Aluminum Nitride (AlN) Ceramics Components
Precision Manufacturing: 40 Years of Excellence
- Producing both small and large batches of parts
- Focus on quick turnaround times
- Strict quality control
- Team of expert engineers and technicians.
Get a Quote Today
Aluminum Nitride (AlN) Ceramics Components Leading Manufacturer
WHy Yomua Aluminum Nitride (AlN) Ceramics
- 40 Years of Rich Manufacturing: Our advanced manufacturing techniques enable us to achieve the tightest tolerances and the most intricate surface finishes more than four decades.
- Dedicated Engineering Team: Our team of experienced engineers, with decades of combined experience in AlN materials science and manufacturing, drives innovation and ensures consistent quality in every project.
- Rigorous Standards: We adhere to a rigorous quality control system that encompasses every stage of the manufacturing process, from raw material inspection to final product testing.
- Fast Turnaround: We prioritize prompt delivery to minimize your project timelines and accelerate your time-to-market.
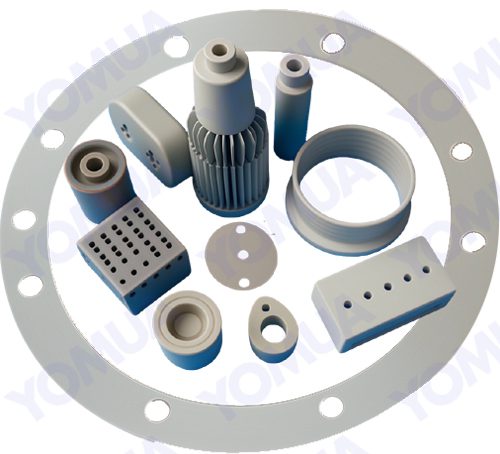
Custom ManufacturingAluminum Nitride (AlN) Ceramics Components
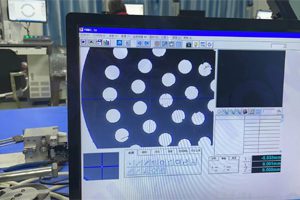
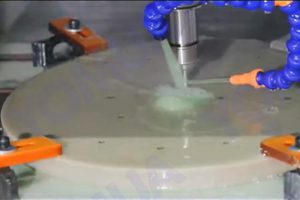
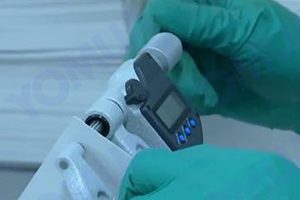
- Reliable Support: Our dedicated after-sales service team provides ongoing support and assistance to ensure your continued success. We are readily available to address any questions or concerns you may have, provide technical guidance, and assist with any post-delivery requirements.
Aluminum Nitride (AlN) Properties
Property Sort | Property Content | Unit | Property Index |
Basic Properties | Appearance/color | – | Gray |
Water absorption | % | 0 | |
Volume density | g/cm3 | ≥ 3.30 | |
Surface roughness | µm | 0.3-0.6 | |
Camber | (length %) | <2% | |
Thermal Properties | Thermal conductivity (30°C) | W/m.k | ≥180 |
Thermal expansivity (20°C-300°C) | (×10-6/°C) | 4.4 | |
Thermal expansivity (300°C-800°C) | (×10-6/°C) | 4.8 | |
Mechanical Properties | Flexural strength | MPa | ≥450 |
Modulus of elasticity | GPa | 320 | |
Moh’s hardness | – | 8 | |
Electrical Properties | Dielectric constant | – | 8.9 |
Dielectric loss | ×10-4 | 2.8 | |
Dielectric strength | KV/mm | ≥17 | |
Volume resistivity | Ω.cm | ≥1014 |
Note: Data provided is for general guidance only. Actual material properties may exhibit variation depending on specific products. More information ,please contact Yomua.
Aluminum Nitride (AlN) Ceramics Products
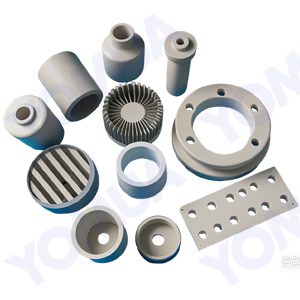
Customized Aluminum Nitride (AlN) Ceramics Parts
Yomua custom AlN ceramic manufacturing fulfills your unique needs by providing high-quality, made-to-order ceramic components.
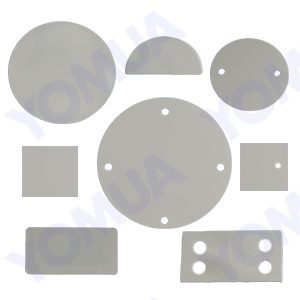
Aluminum Nitride (AlN) Ceramic Substrate
Aluminum Nitride (AlN) Ceramic Substrate is a ceramic known for its highest thermal conductivity, excellent electrical insulation, and low thermal expansion.
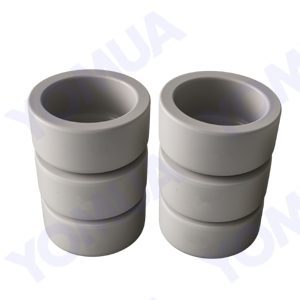
Aluminum Nitride (AlN) Ceramic Crucibles
High thermal conductivity AlN crucible, ideal for high-temperature applications, minimizes heat loss, improves process efficiency.
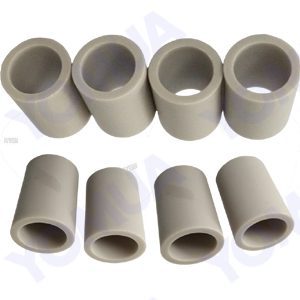
Aluminum Nitride (AlN) Ceramic Pipes
Aluminum Nitride ceramic pipes exhibit high thermal conductivity, electrical insulation, and corrosion resistance, ideal for many applications.
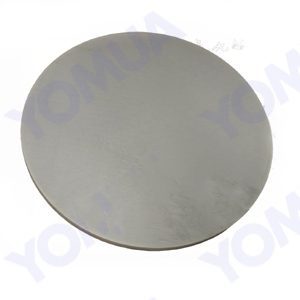
Aluminum Nitride (AlN) Ceramic Plate
Aluminum Nitride (AlN) ceramic disks are utilized in semiconductor manufacturing equipment because of the thermal and electrical properties.
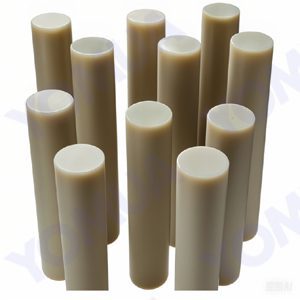
Aluminum Nitride (AlN) Ceramic Rod
Aluminum nitride (AlN) ceramic rods are versatile materials that combine high thermal conductivity with excellent electrical insulation properties.
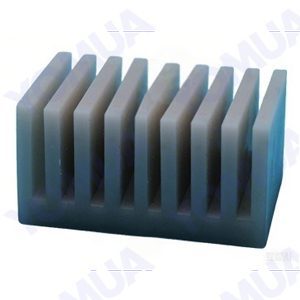
Aluminum Nitride (AlN) Ceramic Heat Sink
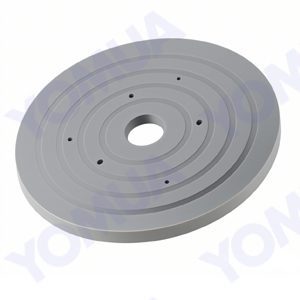
Aluminum Nitride (AlN) Ceramic Heater Substrate
deal for semiconductor manufacturing, vacuum evaporation, sputtering, and CVD, due to their high thermal conductivity and electrical insulation.
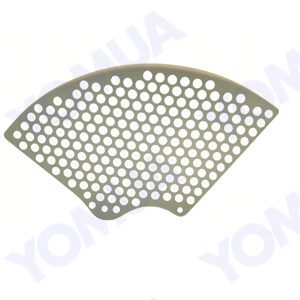
Porous Aluminum Nitride (AlN) Ceramic Parts
Porous Aluminum Nitride ceramic parts leverage the beneficial properties of aluminum nitride while introducing unique advantages through controlled porosity.

Aluminum Nitride (AlN) Ceramic Washer
Aluminum Nitride (AlN) Ceramic Washer is utilized in various electronic applications where heat management and electrical isolation are critical.
Reviews for Aluminum Nitride (AlN) Ceramics ....

Developing Customer Happiness with Yomua



Aluminum Nitride (AlN) Ceramics Related Products
Silicon-nitrogen compound,Strong, durable, and heat-resistant ceramic
Highly durable industrial ceramic, known for its hardness and wear resistance
Extremely hard ceramic, high thermal conductivity, excellent wear resistance
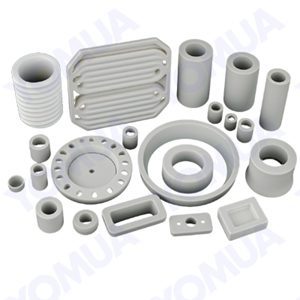
Boron Nitride(BN) Ceramics
Excellent thermal conductivity, high electrical resistivity, and chemical inertness
Aluminum Nitride (AlN) Ceramics Components Guide
This in-depth guide is designed to equip engineers, purchasing persons ,designers, and material scientists with a thorough understanding of Aluminum Nitride Ceramics (AlN). It provides comprehensive information to empower users to effectively leverage the unique properties of AlN and drive innovation across a wide range of industries.
Frequently Asked Questions
What is Aluminum Nitride or ALN ?
Aluminum nitride (AlN) is a solid nitride compound composed of aluminum and nitrogen. It is notable for its high thermal conductivity, which can reach up to 321 W/(m·K), making it an excellent material for applications requiring efficient heat dissipation. AlN is also an electrical insulator, with pure AlN exhibiting very low electrical conductivity in the range of 10^(-11) to 10^(-13) Ω^(-1)·cm^(-1). When doped, this conductivity can increase significantly.
- Chemical Formula: AlN
- CAS Registry Number: 2428-09-5
- PubChem Compound ID: 14774
- SMILES Identifier: [Al]#[N]
- Appearance: White to gray powder or transparent crystals
- Density: 3.26 g/cm³
- Melting Point: 2,200 °C (3,990 °F)
- Crystal Structure:
- Wurtzite: The most common structure, characterized by a hexagonal lattice with alternating layers of aluminum and nitrogen atoms. Each atom is tetrahedrally coordinated.
- Zincblende: A metastable cubic structure, often found in thin film applications. This structure also exhibits tetrahedral coordination.
What is Aluminum Nitride Ceramic or ALN Ceramic?
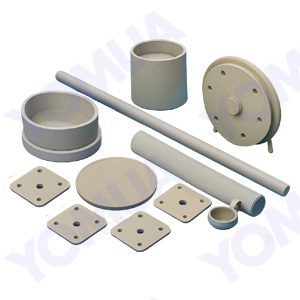
Aluminum nitride (AlN) ceramic is a non-oxide ceramic material primarily composed of aluminum and nitrogen, with the chemical formula AlN. It is recognized for its exceptional thermal conductivity and electrical insulation properties, making it a valuable material in various industrial applications.
Chemical Composition and Structure
- Chemical Formula: AlN
- Composition: Approximately 65.81% aluminum and 34.19% nitrogen by weight.
- Crystal Structure:AIN crystals use 〔AIN〕tetrahedron as structural unit, belong to hexagonal system, have wurtzite structure, and are covalent bond compounds. Its appearance is usually white or off-white with a slight bluish tint. Single crystals are colorless and transparent. The sublimation decomposition temperature under normal pressure is 2450℃, and the specific gravity is 3.261g/cm³.
What are the Properties of Aluminum Nitride Ceramic or ALN Ceramic?
Aluminum Nitride (AlN) ceramic is a high-performance material with a unique combination of properties that make it invaluable in various industrial applications.
Key Properties:
- High Thermal Conductivity: AlN excels at conducting heat, making it ideal for thermal management applications. This property is crucial for dissipating heat in electronic devices and preventing overheating.
- Excellent Electrical Insulation: AlN is an excellent electrical insulator, meaning it can withstand high voltages without conducting electricity. This property is essential in various electronic components and high-voltage applications.
- Low Thermal Expansion: AlN has a low coefficient of thermal expansion, which means it expands and contracts minimally with temperature changes. This property is important for maintaining dimensional stability in electronic devices.
- Good Mechanical Strength: AlN possesses good mechanical strength, making it durable and resistant to mechanical stress.
- Chemical Resistance: AlN exhibits resistance to chemical corrosion, making it suitable for use in harsh environments.
- Stability at High Temperatures: AlN can withstand high temperatures without significant degradation, ensuring its reliability in demanding applications.
Additional Properties:
- Non-Toxic: Unlike some other high-performance ceramics, AlN is non-toxic, making it safer to handle and process.
- Machinability: AlN can be machined with precision, allowing for complex shapes and designs.
- Metallization Compatibility: AlN can be metallized, enabling the integration of electronic components onto its surface.
In Conclusion:
The unique combination of properties in AlN ceramic makes it a critical material in modern technology. It enables the development of smaller, more efficient, and more reliable electronic devices.
What are The Crystalline Structures of Aluminum Nitride (AlN) ?
Aluminum Nitride (AlN) is a versatile ceramic material that primarily exists in two crystalline structures: the hexagonal wurtzite structure and the cubic zincblende structure. Each structure offers unique properties, making AlN suitable for a wide range of applications.
1. Wurtzite Structure
- Hexagonal Lattice: The most common form of AlN, the wurtzite structure, is characterized by a hexagonal lattice arrangement.
- Alternating Layers: Aluminum and nitrogen atoms alternate along the c-axis, forming a tightly packed structure.
- Tetrahedral Coordination: Each atom is surrounded by four nearest neighbors in a tetrahedral configuration, resulting in strong covalent bonding.
- Polarization: The significant difference in electronegativity between Al and N atoms leads to spontaneous polarization along the c-axis. This property is essential for piezoelectric and pyroelectric applications.
2. Zincblende Structure
- Cubic Lattice: The zincblende structure is less common and typically found in thin film forms.
- Face-Centered Cubic Lattice: Aluminum and nitrogen atoms alternate in a face-centered cubic arrangement.
- Tetrahedral Coordination: Similar to the wurtzite structure, each atom is tetrahedrally coordinated.
- Metastability: The zincblende phase is metastable under normal conditions and can revert to the wurtzite phase at higher temperatures.
Comparison of Structures
Property | Wurtzite | Zincblende |
---|---|---|
Symmetry | Hexagonal | Cubic |
Polarization | High | Low |
Piezoelectric Effect | Strong | Weak |
Thermal Conductivity | High | High |
Electrical Conductivity | Low (intrinsic) | Low (intrinsic) |
Stability | Stable | Metastable |
In conclusion, both wurtzite and zincblende AlN offer unique properties that make them valuable materials for a wide range of applications, including electronics, optoelectronics, and high-temperature ceramics. The wurtzite structure, with its strong polarization and piezoelectric properties, is particularly important for devices like sensors, actuators, and high-power electronics. The zincblende structure, while less common, may offer potential advantages in specific applications, such as high-frequency electronics.
What are The Types of Aluminum Nitride (AlN) Ceramics?
While there aren’t distinct “types” of aluminum nitride (AlN) ceramics in the same way as other materials, different grades and formulations exist based on purity, processing techniques, and specific applications. These variations can influence the material’s properties, such as thermal conductivity, mechanical strength, and electrical resistivity.
Here are some common classifications based on their properties and applications:
1. High Thermal Conductivity AlN Ceramics:
- These are specifically designed for applications that require efficient heat dissipation, such as heat sinks for electronic devices.
- They often have a thermal conductivity of 170 W/mK or higher.
- High-purity AlN powder and advanced processing techniques are used to achieve these high thermal conductivity values.
2. High-Purity AlN Ceramics:
- These ceramics are produced using high-purity AlN powder, resulting in minimal impurities.
- They are often used in high-frequency electronic devices and optoelectronic applications where purity is critical.
3. Injection-Molded AlN Ceramics:
- This type of AlN ceramic is produced using injection molding techniques, allowing for complex shapes and precise dimensions.
- They are commonly used in electronic packaging and heat sinks.
4. Sintered AlN Ceramics:
- These ceramics are produced through sintering processes, which involve heating the AlN powder to high temperatures to bond the particles together.
- They are widely used in various applications, including electronics, optics, and mechanics.
It’s important to note that the specific properties of AlN ceramics can vary depending on the manufacturing process, the purity of the starting materials, and the desired application. Therefore, careful consideration of these factors is essential when selecting an AlN ceramic for a particular application.
Ultimately, the choice of AlN ceramic will depend on the specific requirements of the application, such as thermal conductivity, mechanical strength, electrical resistivity, and cost.
What are The Advantages of Aluminum Nitride (AlN) Ceramics?
Aluminum Nitride (AlN) ceramics offer a compelling combination of properties that make them valuable for various applications. Here’s a breakdown of their key advantages:
Thermal Management:
- High Thermal Conductivity: AlN excels at dissipating heat, with a thermal conductivity ranging from 170 to 230 W/mK. This makes it ideal for applications like power modules and LEDs where efficient heat transfer is crucial.
- Thermal Shock Resistance: Its low coefficient of thermal expansion (CTE) enables AlN to withstand rapid temperature fluctuations without cracking or deforming.
Electrical Performance:
- High Electrical Insulation: AlN is a non-conductive material with excellent dielectric strength, making it suitable for high-voltage applications and preventing electrical breakdowns.
Mechanical Properties:
- Strength and Hardness: AlN ceramics offer significant mechanical strength and hardness, enabling them to withstand harsh conditions and resist wear in demanding environments like aerospace and automotive industries.
Safety and Environmental Considerations:
- Low Toxicity: Unlike some alternatives like Beryllium Oxide (BeO), AlN is non-toxic, making it safer for manufacturing and handling.
Temperature Range:
- Wide Temperature Tolerance: AlN can operate reliably over a broad temperature range, from -40°C to 1000°C, making it suitable for extreme environments.
In conclusion, AlN ceramics provide a robust and versatile solution for various applications, particularly those requiring efficient thermal management, electrical insulation, and mechanical strength.
What are The Disadvantages of Aluminum Nitride (AlN) Ceramics?
Aluminum Nitride (AlN) ceramics, while offering superior thermal conductivity and electrical insulation, present several challenges that limit their widespread adoption:
Cost and Availability:
- High Production Cost: AlN manufacturing is complex and requires specialized equipment, making it more expensive than other ceramic materials like alumina.
- Limited Availability: The relative novelty of AlN in the market and fewer manufacturers capable of producing it at scale contribute to its limited availability and higher costs.
Processing Challenges:
- Machining Difficulty: The hardness and brittleness of AlN make it challenging to machine, necessitating specialized tools and techniques that increase processing costs and time.
Environmental and Health Considerations:
- Hydrolysis Sensitivity: AlN can react with moisture, degrading its performance over time, especially in humid environments.
- Toxicity: Exposure to AlN dust can be harmful to health, requiring careful handling and protective measures.
Mechanical Limitations:
- Brittleness: While strong, AlN’s brittleness makes it susceptible to fracture under impact or excessive stress, limiting its suitability for certain structural applications.
In conclusion, while AlN offers significant advantages, its cost, availability, processing challenges, environmental sensitivity, and mechanical limitations need to be carefully considered when evaluating its suitability for specific applications.
What are The Applications of Aluminum Nitride (AlN) Ceramics?
Aluminum Nitride (AlN) ceramics are a versatile material with a unique combination of properties that make them suitable for a wide range of applications. Here are some of the key applications of AlN ceramics:
Electronics and Semiconductor Industry:
- High-Power Electronics: AlN’s high thermal conductivity and electrical insulation properties make it ideal for use in high-power electronic devices such as power transistors, diodes, and integrated circuits. It helps dissipate heat efficiently, improving device performance and reliability.
- Semiconductor Manufacturing: AlN is used as a substrate material in the production of semiconductor devices. Its thermal conductivity helps to remove heat generated during the manufacturing process, improving yield and device performance.
- LED Lighting: AlN is used as a substrate material for high-power LEDs. Its high thermal conductivity helps to dissipate heat generated by the LED chips, improving their efficiency and lifespan.
Aerospace and Defense:
- Heat Sinks and Thermal Management: AlN’s high thermal conductivity makes it ideal for use in heat sinks and thermal management solutions for aerospace and defense applications. It helps to cool critical components, such as electronic systems and power supplies, ensuring their reliable operation in harsh environments.
- Radar Systems: AlN’s low dielectric constant and high thermal conductivity make it suitable for use in radar systems. It helps to reduce signal loss and improve system performance.
Medical Devices:
- Implantable Medical Devices: AlN’s biocompatibility and electrical insulation properties make it suitable for use in implantable medical devices, such as pacemakers and cochlear implants. It helps to protect sensitive electronic components from damage and interference.
Other Applications:
- Laser Systems: AlN’s high thermal conductivity and optical transparency make it suitable for use in laser systems. It helps to dissipate heat generated by the laser, improving its efficiency and stability.
- Automotive Industry: AlN is used in automotive electronics, such as power modules and sensors, to improve their thermal performance and reliability.
In conclusion, AlN ceramics are a valuable material with a wide range of applications. Their unique combination of properties, including high thermal conductivity, electrical insulation, and biocompatibility, make them essential for many industries, from electronics and semiconductors to aerospace and medicine.
What is the Challenges in Manufacturing Aluminum Nitride (AlN) Ceramics?
Aluminum Nitride (AlN) ceramics, with their exceptional thermal conductivity and electrical insulation properties, hold immense promise for a wide range of applications, particularly in the electronics industry. However, their manufacturing process presents several significant challenges.
Material Properties and Processing Challenges
- Brittleness: AlN’s inherent brittleness makes it susceptible to cracking and chipping, especially during processing of larger components.
- High Melting Point: This necessitates high-temperature sintering processes, requiring specialized equipment and precise control of the atmosphere to avoid oxygen contamination, which can degrade electrical and thermal properties.
- Complex Processing Techniques: The covalent bonding structure of AlN demands specialized processing techniques. Traditional ceramic processing methods may not be directly applicable.
- Surface Preparation: AlN readily forms an oxide layer, hindering subsequent processing steps like metallization and bonding. Careful surface preparation techniques are essential.
- Thermal Shock Resistance: While AlN exhibits good thermal shock resistance, rapid temperature changes during processing can still lead to fractures. Strict temperature control is crucial.
Environmental and Economic Considerations
- High-Energy Consumption: The high-temperature sintering process is energy-intensive, contributing to a significant environmental footprint.
- Raw Material Costs: High-purity AlN powder and specialized sintering equipment can be expensive, increasing production costs.
- Waste Generation: The manufacturing process can generate waste products, including spent tooling and processing chemicals.
Machining Challenges
- Hardness and Brittleness: AlN’s hardness and brittleness make it difficult to machine into complex shapes. Traditional machining techniques can lead to significant tool wear and part breakage.
- Thermal Shock Resistance: AlN’s high thermal conductivity makes it susceptible to thermal shock during machining, potentially causing cracking.
Addressing the Challenges
To overcome these challenges and realize the full potential of AlN ceramics, researchers and manufacturers are exploring various strategies:
- Advanced Processing Techniques: Developing innovative techniques like pressureless sintering and hot pressing can reduce energy consumption and improve material properties.
- Surface Modification: Surface treatments like chemical etching and plasma cleaning can enhance bonding and metallization.
- Machining Innovations: Advanced machining techniques, such as diamond or cubic boron nitride (CBN) tooling, can improve machining efficiency and reduce tool wear.
- Material Optimization: Tailoring the composition and microstructure of AlN can enhance its mechanical and thermal properties.
Challenges in AlN Ceramics Manufacturing
Challenge | Description |
---|---|
Material Properties | |
Brittleness | Susceptible to cracking and chipping during processing, especially for larger components. |
High Melting Point | Requires high-temperature sintering, demanding specialized equipment and precise atmosphere control. |
Processing Challenges | |
Complex Processing Techniques | Covalent bonding structure necessitates specialized processing methods. |
Surface Preparation | Readily forms an oxide layer, hindering subsequent processing steps. |
Thermal Shock Resistance | While good, rapid temperature changes can still lead to fractures. |
Environmental and Economic Considerations | |
High-Energy Consumption | High-temperature sintering is energy-intensive. |
Raw Material Costs | High-purity AlN powder and specialized equipment are expensive. |
Waste Generation | Manufacturing process generates waste products. |
Machining Challenges | |
Hardness and Brittleness | Difficult to machine into complex shapes, leading to tool wear and part breakage. |
Thermal Shock Resistance | Susceptible to thermal shock during machining, potentially causing cracking. |
Overcoming these challenges requires careful consideration of material properties, process optimization, and the use of specialized equipment. By addressing these issues, manufacturers can harness the full potential of AlN ceramics for various applications, particularly in the electronics industry.
What is the Difference of Silicon Nitride Ceramics and Aluminum Nitride (AlN) Ceramics?
Silicon Nitride (Si3N4) and Aluminum Nitride (AlN) are both high-performance ceramic materials with excellent properties, but they have distinct differences in their characteristics and applications.
Thermal Conductivity:
- AlN: Excels in thermal conductivity, making it ideal for heat dissipation applications like heat sinks and substrates for electronic devices.
- Si3N4: Has lower thermal conductivity compared to AlN, but it still offers good thermal shock resistance.
Thermal Expansion:
- AlN: Has a thermal expansion coefficient that closely matches that of silicon, making it suitable for use with semiconductor devices.
- Si3N4: Has a very low thermal expansion coefficient, making it resistant to thermal shock and ideal for high-temperature applications.
Mechanical Properties:
- Si3N4: Offers superior mechanical strength, hardness, and wear resistance, making it suitable for demanding applications like engine components and cutting tools.
- AlN: While not as strong as Si3N4, it still possesses good mechanical properties, especially in terms of fracture toughness.
Chemical Resistance:
- Si3N4: Exhibits excellent chemical resistance to most acids and alkalis, making it suitable for harsh environments.
- AlN: Offers good chemical resistance but may be susceptible to attack by strong acids and alkalis.
Electrical Properties:
- Si3N4: Is an electrical insulator, making it suitable for applications where electrical isolation is required.
- AlN: Has a higher electrical conductivity than Si3N4, making it useful for some electronic applications.
Cost:
- AlN: Generally more expensive to produce than Si3N4 due to the more complex manufacturing process.
Applications:
- AlN: Used in electronic packaging, heat sinks, power modules, and LED lighting.
- Si3N4: Used in engine components, cutting tools, bearings, and high-temperature structural components.
Table Summary:
Property | Silicon Nitride (Si3N4) | Aluminum Nitride (AlN) |
---|---|---|
Thermal Conductivity | Low | High |
Thermal Expansion | Low | Matches Silicon |
Mechanical Strength | High | Good |
Chemical Resistance | Excellent | Good |
Electrical Properties | Insulator | Higher Conductivity |
Cost | Lower | Higher |
In conclusion, the choice between Si3N4 and AlN depends on the specific requirements of the application. Si3N4 is well-suited for high-temperature, high-stress, and chemically harsh environments, while AlN excels in thermal management and electronic applications where high thermal conductivity and matching thermal expansion are critical
What material can be Replaced by Aluminum Nitride in Industry?
Aluminum nitride (AlN) is a promising material that can replace various traditional materials in industrial applications. Here are some key areas where AlN can be used as a substitute:
1. Replacing Aluminum Oxide:
- Enhanced Thermal Conductivity: AlN significantly outperforms aluminum oxide in terms of thermal conductivity, making it ideal for heat dissipation in electronic devices, high-power electronics, and LED lighting.
- Improved Mechanical Properties: AlN possesses higher hardness and better wear resistance, making it suitable for cutting tools, molds, and other precision machining applications.
2. Replacing Beryllium Oxide:
- Enhanced Safety: Unlike beryllium oxide, AlN is non-toxic, reducing health risks during manufacturing and use.
- Similar Performance: AlN offers comparable electrical and thermal properties to beryllium oxide, making it a suitable replacement in RF power devices, microwave communications, and other high-performance applications.
3. Replacing Metal Materials:
- High-Temperature Applications: AlN’s high melting point and thermal stability make it suitable for high-temperature environments where metals may soften or melt. It can be used in furnace components, heat treatment equipment, and other applications requiring high-temperature resistance.
- Electrical Insulation: AlN’s excellent electrical insulation properties make it a good replacement for metal in applications where electrical isolation is crucial, such as electronic packaging and high-voltage equipment.
4. Replacing Traditional Ceramic Materials:
- Complex Shapes: AlN can be processed into complex shapes, making it suitable for components with intricate designs.
- Improved Performance Stability: AlN offers better stability in terms of chemical and thermal properties, making it ideal for applications demanding high reliability, such as aerospace and military equipment.
Property | AlN Ceramics | Traditional Materials (e.g., Al2O3, BeO) |
---|---|---|
Thermal Conductivity | Significantly higher | Lower |
Electrical Insulation | Excellent | Good |
Mechanical Strength | High | Moderate to high |
Thermal Shock Resistance | High | Moderate |
Chemical Stability | High | Moderate |
Toxicity | Non-toxic | Some materials (e.g., BeO) can be toxic |
Cost | Higher | Lower |
In conclusion, AlN’s unique properties make it a versatile material with the potential to replace traditional materials in various industries. Its high thermal conductivity, excellent electrical insulation, and superior mechanical properties contribute to improved performance, increased efficiency, and enhanced reliability in a wide range of applications.
How is Aluminum Nitride (AlN) Ceramic Manufactured?
Aluminum Nitride (AlN) ceramics are gaining significant attention due to their exceptional thermal and electrical properties. The manufacturing process of AlN ceramics involves several critical steps:
1. Powder Synthesis:
- Direct Nitridation: High-purity aluminum powder is directly reacted with nitrogen gas at elevated temperatures (1200-1400°C) to form AlN powder.
- Carbothermal Reduction-Nitridation: A mixture of alumina (Al₂O₃) and carbon is heated in a nitrogen atmosphere to yield AlN powder.
2. Powder Processing:
- Milling: The synthesized AlN powder is milled to achieve the desired particle size and shape distribution.
- Mixing: Additives, such as sintering aids (e.g., oxides of magnesium, calcium, or yttrium), may be added to the AlN powder and mixed thoroughly.
3. Shape Forming:
- Pressing: The AlN powder is pressed into the desired shape using techniques like cold isostatic pressing or hot pressing.
- Injection Molding: AlN powder can be mixed with organic binders to form a moldable paste, which is injected into molds to create complex shapes.
4. Sintering:
- High-Temperature Sintering: The formed AlN components are sintered at high temperatures (1800-2000°C) in a controlled atmosphere to densify the material and enhance its mechanical properties.
- Pressure-Assisted Sintering: Techniques like hot pressing or spark plasma sintering can be employed to accelerate the sintering process and achieve higher densities.
5. Machining and Finishing:
- Machining: AlN ceramics can be machined using diamond-tipped tools to attain precise dimensions and complex shapes.
- Polishing: The machined components are polished to achieve a smooth surface finish.
Challenges in Manufacturing AlN Ceramics:
- High-Temperature Processing: The high temperatures required for sintering can lead to energy consumption and equipment challenges.
- Brittleness: AlN is inherently brittle, making it susceptible to cracking and chipping during processing.
- Expensive Raw Materials: High-purity AlN powder and specialized sintering equipment can increase production costs.
- Complex Processing Techniques: Specialized techniques are necessary to achieve the desired properties, which can be complex and time-consuming.
Advanced Manufacturing Techniques for AlN Ceramics:
To address these challenges and further optimize the manufacturing process, advanced techniques are being explored:
- Additive Manufacturing (3D Printing):
- Direct Ink Writing: AlN ceramic inks can be extruded layer-by-layer to create complex 3D structures.
- Powder Bed Fusion: AlN powder can be selectively fused using laser or electron beam sintering to produce dense, high-quality components.
- Microwave Sintering:
- Rapid heating and enhanced densification can be achieved through microwave sintering.
- Spark Plasma Sintering (SPS):
- High-pressure, high-temperature sintering can significantly reduce sintering time and produce dense, fine-grained AlN ceramics.
By adopting these advanced techniques and addressing the challenges, the manufacturing of AlN ceramics can be further optimized to produce high-quality components with improved performance and reduced costs.
what is the Process of Getting Samples from Yomua for Aluminium Nitride Ceramic?
Yes, it is possible to obtain samples of Aluminum Nitride (AlN) products from Yomua before placing a bulk order. Yomua is a well-established manufacturer of advanced ceramic materials, including AlN, and they often provide samples to potential customers to evaluate their products.
Here’s a general process to obtain AlN samples from Yomua:
- Contact Yomua:
- Reach out to our sales or technical team through email or inquiry or phone.
- Specify Your Requirements:
- Clearly communicate your specific needs, such as the desired dimensions, tolerances, surface finish, and any other relevant specifications.
- Explain your intended application for the AlN product.
- Discuss Sample Quantity and Cost:
- Most suppliers offer samples at a nominal cost or even for free, especially for smaller quantities.
- Negotiate the sample quantity and pricing with us.
- Provide Necessary Information:
- Share any relevant information about your application, such as the operating environment, thermal requirements, and mechanical stresses.
- This will help Yomua recommend the most suitable AlN product.
- Place the Sample Order:
- Once you’ve agreed on the details, place the sample order with us.
- You may need to provide payment information or sign a sample agreement.
- Receive and Evaluate the Samples:
- Yomua will ship the samples to you.
- Thoroughly evaluate the samples to assess their properties, quality, and suitability for your application.
- Provide Feedback:
- Share your feedback with us, including any specific observations or suggestions for improvement.
- This can help build a strong relationship with the supplier and improve future collaborations.
Additional Tips:
- Be Specific: Clearly communicate your needs to ensure the samples meet your expectations.
- Consider Customization: If you have specific needs, discuss customization options with us.
- Check Lead Times: Inquire about the expected lead time for sample delivery to plan your evaluation process accordingly.
- Ask Questions: Don’t hesitate to ask questions about the material properties, manufacturing processes, or any other concerns you may have.
By following these steps and considering the factors mentioned above, you can effectively obtain AlN samples from us and make informed decisions about your bulk order.
How do Aluminum Nitride (AlN) Ceramics Compare to Alumina Ceramics?
Aluminum Nitride (AlN) and Alumina (Al₂O₃) are two prominent advanced ceramic materials, each offering distinct properties that make them suitable for a wide range of applications. While they share similarities in terms of mechanical strength and thermal stability, their unique characteristics set them apart.
Similarities:
- Ceramic Nature: Both materials are ceramic, offering high hardness, excellent wear resistance, and good chemical stability.
- Electrical Insulation: Both are excellent electrical insulators, making them suitable for electronic components.
Chemical Composition and Structure
- Aluminum Nitride (AlN): A compound semiconductor comprised of aluminum and nitrogen atoms, AlN crystallizes in a wurtzite structure. The presence of nitrogen imparts specific properties to this material.
- Alumina (Al₂O₃): Composed of aluminum and oxygen, alumina exists in various crystalline forms, with alpha-alumina being the most common and stable.
Mechanical Properties
- Hardness and Strength: Both materials are renowned for their exceptional hardness. However, alumina typically exhibits higher hardness values compared to AlN.
- Fracture Toughness: Alumina generally possesses superior fracture toughness, making it more resilient to crack propagation.
Thermal Properties
- Thermal Conductivity: AlN stands out for its remarkably high thermal conductivity, which can exceed 200 W/m·K. This property makes it an ideal choice for heat dissipation applications in electronics. In contrast, alumina has a lower thermal conductivity, typically around 20-30 W/m·K.
- Thermal Expansion Coefficient: AlN exhibits a lower coefficient of thermal expansion (CTE) compared to alumina. This means that AlN experiences less dimensional change with temperature fluctuations.
Electrical Properties
- Electrical Insulation: Both materials are excellent electrical insulators. However, AlN’s wide bandgap (~6 eV) gives it superior dielectric properties, making it suitable for high-frequency electronic applications.
- Piezoelectric Properties: AlN possesses piezoelectric properties, which means it can convert mechanical energy into electrical energy and vice versa. This makes it useful in various sensor and actuator applications. Alumina, on the other hand, does not exhibit piezoelectric behavior.
Application
Application | Aluminum Nitride (AlN) | Alumina (Al₂O₃) |
---|---|---|
Electronics | High-power devices, heat sinks, RF components | Insulators, substrates, packaging |
Mechanical Engineering | Structural components in high-temperature environments | Wear-resistant components, cutting tools |
Biomedical | Sensors, actuators | Dental implants, bone replacements |
- AlN excels in thermal management applications due to its high thermal conductivity. It’s particularly useful in high-power electronics and RF devices.
- Alumina is a versatile material with high mechanical strength and excellent electrical insulation. It’s widely used in electronics, mechanical engineering, and biomedical applications.
A Comparative Analysis: Aluminum Nitride (AlN) vs. Alumina (Al₂O₃) Ceramics
Property | Aluminum Nitride (AlN) | Alumina (Al₂O₃) |
---|---|---|
Chemical Composition | Aluminum and Nitrogen | Aluminum and Oxygen |
Crystal Structure | Wurtzite | Alpha-alumina (most common) |
Hardness | High | Very high |
Fracture Toughness | Moderate | High |
Thermal Conductivity | High (200+ W/m·K) | Moderate (20-30 W/m·K) |
Thermal Expansion Coefficient | Low | Moderate |
Electrical Insulation | Excellent | Excellent |
Piezoelectric Properties | Yes | No |
Conclusion
By understanding the unique properties of AlN and alumina, engineers and designers can select the appropriate material for specific applications. AlN’s high thermal conductivity and piezoelectric properties make it ideal for electronics and sensor applications, while alumina’s superior hardness and fracture toughness make it suitable for mechanical components and wear-resistant coatings.
Are there Alternative Materials that can Replace Aluminium Nitroide ?
While AlN is an excellent material for many applications, there are alternative materials that can be considered, depending on specific requirements and cost constraints:
1. Diamond
- Advantages: Extremely high thermal conductivity, exceptional hardness, and chemical inertness.
- Disadvantages: High cost, difficulty in processing, and limited availability in large sizes.
- Applications: High-power electronic devices, heat sinks for extreme environments.
2. Cubic Boron Nitride (cBN)
- Advantages: High thermal conductivity, excellent mechanical properties, and chemical resistance.
- Disadvantages: Relatively high cost and complex manufacturing process.
- Applications: Cutting tools, wear-resistant components, and high-temperature applications.
3. Silicon Carbide (SiC)
- Advantages: High thermal conductivity, high strength, and good chemical resistance.
- Disadvantages: Lower thermal conductivity compared to AlN, and can be more brittle.
- Applications: Semiconductor substrates, heat sinks, and structural components in high-temperature environments.
4. Boron Nitride (BN)
- Advantages: Excellent thermal conductivity, low thermal expansion, and good electrical insulation.
- Disadvantages: Lower mechanical strength compared to AlN.
- Applications: High-temperature lubricants, heat sinks, and electrical insulation.
5. Copper and Copper Alloys
- Advantages: High thermal conductivity, good electrical conductivity, and ease of processing.
- Disadvantages: Lower mechanical strength and thermal expansion compared to ceramics.
- Applications: Heat sinks, heat spreaders, and thermal interface materials.
When to Consider Alternatives to AlN:
- Cost Constraints: If cost is a major concern, materials like SiC or copper alloys might be more economical options, especially for large-scale applications.
- Specific Property Requirements: For applications requiring extremely high hardness or chemical resistance, diamond or cBN might be preferred.
- Processing Limitations: If complex shapes or thin-film applications are required, materials like SiC or BN might be more suitable due to their processing characteristics.
It’s important to note that the choice of material depends on a variety of factors, including the specific application requirements, cost, and manufacturing feasibility. In many cases, a combination of materials or advanced manufacturing techniques may be necessary to achieve optimal performance.
Comparison of AlN and Alternative Materials
Material | Thermal Conductivity | Mechanical Strength | Cost | Processing | Applications |
---|---|---|---|---|---|
Aluminum Nitride (AlN) | High | Good | Moderate | Moderate | High-power electronics, heat sinks, RF components |
Diamond | Extremely High | Extremely High | Very High | Difficult | High-power electronics, extreme environments |
Cubic Boron Nitride (cBN) | High | Very High | High | Complex | Cutting tools, wear-resistant components, high-temperature applications |
Silicon Carbide (SiC) | High | High | Moderate | Moderate | Semiconductor substrates, heat sinks, high-temperature components |
Boron Nitride (BN) | High | Moderate | Moderate | Moderate | High-temperature lubricants, heat sinks, electrical insulation |
Copper and Copper Alloys | High | Moderate | Low | Easy | Heat sinks, heat spreaders, thermal interface materials |
What are Some Common Misconceptions About Aluminium Nitride ?
Here are some common misconceptions about Aluminum Nitride (AlN) Ceramics that you should be aware of:
Misconception 1: AlN is Brittle and Fragile
While AlN is a ceramic material, it is not as brittle as traditional ceramics. It possesses excellent mechanical strength and toughness, making it suitable for various applications that require durability.
Misconception 2: AlN is Difficult to Machine
While early AlN materials were challenging to machine, advancements in manufacturing techniques have made it easier to machine AlN into complex shapes. Machinable grades of AlN are now readily available.
Misconception 3: AlN is Expensive
While AlN can be more expensive than traditional materials like aluminum oxide, its superior performance and long-term benefits often offset the initial cost. Additionally, as the demand for AlN increases, production costs are gradually decreasing.
Misconception 4: AlN is Sensitive to Moisture
While AlN can react with moisture over extended periods, especially in powder form, sintered AlN ceramics are highly resistant to moisture and can be used in various environmental conditions.
Misconception 5: AlN is a New Material
AlN has been known for decades, but advancements in manufacturing techniques and a growing understanding of its properties have led to its increased adoption in recent years.
By understanding these misconceptions and the true capabilities of AlN, buyers can make informed decisions and leverage the benefits of this advanced ceramic material.
What is the Surface Roughness of the ALN ceramic?
The surface roughness of AlN ceramics is a crucial factor influencing their performance in various applications, particularly in the electronics industry. It significantly impacts thermal conductivity, electrical insulation, and the ability to bond with other materials.
Manufacturing Processes and Surface Finish
The manufacturing process employed plays a significant role in determining the final surface roughness of AlN ceramics. Common techniques such as polishing, lapping, and metallization can influence the surface smoothness.
Typical Surface Roughness Values
High-quality AlN substrates typically exhibit a surface roughness (Ra) in the range of 0.1 to 0.5 micrometers (µm). This level of smoothness is essential for optimal performance in semiconductor applications.
Importance of Surface Roughness
A smoother surface offers several advantages:
- Enhanced Thermal Conductivity: A lower surface roughness minimizes air gaps between the ceramic and other components, improving thermal conductivity.
- Improved Adhesion: A smooth surface promotes better adhesion when bonding with other materials, such as metallization layers or heat sinks.
- Enhanced Electrical Insulation: A well-polished surface can contribute to better electrical insulation properties.
Quality Control and Measurement
Manufacturers employ rigorous quality control measures to ensure that the surface roughness of AlN ceramics meets specified tolerances. This often involves using profilometers or atomic force microscopy (AFM) to accurately measure the surface roughness.
By carefully controlling the manufacturing process and adhering to stringent quality standards, manufacturers can produce AlN ceramics with the desired surface roughness, optimizing their performance in a wide range of applications.
What is the Differences Between Aluminum Nitride (AlN) Ceramics and Zirconia Ceramics?
Aluminum Nitride (AlN) and Zirconia are two advanced ceramic materials with distinct properties, making them suitable for diverse applications. Let’s delve into a comparative analysis of their characteristics.
Composition and Structure
- AlN: Composed of aluminum and nitrogen, AlN exhibits a hexagonal wurtzite crystal structure.
- Zirconia: Primarily zirconium dioxide (ZrO2), zirconia can exist in various crystalline phases, with the tetragonal phase stabilized by additives like yttria being commonly used.
Thermal Properties
- AlN: Excels in thermal conductivity (150-200 W/m·K), making it ideal for heat dissipation applications.
- Zirconia: Lower thermal conductivity (2-3 W/m·K) but a high melting point (~2700°C), suitable for high-temperature environments.
Mechanical Properties
- AlN: High mechanical strength and hardness but brittle.
- Zirconia: Exceptional toughness and fracture resistance due to transformation toughening.
Electrical Properties
- AlN: Excellent electrical insulator, often used in electronic components.
- Zirconia: Can be both insulating or conductive (when doped), finding applications in solid oxide fuel cells.
Chemical Resistance
- AlN: Resistant to thermal shock and chemical attack.
- Zirconia: Good chemical resistance, particularly to acids and alkalis.
Applications
- AlN:
- Electronics (heat sinks, substrates)
- Automotive components
- Aerospace components
- Zirconia:
- Dental implants
- Cutting tools
- Sensors
- Fuel cells
Cost and Availability
- AlN: Higher production cost due to complex synthesis and sintering processes.
- Zirconia: More readily available and generally less expensive.
Choosing the Right Material
The selection between AlN and Zirconia hinges on the specific application requirements.
- Prioritize thermal conductivity and electrical insulation: AlN is the preferred choice.
- Require high mechanical strength and toughness: Zirconia is often the optimal material.
By understanding the unique properties of these materials, engineers and designers can make informed decisions to optimize the performance of their products.
Property | AlN | Zirconia |
---|---|---|
Thermal Conductivity | High | Low-Medium |
Electrical Conductivity | Insulator | Can be conductive or insulating |
Mechanical Strength | High (brittle) | High (tough) |
Chemical Resistance | Good | Good |
Conclusion
In conclusion, both Aluminum Nitride (AlN) and Zirconia are versatile ceramic materials with distinct properties. AlN excels in thermal conductivity and electrical insulation, making it ideal for electronic and high-temperature applications. Zirconia, on the other hand, offers superior mechanical properties, particularly toughness and fracture resistance, making it suitable for structural and biomedical applications.
The choice between these two materials depends on the specific requirements of the application. By carefully considering factors such as thermal conductivity, mechanical strength, electrical properties, and chemical resistance, engineers and designers can select the optimal material to achieve desired performance.
What is the Factors Affecting the Cost of Aluminum Nitride (AlN) Ceramic ?
The cost of Aluminum Nitride (AlN) ceramic materials is influenced by a complex interplay of factors, including:
1. Raw Material Quality and Purity:
- High-Purity Requirements: AlN ceramics demand high-purity aluminum and nitrogen sources to achieve optimal thermal conductivity and mechanical properties.
- Purification Costs: Impurities can degrade performance, necessitating expensive purification processes or higher-quality raw materials.
2. Manufacturing Process Complexity:
- Energy-Intensive Synthesis: Methods like direct nitridation and carbon thermal reduction involve high-temperature processes, significantly impacting energy costs.
- Specialized Equipment: Advanced equipment is often required for precise control over synthesis and molding, increasing capital costs.
- Environmental Considerations: AlN’s hydrophilicity necessitates careful handling to prevent oxidation. This often involves organic slurries, which can incur additional environmental compliance costs.
3. Molding Techniques:
- Traditional Methods: Hot pressing and isostatic pressing are effective but have high operational costs due to low production efficiency.
- Emerging Technologies: Newer methods like flow casting can reduce costs but require substantial investment in new technologies and processes.
4. Market Dynamics:
- Demand and Supply: Increasing demand from sectors like electronics and automotive drives up prices as manufacturers strive to meet growing needs.
- Competition: Competition among producers can influence pricing strategies, as companies may invest in R&D to differentiate their products and improve performance.
Factor | Description | Impact on Cost |
---|---|---|
Raw Material Quality and Purity | High-purity aluminum and nitrogen sources are essential for optimal performance. Impurities can necessitate additional purification steps or higher-quality raw materials. | Increased cost due to higher-quality inputs or additional processing steps. |
Manufacturing Process Complexity | The synthesis and molding processes, including direct nitridation, carbon thermal reduction, hot pressing, and isostatic pressing, can be energy-intensive and require specialized equipment. | Increased energy costs and capital investment in specialized equipment. |
Environmental Considerations | The hydrophilicity of AlN powder requires careful handling and processing to prevent oxidation. This often involves organic slurries, which can incur additional environmental compliance costs. | Increased costs due to specialized handling and disposal procedures. |
Market Dynamics | Market demand, competition, and technological advancements can influence pricing strategies and production costs. | Fluctuating costs due to market forces and technological innovations. |
By understanding these factors, it’s clear that the cost of AlN ceramics is influenced by a combination of technical challenges, manufacturing complexities, and market dynamics. As technology advances and production processes become more efficient, the cost of AlN ceramics may decrease over time.
What are the Emerging Trends in Aluminium Nitride (AlN) ceramic Technology?
AlN ceramic technology is experiencing significant growth and innovation, driven by its unique properties and increasing demand across various industries. Here are some key emerging trends:
1. Enhanced Thermal Management Solutions:
- High Thermal Conductivity: AlN’s exceptional thermal conductivity makes it ideal for applications requiring efficient heat dissipation, especially in high-power electronic devices.
- Miniaturization: As electronic components continue to shrink, AlN substrates become crucial for managing heat within smaller footprints.
2. Integration with Advanced Semiconductor Technologies:
- Power Electronics: AlN’s high-temperature capabilities and low thermal expansion coefficient make it suitable for high-power electronic devices, improving their efficiency and reliability.
- RF Devices: Its excellent dielectric properties enable the development of high-frequency devices, essential for 5G and beyond.
3. Growth in Electric Vehicles and Renewable Energy:
- EV Power Electronics: AlN-based power electronics can significantly improve the efficiency and range of electric vehicles.
- Renewable Energy Systems: AlN’s thermal management properties are beneficial for inverters and power converters used in renewable energy systems.
4. Advanced Manufacturing Techniques:
- Additive Manufacturing: This technique enables the production of complex AlN components with intricate designs, reducing material waste and improving design flexibility.
- Direct Ink Writing: This method allows for the precise deposition of AlN inks to create 3D structures, opening up new possibilities for customized and multifunctional devices.
5. Research and Development:
- Material Engineering: Ongoing research aims to further enhance AlN’s properties, such as improving its dielectric strength, chemical stability, and thermal conductivity.
- Nanocomposites: Combining AlN with other materials at the nanoscale can lead to advanced composites with superior properties.
Trend | Description |
---|---|
Enhanced Thermal Management | High thermal conductivity for efficient heat dissipation in high-power electronic devices. |
Integration with Advanced Semiconductors | Compatibility with advanced semiconductor technologies for improved performance and efficiency in power electronics and RF devices. |
Growth in Electric Vehicles and Renewable Energy | Application in power electronics for EVs and inverters for renewable energy systems. |
Advanced Manufacturing Techniques | Adoption of additive manufacturing and direct ink writing for complex shapes and customized designs. |
Material Engineering and Research | Ongoing research to improve material properties like dielectric strength, chemical stability, and thermal conductivity. |
By leveraging these trends, Aluminium Nitride AlN ceramic technology is poised to revolutionize various industries and drive innovation in the future.
What is the Yomua Capacity to Meet Future Demand for ALN Ceramic Components?
Aluminum Nitride (ALN) ceramic components are advanced materials prized for their exceptional thermal conductivity, electrical insulation, and mechanical strength. Their increasing applications in electronics, aerospace, and automotive industries, particularly in thermal management solutions for high-performance electronic devices, are driving significant market growth.
Yomua is a recognized leader in the advanced ceramics industry, including ALN ceramics.While specific figures on production capacity and supply chain details may not be publicly disclosed, we can make an informed assessment based on their industry reputation and recent developments:
Production Capacity:
- Advanced Manufacturing Facilities: Yomua possesses state-of-the-art manufacturing facilities equipped with advanced technologies to produce high-quality ALN ceramic components.
- Scalability: The company likely has the capacity to scale production to meet increasing demand, especially considering the growing importance of ALN ceramics in various industries.
- Continuous Improvement: Yomua commitment to research and development ensures ongoing optimization of production processes, leading to increased efficiency and capacity.
Supply Chain Stability:
- Diversified Sourcing: Yomua has a diversified supply chain for raw materials, reducing reliance on single sources and mitigating potential risks.
- Strategic Partnerships: Strong partnerships with suppliers can enhance supply chain reliability and ensure a steady flow of raw materials.
- Inventory Management: Effective inventory management practices can help optimize stock levels and minimize disruptions
Technological Capability:
- Research and Development: Yomua invests in research and development to stay at the forefront of ceramic technology, enabling continuous innovation and improvement in ALN ceramic production.
- Material Science Expertise: Yomua’s deep understanding of material science allows it to develop advanced ALN ceramic formulations with superior properties.
- Process Optimization: By optimizing production processes, Yomua can enhance efficiency, reduce costs, and improve product quality.
Additional Considerations:
- Industry Demand: The increasing demand for ALN ceramics, particularly in electronics and automotive industries, drives the need for increased production capacity.
- Global Market Dynamics: Global economic conditions, geopolitical factors, and supply chain disruptions can impact the availability of raw materials and the overall market demand.
- Competitive Landscape: Competition from other ceramic manufacturers may influence Yomuas production capacity and market share.
Conclusion
Yomua, a leading player in the advanced ceramics industry, is well-positioned to meet the growing demand for ALN ceramic components. With its strong technological capabilities, robust supply chain, and commitment to innovation, the company is likely to continue expanding its production capacity to cater to the needs of various industries.
Aluminium Nitride (AlN) Ceramics Conclusion
AlN ceramics are a high-performance material with excellent thermal conductivity, electrical insulation, and thermal expansion matching silicon. They are crucial for advanced thermal management in high-power electronics, 5G technology, electric vehicles, and renewable energy systems. As technology advances, AlN ceramics are poised to play a pivotal role in shaping the future of electronics and beyond.