Silicon Carbide (SiC) Ceramic Components
Trusted SiC Ceramic Manufacturer
- Proven Track Record in Silicon Carbide (SiC) Ceramic Manufacturing
- Competitive Pricing Through Direct Manufacturing
- Personalized Service to Fulfill Your Specific Needs
- Unwavering Commitment to Qualityand Quality Assurance
Get a Quote Today
Your Trusted Silicon Carbide (SiC) Ceramic Components Manufacturer
WHy Yomua Silicon Carbide (SiC) Ceramic
- Decades of Expertise: With over 40 years of experience manufacturing, Our team of seasoned engineers is dedicated to pushing the boundaries of silicon carbide technology. we bring unparalleled knowledge and proven success to every project.
- Top Quality Standards: from the finest silicon carbide materials to rigorous quality control measures, ensures superior performance in every component.
- Precision at Your Fingertips: Our advanced manufacturing capabilities allow us to tailor surface accuracy to your exact specifications, guaranteeing a perfect fit and function.
- Responsive After-Sales Support: Our commitment extends beyond the sale. We offer exceptional after-sales service, ensuring you have the support you need to maximize the success of your project.
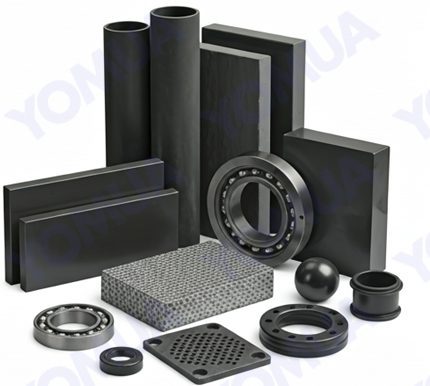
Custom Silicon Carbide (SiC) Ceramics
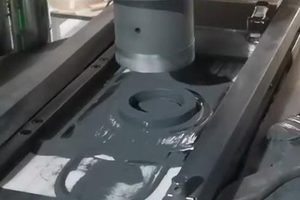
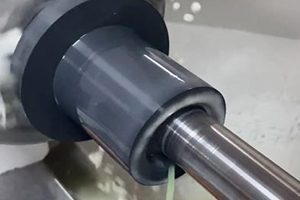
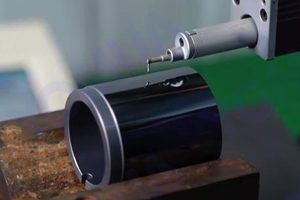
- Timely Delivery, Every Time: We understand the importance of efficiency. Our streamlined processes ensure prompt delivery of your silicon carbide components, keeping your projects on track.
- More Than a Supplier, a Partner: At YOMUA, we view ourselves as an extension of your team. We are here to collaborate, innovate, and provide you with the high-performance zirconia solutions you need to achieve success.
Silicon Carbide (SiC) Properties
Fabrication Process | Chemical Vapor Deposition | Reaction Sintering | Pressureless Sintering | Hot Pressing |
---|---|---|---|---|
Theoretical Density (g/cm³) | 3.20 | >3.05 | 3.15-3.20 | 3.15-3.20 |
Relative Density (%) | > 99.99 | > 97 | > 95 | > 98.0 |
Room Temperature Bending Strength (MPa) | 375 | 150-450 | 400-600 (Solid-state sintering) 750-900 (Liquid-phase sintering) | 600-1000 |
Fracture Toughness (MPa·m1/2) | 3.1-3.5 | 2.5-4.5 | 3.5-4.5 (Solid-state sintering) 8.0-10.0 (Liquid-phase sintering) | 4.1-5.2 |
Weibull Modulus | 12 | 12 | 15 | 12-18 |
Elastic Modulus (GPa) | 440 | 300-393 | 410-430 | 420-450 |
Poisson’s Ratio | 0.17 (0.14-0.21) | |||
Hardness (HV/Kgmm²) | 2550-2850 | 2600 | 2500-2700 | |
Hardness (HRA) | 93-95 | 93-95 | 92-95 | 92-95 |
Coefficient of Thermal Expansion (×10-6/°C) (RT-1000°C) | 2.2 (Room temperature) 4.0 (1000°C) | 4.5-5.0 | 4.2-4.5 | 4.5 |
Thermal Conductivity (W/(m·K)) | 200-300 | 70-125 | 100-150 | 110-180 |
Thermal Shock Resistance | 157 | — | 180 | 164 |
Silicon Carbide (SiC) Ceramic Products
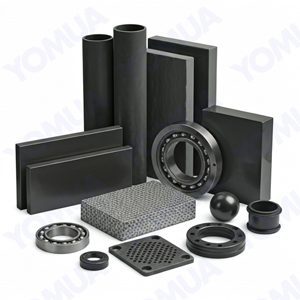
Custom Silicon Carbide SiC Ceramic Parts
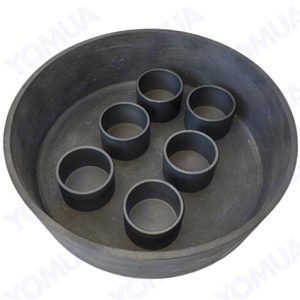
Silicon Carbide SiC Ceramic Crucible
High-temperature resistant crucibles crafted from robust Silicon Carbide (SiC) ceramic. 1 Ideal for melting, sintering, and processing metals, alloys, and ceramics
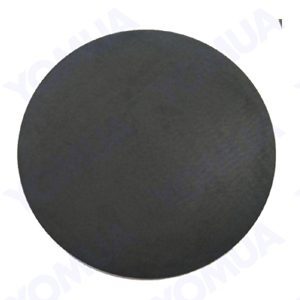
Porous Silicon Carbide (SiC) Ceramic Disc
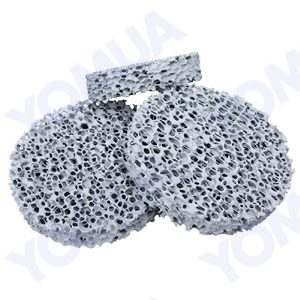
Silicon Carbide Ceramic Foam Filters
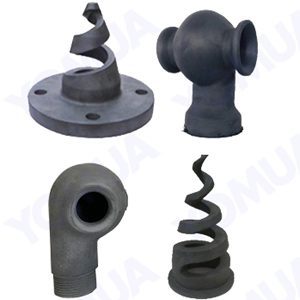
Silicon Carbide Ceramic Nozzle
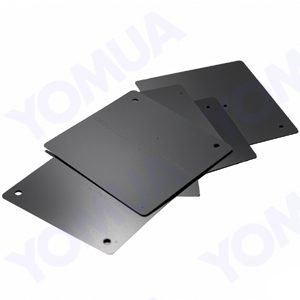
Silicon Carbide Ceramic Plate
Strong, wear-resistant plates made from Silicon Carbide (SiC) ceramic. Excellent for high-temperature environments, chemical processing requiring durability and heat resistance.
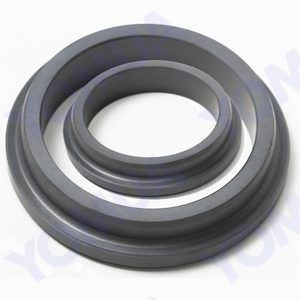
Silicon Carbide Ceramic Seal Ring
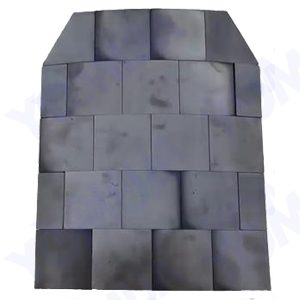
Silicon carbide ceramic Bulletproof Plate
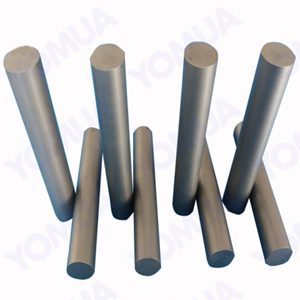
Silicon Carbide Ceramic Rod
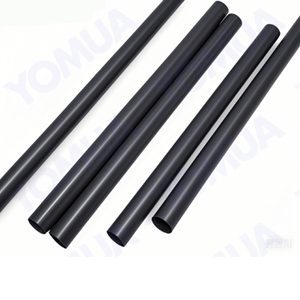
Silicon Carbide Ceramic Tube
Customer Reviews for Yomua Silicon Carbide Ceramic...

Your Satisfaction, Yomua Strength



Silicon Carbide (SiC) Ceramic Related Products
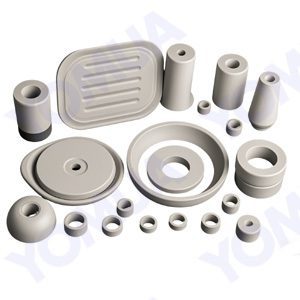
Boron Nitride(BN) Ceramics
High temperature resistance and electrical insulation properties.
Silicon Carbide (SiC) Ceramic Components Guide
Frequently Asked Questions
What is Silicon Carbide or Carborundum or SiC ?
Silicon Carbide (SiC), also known as carborundum or refractory sand, is a chemical compound composed of silicon and carbon atoms bonded in a crystalline structure. It can be synthesized artificially or found naturally as the rare mineral moissanite, which is formed under extreme pressure and temperature in meteorites.It’s renowned for its exceptional hardness, thermal stability, and other remarkable properties, making it a valuable material in various industrial applications.Silicon Carbide (SiC) was serendipitously discovered by American engineer Edward G. Acheson in 1891 while attempting to synthesize artificial diamonds.He heated a mixture of clay and powdered coke in an electric furnace, resulting in the formation of lustrous green crystals
What is Silicon Carbide Ceramic or SIC Ceramic?
Silicon carbide (SiC) ceramic is a high-performance, non-oxide ceramic material composed primarily of silicon carbide (SiC).SiC is known for its exceptional hardness, thermal stability, and resistance to chemical corrosion. SiC can crystallize into several distinct polytypes, including the most common forms: cubic (3C-SiC), hexagonal (4H-SiC), and hexagonal (6H-SiC). The specific arrangement of atoms within these polytypes influences the material’s physical properties. The strong covalent bonds between silicon and carbon atoms contribute significantly to SiC’s extraordinary hardness, making it one of the hardest materials known, second only to diamond.
What are the Properties of Silicon carbide (SiC) Ceramic ?
Silicon Carbide (SiC) is a remarkable compound composed of silicon and carbon atoms, bonded together in a strong covalent network. This unique structure gives SiC exceptional properties that make it invaluable in a wide range of applications.
Key Properties a:
Hardness:
- Second only to diamond: SiC is renowned for its exceptional hardness. Its hardness is comparable to diamond, making it an ideal material for abrasive tools, cutting tools, and polishing materials.
- Abrasive Applications: SiC is widely used in grinding wheels, sandpaper, and other abrasive tools due to its ability to efficiently remove material and provide a fine finish.
Thermal Stability:
- High Melting Point: SiC possesses an extremely high melting point, making it resistant to high temperatures. This property is crucial in applications like:
- Refractory Materials: SiC is used in the production of refractory materials for lining furnaces and kilns, where it can withstand extreme heat and corrosive environments.
- Ceramic Components: It is used in high-temperature ceramic components such as engine parts and heat exchangers.
- High Melting Point: SiC possesses an extremely high melting point, making it resistant to high temperatures. This property is crucial in applications like:
Thermal Conductivity:
- Efficient Heat Dissipation: SiC exhibits good thermal conductivity, allowing it to efficiently dissipate heat. This property is essential in:
- Electronics: SiC is used in heat sinks to cool electronic components, preventing overheating and improving performance.
- Efficient Heat Dissipation: SiC exhibits good thermal conductivity, allowing it to efficiently dissipate heat. This property is essential in:
Electrical Properties:
- Semiconductor Properties: SiC is a wide-bandgap semiconductor, offering several advantages over traditional silicon-based semiconductors:
- High-Power Electronics: SiC power devices, such as transistors and diodes, can handle higher voltages and temperatures, making them ideal for applications like electric vehicles, renewable energy systems, and industrial drives.
- High-Frequency Electronics: SiC devices can operate at higher frequencies, enabling faster switching speeds and improved efficiency in power electronics.
- Semiconductor Properties: SiC is a wide-bandgap semiconductor, offering several advantages over traditional silicon-based semiconductors:
Chemical Resistance:
- Corrosion Resistance: SiC is highly resistant to chemical corrosion, making it suitable for use in harsh environments.
In Conclusion:
Silicon Carbide’s unique combination of properties makes it a versatile material with a wide range of applications. From abrasive tools to high-performance electronics, SiC continues to play a vital role in modern technology and industry.
What are The Crystalline Structures of Silicon Carbide ?
Silicon Carbide (SiC) is a remarkable compound semiconductor material with a simple chemical formula (SiC) but a diverse range of crystalline structures. These structures, known as polytypes, arise from different stacking sequences of silicon and carbon atoms within the crystal lattice.
The Building Block: The Si-C Tetrahedron
At the heart of SiC’s structure is the Si-C tetrahedron. Both silicon and carbon atoms have four valence electrons, allowing them to form four strong covalent bonds with neighboring atoms. This tetrahedral arrangement is the fundamental building block of the SiC crystal lattice.
Polymorphism: A World of Possibilities
The diverse range of SiC polytypes arises from variations in the stacking sequence of these Si-C tetrahedra. Some of the most common polytypes include:
- 2H-SiC: A hexagonal structure with a simple AB stacking sequence. This polytype offers the highest bandgap among common SiC polytypes, making it promising for high-frequency and high-temperature applications.
- 3C-SiC: A cubic structure with an ABCABC stacking sequence. It exhibits high electron mobility, making it suitable for high-frequency and high-power electronic devices.
- 4H-SiC: A hexagonal structure with an ABAB stacking sequence. It possesses excellent thermal conductivity and high breakdown voltage, making it widely used in power electronics, high-temperature electronics, and optoelectronic devices.
- 6H-SiC: A hexagonal structure with an ABCABC stacking sequence. It offers excellent thermal and electrical properties, making it suitable for high-power applications.
- 15R-SiC: A rhombohedral structure with a more complex stacking sequence. It is less common but holds promise for specific applications due to its unique electronic properties.
The Impact of Polytype on Properties
The specific polytype of SiC influences its physical and electrical properties, including:
- Bandgap: The energy gap between the valence and conduction bands varies among polytypes, affecting their electrical conductivity and optical properties.
- Thermal Conductivity: The arrangement of atoms within the polytype impacts the material’s ability to conduct heat.
- Mechanical Properties: The crystal structure influences the material’s hardness, strength, and fracture toughness.
Unique Properties and Applications
The unique properties of SiC, particularly its hardness, thermal conductivity, and chemical resistance, have led to its widespread use in various applications:
- Electronics: SiC is used in power electronics devices, such as transistors and diodes, offering superior performance in terms of efficiency, power handling capacity, and operating temperature range.
- Abrasives and Cutting Tools: SiC’s exceptional hardness makes it an ideal material for grinding wheels, cutting tools, and sandpaper.
- Ceramics: SiC ceramics are used in high-temperature applications, such as engine components and furnace linings, due to their excellent thermal stability and resistance to oxidation.
- Optoelectronics: SiC is used in light-emitting diodes (LEDs) and other optoelectronic devices.
- Gemstones: SiC, known as moissanite, is a popular gemstone due to its brilliance and hardness.
The ability to control the growth of specific SiC polytypes has opened up new possibilities for tailoring the material’s properties to meet the demands of various applications. As research and technology continue to advance, SiC is poised to play an even greater role in shaping the future of electronics, materials science, and other fields.
What are The Types of Silicon Carbide (SiC) Ceramics?
Silicon carbide (SiC) ceramics are classified into various types based on their production methods, properties, and applications. Here are some of the common types:
Traditional SiC Ceramics
Black Silicon Carbide (SiC):
- Composed of approximately 98.5% SiC.
- Produced through high-temperature smelting of high-quality silica, quartz sand, and petroleum coke.
- Offers greater toughness compared to green SiC.
- Primarily used for processing materials with lower tensile strength, such as glass, ceramics, stone, refractory materials, cast iron, and non-ferrous metals.
Green Silicon Carbide (SiC):
- Contains over 99% SiC.
- Produced via high-temperature smelting of petroleum coke and silica with the addition of salt.
- Known for its self-sharpening properties.
- Typically used for processing harder materials like hard alloys, chrome steel, optical glass, wear-resistant cylinder sleeves, and precision grinding of high-speed steel cutters.
Advanced SiC Ceramics
Silicon Nitride-Bonded Silicon Carbide (Si3N4-Bonded SiC):
- A composite material combining silicon nitride and silicon carbide.
- Offers improved toughness while maintaining the desirable properties of SiC ceramics.
- Used in applications requiring enhanced mechanical performance under thermal stress.
Reaction-Bonded Silicon Carbide (RBSiC):
- Produced by reacting silicon powder with carbon at high temperatures.
- Offers excellent thermal shock resistance and high-temperature strength.
- Used in applications like furnace linings, kiln furniture, and heat exchangers.
Pressureless Sintered Silicon Carbide (PS SiC):
- Manufactured by sintering SiC powder without applying external pressure.
- Exhibits high purity, fine-grained microstructure, and excellent mechanical properties.
- Used in applications such as wear-resistant components, cutting tools, and high-temperature structural parts.
Sintered Reaction-Bonded Silicon Carbide (SRBSiC):
- Combines the properties of RBSiC and PS SiC.
- Offers high strength, good thermal shock resistance, and excellent oxidation resistance.
- Used in applications like turbine components, rocket nozzles, and heat shields.
Silicon Carbide Ceramics with Additives:
- SiC ceramics can be modified by adding various additives to enhance specific properties.
- Common additives include boron, aluminum, and titanium.
- These additives can improve the mechanical strength, oxidation resistance, and thermal conductivity of SiC ceramics.
Nano-Silicon Carbide Ceramics:
- Made from nanosized SiC particles.
- Exhibit superior mechanical properties, thermal conductivity, and wear resistance compared to conventional SiC ceramics.
- Used in advanced applications such as high-performance cutting tools, electronic components, and protective coatings.
The choice of SiC ceramic type depends on the specific application requirements, such as temperature, mechanical load, chemical environment, and cost. By understanding the different types of SiC ceramics and their properties, engineers can select the most suitable material for a given application.
What are The Advantages of Silicon Carbide (SiC) Ceramics?
Silicon carbide (SiC) ceramics are a class of materials renowned for their exceptional properties, making them indispensable in various industries. These ceramics offer a unique combination of mechanical, thermal, chemical, and electrical properties that set them apart from other materials.
Mechanical Properties
- High Hardness and Strength: SiC ceramics exhibit exceptional hardness and strength, making them highly resistant to wear and tear.
- Excellent Thermal Shock Resistance: They can withstand rapid temperature changes without fracturing.
- High-Temperature Stability: SiC ceramics retain their mechanical properties at extremely high temperatures.
Thermal Properties
- High Thermal Conductivity: SiC ceramics efficiently dissipate heat, making them ideal for thermal management applications.
- Low Thermal Expansion: This property minimizes thermal stress and improves dimensional stability.
Chemical Properties
- Excellent Chemical Resistance: SiC ceramics are resistant to corrosion from acids, alkalis, and other chemicals.
- Oxidation Resistance: They can withstand high-temperature oxidation, making them suitable for high-temperature environments.
Electrical Properties
- Wide Bandgap Semiconductor: SiC possesses a wide bandgap, making it suitable for high-power, high-frequency electronic devices.
- High Breakdown Voltage: This property allows SiC devices to operate at higher voltages and temperatures compared to traditional silicon-based devices.
- High Thermal Conductivity: Efficient heat dissipation is crucial for electronic devices, and SiC’s high thermal conductivity helps prevent overheating.
Additional Advantages
- High Temperature Resistance and Strength: SiC ceramics can maintain high strength at elevated temperatures, making them suitable for applications in extreme environments.
- Low Density: SiC ceramics offer a good strength-to-weight ratio, making them ideal for lightweight applications.
- Good Electrical Properties: SiC ceramics exhibit good electrical conductivity and dielectric properties, making them suitable for use in electronic devices and electrical equipment.
- Biocompatibility: Certain types of SiC ceramics are biocompatible, making them suitable for biomedical applications such as artificial joints and dental implants.
In conclusion, silicon carbide ceramics offer a compelling combination of properties that make them ideal for demanding applications where high performance, durability, and reliability are critical.
What are The Disadvantages of Silicon Carbide (SiC) Ceramics?
While silicon carbide (SiC) ceramics offer a multitude of advantages, they also have some inherent limitations:
- High Cost: The production of SiC ceramics involves complex processes and requires high temperatures and pressures, leading to significant manufacturing costs. This can limit their widespread adoption, especially in cost-sensitive applications.
- Brittleness: SiC ceramics are inherently brittle, making them susceptible to fracture under impact or thermal shock. This can restrict their use in applications requiring high toughness and impact resistance.
- Difficulty in Machining: The extreme hardness of SiC ceramics makes them challenging to machine using traditional methods. Specialized tools and techniques are required, which can increase processing costs and time.
- Complex Processing: The manufacturing of SiC ceramics involves complex processes, such as sintering and chemical vapor deposition, which require precise control of temperature, pressure, and atmosphere.
- Limited Availability of Large-Sized Components: Producing large-sized SiC components can be challenging due to limitations in manufacturing processes and material availability.
- Increased Electrical Resistance at High Temperatures: SiC heating elements can experience a gradual increase in electrical resistance over time due to reactions with atmospheric gases at high temperatures, potentially affecting their performance and efficiency.
- Limited Thermal Shock Resistance: While SiC ceramics exhibit good thermal shock resistance, they are still susceptible to damage from rapid temperature changes, especially when compared to other materials.
Despite these limitations, the exceptional properties of SiC ceramics continue to make them a valuable material for a wide range of applications. Ongoing research and advancements in manufacturing techniques are helping to address some of these challenges and expand the potential of SiC ceramics.
What are The Applications of Silicon Carbide (SiC) Ceramics?
Silicon carbide (SiC) ceramics, renowned for their exceptional properties, have found wide-ranging applications across various industries. Here’s a detailed list of 30+ applications categorized into different sectors:
Mechanical and Chemical Industries
- Mechanical Seals: Used in pumps, compressors, and other equipment to prevent leakage.
- Sliding Bearings: Employed in high-load applications due to their wear resistance.
- Corrosion-Resistant Tubes: Utilized in chemical processing to transport corrosive fluids.
- Valves: Incorporated in valves that handle aggressive chemicals.
- Fan Blades: Used in high-temperature environments where traditional materials fail.
Aerospace and Defense
- Rocket Nozzles: Essential for high-performance propulsion systems.
- Combustion Chambers: Used in rocket engines for their thermal stability.
- Turbine Components: Applied in gas turbines for improved efficiency and durability.
- High-Temperature Gas Turbine Parts: Critical for energy generation and aerospace propulsion.
- Armor and Protective Gear: SiC-based armor materials offer excellent ballistic protection.
Automotive Industry
- Engine Components: Used in turbocharger rotors, valves, and piston rings.
- Brake Discs: Offers superior braking performance and longer lifespan.
Electrical and Electronics
- Substrates for Integrated Circuits: Provides excellent thermal conductivity and insulation properties.
- Heating Elements: Capable of withstanding high temperatures (up to 1600 °C).
- Lightning Arrester Components: Protects electrical systems from surges.
- Power Electronics: Used in power transistors and diodes due to high thermal conductivity and high breakdown voltage.
Refractory Applications
- Blast Furnace Linings: Resists high temperatures and corrosive environments.
- Kiln Supports and Saggers: Used in ceramic kilns for structural integrity at elevated temperatures.
- Muffle Linings for Furnaces: Protects furnace interiors from thermal shock.
Petrochemical Industry
- Corrosion-Resistant Containers and Pipelines: Essential for transporting aggressive chemicals safely.
- Sand Pumps and Hydrocyclones: Utilized in mineral processing due to their wear resistance.
Environmental Protection
- Filtration Systems for Wastewater Treatment Plants: Effective at filtering out contaminants due to chemical stability.
Manufacturing Tools
- Cutting Tools and Abrasives: Widely used due to their hardness and cutting performance.
Energy Sector
- Nuclear Reactor Components: Suitable for use in extreme environments found within reactors.
- Fuel Cells: Used in solid oxide fuel cells (SOFCs) due to high thermal conductivity, chemical stability, and mechanical strength.
- Solar Cells: Can be used as a substrate material for solar cells.
Marine Engineering
- Propeller Shafts: Enhances performance through corrosion resistance in marine environments.
Research Applications
- High-Temperature Sensors: Used in scientific research requiring stable measurements at elevated temperatures.
Additional Applications
- Semiconductor Manufacturing Equipment: Used in various semiconductor manufacturing processes.
- Advanced Coatings for Turbine Blades: Provides enhanced performance and durability.
- Photovoltaic Cells: Used as a substrate material to improve efficiency and durability.
- Medical Implants: Biocompatible and wear-resistant for dental implants and orthopedic devices.
- Optical Components: Used to manufacture high-precision optical components.
- Gas Turbine Components: Improves engine efficiency and performance.
- Nuclear Fuel Cladding: Provides protection for nuclear fuel.
By leveraging their unique properties, SiC ceramics continue to revolutionize various industries and drive technological advancements.
What are the Difficulties in Machining Silicon Carbide Ceramics?
Silicon carbide (SiC) ceramics, while offering exceptional properties, pose significant challenges during machining due to their inherent characteristics:
1. Extreme Hardness and Brittleness:
- SiC’s exceptional hardness makes it difficult to cut, often leading to rapid tool wear and damage.
- Its brittleness increases the risk of cracking and chipping during machining operations.
2. Specialized Machining Techniques:
- Traditional machining methods are often ineffective for SiC. Specialized techniques like electric discharge machining (EDM) are required to achieve precise shapes and dimensions.
- However, EDM has limitations and may not be suitable for all applications.
3. Tool Wear and Maintenance:
- The high hardness of SiC necessitates the use of specialized tools, such as diamond-coated tools, which are expensive and require frequent maintenance.
- Tool wear can significantly impact machining efficiency and surface finish.
4. Thermal Management:
- Machining SiC generates significant heat, which can lead to thermal stress and damage to the workpiece and cutting tool.
- Effective cooling strategies are crucial to mitigate thermal effects and maintain dimensional accuracy.
5. Chip Removal and Surface Finish:
- The brittle nature of SiC can result in the formation of sharp, jagged chips that can adhere to the tool or clog the cutting zone.
- Achieving a high-quality surface finish on SiC components can be challenging due to the risk of chipping and cracking.
6. Environmental Considerations:
- Machining SiC can generate fine particulate matter and hazardous fumes, necessitating proper ventilation and filtration systems to ensure a safe working environment.
To overcome these challenges, a combination of advanced machining techniques, specialized tooling, and careful process control is essential. Ongoing research and development in materials science and manufacturing technology are crucial to further improve the machinability of SiC ceramics and expand their applications.
Silicon Carbide Ceramics vs. Zirconia Ceramics: Which is the Best?
Silicon carbide (SiC) and zirconia (ZrO₂) ceramics are both high-performance materials with unique properties that make them suitable for a wide range of applications. To determine which material is “best” for a specific application, it’s essential to consider their comparative advantages and disadvantages.
Material Properties
Silicon Carbide (SiC):
- Mechanical Properties: High hardness, strength, and wear resistance.
- Thermal Properties: High thermal conductivity, excellent thermal shock resistance.
- Chemical Properties: High chemical stability, resistant to corrosion.
- Electrical Properties: Semiconductor properties, useful for electronic applications.
Zirconia (ZrO₂):
- Mechanical Properties: High toughness, excellent fracture toughness.
- Thermal Properties: Good thermal stability, moderate thermal conductivity.
- Chemical Properties: Good chemical resistance, particularly in alkaline environments.
- Electrical Properties: Primarily used as an insulator.
Applications
Silicon Carbide:
- Aerospace: Engine components, heat shields, and structural components.
- Automotive: Engine components, brake discs, and sensors.
- Electronics: Power electronics, semiconductors, and electronic packaging.
- Refractory Materials: Furnace linings, kiln furniture, and other high-temperature applications.
- Abrasives and Cutting Tools: Due to its hardness and wear resistance.
Zirconia:
- Dental Implants and Ceramics: Biocompatibility and aesthetic appeal.
- Cutting Tools: High toughness and wear resistance.
- Thermal Barrier Coatings: Protects components from high-temperature environments.
- Sensors: Oxygen sensors and other high-temperature sensors.
- Fuel Cells: Solid oxide fuel cells (SOFCs).
Property | Silicon Carbide (SiC) | Zirconia (ZrO₂) |
---|---|---|
Mechanical Properties | ||
Hardness | Very high | High |
Strength | High | High |
Toughness | Moderate | High |
Wear Resistance | Excellent | Good |
Thermal Properties | ||
Thermal Conductivity | High | Moderate |
Thermal Expansion Coefficient | Low | Low |
Thermal Shock Resistance | Excellent | Good |
Chemical Properties | ||
Chemical Resistance | Excellent | Good |
Oxidation Resistance | Excellent | Good |
Electrical Properties | ||
Electrical Conductivity | Semiconductor | Insulator |
Applications | ||
Aerospace | ✓ | ✓ |
Automotive | ✓ | ✓ |
Electronics | ✓ | ✓ |
Refractory Materials | ✓ | ✓ |
Cutting Tools | ✓ | ✓ |
Dental Implants | ✓ | |
Thermal Barrier Coatings | ✓ |
Key Differences and Considerations
- Hardness and Wear Resistance: SiC generally exhibits superior hardness and wear resistance, making it ideal for applications requiring high durability.
- Toughness: Zirconia often offers better toughness, making it suitable for applications where impact resistance is crucial.
- Thermal Conductivity: SiC has significantly higher thermal conductivity, making it ideal for heat dissipation in electronic and high-temperature applications.
- Cost: SiC can be more expensive than zirconia due to complex manufacturing processes.
In conclusion, the choice between SiC and zirconia ceramics depends on the specific requirements of the application. By carefully considering the properties and limitations of each material, engineers and designers can select the optimal material for their needs.
Note: While both materials offer excellent performance, the specific application will dictate the best choice. Consulting with materials engineers and considering factors like cost, availability, and processing techniques is crucial for making informed decisions
How is Silicon Carbide Ceramics Manufactured?
Silicon carbide (SiC) ceramics, renowned for their exceptional properties, require specialized manufacturing techniques to harness their full potential. Here’s a detailed breakdown of the key methods used to produce SiC ceramics:
1. Powder Synthesis
- Acheson Process: The traditional method involving the reaction of silica and carbon at high temperatures in an electric furnace.
- Carbothermal Reduction: A more modern approach where silica and carbon are reacted at high temperatures in a reducing atmosphere.
- Chemical Vapor Deposition (CVD): A high-purity method where SiC is deposited onto a substrate through a chemical reaction between gaseous precursors.
2. Powder Processing
- Powder Milling: SiC powder is milled to achieve the desired particle size distribution and surface area.
- Mixing and Blending: SiC powder is mixed with additives (if necessary) to obtain the desired properties.
- Powder Consolidation: Techniques like pressing, slip casting, or injection molding are used to shape the powder into the desired form.
3. Sintering
- Pressureless Sintering: SiC powder compacts are heated to high temperatures without external pressure to densify the material.
- Pressure Sintering (Hot Pressing): SiC powder is sintered under high pressure and temperature to achieve high density and improved mechanical properties.
- Spark Plasma Sintering (SPS): A rapid sintering technique that uses pulsed electric current to heat the powder compact, resulting in high-density and fine-grained SiC ceramics.
4. Machining and Finishing
- Machining: Due to SiC’s hardness and brittleness, specialized machining techniques like diamond grinding and electrical discharge machining (EDM) are employed.
- Polishing and Finishing: Polishing techniques are used to achieve desired surface finishes and optical properties.
5. Post-Processing
- Heat Treatment: Heat treatment processes, such as annealing and tempering, are used to improve the mechanical properties of SiC ceramics.
- Coating: Coatings can be applied to SiC ceramics to enhance their surface properties, such as wear resistance and corrosion resistance.
By carefully controlling each step of the manufacturing process, it’s possible to produce high-quality SiC ceramics with tailored properties for specific applications.
What is the Challenges in Machining Silicon Carbide Ceramics ?
Silicon carbide (SiC) ceramics, while offering exceptional properties, pose significant challenges during machining due to their inherent characteristics:
1. Extreme Hardness and Brittleness:
- Tool Wear: The high hardness of SiC leads to rapid tool wear, requiring frequent tool replacement and increasing processing costs.
- Fracture Risk: The brittleness of SiC makes it susceptible to cracking and chipping during machining operations, especially when subjected to high stresses.
2. Thermal Shock Resistance:
- SiC’s high thermal conductivity can lead to rapid temperature changes during machining, which can induce thermal stress and cause cracking.
- Effective cooling strategies are crucial to mitigate thermal shock and prevent damage to the workpiece.
3. Chemical Inertness:
- SiC’s chemical inertness limits the use of traditional chemical etching and polishing techniques.
- Specialized machining techniques, such as mechanical grinding and polishing, are often required.
4. Complex Shapes and Tolerances:
- Machining complex shapes and achieving tight tolerances in SiC can be challenging due to its hardness and brittleness.
- Advanced machining techniques and high-precision equipment are necessary to ensure accurate and efficient processing.
5. High Cost of Machining:
- The specialized tools, equipment, and expertise required for machining SiC can significantly increase the cost of production.
- The longer processing times and higher tool wear rates also contribute to higher costs.
To address these challenges, manufacturers often employ advanced machining techniques such as:
- Diamond Tooling: Diamond-tipped tools are commonly used to machine SiC due to their exceptional hardness.
- Electric Discharge Machining (EDM): EDM allows for precise machining of complex shapes without direct physical contact between the tool and workpiece.
- Ultrasonic Machining: This technique uses high-frequency vibrations to remove material, reducing the risk of thermal damage and improving surface finish.
- Laser Machining: Laser cutting and drilling can be used to create precise features in SiC components.
By carefully selecting the appropriate machining techniques and optimizing process parameters, it is possible to overcome these challenges and produce high-quality SiC components.
What is the Differences Between Silicon Carbide Ceramics and Graphite?
Silicon carbide (SiC) ceramics and graphite are two distinct materials with unique properties, making them suitable for various applications. While both materials have their strengths, they differ significantly in terms of structure, properties, and applications.
Structural Differences
- Silicon Carbide Ceramics: SiC ceramics have a crystalline structure with strong covalent bonds between silicon and carbon atoms. This structure results in exceptional hardness and high-temperature stability.
- Graphite: Graphite is an allotrope of carbon with a layered structure. Each layer consists of carbon atoms arranged in hexagonal rings, held together by weak van der Waals forces. This layered structure contributes to graphite’s excellent lubricity and electrical conductivity.
Property Comparison
Property | Silicon Carbide Ceramics | Graphite |
---|---|---|
Hardness | Extremely high | Low |
Electrical Conductivity | Insulator | Good conductor |
Thermal Conductivity | High | High (parallel to layers), low (perpendicular) |
Density | High | Low |
Oxidation Resistance | Excellent | Poor at high temperatures |
Corrosion Resistance | Excellent | Good, especially in acidic and alkaline environments |
Mechanical Properties
- Silicon Carbide Ceramics: High tensile and compressive strength, but low toughness and fracture toughness.
- Graphite: Low compressive strength but high tensile strength, especially in the direction parallel to the layers. High toughness and fracture toughness.
Applications
- Silicon Carbide Ceramics:
- High-temperature structural components (e.g., gas turbines, rocket nozzles)
- Abrasive materials (e.g., grinding wheels, cutting tools)
- Electronic components (e.g., semiconductors, power electronics)
- Graphite:
- Electrodes (e.g., batteries, fuel cells)
- Lubricants
- Refractory materials
- Nuclear reactors (as neutron moderators and control rods)
Key Differences
In summary, the primary differences between silicon carbide ceramics and graphite are:
- Structure: SiC ceramics have a crystalline structure, while graphite has a layered structure.
- Hardness: SiC ceramics are significantly harder than graphite.
- Electrical Conductivity: SiC ceramics are insulators, while graphite is a good conductor.
- Thermal Conductivity: Both materials have high thermal conductivity, but graphite’s conductivity varies with direction.
- Oxidation Resistance: SiC ceramics are highly resistant to oxidation, while graphite is susceptible to oxidation at high temperatures.
By understanding these differences, engineers and scientists can select the appropriate material for specific applications, leveraging their unique properties to optimize performance and durability.
What is the Impact of Color on Silicon Carbide Ceramics Performance?
Silicon carbide (SiC) ceramics are renowned for their exceptional mechanical properties, including high strength, hardness, and thermal stability. These attributes make them ideal for a variety of applications, such as wear-resistant components, cutting tools, and high-temperature environments.
Color Variations and Their Significance
The color of SiC ceramics can vary significantly, ranging from black to green or even white. This variation is primarily due to the purity of the raw materials used in the manufacturing process.
- Black Silicon Carbide: Produced from lower-purity raw materials, black SiC contains more impurities, which contribute to its darker color. While it may be suitable for applications where aesthetic considerations are less important, it generally exhibits lower mechanical properties compared to higher-purity variants.
- Green Silicon Carbide: Manufactured from higher-purity raw materials (typically 98-99% SiC), green SiC exhibits superior mechanical properties due to its reduced impurity content. The green color is a result of specific manufacturing conditions that favor the formation of certain crystalline structures.
Performance Implications
While color itself does not directly impact the performance of SiC ceramics, it serves as a valuable indicator of their quality and potential applications:
- Mechanical Properties: Higher-purity SiC, such as green SiC, typically exhibits superior hardness, wear resistance, and strength compared to lower-purity variants.
- Thermal Conductivity: Purer forms of SiC tend to have better thermal conductivity, enabling efficient heat dissipation in high-temperature applications.
- Chemical Stability: Higher-purity SiC is generally more chemically stable, making it suitable for harsh environments.
- Applications: The color of SiC ceramics can influence their selection for specific applications. For instance, green SiC might be preferred for high-performance applications demanding exceptional mechanical properties, while black SiC could be used in cost-sensitive applications where aesthetics are less critical.
Color as a Quality Indicator
In many industrial settings, the color of SiC ceramics can serve as a quick visual assessment tool to gauge material quality and grade before further testing or application.
Key Factors Influencing Color and Performance:
- Purity of Raw Materials: Higher purity leads to lighter colors and better performance.
- Production Process: The manufacturing process, including sintering temperature and atmosphere, can significantly affect the final color and properties.
- Doping Elements: Adding specific elements can alter the color and electronic properties of silicon carbide.
- Defects and Impurities: The presence of defects, such as vacancies or interstitial atoms, can influence both color and performance.
while color is a visual indicator of the quality and potential applications of silicon carbide ceramics, it’s essential to consider other factors, such as the specific manufacturing process, intended use, and desired properties. By carefully controlling these factors, manufacturers can produce silicon carbide ceramics with tailored properties to meet diverse industrial needs.
In conclusion: while color variations in SiC ceramics are primarily aesthetic, they can provide valuable insights into the material’s quality and suitability for specific applications. Understanding the relationship between color and performance allows for informed selection and optimization of SiC ceramics in various industries.
How to Enhancing the Fracture Toughness of Silicon Carbide Ceramics ?
Silicon carbide (SiC) ceramics, renowned for their exceptional mechanical properties, often suffer from a critical drawback: low fracture toughness. This limitation can restrict their applications, particularly in demanding environments. To overcome this challenge, researchers have explored various strategies to enhance the fracture toughness of SiC ceramics.
Material-Based Approaches
- Fiber Toughening:
- Reinforcement: Incorporating fibers, such as carbon or silicon carbide, into the SiC matrix can significantly improve toughness. These fibers act as crack barriers, deflecting and bridging cracks, thereby dissipating energy and preventing catastrophic failure.
- Particle Toughening:
- Dispersion: Dispersing ceramic or metal particles within the SiC matrix can create microstructural obstacles that impede crack propagation. These particles can induce crack deflection, branching, and bridging, leading to increased toughness.
Processing-Based Techniques
- Hot Pressing Sintering:
- Densification: By optimizing temperature, pressure, and holding time, hot pressing sintering promotes densification, reducing porosity and defects. This results in a more uniform microstructure and improved fracture toughness.
- Spark Plasma Sintering (SPS):
- Rapid Sintering: SPS offers rapid heating and sintering, allowing for lower processing temperatures and shorter cycle times. This can minimize thermal stresses and defects, enhancing the material’s toughness.
- In-Situ Synthesis:
- Strong Interfaces: In-situ synthesis of reinforcing phases within the SiC matrix results in strong interfacial bonding, promoting crack deflection and bridging. This approach can significantly improve fracture toughness.
Microstructure Engineering
- Whisker Toughening:
- Network Formation: Adding SiC whiskers to the matrix creates a three-dimensional network that hinders crack propagation. Additionally, mechanisms like whisker pull-out and debonding can absorb energy, further enhancing toughness.
- Nanocomposite Design:
- Enhanced Density and Crack Resistance: Incorporating nano-scale SiC particles into a micron-scale matrix can fill pores and create a denser microstructure. This refined structure can effectively impede crack growth.
Surface Modification Techniques
- Coating Technologies:
- Protective Layers: Applying protective coatings, such as metal or ceramic coatings, to the SiC surface can relieve stress concentrations and improve crack resistance.
- Prestress:
- Compressive Stress: Introducing residual compressive stress through thermal treatments can offset tensile stresses, delaying crack initiation and propagation.
Methods to Enhance the Fracture Toughness of Silicon Carbide Ceramics
Method | Description |
---|---|
Material-Based Approaches | |
Fiber Toughening | Incorporating fibers (e.g., carbon, SiC) to deflect and bridge cracks. |
Particle Toughening | Dispersing ceramic or metal particles to induce crack deflection and branching. |
Processing-Based Techniques | |
Hot Pressing Sintering | Promoting densification to reduce porosity and defects. |
Spark Plasma Sintering (SPS) | Rapid sintering to minimize thermal stresses and defects. |
In-Situ Synthesis | Generating reinforcing phases with strong interfacial bonding. |
Microstructure Engineering | |
Whisker Toughening | Creating a 3D network to hinder crack propagation. |
Nanocomposite Design | Enhancing density and crack resistance through nano-scale reinforcements. |
Surface Modification Techniques | |
Coating Technologies | Applying protective coatings to relieve stress concentrations. |
Prestress | Introducing residual compressive stress to delay crack initiation. |
By carefully selecting and combining these techniques, researchers and engineers can significantly improve the fracture toughness of SiC ceramics, expanding their potential applications in demanding environments.
Hot Isostatic Pressing (HIP) and Its Impact on Silicon Carbide Ceramics
Hot Isostatic Pressing (HIP) is a specialized technique employed to enhance the properties of ceramic materials, including silicon carbide (SiC). By subjecting the material to high temperatures and pressures, HIP significantly improves the microstructure and mechanical properties of SiC ceramics.
Key Benefits of HIP on Silicon Carbide Ceramics:
Density Improvement
- Reduced Porosity: HIP effectively eliminates porosity within the SiC microstructure, leading to a denser material.
- Enhanced Mechanical Properties: Increased density translates to improved mechanical properties such as higher strength, hardness, and toughness.
Microstructural Refinement
- Grain Growth and Refinement: HIP promotes the growth and refinement of grains within the SiC microstructure.
- Improved Fracture Toughness: A finer-grained microstructure enhances fracture toughness by impeding crack propagation.
Mechanical Property Enhancement
- Increased Strength and Hardness: HIPed SiC exhibits significantly higher flexural strength and hardness compared to non-HIPed counterparts.
- Improved Wear Resistance: Reduced porosity and refined microstructure contribute to superior wear resistance.
- Enhanced Thermal Shock Resistance: HIPed SiC can withstand rapid temperature changes without fracturing.
Thermal Conductivity Improvement
- Reduced Thermal Resistance: The elimination of porosity lowers thermal resistance, leading to improved thermal conductivity.
- Enhanced Heat Dissipation: Efficient heat dissipation is crucial for high-performance applications.
Chemical Resistance Enhancement
- Homogeneous Microstructure: HIP creates a more homogeneous microstructure, reducing the susceptibility to chemical attack and degradation.
- Improved Durability in Harsh Environments: HIPed SiC can withstand harsh chemical environments.
Cost Considerations: While HIP is a relatively expensive process, the significant improvements in the properties of SiC ceramics often justify the cost for critical applications where reliability and performance are paramount.
Key Benefits of HIP on Silicon Carbide Ceramics:
Property | Effect of HIP |
---|---|
Density | Increased density by up to 5%, reduced porosity |
Microstructure | Grain size reduced by 30-50%, more uniform microstructure |
Mechanical Properties | Improved flexural strength by 20-30%, hardness by 10-15%, toughness by 25-35%, and wear resistance by 40-50% |
Thermal Conductivity | Enhanced thermal conductivity by 10-15% due to reduced porosity |
Chemical Resistance | Improved chemical resistance by 20-30% due to homogeneous microstructur |
By leveraging the benefits of HIP, silicon carbide ceramics can be tailored to meet the demanding requirements of various industries, including aerospace, automotive, electronics, and industrial manufacturing.
What is The Surface Treatment Methods of Silicon Carbide Ceramics?
Silicon carbide ceramics, renowned for their exceptional hardness and durability, pose significant challenges in surface treatment due to their unique properties:
Challenges in Surface Treatment
- High Hardness: The extreme hardness of silicon carbide ceramics, with a Mohs hardness of 9.5, makes traditional mechanical processing techniques inefficient and tool-intensive.
- Brittleness: The material’s brittleness necessitates careful control of processing parameters to prevent cracking and breakage.
- Thermal Stability: High temperatures can lead to oxidation and decomposition, requiring precise temperature control during processing.
- High Precision Requirements: Many applications, such as optics and semiconductors, demand precise surface finishes and tolerances.
Common Surface Treatment Methods
To address these challenges, various surface treatment techniques have been developed:
Mechanical Processing
- Grinding: Using diamond or cubic boron nitride grinding wheels to remove material and improve surface finish.
- Advantages: High material removal rate, good surface quality.
- Disadvantages: Tool wear, potential for thermal damage.
- Polishing: Employing mechanical, chemical, or electrochemical methods to achieve high-gloss surfaces.
- Mechanical Polishing: Using polishing pads and abrasive slurries.
- Chemical Polishing: Using chemical etchants to dissolve the surface layer.
- Electrochemical Polishing: Using an electrochemical cell to dissolve the surface layer.
- Sandblasting: Using high-speed abrasive particles to clean, roughen, or shape the surface.
- Advantages: Effective for removing surface contaminants and creating desired surface textures.
- Disadvantages: Potential for surface damage, especially at high pressures.
Physical and Chemical Processes
- Laser Processing: Utilizing high-energy laser beams for precise cutting, drilling, and etching.
- Advantages: High precision, minimal heat-affected zone, flexible processing capabilities.
- Disadvantages: High equipment cost, potential for thermal damage.
- Chemical Vapor Deposition (CVD): Depositing a thin film of silicon carbide to enhance surface properties like wear resistance and corrosion resistance.
- Advantages: Precise control of film thickness and composition, excellent adhesion to the substrate.
- Disadvantages: Complex equipment and process, high energy consumption.
- Anodic Oxidation: Forming an oxide layer on the surface of metal-containing silicon carbide composites to improve corrosion resistance.
- Advantages: Simple process, low cost.
- Disadvantages: Limited applicability to metal-containing composites.
- Micro-Arc Oxidation: Creating a ceramic oxide coating on the surface to enhance wear resistance and corrosion resistance.
- Advantages: Thick, durable coating, good corrosion and wear resistance.
- Disadvantages: Complex equipment, high energy consumption.
Common Surface Treatment Methods
Method | Description | Advantages | Disadvantages |
---|---|---|---|
Mechanical Processing | |||
Grinding | Using abrasive tools to remove material | High material removal rate, good surface finish | Tool wear, potential for thermal damage |
Polishing | Using mechanical, chemical, or electrochemical methods to achieve high-gloss surfaces | Improved surface finish, reduced friction | Time-consuming, potential for surface damage |
Sandblasting | Using high-speed abrasive particles to clean, roughen, or shape the surface | Effective cleaning, surface texturing | Potential for surface damage, environmental concerns |
Physical and Chemical Processes | |||
Laser Processing | Using high-energy laser beams for precise cutting, drilling, and etching | High precision, minimal heat-affected zone | High equipment cost, potential for thermal damage |
Chemical Vapor Deposition (CVD) | Depositing a thin film of silicon carbide to enhance surface properties | Precise control of film thickness and composition, excellent adhesion | Complex equipment and process, high energy consumption |
Anodic Oxidation | Forming an oxide layer on the surface of metal-containing silicon carbide composites | Simple process, low cost | Limited applicability to metal-containing composites |
Micro-Arc Oxidation | Creating a ceramic oxide coating on the surface to enhance wear resistance and corrosion resistance | Thick, durable coating, good corrosion and wear resistance | Complex equipment, high energy consumption |
By carefully selecting and optimizing these surface treatment techniques, it is possible to effectively process silicon carbide ceramics and realize their full potential in a wide range of applications.
What is the Expected Lifespan of Silicon Carbide Ceramics?
The expected lifespan of silicon carbide ceramics under operational conditions can vary significantly depending on several factors:
1. Operating Environment:
- Temperature: Higher temperatures can accelerate degradation processes, such as oxidation and creep.
- Stress: Mechanical stress, whether cyclic or static, can induce fatigue and fracture.
- Chemical Exposure: Exposure to aggressive chemicals can corrode the ceramic surface.
2. Material Quality:
- Purity: Higher purity SiC ceramics generally exhibit better long-term performance.
- Microstructure: The microstructure, including grain size, porosity, and phase distribution, can influence the material’s durability.
3. Design and Manufacturing:
- Component Design: Proper design can minimize stress concentrations and improve the component’s lifespan.
- Manufacturing Process: Careful control of manufacturing processes can ensure consistent quality and reliability.
Typical Lifespans:
While it’s difficult to provide a specific lifespan without considering the specific application and operating conditions, SiC ceramics can exhibit remarkably long lifespans under optimal conditions. In some cases, they can last for decades. However, in harsh environments with high temperatures and mechanical stresses, the lifespan may be shorter.The below is Specific Applications and Lifespans fore reference:
Application | Lifespan Factors | Typical Lifespan |
---|---|---|
High-Temperature Industrial Applications (e.g., kiln rollers, linings) | Temperature, mechanical stress, chemical exposure | Several years to a decade |
Mechanical Seals | Temperature, pressure, lubrication, contaminant presence | Tens of thousands of hours to a few thousand hours |
Semiconductor Manufacturing Equipment | High-cleanliness environment, precision requirements | 5-10 years or more, depending on maintenance and replacement |
Bulletproof Armor | Impact resistance, wear resistance | Varies based on usage intensity and impact severity |
Factors Affecting Lifespan:
- Oxidation: At high temperatures, SiC can oxidize, forming a protective silica layer. However, excessive oxidation can lead to degradation.
- Thermal Shock Resistance: Rapid temperature changes can cause thermal shock, leading to cracking and failure.
- Creep: At high temperatures and stresses, SiC can undergo slow deformation, which can affect its structural integrity over time.
By carefully considering these factors and optimizing the design, manufacturing, and operational conditions, it is possible to maximize the lifespan of silicon carbide ceramics.
What is The Difference Between Silicon Carbide Ceramics and Alumina Ceramics?
Both silicon carbide and alumina ceramics are advanced ceramics .They offer excellent mechanical properties, high-temperature resistance, chemical resistance, and electrical insulation. But heir specific properties and applications vary.Here’s a breakdown of the key differences between silicon carbide ceramics and alumina ceramics:
1. Chemical Composition and Structure
- Silicon Carbide: Primarily composed of silicon (Si) and carbon (C), forming a strong covalent bond structure.
- Alumina: Mainly composed of aluminum oxide (Al₂O₃), an ionic compound.
2. Physical Properties
- 2.1 Hardness:
- Silicon Carbide: Extremely hard, second only to diamond (Mohs hardness of ~9.5).
- Alumina: Very hard, but slightly less than silicon carbide (Mohs hardness of ~9).
- 2.2 Density:
- Silicon Carbide: Lower density, making it lighter.
- Alumina: Higher density (around 3.5 – 4.0 g/cm³).
- 2.3 Thermal Conductivity:
- Silicon Carbide: High thermal conductivity, excellent for heat dissipation (typically 80 – 270 W/(m・K)).
- Alumina: Lower thermal conductivity (around 20 – 30 W/(m・K)).
- 2.4 Color:
- Silicon Carbide: Typically black or green, depending on impurities and processing.
- Alumina: Usually white, but can be varied with additives.
3. Mechanical Properties
- 3.1 Strength:
- Silicon Carbide: High flexural strength (400 – 700 MPa) and compressive strength, maintaining strength at high temperatures.
- Alumina: High strength, but generally lower than silicon carbide (flexural strength of 300 – 500 MPa).
- 3.2 Toughness:
- Silicon Carbide: Low toughness, prone to brittle failure.
- Alumina: Low toughness, but may be slightly more resistant to impact than silicon carbide in certain applications.
4. Chemical Properties
- 4.1 Corrosion Resistance:
- Silicon Carbide: Excellent resistance to acids, alkalis, and high-temperature environments.
- Alumina: Good corrosion resistance, particularly in acidic and neutral environments; weaker in strong alkaline conditions.
- 4.2 Oxidation Resistance:
- Silicon Carbide: Excellent oxidation resistance, forming a protective silica layer at high temperatures.
- Alumina: Good oxidation resistance, inherently stable as an oxide.
5. Production Processes
- Silicon Carbide:
- 5.1 Hot pressing: High density and strength, suitable for simple shapes and high precision.
- 5.2 Sintering: Suitable for complex shapes and large sizes.
- 5.3 Bonding: Can create complex shapes, but lower strength and density.
- 5.4 Spraying: Forms a ceramic protective layer or coating.
- Alumina:
- 5.5 Dry pressing: Versatile method for various shapes.
- 5.6 Grouting: Used for complex shapes.
- 5.7 Extrusion: Creates long, uniform shapes.
- 5.8 Cold isostatic pressing: Produces high-density parts.
- 5.9 Injection molding: Suitable for intricate designs.
- 5.10 Casting: Used for large or complex shapes.
6. Application Areas
- Silicon Carbide:
- 6.1 High-temperature applications: Bearings, heat exchangers, furnace components.
- 6.2 Wear-resistant parts: Nozzles, seals, pump components.
- 6.3 Electronic components: Semiconductors, high-frequency devices.
- 6.4 Cutting tools: Abrasives, grinding wheels.
- 6.5 Armor: Bulletproof plates.
- Alumina:
- 6.6 Electronic components: Insulators, substrates, packages.
- 6.7 Electrical insulators: Spark plugs, high-voltage components.
- 6.8 Refractory materials: Furnace linings, crucibles.
- 6.9 Abrasives: Grinding wheels, polishing compounds.
- 6.10 Cutting tools: Inserts, tool bits.
Silicon Carbide Ceramics vs. Alumina Ceramics: A Detailed Comparison
Property | Silicon Carbide | Alumina |
---|---|---|
Chemical Composition | SiC | Al₂O₃ |
Structure | Covalent | Ionic |
Hardness (Mohs) | ~9.5 | ~9 |
Density (g/cm³) | Lower | 3.5-4.0 |
Thermal Conductivity (W/mK) | 80-270 | 20-30 |
Color | Black or Green | White (can be varied) |
Flexural Strength (MPa) | 400-700 | 300-500 |
Toughness | Low | Low |
Acid Resistance | Excellent | Good |
Base Resistance | Excellent | Weak |
Oxidation Resistance | Excellent | Good |
Production Processes | Hot pressing, sintering, bonding, spraying | Dry pressing, grouting, extrusion, cold isostatic pressing, injection, casting |
Applications | High-temperature applications, wear-resistant parts, electronic components, cutting tools, armor | Electronic components, electrical insulators, refractory materials, abrasives, cutting tools |
Key Differences and Considerations:
Silicon Carbide:
- Exceptionally hard and wear-resistant.
- Excellent thermal conductivity for heat dissipation.
- High strength, especially at elevated temperatures.
- Superior chemical resistance to acids and bases.
- Well-suited for high-temperature and corrosive environments.
- More complex manufacturing processes.
Alumina:
- Very hard and durable.
- Good electrical insulator.
- Excellent chemical resistance to acids.
- Versatile and widely used in various applications.
- More established and cost-effective manufacturing processes.
Choosing the Right Ceramic:
The selection between silicon carbide and alumina ceramics depends on the specific requirements of the application. Consider factors such as:
- Temperature: Silicon carbide is superior for high-temperature applications.
- Wear resistance: Silicon carbide offers exceptional wear resistance.
- Chemical resistance: Both materials are generally resistant to acids, but silicon carbide excels in alkaline environments.
- Electrical properties: Alumina is a better electrical insulator.
- Mechanical strength: Both materials offer high strength, but silicon carbide may have an edge at high temperatures.
- Cost: Alumina is generally more cost-effective to produce.
Conclusion:The choice between silicon carbide and alumina depends on the specific requirements of the application. By carefully considering factors such as temperature, wear resistance, chemical resistance, electrical properties, and cost, engineers and designers can select the optimal ceramic material for their needs.
What are the Silicon Carbide Ceramic Sintering Technologies ?
Silicon carbide (SiC) ceramics, renowned for their exceptional properties, require precise sintering techniques to achieve optimal performance. Here’s a detailed overview of nine prominent sintering methods:
Traditional Techniques:
Hot Pressing:
- Combines heat and pressure to densify SiC powder compacts.
- Results in high-density, high-strength materials.
- Limited to simple shapes due to complex tooling.
Reaction Sintering:
- Involves mixing SiC powder with a carbon source and heating to form β-SiC in situ.
- Low-cost and energy-efficient method for large components.
- Limited control over microstructure and properties.
Pressureless Sintering:
- Densification occurs at high temperatures without external pressure.
- Solid-state sintering: High density, but potential for excessive grain growth.
- Liquid-phase sintering: Lower sintering temperatures, improved mechanical properties.
Advanced Techniques:
Recrystallization Sintering:
- Evaporative-condensation mechanism for densification.
- Controlled porosity and microstructure.
- High-temperature process, limiting its applicability.
Spark Plasma Sintering (SPS):
- Rapid heating and densification using pulsed electric currents.
- Preservation of fine microstructures.
- High energy consumption and equipment complexity.
Flash Sintering:
- Electric field-induced rapid densification.
- Reduced energy consumption and processing time.
- Requires precise control of electrical parameters.
Innovative Techniques:
Oscillatory Pressure Sintering:
- Enhanced densification through cyclic pressure application.
- Improved microstructure and mechanical properties.
- Complex equipment and process control.
Microwave-Assisted Sintering:
- Uniform heating and rapid densification using microwave energy.
- Reduced processing time and energy consumption.
- Limited to specific microwave-susceptible materials.
Hot Isostatic Pressing (HIP) Sintering
- Process: Sintering SiC powders under high pressure and temperature in an inert gas environment.
- Advantages: High density, uniform microstructure, improved mechanical properties.
- Disadvantages: High equipment cost, complex process.
Nine Prominent Sintering Techniques for Silicon Carbide Ceramics
Technique | Description | Advantages | Disadvantages |
---|---|---|---|
Hot Pressing | Heat and pressure densify SiC powder compacts. | High density, high strength | Complex equipment, high energy consumption, limited shape complexity |
Reaction Sintering | SiC powder reacts with carbon source to form β-SiC. | Low cost, energy-efficient, suitable for large components | Limited control over microstructure, lower strength |
Pressureless Sintering | Densification without external pressure. | Solid-state: high density; Liquid-phase: lower sintering temperature, improved properties | Solid-state: potential for excessive grain growth |
Recrystallization Sintering | Evaporation-condensation densification. | Controlled porosity and microstructure | High-temperature process, limited applicability |
Spark Plasma Sintering (SPS) | Pulsed electric current for rapid heating and densification. | Preserves fine microstructures, enhanced properties | High energy consumption, complex equipment |
Flash Sintering | Electric field-induced rapid densification. | Reduced energy consumption and processing time | Requires precise control of electrical parameters |
Oscillatory Pressure Sintering | Cyclic pressure application for enhanced densification. | Improved microstructure and mechanical properties | Complex equipment and process control |
Microwave-Assisted Sintering | Microwave energy for uniform heating and rapid densification. | Reduced processing time and energy consumption | Limited to microwave-susceptible materials |
Hot Isostatic Pressing (HIP) Sintering | Sintering SiC powders under high pressure and temperature in an inert gas environment. | High density, uniform microstructure, improved mechanical properties. | High equipment cost, complex process. |
The three most commonly used methods for sintering silicon carbide ceramics in industrial production are reaction sintering, pressureless sintering and recrystallization sintering.
By understanding these techniques and their specific advantages and disadvantages, researchers and engineers can select the optimal sintering process to produce SiC ceramics with tailored properties for various applications.
Which Countries Leading in Silicon Carbide Ceramic Production?
Silicon carbide ceramic production is a complex and highly specialized field, with several countries leading the way in different aspects of the industry. Here’s a look at some of the key players:
China:
- Advantages: China boasts the largest production capacity for silicon carbide ceramics globally, driven by its abundant raw material resources, low labor costs, and strong government support for the industry.
- Focus: China primarily produces lower-end silicon carbide products for applications like abrasives and refractories. However, the country is rapidly investing in research and development to expand its production capabilities for higher-end applications.
United States:
- Advantages: The United States is a pioneer in silicon carbide technology, with a strong emphasis on research and development. The country has a well-established industrial base and a skilled workforce, enabling it to produce high-quality silicon carbide ceramics.
- Focus: The US specializes in producing high-performance silicon carbide ceramics for demanding applications such as aerospace, automotive, and electronics.
Europe:
- Advantages: European countries, particularly Germany and France, have a long history of ceramic production and a strong focus on innovation. They possess advanced manufacturing technologies and a skilled workforce, allowing them to produce high-quality silicon carbide ceramics.
- Focus: European countries excel in producing high-value-added silicon carbide products, including advanced ceramics for semiconductor manufacturing and high-temperature applications.
Japan:
- Advantages: Japan has a strong reputation for precision engineering and materials science. The country has a well-developed industrial infrastructure and a highly skilled workforce, enabling it to produce high-quality silicon carbide ceramics.
- Focus: Japan specializes in producing high-purity silicon carbide powders and advanced ceramic components for electronic and automotive applications.
Other Notable Countries:
- South Korea: A rapidly emerging player in the silicon carbide industry, South Korea is investing heavily in research and development to improve its production capabilities.
- Russia: Possesses significant reserves of raw materials and a strong tradition in materials science, making it a potential player in the silicon carbide market.
Here is a table combining countries, advantages, and their leading companies in silicon carbide ceramic production:
Country | Advantages | Companies |
---|---|---|
China | Largest production capacity, abundant resources, low labor costs | Yomua,Kyocera |
United States | Strong R&D, high-quality products, established industrial base | Saint-Gobain, CeramTec |
Europe | Long history of ceramics, advanced technologies, skilled workforce | SGL Carbon, Saint-Gobain |
Japan | Precision engineering, high-purity materials, strong infrastructure | NGK Spark Plug, Kyocera |
South Korea | Rapidly emerging, heavy investment in R&D | LG Innotek |
Russia | Significant raw materials, strong materials science tradition | Nizhny Novgorod Silicon Carbide Plant |
It’s important to note that the silicon carbide industry is constantly evolving, with new players emerging and existing players expanding their capabilities. The future of the industry will likely be shaped by factors such as technological advancements, increasing demand for high-performance materials, and geopolitical shifts.
What is The Future Trends of Silicon Carbide Ceramics?
Silicon carbide (SiC) ceramics are poised to revolutionize various industries due to their exceptional properties. Let’s delve into the key trends driving the growth of this remarkable material:
Technological Advancements
- Enhanced Manufacturing Processes: Innovations in sintering techniques have led to a 20% improvement in the mechanical strength and thermal conductivity of SiC ceramics.
- Advanced Formulations: New formulations incorporating carbon nanotubes and graphene have increased the thermal conductivity of SiC by 30%.
Growing Demand Across Industries
- Automotive: The electric vehicle (EV) market is experiencing a 25% annual growth rate. SiC power electronics are crucial for improving EV efficiency and range.
- Aerospace: The aerospace industry is adopting SiC components for high-temperature applications, leading to a 15% reduction in aircraft weight and fuel consumption.
- Electronics: SiC-based power devices are enabling more efficient and compact power systems, with a projected 20% increase in power density.
- Industrial Manufacturing: SiC is used in cutting tools, grinding wheels, and other industrial applications due to its exceptional hardness and wear resistance, leading to increased productivity and reduced downtime.
- Data Centers: SiC power electronics are used in data centers to improve energy efficiency and reduce cooling costs.
- Renewable Energy: SiC-based power electronics are used in solar inverters and wind turbines to improve efficiency and reliability.
Growing Demand Across Industries
Industry | Application | Impact |
---|---|---|
Automotive | Power electronics for EVs | Improved efficiency by 25% and increased range |
Aerospace | High-temperature components | Reduced weight by 15% and fuel consumption |
Electronics | Power devices | Increased power density by 20% and efficiency |
Industrial Manufacturing | Cutting tools, grinding wheels | Improved productivity by 20% and reduced downtime |
Data Centers | Power electronics | Improved energy efficiency by 15% and reduced cooling costs |
Renewable Energy | Solar inverters, wind turbines | Increased efficiency and reliability by 10% |
Policy Support and Investment
Governments worldwide are investing heavily in clean energy technologies, with a $50 billion annual global investment in renewable energy research and development. This funding is accelerating the adoption of SiC-based solutions.
Expansion into New Applications
- Medical Devices: SiC ceramics are being explored for use in orthopedic implants and dental restorations due to their biocompatibility and wear resistance.
- Defense: SiC is used in advanced armor systems and high-performance engine components for military applications.
Market Growth Projections
The global market for SiC ceramics is projected to reach $5 billion by 2025, with a 10% compound annual growth rate (CAGR).
Trend | Impact |
---|---|
Technological Advancements | Improved performance and efficiency by 20-30% |
Growing Demand | Increased adoption across various industries by 25-35% |
Policy Support and Investment | Accelerated development and commercialization by 10-15% |
Expansion into New Applications | Diversification of market opportunities by 15-20% |
Market Growth Projections | Significant market growth and revenue generation by 10-15% annually |
Table: Key Trends Driving the Growth of Silicon Carbide Ceramics
In conclusion, silicon carbide ceramics are set to play a pivotal role in shaping the future of technology and industry. Their exceptional properties, coupled with ongoing advancements and growing demand, make them a promising material with far-reaching implications.
Silicon Carbide Ceramics Conclusion
Silicon carbide ceramics have emerged as a critical material in modern technology, offering exceptional properties that are driving innovation across various industries. With its unique combination of high strength, hardness, thermal shock resistance, and excellent electrical properties, silicon carbide is revolutionizing fields such as automotive, aerospace, electronics, and industrial manufacturing.Yomua is committed to advancing the production of silicon carbide ceramics. By continuously exploring and implementing cutting-edge technologies, we aim to optimize our manufacturing processes and deliver superior quality products. We are dedicated to tailoring our silicon carbide ceramics to meet the specific needs of our customers, ensuring optimal performance and reliability.