It is used in the production of ceramics with specific properties.
Coexistence with Other Phases
Often, theta alumina coexists with gamma and alpha alumina during synthesis processes. This coexistence can influence the overall properties of the material:
- Thermal Stability: The presence of alpha alumina can improve the overall thermal stability of the material.
- Catalytic Activity: The presence of gamma alumina can enhance the catalytic activity due to its higher surface area.
In conclusion, theta alumina is a valuable intermediate phase in the production of various alumina-based materials, offering a balance of properties between gamma and alpha alumina.
7. κ-Al2O3
Kappa alumina(κ-Al2O3) is a crystalline form of aluminum oxide (Al₂O₃) produced by calcining alumina trihydrate (Al(OH)₃) at temperatures between 800°C and 1150°C.
Formation Process
- Starting Material: Alumina trihydrate (Al(OH)₃) is the starting material, commonly derived from bauxite ore.
- Calcination: The alumina trihydrate is heated to high temperatures in a controlled process known as calcination.
- Dehydration: As the temperature increases, water molecules are removed from the alumina trihydrate.
- Phase Transformation: Between 800°C and 1000°C, the structure transforms from gamma alumina (γ-Al₂O₃) to kappa alumina (κ-Al₂O₃).
- Cooling: After reaching the desired temperature, the material is cooled down, influencing the final properties of the κ-Al₂O₃.
Crystal Structure and Properties
- Hexagonal Crystal Structure: Kappa alumina exhibits a hexagonal crystal structure, which contributes to its unique properties.
- High Thermal Stability: The hexagonal structure provides high thermal stability, making it suitable for high-temperature applications.
- Mechanical Strength: The specific arrangement of atoms in the crystal lattice contributes to its mechanical strength.
Property | Value |
---|---|
Crystal Structure | Hexagonal |
Thermal Stability | High |
Mechanical Strength | High |
Applications | Refractory bonding agent, purifying agent, adsorbent, catalyst support, electrical insulator |
Applications
Due to its unique properties, kappa alumina finds applications in various industries:
- Refractory Bonding Agent: Its high melting point and thermal stability make it suitable for bonding refractory materials.
- Purifying Agent: It can be used to purify gases and liquids by adsorbing impurities.
- Adsorbent: Its porous structure makes it an effective adsorbent for various substances.
- Catalyst Support: It can be used as a support material for catalysts, providing a stable platform for catalytic reactions.
- Electrical Insulator: Its electrical insulating properties make it useful in electronic components.
In conclusion, kappa alumina is a valuable material with applications in diverse fields, including metallurgy, ceramics, and catalysis. Its unique properties, derived from its specific crystal structure and formation process, make it a crucial component in many industrial processes.
8. ρ-Al2O3
Rho alumina(ρ-Al2O3) is a form of aluminum oxide (Al₂O₃) characterized by its poorly crystalline, almost amorphous structure. It is produced by dehydrating alumina trihydrate (Al₂O₃·3H₂O) under specific conditions, such as low pressure and controlled temperature.
Production Process
- Starting Material: Alumina trihydrate is the starting material.
- Dehydration: The alumina trihydrate is dehydrated under vacuum conditions at low pressure (below 2.66 Pa).
- Amorphous Structure Formation: The specific conditions of dehydration lead to the formation of a poorly crystalline, almost amorphous structure.
Properties and Applications
- Amorphous Structure: This unique structure contributes to its high surface area and reactivity.
- High Surface Area: The high surface area makes it an excellent adsorbent and catalyst support.
- Thermal Stability: While not as thermally stable as alpha alumina, it still exhibits good thermal resistance.
Property Value Crystal Structure Poorly crystalline, almost amorphous Thermal Stability Moderate Surface Area High Porosity High Applications Refractory materials, ceramic coatings, catalyst supports, adsorbents, electronics, environmental technology, cosmetics
Applications:
- Refractory Materials: Used in high-temperature applications like steelmaking and glass production.
- Ceramic Coatings: Used to enhance the durability and corrosion resistance of ceramic materials.
- Catalyst Supports: Used as a support for catalysts in various chemical processes.
- Adsorbents: Used to adsorb impurities from gases and liquids.
- Other Applications: Used in electronics, environmental technology, and cosmetics.
Rho alumina’s unique properties and versatility make it a valuable material in various industries.
9. χ-Al2O3
Chi alumina(χ-Al2O3) is a specific form of aluminum oxide (Al₂O₃) produced by calcining alumina trihydrate (Al₂O₃·3H₂O) at temperatures between 500°C and 750°C in a protective gas atmosphere.
Production Process
- Starting Material: Alumina trihydrate with a particle size less than 75 micrometers is used as the starting material.
- Calcination: The alumina trihydrate is heated to temperatures between 500°C and 750°C in a protective gas atmosphere to prevent oxidation and contamination.
- Phase Transformation: During calcination, the alumina trihydrate undergoes dehydration and phase transformation to form chi alumina.
Property Value Crystal Structure Poorly defined, often amorphous Thermal Stability Moderate Surface Area High Porosity High Applications Drying agent, desiccant, water purification, catalyst support, air separation and oxygen production
Properties and Applications
- High Surface Area and Porosity: Chi alumina has a high surface area and porosity, making it an excellent adsorbent and desiccant.
- Applications:
- Drying and Dehydration: Used to dry air, natural gas, and petroleum cracking gas.
- Water Purification: Used to remove fluoride ions from drinking water.
- Catalysis: Used as a catalyst support and in the production of hydrogen peroxide.
- Dechlorination: Used to dechlorinate viscous resins.
- Air Separation and Oxygen Production: Used in air separation processes to produce oxygen.
Chi alumina’s unique properties and versatility make it a valuable material in various industrial applications.
All Crystalline Structures of Alumina Crystal Structure ,Key Properties and Applications:
Polymorph | Crystal Structure | Key Properties | Applications |
---|---|---|---|
α-Al₂O₃ | Triangular | Thermodynamically stable, high melting point, high hardness, excellent wear resistance, high mechanical strength, good electrical insulation, high corrosion resistance | Refractory materials, abrasives, ceramics, catalyst supports |
β-Al₂O₃ | Hexagonal | High density, low porosity, high mechanical strength, good thermal shock resistance, high ionic conductivity | Solid electrolytes in sodium-sulfur batteries, ceramic spacers, room temperature batteries, sodium thermal components, glass and ceramic raw materials |
γ-Al₂O₃ | Cubic | High surface area, high porosity, high adsorption capacity, high catalytic activity | Catalyst supports, desiccants, adsorbents, water purification, chemical mechanical polishing (CMP) slurries |
δ-Al₂O₃ | Tetragonal | High adsorption capacity, high catalytic activity | Catalyst supports, desiccants, adsorbents |
η-Al₂O₃ | Cubic | High surface area, high porosity | Catalyst supports |
θ-Al₂O₃ | Monoclinic | Intermediate properties between γ-Al₂O₃ and α-Al₂O₃ | Catalyst supports, refractory materials |
κ-Al₂O₃ | Hexagonal | High thermal stability, good mechanical strength, moderate surface area and porosity | Refractory bonding agents, purifying agents, adsorbents |
ρ-Al₂O₃ | Poorly crystalline, almost amorphous | High surface area, high porosity, good adsorbent properties | Refractory materials, ceramic coatings, catalyst supports, adsorbents |
χ-Al₂O₃ | Poorly crystalline, often derived from γ-Al₂O₃ | High surface area, high porosity, good adsorbent and desiccant properties, often used as a catalyst support or in gas purification processes | Desiccants, dehydrating agents, water purification, catalyst supports, air separation and oxygen production |
What are the Types of Alumina Ceramics?
Based on Purity
High-Purity Alumina Ceramics:
- Al2O3 content > 99.9%
- High-temperature applications (e.g., crucibles, furnace tubes)
- Optical applications (e.g., sodium lamps, laser materials)
- Electronic applications (e.g., integrated circuit substrates, high-frequency insulators)
Ordinary Alumina Ceramics:
- Al2O3 content ranges from 85% to 99%
- Various applications, including:
- Wear-resistant parts (e.g., bearings, seals)
- Corrosion-resistant parts
- Electrical insulators
- Refractory materials
Based on Crystalline Phase
Corundum Ceramics:
- Primarily composed of α-Al2O3
- High strength, hardness, and thermal shock resistance
- Used in high-temperature, high-stress environments
Corundum-Mullite Ceramics:
- Combination of α-Al2O3 and mullite (3Al2O3·2SiO2)
- Good thermal shock resistance and creep resistance
- Used in high-temperature applications requiring thermal stability
Mullite Ceramics:
- Primarily composed of mullite
- Excellent thermal shock resistance and creep resistance
- Used in high-temperature environments, especially those involving thermal cycling
Based on Porosity
Dense Alumina Ceramics:
- Low porosity, high strength, and good mechanical properties
- Used in structural components and wear-resistant parts
Porous Alumina Ceramics:
- High porosity, good permeability, and high surface area
- Used as filters, catalyst supports, and biomaterials
Based on Molding Process
Pressure Casting:
- High-precision parts with complex shapes
- Used in electronic components and precision engineering
Slip Casting:
- Large, complex shapes with good dimensional accuracy
- Used in sanitary ware, tableware, and technical ceramics
Injection Molding:
- Mass production of complex shapes with fine details
- Used in electronic components, automotive parts, and medical devices
Tape Casting:
- Production of thin, flat ceramic sheets
- Used in electronic substrates, capacitors, and sensors
Classification | Description | Applications |
Based on Purity | ||
High-Purity Alumina | Al2O3 content > 99.9% | High-temperature applications, optical components, electronics |
Ordinary Alumina | Al2O3 content 85-99% | Wear-resistant parts, corrosion-resistant parts, electrical insulators, refractories |
Based on Crystalline Phase | ||
Corundum Ceramics | Primarily α-Al2O3 | High-temperature, high-stress applications |
Corundum-Mullite Ceramics | α-Al2O3 and mullite (3Al2O3·2SiO2) | High-temperature applications requiring thermal stability |
Mullite Ceramics | Primarily mullite | High-temperature applications, especially thermal cycling |
Based on Porosity | ||
Dense Alumina Ceramics | Low porosity, high strength | Structural components, wear-resistant parts |
Porous Alumina Ceramics | High porosity, good permeability | Filters, catalyst supports, biomaterials |
Based on Molding Process | ||
Pressure Casting | High-precision parts with complex shapes | Electronic components, precision engineering |
Slip Casting | Large, complex shapes with good dimensional accuracy | Sanitary ware, tableware, technical ceramics |
Injection Molding | Mass production of complex shapes | Electronic components, automotive parts, medical devices |
Tape Casting | Production of thin, flat ceramic sheets | Electronic substrates, capacitors, sensor |
By understanding these classifications, one can select the most suitable alumina ceramic for specific applications based on their desired properties and performance requirements
What are the Advantages of Alumina Ceramics?
Alumina ceramics offer a unique blend of properties that make them ideal for a wide range of applications. Here are some of their key advantages:
- Exceptional Hardness and Wear Resistance: Alumina ceramics boast a Rockwell hardness of HRA80-90, second only to diamond. This extraordinary hardness translates to superior wear resistance, significantly outperforming traditional materials like wear-resistant steel and stainless steel.
- Lightweight: With a density of 3.6-3.8 g/cm³, alumina ceramics are significantly lighter than steel, reducing equipment weight and improving efficiency.
- Cost-Effective: Compared to other advanced ceramics, alumina ceramics offer a favorable cost-performance ratio, making them a popular choice for diverse applications.
- Excellent Thermal Properties: Alumina ceramics exhibit remarkable thermal properties, including:
- High thermal shock resistance
- Low thermal expansion coefficient
- Good thermal conductivity
- Chemical Resistance: Alumina ceramics are highly resistant to chemical attack and molten metal corrosion, ensuring durability in harsh environments.
- Non-Combustible and Durable: Alumina ceramics are inherently non-combustible and possess superior strength and durability compared to organic and metallic materials.
Property | Description |
---|---|
Hardness and Wear Resistance | Exceptionally hard, second only to diamond, offering superior wear resistance. |
Lightweight | Significantly lighter than steel, reducing equipment weight and improving efficiency. |
Cost-Effective | Favorable cost-performance ratio compared to other advanced ceramics. |
Thermal Properties | High thermal shock resistance, low thermal expansion coefficient, and good thermal conductivity. |
Chemical Resistance | Highly resistant to chemical attack and molten metal corrosion. |
Non-Combustible and Durable | Inherently non-combustible and possesses superior strength and durability. |
These combined properties make alumina ceramics a versatile and reliable material for various industries, including automotive, aerospace, electronics, and manufacturing.
What are the Disadvantages of Alumina Ceramics?
While alumina ceramics offer numerous advantages, they also have certain limitations:
- Brittleness: Alumina ceramics are inherently brittle, making them susceptible to fracture under impact or sudden stress. This brittleness limits their use in applications requiring high impact resistance.
- Thermal Shock Sensitivity: Alumina ceramics are sensitive to rapid temperature changes. This thermal shock can lead to cracking or even complete failure of the ceramic component.
- Processing Challenges: The fabrication of complex shapes from alumina ceramics can be challenging and requires specialized techniques.
- Recycling Difficulties: Recycling alumina ceramic products can be complex and energy-intensive, limiting their sustainability.
Property Description Brittleness Susceptible to fracture under impact or sudden stress. Thermal Shock Sensitivity Sensitive to rapid temperature changes, leading to cracking or failure. Processing Challenges Complex fabrication of complex shapes. Recycling Difficulties Difficult and energy-intensive recycling process.
It’s important to note that while these limitations exist, advancements in ceramic engineering and processing techniques are continually addressing these challenges.
What are the Functions and Applications of Alumina Ceramics?
Alumina ceramics, primarily composed of aluminum oxide (Al₂O₃), exhibit a wide range of properties that make them suitable for various applications across multiple industries.
Key Functions and Applications
Electrical Function
- Insulation: Alumina’s high resistivity and dielectric strength make it ideal for integrated circuit chips and packages, preventing electrical leakage.
- Ionic Conductivity: Certain formulations are used in sodium-sulfur batteries and oxygen sensors due to their ionic conductivity.
Optical Function
- High-pressure Sodium Vapor Lamp Luminous Tubes: Alumina’s temperature resistance and light transmission properties make it suitable for these tubes.
- Laser Material: Its optical clarity and thermal stability make it a valuable material for solid-state lasers.
Chemical Function
- Catalyst Support: Alumina enhances reaction rates in various chemical processes.
- Exhaust Gas Purification: Its porous structure allows it to adsorb harmful substances.
- Corrosion-resistant Materials: Alumina’s chemical inertness makes it ideal for corrosive environments.
- Solid Enzyme Carriers: It can be used as a carrier for enzymes in biochemical reactions.
Biological Function
- Artificial Bone and Tooth Roots: Alumina’s biocompatibility allows it to integrate well with biological tissues.
Sound Absorption Function
- Sound-absorbing Panels: Its porous structure enables effective sound absorption.
Thermal Function
- Heat-resistant Structural Materials: Alumina’s high melting point makes it suitable for high-temperature environments.
- Heat-insulating Materials: Its low thermal conductivity makes it an effective insulator.
Mechanical Function
- Abrasive Materials and Cutting Tools: Alumina’s hardness makes it ideal for grinding and cutting.
- Bearings and Mechanical Precision Parts: Its wear resistance contributes to the longevity and reliability of these components.
Visualizing Alumina’s Applications
Real-world Examples
- Electronics: Alumina is used in the packaging of smartphones and other electronic devices.
- Medicine: Alumina-based dental implants are a common choice for tooth replacement.
- Automotive: Alumina ceramics are used in catalytic converters to reduce harmful emissions.
Future Trends As technology continues to advance, alumina ceramics are poised to play an even more significant role. Potential future applications include:
- 5G Communication: Alumina’s high-frequency properties make it suitable for 5G antennas and components.
- Advanced Medical Devices: Its biocompatibility and strength make it ideal for innovative medical implants.
Function | Applications |
---|---|
Electrical | Integrated circuit chips, packages, spark plugs |
Na-S cell solid electrolyte, oxygen sensor | |
Optical | High-pressure sodium vapor lamp luminous tube, laser material |
Chemical | Control of chemical reactions, purification of exhaust gases, catalyst carriers |
Corrosion-resistant materials, solid enzyme carriers | |
Biological | Artificial bone, artificial tooth roots |
Sound Absorption | Sound-absorbing panels |
Thermal | Heat-resistant, heat-insulating structural materials |
Mechanical | Abrasive materials, cutting materials, bearings, mechanical precision part |
By understanding the diverse properties and applications of alumina ceramics, we can appreciate their vital role in modern technology and industry.
What are the Difficulties in Machining Alumina Ceramics?
lumina ceramics, renowned for their exceptional properties like hardness, high temperature resistance, and chemical stability, present significant challenges during machining. Here are the primary difficulties:
1. High Hardness and Brittleness
- Strong Atomic Bonds: The strong ionic bonds between aluminum and oxygen ions result in high hardness and brittleness.
- Chip Formation: The material’s tendency to fracture rather than deform plastically leads to difficulties in chip formation and removal.
- Tool Wear: The high hardness causes rapid wear of cutting tools, reducing tool life and compromising machining accuracy.
2. Low Thermal Conductivity
- Heat Build-Up: The low thermal conductivity of alumina ceramics leads to heat accumulation at the cutting edge, increasing tool wear and potentially causing thermal shock to the workpiece.
3. Chemical Reactivity
- Tool Material Compatibility: Alumina ceramics can react with certain tool materials, leading to chemical wear and reduced tool life.
4. Difficult to Achieve High Precision
- Microcracking: The brittle nature of alumina ceramics can lead to microcracking during machining, affecting the final surface finish and dimensional accuracy.
5. High Cost of Machining
- Specialized Tools: The need for specialized cutting tools and slow machining speeds increases the cost of machining alumina ceramics.
- Tool Replacement: Frequent tool replacement due to wear further contributes to higher costs.
Challenge | Description |
---|---|
High Hardness and Brittleness | Strong atomic bonds lead to difficulty in chip formation, rapid tool wear, and microcracking. |
Low Thermal Conductivity | Heat build-up at the cutting edge, increasing tool wear and thermal shock. |
Chemical Reactivity | Potential reactions with tool materials, leading to chemical wear. |
Difficult to Achieve High Precision | Microcracking and tool wear can affect surface finish and dimensional accuracy. |
High Cost of Machining | Specialized tools and slow machining speeds increase costs. |
To address these challenges, advanced machining techniques, such as diamond or cubic boron nitride (CBN) tooling, cryogenic machining, and ultrasonic machining, are often employed. However, these techniques can be expensive and require specialized expertise.
What is the Raw Material of Alumina Ceramics?
The primary raw material for alumina ceramics is alumina powder. Specifically, α-Al2O3 (alpha-alumina) is the most commonly used form due to its desirable properties:
- High hardness and wear resistance: This makes it ideal for applications like cutting tools and bearings.
- High temperature stability: It can withstand high temperatures without significant degradation.
- Good mechanical and electrical properties: It exhibits excellent strength and insulation properties.
The higher the content of α-Al2O3 in the ceramic, the better its overall performance, including increased strength, density, and wear resistance. For high-purity or transparent alumina ceramics, the purity of the raw material must be extremely high (>99.9%) and the powder must be finely ground with a uniform particle size distribution.
How is the Raw Material of Alumina Prepared?
The primary raw material for alumina ceramics is alumina powder, predominantly in the form of α-Al2O3. This is typically derived from bauxite ore through a multi-step refining process.
Traditional Method (Bayer Process)
- Mining and Bauxite Preparation: Bauxite ore is mined and then crushed and ground to a fine powder.
- Digestion: The powdered bauxite is digested in a concentrated sodium hydroxide solution under high pressure and temperature. This process dissolves the alumina, forming sodium aluminate.
- Precipitation: The sodium aluminate solution is cooled and seeded with aluminum hydroxide crystals. This triggers the precipitation of aluminum hydroxide.
- Calcination: The precipitated aluminum hydroxide is calcined at high temperatures to remove water and convert it into alumina powder.
High-Purity Alumina Preparation
For applications requiring high-purity alumina, more sophisticated methods are employed:
- Organic Aluminum Salt Hydrothermal Decomposition: Organic aluminum salts are hydrolyzed under hydrothermal conditions to form aluminum hydroxide, which is then calcined.
- Aluminum Water Discharge Oxidation: Aluminum metal is oxidized in water to form aluminum hydroxide, which is subsequently calcined.
- Thermal Decomposition of Aluminum Sulfate and Ammonium Carbonate: Aluminum sulfate and ammonium carbonate are mixed and heated to decompose, yielding alumina powder.
- Thermal Decomposition of Ammonium Alum: Ammonium alum is heated to decompose, producing alumina powder.
The ammonium alum thermal decomposition method is particularly favored for producing high-purity alumina powder with fine particle size and narrow particle size distribution.
By carefully controlling the processing conditions, it is possible to produce alumina powder with the desired purity, particle size, and morphology for various applications.
Why Pre-Sintering is Crucial for Alumina Ceramics?
Pre-sintering is a critical step in the production of alumina ceramics for several reasons:
Phase Transformation and Volume Shrinkage:
- γ-Al2O3 to α-Al2O3: Industrial alumina powder often contains γ-Al2O3, a metastable phase.
- Irreversible Volume Change: Upon heating above 1200°C, γ-Al2O3 undergoes an irreversible phase transformation to α-Al2O3, resulting in a significant volume shrinkage of about 14%.
- Dimensional Control: Pre-sintering the powder partially densifies it and stabilizes the α-Al2O3 phase, minimizing this volume change during subsequent firing, thus improving dimensional control of the final ceramic product.
Impurity Removal:
- Volatile Impurities: Pre-sintering can drive off volatile impurities like Na2O, which can negatively impact the properties of the final ceramic.
- Improved Purity: By removing these impurities, the purity of the alumina powder is enhanced, leading to improved performance of the final ceramic.
Enhanced Sinterability:
- Particle Bonding: Pre-sintering promotes the bonding of alumina particles, creating a more sinterable powder compact.
- Reduced Porosity: This initial densification reduces the amount of porosity in the green body, leading to faster and more efficient sintering.
In summary, pre-sintering is essential to control the phase transformation of alumina, minimize volume shrinkage, remove impurities, and improve the sinterability of the powder, ultimately leading to the production of high-quality alumina ceramics with desired properties.
What are the Factors that Affect Pre-sintering Quality?
Pre-sintering is a critical step in the production of alumina ceramics. Several factors influence the quality of the pre-sintered powder:
1. Additives
- Purpose: Additives are used to enhance the sintering process, improve the properties of the final ceramic, and reduce the sintering temperature.
- Common Additives:
- H3BO3, NH4F, AlF3: These additives promote phase transformation from γ-Al2O3 to α-Al2O3 and help remove impurities like Na2O. The optimal addition range is typically between 0.3% and 3% by weight of the alumina powder.
- High-Purity Alumina (VK-L100G): This additive can lower the sintering temperature by up to 50°C.
2. Pre-Sintering Temperature
- Optimal Temperature: The pre-sintering temperature should be carefully controlled.
- Too Low: Incomplete phase transformation to α-Al2O3, leading to poor electrical properties.
- Too High: Excessive sintering, resulting in difficulty in subsequent processing and reduced reactivity.
- Typical Temperature Range: 1400-1450°C. However, the optimal temperature can vary depending on the specific alumina powder and additives used.
3. Atmosphere
- Reducing Atmosphere: A reducing atmosphere, such as a CO+H2 mixture, is often preferred for pre-sintering alumina.
- Benefits of Reducing Atmosphere:
- Promotes phase transformation by reducing the activation energy for the conversion of γ-Al2O3 to α-Al2O3.
- Reduces impurity levels, particularly alkali metal impurities, which can degrade the electrical properties of the ceramic.
- Improves the overall quality of the pre-sintered powder by creating a more uniform microstructure.
Factor | Effect on Pre-Sintering Quality |
---|---|
Additives | * Promotes phase transformation (γ-Al2O3 to α-Al2O3) * Removes impurities (e.g., Na2O) * Reduces sintering temperature |
Pre-Sintering Temperature | * Too low: Incomplete phase transformation * Too high: Excessive sintering, reduced reactivity |
Atmosphere | * Reducing atmosphere (e.g., CO+H2) promotes phase transformation and reduces impurities |
By carefully controlling these factors, it is possible to achieve high-quality pre-sintered alumina powder, which is essential for producing high-performance alumina ceramics.
How to Check the Quality of Al2O3 Pre-sintering?
Here are some common methods to assess the quality of pre-sintered alumina powder:
1. Dyeing Method
- Principle: The porous structure of γ-Al2O3 allows it to absorb dyes, while the dense structure of α-Al2O3 does not.
- Procedure: The pre-sintered powder is immersed in a dye solution (e.g., alizarin red, methylene blue) for a specific time (e.g., 10-30 minutes).
- Interpretation: The extent of dye adsorption indicates the amount of unconverted γ-Al2O3. A darker color suggests a higher content of γ-Al2O3, while a lighter color indicates a higher degree of conversion to α-Al2O3.
2. Optical Microscopy
- Principle: The refractive index of α-Al2O3 differs from that of γ-Al2O3.
- Procedure: The pre-sintered powder is examined under a polarizing microscope using immersion oil with a known refractive index (e.g., 1.730).
- Interpretation: The phase composition can be determined by observing the interference colors of the particles. Particles with a refractive index higher than 1.730 are primarily α-Al2O3, while those with a lower refractive index are predominantly γ-Al2O3.
3. Density Measurement
- Principle: The density of α-Al2O3 is higher than that of γ-Al2O3.
- Procedure: The bulk density of the pre-sintered powder is measured using a pycnometer or other suitable method.
- Interpretation: A higher density indicates a higher degree of conversion to α-Al2O3. However, this method alone may not be sufficient to assess the quality, as other factors like particle size distribution and porosity can also affect the bulk density. A typical density for well-sintered α-Al2O3 is around 3.95 g/cm³.
4. X-ray Diffraction (XRD)
- Principle: XRD can identify the crystalline phases present in a material.
- Procedure: The pre-sintered powder is analyzed using XRD to determine the relative amounts of α-Al2O3 and γ-Al2O3.
- Interpretation: The intensity of the diffraction peaks corresponding to α-Al2O3 can be used to quantify the degree of conversion. A well-sintered sample should exhibit strong diffraction peaks for α-Al2O3 and minimal peaks for γ-Al2O3.
Method | Principle | Procedure | Interpretation |
---|---|---|---|
Dyeing Method | Difference in porosity between α-Al2O3 and γ-Al2O3 | Immerse powder in dye solution | Darker color indicates higher γ-Al2O3 content |
Optical Microscopy | Difference in refractive index | Examine powder under polarizing microscope with immersion oil | Higher refractive index indicates α-Al2O3 |
Density Measurement | Higher density of α-Al2O3 | Measure bulk density | Higher density indicates higher α-Al2O3 content |
X-ray Diffraction (XRD) | Identification of crystalline phases | Analyze powder using XRD | Intensity of α-Al2O3 peaks indicates degree of conversion |
By combining these methods, a comprehensive assessment of the quality of pre-sintered alumina powder can be obtained.
What is the Preparation Method of Alumina Powder?
Alumina powder, primarily in the form of α-Al₂O₃, can be prepared through various methods:
1. Solid-Phase Method
- Process: Grinding aluminum salts or alumina, followed by calcination.
- Advantages: Low cost, large-scale production, and simple process.
- Disadvantages: High energy consumption, low efficiency, large particle size distribution, and potential for particle oxidation and deformation.
2. Gas-Phase Method
- Process: Conversion of materials into a gaseous state through techniques like evaporation, plasma, laser, or electron beam, followed by chemical reaction and condensation.
- Advantages: Precise control of reaction conditions, fine particle size, narrow particle size distribution, and good dispersibility.
- Disadvantages: Low yield and challenging powder collection.
Sub-categories of Gas-Phase Method:
- Evaporation-Condensation Method: Physical process involving evaporation and condensation of a material.
- Chemical Vapor Deposition (CVD): Chemical reactions between gaseous precursors to form solid deposits.
3. Liquid-Phase Method
- Process: Precipitation of aluminum ions from a solution using a suitable precipitant or through processes like evaporation, sublimation, or hydrolysis.
- Advantages: Precise control of chemical composition, uniform particle size, simple equipment, and low operating temperature.
- Disadvantages: Tendency for particle agglomeration and difficulty in dispersion.
Common Liquid-Phase Methods:
- Precipitation Method: Precipitation of aluminum hydroxide from a solution of aluminum salt using a base.
- Sol-Gel Method: Formation of a sol (colloidal suspension) followed by gelation and drying.
- Hydrothermal Method: Synthesis of materials under high temperature and pressure in aqueous solution.
Method | Process | Advantages | Disadvantages |
---|---|---|---|
Solid-Phase | Grinding and calcination | Low cost, large-scale production, simple process | High energy consumption, low efficiency, large particle size distribution, particle oxidation and deformation |
Gas-Phase | Evaporation, plasma, laser, or electron beam followed by chemical reaction and condensation | Precise control, fine particle size, narrow distribution, good dispersibility | Low yield, challenging powder collection |
Liquid-Phase | Precipitation, sol-gel, or hydrothermal methods | Precise chemical composition, uniform particle size, simple equipment, low temperature | Particle agglomeration, difficult dispersion |
The choice of method depends on the desired properties of the alumina powder, such as purity, particle size, morphology, and cost. For high-purity and fine-particle-size alumina, gas-phase and liquid-phase methods are often preferred. For lower-purity and coarser-particle-size alumina, the solid-phase method may be more suitable.
What is the Production Process of Alumina Ceramics?
1. Raw Material Preparation
- Pre-sintering: Industrial alumina often contains γ-Al₂O₃, which is less stable than α-Al₂O₃. Pre-sintering converts γ-Al₂O₃ to α-Al₂O₃, reducing shrinkage during subsequent firing.
2. Grinding
- Particle Size Reduction: The pre-sintered alumina is ground to a fine powder, typically with a specific surface area greater than 7000 cm²/g.
- Particle Size Distribution: A well-defined particle size distribution is crucial for optimal sintering. Particles smaller than 2 µm should constitute a significant portion of the powder.
3. Formulation
- Composition: The formulation of alumina ceramics varies depending on the desired properties. Common compositions include 75%, 80%, 95%, and 99% alumina ceramics.
- Additives: Additives like silica, calcium oxide, and magnesia can be added to modify the properties of the ceramic, such as sintering temperature and mechanical strength.
4. Additive Blending
- Deflocculants: These additives, like HCl, improve the fluidity of the slurry.
- Binders and Plasticizers: These additives, such as organic polymers, enhance the plasticity and strength of the green body.
5. Forming
- Dry Pressing: Suitable for simple shapes, involves compacting dry powder under high pressure.
- Slip Casting: Used for complex shapes, involves pouring a slurry into a porous mold and allowing the water to be absorbed.
- Injection Molding: Suitable for mass production of complex shapes, involves injecting a slurry into a mold under high pressure.
- Other Methods: Pressure casting, extrusion, and hot pressing are also used depending on the desired shape and properties.
6. Drying
- Removal of Moisture: The formed green bodies are dried to remove excess moisture.
- Drying Techniques: Drying can be done by air drying, oven drying, or microwave drying.
7. Sintering
- Densification: The green bodies are heated to high temperatures to densify and form a solid ceramic.
- Sintering Atmosphere: The sintering atmosphere can be air, nitrogen, or a reducing atmosphere.
- Sintering Temperature: The sintering temperature depends on the desired properties and the specific alumina composition.
8. Machining and Finishing
- Machining: The sintered ceramic parts are machined to the final shape and size using techniques like grinding, drilling, and polishing.
- Finishing: Surface treatments like polishing and glazing can be applied to improve the appearance and performance of the ceramic parts.
9. Inspection
Quality Control:
- Visual Inspection: Checking for defects like cracks, chips, or discoloration.
- Dimensional Inspection: Verifying that the parts meet the specified dimensions and tolerances.
- Density Measurement: Ensuring the desired density and porosity.
- Mechanical Testing: Testing for properties like hardness, strength, and fracture toughness.
- Thermal Shock Resistance: Evaluating the ability to withstand rapid temperature changes.
- Chemical Resistance: Assessing resistance to acids, bases, and other chemicals.
- Electrical Properties: Measuring electrical conductivity, dielectric strength, and other relevant properties.
Quality Assurance:
- Statistical Process Control (SPC): Monitoring key process parameters and identifying potential issues.
- Root Cause Analysis (RCA): Investigating the root causes of defects and implementing corrective actions.
- Continuous Improvement: Implementing measures to improve product quality and process efficiency.
10. Packing
- Packaging Material Selection: Choosing appropriate packaging materials to protect the products during transportation and storage.
- Packaging Design: Designing packaging that is durable, cost-effective, and environmentally friendly.
- Labeling and Marking: Clearly labeling the packages with product information, batch number, and handling instructions.
- Palletizing: Organizing the packaged products onto pallets for efficient transportation.
- Storage: Storing the packaged products in a clean, dry, and secure environment.
By following these steps, manufacturers can ensure that alumina ceramic products meet the highest quality standards and are delivered to customers in excellent condition.
By carefully controlling each step of the production process, it is possible to produce high-quality alumina ceramics with a wide range of properties and applications.
Is Alumina Ceramic Safe? is it Harmful for Body?
Yes, alumina ceramic products are generally safe for everyday use. They are not toxic and do not pose a health risk when used as intended. However, it is important to be aware of the following:
- Occupational Hazards: During the manufacturing process, exposure to alumina dust can be harmful. Workers should wear appropriate protective equipment, such as masks and gloves, to avoid inhaling or ingesting the dust.
- Accidental Ingestion: While alumina ceramic itself is not toxic, ingesting large amounts of ceramic dust can cause digestive issues. If you accidentally ingest alumina ceramic, drink plenty of water and seek medical attention if necessary.
- Eye and Skin Contact: Alumina ceramic dust can irritate the eyes and skin. If you get alumina ceramic dust in your eyes or on your skin, rinse thoroughly with water and seek medical attention if irritation persists.
Overall, alumina ceramic products are safe for consumers. However, it is important to handle them with care, especially during manufacturing and processing, to avoid potential health risks.
What is The Impact of Isostatic Pressing on Alumina Ceramics ?
Isostatic pressing is a critical technique in the production of alumina ceramics, significantly influencing their final properties. This method involves applying uniform pressure from all directions to compact ceramic powders into a desired shape. Two primary isostatic pressing methods are commonly used:
Cold Isostatic Pressing (CIP)
In CIP, ceramic powder is placed in a flexible mold and subjected to high pressure at room temperature. This method is relatively cost-effective and suitable for producing complex shapes. However, the resulting ceramics may exhibit lower density and mechanical properties compared to those produced by HIP.
Advantages of CIP:
- Uniform density and microstructure
- Excellent dimensional accuracy
- Ability to produce complex shapes
Disadvantages of CIP:
- Limited green strength, requiring careful handling
- Potential for mold deformation at high pressures
Hot Isostatic Pressing (HIP)
HIP involves applying high pressure and temperature simultaneously to the ceramic powder in a sealed container. This process results in higher density, finer grain size, and improved mechanical properties, such as higher strength and toughness. However, HIP is more energy-intensive and requires specialized equipment.
Advantages of HIP:
- Very high density and uniform microstructure
- Elimination of pores and defects
- Improved mechanical properties
Disadvantages of HIP:
- High energy consumption
- Complex equipment and process
Feature | Cold Isostatic Pressing (CIP) | Hot Isostatic Pressing (HIP) |
---|---|---|
Pressure | Room temperature | High temperature and pressure |
Density | Lower density | Higher density |
Microstructure | Larger grain size | Finer grain size |
Mechanical Properties | Moderate strength and toughness | Superior strength and toughness |
Complexity of Shapes | Can produce complex shapes | Can produce complex shapes, but requires more careful mold design |
Cost | Lower cost | Higher cost due to energy consumption and specialized equipment |
Key Factors Influencing the Quality of Alumina Ceramics:
- Pressure: Higher pressure generally leads to higher density and improved mechanical properties. However, excessive pressure can cause cracking and deformation.
- Temperature: In the case of HIP, temperature plays a crucial role in densification and grain growth.
- Holding Time: The duration of the pressing process affects the degree of densification and microstructure development.
- Powder Characteristics: Particle size distribution, shape, and surface area of the alumina powder significantly impact the densification behavior.
- Mold Design: The design of the mold influences the final shape and dimensions of the ceramic component.
Impact on Ceramic Properties:
- Density: Higher density leads to improved mechanical properties, thermal conductivity, and electrical conductivity.
- Microstructure: A fine-grained microstructure with uniform grain size enhances the mechanical properties and resistance to thermal shock.
- Mechanical Properties: Isostatic pressing can significantly improve the strength, hardness, and fracture toughness of alumina ceramics.
- Dimensional Accuracy: Precise control of pressure and temperature allows for accurate control of the final dimensions of the ceramic components.
By carefully controlling the isostatic pressing parameters, it is possible to produce high-quality alumina ceramics with tailored properties for specific applications.
What is the Key Factors Affecting Sintering of Alumina Ceramics?
Sintering is a critical step in the production of alumina ceramics, significantly impacting their final properties. This process involves heating a compacted powder compact to a high temperature below its melting point, leading to densification and the formation of a solid, ceramic body.
1. Temperature Control:
- Optimal Temperature: The sintering temperature must be carefully controlled to achieve optimal densification and phase transformation. For alumina ceramics, this typically ranges from 1500°C to 1800°C.
- Temperature Gradients: Excessive temperature gradients can induce thermal stresses, potentially leading to cracking and deformation of the ceramic body.
- Holding Time: Sufficient holding time at the peak temperature is necessary to complete the sintering process and ensure adequate densification and grain growth.
2. Atmosphere Control:
- Reducing Atmosphere: A reducing atmosphere, such as hydrogen or a mixture of hydrogen and nitrogen, can prevent oxidation of the alumina powder and maintain the desired properties of the ceramic. This is particularly important for high-purity alumina ceramics.
- Inert Atmosphere: An inert atmosphere, such as argon or nitrogen, can be used to minimize contamination and maintain a stable environment during the sintering process.
3. Heating and Cooling Rates:
- Slow Heating: Gradual heating rates can reduce thermal shock and prevent cracking, especially for large or complex ceramic components.
- Controlled Cooling: Slow cooling can minimize residual stresses and improve the final microstructure of the ceramic. Rapid cooling can lead to the formation of defects and reduced mechanical properties.
4. Sintering Aids:
- Additives: Small amounts of additives, such as magnesium oxide (MgO) or calcium oxide (CaO), can enhance densification and control grain growth during sintering. These additives can lower the sintering temperature, increase the sintered density, and improve the mechanical properties of the ceramic.
Sintering Mechanisms
The sintering process involves several mechanisms, including:
- Neck Growth: Initial contact between particles leads to the formation of necks, which grow and bridge the gaps between particles.
- Grain Boundary Diffusion: Atoms diffuse along grain boundaries, leading to densification and grain growth.
- Volume Diffusion: Atoms diffuse through the bulk material, contributing to densification and pore elimination.
By carefully controlling the sintering parameters and employing appropriate sintering aids, it is possible to produce high-quality alumina ceramics with excellent mechanical, thermal, and electrical properties.
What is the Maintenance Cost of Alumina Ceramics?
Alumina ceramics are renowned for their exceptional physical and chemical properties, which directly translate into significant cost savings in terms of maintenance.
Key Factors Contributing to Low Maintenance Costs:
Exceptional Wear Resistance and Longevity:
- High Hardness: Alumina ceramics possess exceptional hardness, enabling them to withstand wear and tear in high-speed and high-friction environments.
- Extended Lifespan: This inherent durability significantly extends the lifespan of components, reducing the frequency of replacements and associated costs.
Superior Corrosion Resistance:
- Chemical Inertness: Alumina ceramics exhibit excellent resistance to a wide range of chemicals, including acids, alkalis, and salts. This chemical inertness minimizes degradation and corrosion, reducing the need for frequent repairs and replacements.
Outstanding Stability and Reliability:
- Extreme Condition Tolerance: Alumina ceramics can maintain stable performance under extreme conditions, such as high temperatures and high pressures.
- Reduced Downtime: This exceptional stability and reliability minimize downtime caused by failures, leading to significant cost savings.
Ease of Maintenance:
- Simple Cleaning: Alumina ceramics are relatively easy to clean with mild detergents and soft cloths.
- Minimal Special Treatment: Due to their inherent properties, they require minimal special maintenance or treatment.
Cost Considerations and Influencing Factors:
While alumina ceramics offer significant long-term cost savings, several factors can influence the overall cost:
- Raw Material Costs: The cost of raw materials, such as alumina powder and additives, can impact the final price of alumina ceramic products.
- Manufacturing Process Costs: The complexity of the manufacturing process, including shaping, sintering, and finishing, can also affect the cost.
- Production Scale: Economies of scale can reduce production costs and, consequently, the final price of alumina ceramic products.
- Application-Specific Requirements: High-performance applications, such as those in aerospace or medical industries, may require specialized processing techniques and high-quality materials, leading to higher costs.
In conclusion, alumina ceramics offer a compelling value proposition due to their low maintenance costs and exceptional performance. By understanding the factors influencing costs and implementing appropriate maintenance practices, businesses can maximize the benefits of this versatile material.
What is the Price of Alumina Ceramics?
he price of alumina ceramics can vary widely depending on several factors:
Product Type:
- Simple Shapes: Basic shapes like plates, tubes, and rods tend to be more affordable.
- Complex Shapes: Custom-shaped or precision-engineered components can be more expensive due to the additional processing required.
- High-Performance Ceramics: Specialized ceramics with advanced properties, such as high purity or high strength, may command higher prices.
Material Grade:
- Purity: Higher purity alumina ceramics, especially those used in high-tech applications, are generally more expensive.
- Grain Size: The grain size of the alumina powder can impact the final properties and cost of the ceramic.
Manufacturing Process:
- Complexity: Complex manufacturing processes, such as those involving intricate shapes or specialized coatings, can increase the cost.
- Volume: Larger production volumes can lead to economies of scale and lower unit costs.
Market Demand:
- Asia-Pacific: This region dominates the global alumina ceramics market due to rapid industrialization, increasing demand for electronics, and growing automotive industries.
- North America and Europe: These regions are significant markets for high-performance alumina ceramics, particularly in the automotive, aerospace, and medical sectors.
Additional Services:
- Customization: Customizing the shape, size, or properties of alumina ceramics can incur additional costs.
- Finishing: Surface treatments like polishing or coating can also affect the price.
To get a precise quote for your specific alumina ceramic needs, it’s best to consult with a manufacturer or supplier. They can provide you with detailed pricing information based on your requirements.
However, it’s generally true that alumina ceramics offer a good value proposition compared to other advanced ceramics. They often provide excellent performance at a reasonable cost, making them a popular choice for a wide range of applications.
Can Yomua Accept Small Quantities of Custom-made Alumina Ceramic Components?
Yomua is a company that specializes in the production of advanced ceramic components, particularly alumina ceramics. We are known for their expertise in custom manufacturing and have a range of capabilities that allow us to cater to various industries, including electronics, medical devices, and industrial applications.
Many manufacturers in the ceramics industry have minimum order quantities (MOQs) due to the costs associated with setup and production runs. But for Yomua,We have flexible options depending on:
- The complexity of the part
- The materials used
- The production method chosen
Yomua has been known to accommodate smaller orders to support our customers development.Especially if align with our operational efficiencies or if we are part of a larger ongoing project.
Yomua places a strong emphasis on customer service and collaboration with clients. Our willingness to accept small quantities often reflects our commitment to meeting customer needs. We may offer tailored solutions or work closely with clients during the design phase to ensure that even small orders can be produced efficiently.
In conclusion, Yomua can accept small quantities of custom-made alumina ceramic components, although this may depend on factors such as part complexity, production methods, and current operational capacities. It is advisable for you to directly contact us for specific inquiries regarding your projects to get detailed information about minimum order requirements and customization options.
Alumina Al2O3 Ceramic Components Conclusion
Alumina ceramic, primarily composed of aluminum oxide (Al2O3), is a high-performance material with exceptional properties. Its outstanding mechanical strength, thermal stability, and electrical insulation make it ideal for diverse applications. From aerospace components to biomedical implants, alumina ceramics offer durability, reliability, and precision.
The production process involves several key steps: powder preparation, shaping techniques like pressing or casting, high-temperature sintering to densify the material, and final machining for precise dimensions. While alumina ceramics are generally safe and non-toxic, proper handling and disposal of manufacturing byproducts are essential.
Yomua, a leading manufacturer, specializes in custom alumina ceramic components, even in small quantities. Their expertise and advanced manufacturing capabilities ensure the delivery of high-quality products tailored to specific requirements.