Zirconia Ceramics Components
Yomua:Trusted Partner in China
- Decades of Manufacturing Zirconia Ceramic Components.
- Utilizing Top ZrO2 Powder for Exceptional Performance.
- Rigorous Quality Control Ensures Consistent Excellence.
- Understanding and meeting your specific needs.
- Our Own Factory Ensure competitive pricing without Compromising Quality.
Get a Quote Today
Zirconia Ceramics Components Leading Manufacturer
WHy Choose Yomua
- Over 40 Years of Expertise: We leverage our extensive experience to deliver exceptional zirconia ceramic components.
- Uncompromising Quality: We use only the highest-grade zirconia raw materials for unmatched performance and durability.
- Customizable Surface Accuracy: We meet your precise specifications, ensuring a perfect fit and function for every application.
- Dedicated Engineering Team: Our team of experienced engineers ensures consistent quality and innovation in every project.
- Rigorous Quality Control: Our meticulous quality control system guarantees every component meets the highest standards.
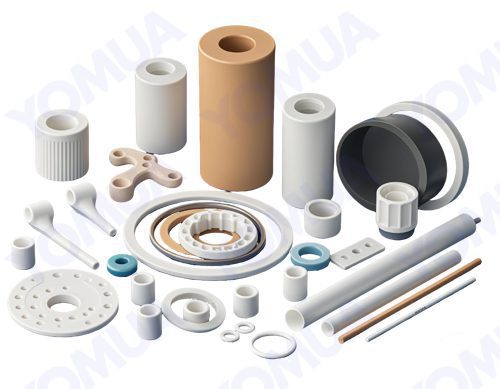
Custom Manufacturing Zirconia Ceramics
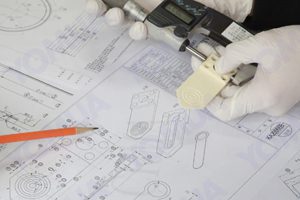
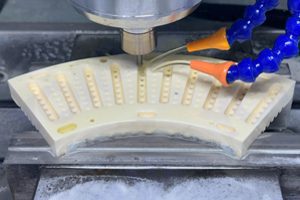
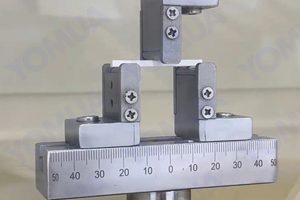
- Exceptional Customer Service: We partner with you to understand your needs and provide clear communication throughout the entire process.
- Reliable After-Sales Support: Our responsive after-sales service ensures you receive the support you need, whenever you need it.
- Fast Turnaround Times: We prioritize prompt delivery to keep your projects on track.
Zirconia ZrO2 Properties
Property | Unit | Magnesia-Stabilized Zirconia (MSZ) | Yttria-Stabilized Zirconia (YTZP) | Ceria-Stabilized Zirconia (CSZ) |
---|---|---|---|---|
Density | g/cm³ | 5.72 | 6.02-6.07 | 6.2 |
Hardness (Vickers) | GPa | 11.7 GPa | 12.5 GPa | 11.7 GPa |
Fracture Toughness | MPa√m | 12 | 8-10 | 12 |
Flexural Strength | MPa | 620 | 951-1380 | 551 |
Thermal Conductivity | W/mK | 3 | 2 | 3.5 |
Coefficient of Thermal Expansion (α) | 10⁻⁶/°C | 8.9-10 | 6.9-10.6 | 6.9-10.5 |
Maximum Use Temperature | °C | 1200 | 500-1000 | 537-1155 |
Dielectric Strength | V/mil | 300 | 240 | 250 |
Dielectric Constant | – | 22.7-29.2 | 30 | 30 |
Volume Resistivity | Ω·cm | >10¹³ | >10¹³ | >10¹³ |
Your Trusted Zirconia ZrO2 Ceramics Partner
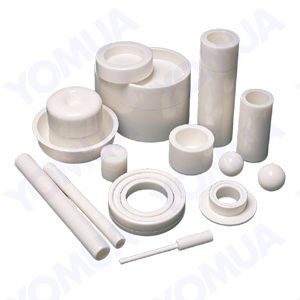
Customized Zirconia Ceramic Parts
YOUMA manufactures OEM precision zirconia ceramic components and parts for a variety of applications and industries.
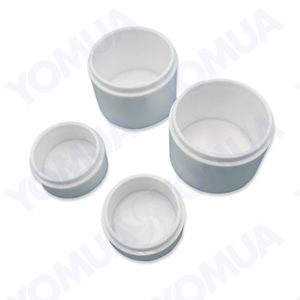
Zirconia Ceramic Crucible
Melt superalloys and precious metals such as platinum, palladium, ruthenium and cesium along with their alloys at temperatures up to 2200°C
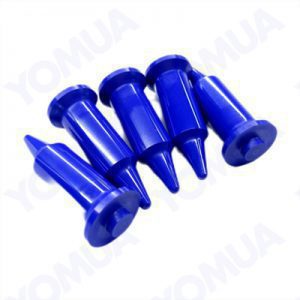
Zirconia Ceramic Positioning Pin
High-temperatures and high-pressures.Used for industrial welding , chemical processing, precision machining and assembly etc.,
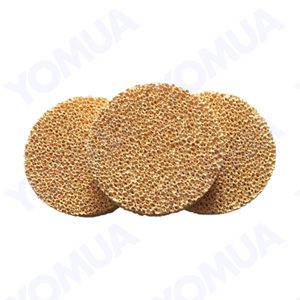
Zirconia Ceramic Foam Filters
Used for filtration of molten steel and steel alloys based superalloy castings and remove inclusions, reduce trapped gas from liquid metal etc.,
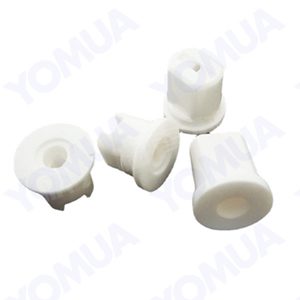
Zirconia Ceramic Nozzle
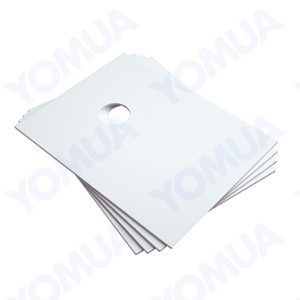
Zirconia Ceramic Plate
Durable, heat-resistant, and chemically resistant flat sheets used in various industries for their exceptional properties and precision machinability.
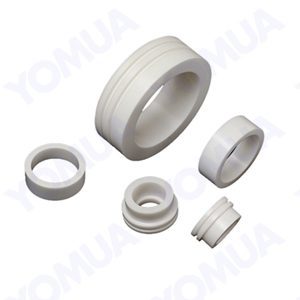
Zirconia Ceramic Ring
Used in jewelry, industrial seals, and high-temperature components, due to their strength, hardness, durability,and chemical corrosion.

Zirconia Ceramic Knife
Boast an incredibly sharp edge that lasts significantly longer than traditional steel knives. Their non-porous surface prevents bacteria growth and resists corrosion and staining.
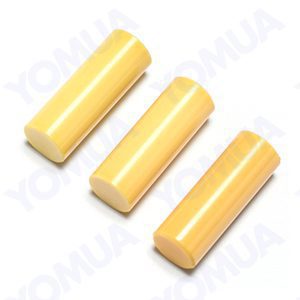
Zirconia Ceramic Rod
Highly precise and stable, offering excellent heat resistance and chemical inertness that make them ideal for various industries: electronics, aerospace, and medical devices etc.,
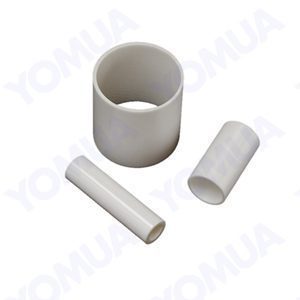
Zirconia Ceramic Tube
Known as pipe , precisely manufactured, ensuring dimensional accuracy and surface finish combined with precision manufacturing, make them indispensable in many applications.
Happy Customers Say about Yomua Zirconia Ceramic....

Your Satisfaction, Our Strength



Zirconia ZrO2 Ceramic Related Products
high thermal conductivity, excellent electrical insulation, and good mechanical strength.
High fracture toughness, excellent wear resistance, and superior corrosion resistance.
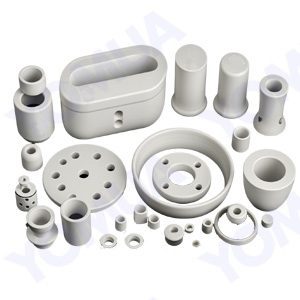
Yomua Boron Nitride(BN) Ceramics
High-temperature stability, excellent electrical insulation, and good thermal conductivity.
Zirconia ZrO2 Ceramics Components Guide
This guide will help you to understanding the Zirconia, or zirconium dioxide (ZrO2) ceramic material.Whether you’re an engineer, designer, or material scientist, this guide equips you with the necessary knowledge to work effectively with zirconia ceramics. By leveraging the information presented here, you can unlock the full potential of this versatile material and contribute to groundbreaking innovations across various industries.
Frequently Asked Questions
What is Zirconia or Zirconium dioxide or ZrO2 ?
Zirconium dioxide, often referred to as zirconia or ZrO2, is a one of advanced ceramic materials engineered to possess specific properties that make them suitable for demanding applications.Renowned for its extraordinary hardness, durability, and resistance to high temperatures and chemical corrosion, zirconia has become indispensable in various industries.
What is Zirconia Ceramic or Zirconium Oxide Ceramic?
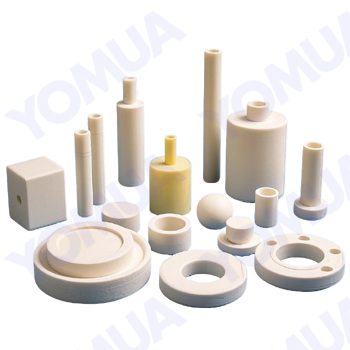
Zirconia ceramic, primarily composed of zirconium dioxide (ZrO2), is a versatile oxide ceramic material. While it offers unique properties like high strength, excellent thermal shock resistance, and good chemical resistance, it’s not necessarily the most flexible or cost-effective option among oxide ceramics. Zirconia’s specific properties make it invaluable in certain applications. Its high strength and toughness, especially at elevated temperatures, make it suitable for high-performance engine components, cutting tools, and structural ceramics. Additionally, its biocompatibility makes it an ideal material for dental implants and other medical devices.
What are the Characteristics of Zirconia Ceramic Materials?
Zirconia ceramic materials are renowned for their exceptional combination of properties that make them highly desirable for a wide range of applications.
Mechanical Properties:
- High Strength and Toughness: Zirconia ceramics exhibit extraordinary strength and toughness, making them highly resistant to fracture and wear. This property is particularly beneficial in applications where mechanical stress and impact loads are significant, such as cutting tools, engine components, and structural ceramics.
- Phase Transformation Toughening: A unique mechanism where zirconia undergoes a phase transformation under stress, absorbing energy and preventing crack propagation. This phenomenon significantly enhances the toughness and durability of zirconia ceramics, making them suitable for demanding environments.
Thermal Properties:
- Excellent Thermal Shock Resistance: Zirconia ceramics can withstand rapid changes in temperature without cracking or breaking. This property is crucial in applications involving thermal cycling, such as engine components, furnace linings, and heat exchangers.
- Low Thermal Conductivity: Zirconia ceramics are poor conductors of heat, making them effective thermal insulators. This property is valuable in applications where heat management and energy efficiency are critical, such as thermal barrier coatings and insulation materials.
- High Melting Point: Zirconia ceramics possess a high melting point, enabling them to withstand extreme temperatures without melting or degrading. This property is essential for high-temperature applications, such as furnace linings, refractory materials, and aerospace components.
Chemical Properties:
- Good Chemical Resistance: Zirconia ceramics are resistant to corrosion from a wide range of chemicals, including acids and alkalis. This property makes them suitable for applications in harsh chemical environments, such as chemical processing equipment and pollution control devices.
Biocompatibility:
- Biocompatibility: Certain forms of zirconia are biocompatible, making them ideal for medical implants and dental restorations. This property, coupled with their strength and durability, makes zirconia ceramics a preferred choice for dental implants, orthopedic implants, and other biomedical applications.
Aesthetic Appeal:
- Aesthetic Appeal: Zirconia can be polished to a high luster, making it attractive for jewelry and other decorative applications. Its brilliance and durability make it a popular choice for creating stunning jewelry pieces.
By understanding and leveraging these exceptional properties, engineers and designers can continue to innovate and develop new applications for zirconia ceramics, pushing the boundaries of material science and engineering.
What are The Crystalline Structures of Zirconia and Their Applications?
Zirconia (ZrO2) exhibits multiple crystalline structures, each with distinct properties and applications:
1. Monoclinic Zirconia(m-ZrO2)
- Structure: A low-symmetry structure, stable at room temperature.
- Applications:
- Refractory materials for high-temperature application
- Ceramic pigments and glazes
2. Tetragonal Zirconia (t-ZrO2)
- Structure: A higher-symmetry structure, stable at intermediate temperatures.
- Applications:
- Structural ceramics
- High-performance ceramics for engine components
- Cutting tools
3. Cubic Zirconia (c-ZrO2)
- Structure: A high-symmetry, highly symmetric structure, stable at high temperatures.
- Applications:
- Solid oxide fuel cells (SOFCs)
- Oxygen sensors
- Cubic zirconia gemstones (simulants for diamonds)
Phase Transformations: One of the most intriguing aspects of zirconia is its ability to undergo phase transformations between these structures as temperature changes. This property, known as phase transformation toughening, significantly enhances the mechanical properties of zirconia ceramics. By controlling the phase transformation process, materials scientists can tailor the properties of zirconia ceramics to specific applications.
The low-temperature monoclinic crystal (m-ZrO2), the medium-temperature tetragonal crystal (t-ZrO2), and the high-temperature cubic crystal (c-ZrO2) exist in different temperature ranges and can be transformed into each other.

The three crystal forms of zirconium dioxide can transform into each other with the change of temperature: above 1170℃, the monoclinic phase will transform into the tetragonal phase; above 2370℃, the tetragonal phase will transform into the cubic phase.
Generally, ceramic materials are brittle and hard, but zirconia ceramics are special because of the transition between the tetragonal phase and the monoclinic phase mentioned above, which makes them more ductile. This phase transition is a martensitic transition, and its characteristics are as follows:
a. It has a nucleation growth process, and the t-m phase transition is diffusion-free and takes place in a very high temperature range. The atoms undergo orderly displacement, but the displacement is less than one atomic distance, and the adjacent atoms remain adjacent after the phase transition;
b. The t-m phase transition is accompanied by a large volume change (3%-5%) and shear strain (1%-7%), and the phase transition is reversible. When heated, the m-t phase transition will occur again;
c. The t-m phase transition temperature is determined by the grain size and external force. The finer the grain, the lower the phase transition temperature. When the external pressure is higher than 3700MPa, the tetragonal zirconia can be retained to room temperature.
Stabilized Zirconia: Pure zirconium dioxide will undergo t-m phase transition, which can easily cause the product to break and lose its practical value. Therefore, in the production process, Y2O3, CeO2, CaO and MgO are often used to stabilize zirconia ceramics. The principle is to introduce these metal ions Y3+, Ca2+, Mg2+, Ce2+, etc. into the crystal structure of zirconia to replace Zr4+ to form a solid solution, so that the tetragonal zirconia can be retained at room temperature without phase change, thereby stabilizing the zirconia ceramic material.
By understanding the various crystalline structures of zirconia and the factors influencing their stability, researchers and engineers can develop innovative materials with tailored properties to meet the demands of modern technology.
What are The Types of Zirconia Ceramics?
1.Based on their crystalline structure and stabilization methods.
Here are the primary types:
1. Partially Stabilized Zirconia (PSZ)
- Stabilization: Typically stabilized with yttria (Y2O3) or magnesia (MgO).
- Properties: High strength, toughness, and thermal shock resistance.
- Applications: Engine components, cutting tools, and structural ceramics.
2. Fully Stabilized Zirconia (FSZ)
- Stabilization: Fully stabilized with yttria or other stabilizing oxides.
- Properties: Excellent thermal and chemical stability.
- Applications: Solid oxide fuel cells (SOFCs), oxygen sensors, and high-temperature applications.
3. Tetragonal Zirconia Polycrystal (TZP)
- Structure: Primarily composed of tetragonal zirconia crystals.
- Properties: High strength, toughness, and wear resistance.
- Applications: Dental implants, cutting tools, and structural ceramics.
4. Yttria-Stabilized Zirconia (YSZ)
- Stabilization: Stabilized with yttria.
- Properties: Excellent ionic conductivity, high thermal shock resistance, and chemical stability.
- Applications: Solid oxide fuel cells, oxygen sensors, and thermal barrier coatings.
5. Ceria-Stabilized Zirconia (CSZ)
- Stabilization: Stabilized with ceria (CeO2).
- Properties: High ionic conductivity, especially at lower temperatures.
- Applications: Solid oxide fuel cells, oxygen sensors, and catalytic converters.
The choice of zirconia ceramic type depends on the specific application requirements, such as mechanical strength, thermal shock resistance, chemical resistance, electrical conductivity, and biocompatibility. By understanding the unique properties of each type, engineers and designers can select the optimal zirconia ceramic for their needs.
2.Based on purity of ZrO2.
While the purity of ZrO2 is a crucial factor in determining the performance of zirconia ceramics, the primary classification is based on their crystalline structure and stabilization methods. However, higher purity ZrO2 generally leads to better performance in terms of strength, toughness, and thermal shock resistance.
Here’s a brief overview of how purity can influence the performance of zirconia ceramics:
1.High-Purity ZrO2 (typically >99.5%):
- Enhanced Properties: Higher purity ZrO2 leads to ceramics with superior properties, such as increased strength, improved thermal shock resistance, and better electrical insulation.
- Reduced Impurities: Fewer impurities in the starting material minimize defects and imperfections in the ceramic structure, leading to enhanced performance.
- Precise Control: High-purity ZrO2 allows for more precise control over the manufacturing process, resulting in more consistent and reliable ceramic products.
2.Lower-Purity ZrO2 (typically <99.5%):
- Degraded Properties: Lower-purity ZrO2 can lead to ceramics with reduced performance, such as decreased strength, increased porosity, and lower thermal conductivity.
- Increased Impurities: Impurities can act as defects, weakening the ceramic structure and reducing its overall performance.
- Less Consistent Properties: Lower-purity ZrO2 can result in variations in the final properties of the ceramic, making it more difficult to control the manufacturing process.
In conclusion, while the specific classification of zirconia ceramics is not directly based on purity, the purity of the starting materials and the processing techniques used can significantly impact the final properties of the ceramic. High-purity ZrO2 is generally preferred for applications that require superior performance and reliability.
What are The Advantages of Zirconia Ceramics?
Zirconia ceramics offer a unique combination of properties that make them highly desirable for a wide range of applications. Here are some of the key advantages:
- Exceptional Strength and Toughness: Zirconia ceramics are 5 times stronger than traditional porcelain, making them highly resistant to fracture and wear.
- Excellent Thermal Shock Resistance: They can withstand temperature changes of up to 1000°C without cracking or breaking.
- Good Chemical Resistance: Zirconia ceramics are resistant to corrosion from a wide range of chemicals, making them ideal for use in harsh environments.
- High Melting Point: They have a melting point of over 2700°C, allowing them to withstand extreme temperatures.
- Low Thermal Conductivity: Zirconia ceramics are poor conductors of heat, making them suitable for thermal insulation applications.
- Biocompatibility: Certain forms of zirconia are biocompatible, making them ideal for medical implants and dental restorations.
- Aesthetic Appeal: Zirconia can be polished to a high luster, making it attractive for jewelry and other decorative applications.
- Phase Transformation Toughening: Zirconia undergoes a phase transformation under stress, absorbing energy and preventing crack propagation, making it up to 10 times tougher than traditional ceramics.
In conclusion, Zirconia ceramics, with their exceptional properties, have established themselves as a versatile and high-performance material across various industries. Their unique combination of strength, toughness, thermal shock resistance, chemical resistance, and biocompatibility makes them suitable for a wide range of applications.
What are The Disadvantages of Zirconia Ceramics?
While zirconia ceramics offer numerous advantages, they also have some limitations:
- Cost: Zirconia ceramics can be more expensive than traditional ceramic materials due to the complex manufacturing processes involved.
- Difficulty in Machining: Zirconia is a hard material, making it more difficult to machine and shape compared to other ceramics.
- Potential for Chipping: While zirconia is highly durable, it can still chip or fracture under extreme stress, especially in thin sections.
- Limited Color Options: Zirconia can be challenging to color match to natural teeth, especially in the case of monolithic zirconia crowns.
- Potential Wear on Opposing Teeth: The hardness of zirconia can lead to increased wear on opposing teeth over time.
Despite these limitations, zirconia ceramics remain a valuable material with a wide range of applications, and ongoing research and development continue to address these challenges.
What are The Applications of Zirconia Ceramics?
These are just some of the many applications of zirconia ceramics, showcasing its versatility and importance in modern technology.
- Dental Implants and Crowns: Biocompatible and aesthetically pleasing.
- Orthopedic Implants: High strength and biocompatibility for implants like hip and knee replacements.
- Cutting Tools: Exceptional hardness and wear resistance for cutting tools.
- Engine Components: High-temperature resistance and thermal shock resistance for engine parts like spark plug insulators and oxygen sensors.
- Solid Oxide Fuel Cells (SOFCs): Ionic conductivity for efficient energy conversion.
- Oxygen Sensors: Ability to conduct oxygen ions at high temperatures for accurate oxygen sensing.
- Electronic Components: Electrical insulation and high-temperature stability for various electronic components.
- Refractory Materials: High melting point and thermal shock resistance for furnace linings and other high-temperature applications.
- Wear-Resistant Coatings: Protective coatings for surfaces exposed to wear and corrosion.
- Ceramic Bearings: High hardness and low friction for high-performance bearings.
- Jewelry: Cubic zirconia as a popular diamond simulant.
- Thermal Barrier Coatings: Protection of surfaces from extreme heat, especially in aerospace applications.
- Laboratory Equipment: Crucibles, tubes, and other labware that require high temperature and chemical resistance.
- Fuel Cell Components: Key components in solid oxide fuel cells for clean energy generation.
- Sensor Technology: Various sensors, including gas sensors and pressure sensors.
- Medical Devices: Surgical instruments, implants, and other medical devices.
- Automotive Components: Various components like valve seats, spark plug insulators, and turbocharger components.
- Aerospace Components: High-temperature components for jet engines and rocket engines.
- Nuclear Industry: Components for nuclear reactors and waste storage.
- Optical Components: Lenses, mirrors, and other optical components due to their optical transparency and hardness.
What are the Challenges in Machining Zirconia Ceramics?
Zirconia ceramics, renowned for their exceptional mechanical properties, pose unique challenges during machining due to their inherent characteristics:
1. Extreme Hardness and Brittleness
- Rapid Tool Wear: Zirconia’s high hardness leads to rapid wear of cutting tools, especially traditional carbide tools. This necessitates the use of specialized diamond-tipped or polycrystalline diamond (PCD) tools, which are significantly more expensive.
- Susceptibility to Chipping and Cracking: The brittle nature of zirconia makes it prone to chipping and cracking, particularly under high cutting forces and temperatures. This can result in tool breakage, poor surface finish, and reduced dimensional accuracy.
2. Thermal Shock Sensitivity
- Localized Heat Buildup: Zirconia’s low thermal conductivity can lead to localized heat buildup at the cutting tool-workpiece interface. This can cause thermal stresses and potential thermal shock, resulting in cracking and degradation of the workpiece.
- Necessity for Effective Cooling: To mitigate thermal shock, effective cooling strategies are essential. This often involves the use of water-based coolants or cryogenic cooling methods, which can complicate the machining process.
3. Tool Selection and Geometry
- Specialized Tooling: The extreme hardness of zirconia necessitates the use of specialized tools, such as diamond-tipped tools or PCD inserts. These tools are designed to withstand the high cutting forces and abrasive nature of the material.
- Optimized Tool Geometry: The geometry of the cutting tool, including factors like rake angle, clearance angle, and edge radius, must be carefully designed to minimize cutting forces, reduce heat generation, and improve chip evacuation.
4. Machining Techniques
- Grinding: Grinding is often preferred over traditional cutting methods due to its lower risk of chipping and better control over surface finish. However, it requires precise control over grinding wheel speed, feed rate, and depth of cut.
- Electrical Discharge Machining (EDM): EDM can be used to machine complex shapes in zirconia, but it can be time-consuming and requires specialized equipment and expertise.
- Ultrasonic Machining: Ultrasonic machining employs high-frequency vibrations to remove material, reducing the cutting forces and minimizing the risk of thermal damage. However, it is a relatively slow process.
5. Surface Finish and Dimensional Accuracy
- Surface Integrity: Achieving a desired surface finish on zirconia can be challenging due to its hardness and brittleness. Poor surface finish can lead to stress concentrations and reduced component performance.
- Post-Machining Finishing: Additional finishing processes, such as polishing or lapping, may be required to achieve the desired surface finish and dimensional accuracy.
6. Cost Implications
- Specialized Tooling: The need for specialized tooling, such as diamond-tipped tools, can significantly increase the cost of machining zirconia components.
- Longer Processing Times: Due to the slower cutting speeds and frequent tool changes required, machining zirconia can be a time-consuming process.
- Higher Energy Consumption: The higher cutting forces and longer processing times associated with machining zirconia can lead to increased energy consumption.
To address these challenges, continuous advancements in machining technologies, tool materials, and cooling techniques are being made. However, machining zirconia remains a complex and specialized process that requires careful planning and execution.
What are the Advantages of Zirconia Ceramics Over Alumina Ceramic
While both zirconia and alumina ceramics are high-performance materials, zirconia offers several distinct advantages:
1. Superior Toughness:
- Zirconia exhibits significantly higher toughness than alumina, making it more resistant to fracture and chipping. This is due to a phenomenon known as transformation toughening, where the material undergoes a phase transformation under stress, absorbing energy and preventing crack propagation.
2. Higher Strength:
- Zirconia ceramics often possess higher flexural strength compared to alumina ceramics, especially at elevated temperatures. This makes them suitable for applications requiring high mechanical performance.
3. Better Thermal Shock Resistance:
- Zirconia ceramics can withstand rapid temperature changes more effectively than alumina, reducing the risk of thermal shock failure.
4. Improved Wear Resistance:
- In certain applications, zirconia can offer better wear resistance, particularly in abrasive environments.
However, it’s important to note that the choice between zirconia and alumina ceramics depends on the specific application requirements. Alumina ceramics often offer advantages in terms of cost, electrical insulation, and thermal conductivity.
In summary, zirconia ceramics excel in applications that demand high toughness, strength, and thermal shock resistance, while alumina ceramics are often preferred for their cost-effectiveness and electrical properties.
How is Zirconia Ceramic Manufactured?
Zirconia ceramics are produced through a series of key steps,each contributing to the final properties of the material:
1. Powder Preparation:
- Zirconium Dioxide (ZrO2) Powder: High-purity zirconium dioxide powder is the primary raw material.
- Stabilizer Addition: Stabilizing agents like yttria (Y2O3) or ceria (CeO2) are added to prevent phase transformations and improve the material’s properties.
- Mixing and Milling: The powder and stabilizer are thoroughly mixed and milled to achieve a fine, homogeneous powder.
2. Forming:
Zirconia ceramics can be formed into various shapes and sizes using a variety of techniques such as dry pressing, isostatic pressing, grouting, hot die casting, tape casting, injection molding, plastic extrusion, colloidal solidification, etc. Among them, the most widely used are isostatic pressing and dry pressing:
1) Isostatic Pressing
Isostatic pressing offers several advantages:
- Uniform Density: Pressure is applied uniformly from all directions, resulting in a highly dense and uniform microstructure.
- Complex Shapes: The technique can produce intricate shapes that are difficult to achieve with other methods.
- High Precision: Precise control over dimensions and tolerances.
- Reduced Shrinkage: Lower sintering shrinkage compared to other methods.
2) Dry Pressing
Dry pressing is a widely used technique, especially for producing simple shapes:
- High Production Rates: It is a relatively fast and efficient process.
- Lower Cost: Requires less complex tooling compared to other methods.
- Good Dimensional Control: Precise control over the dimensions of the final product.
Powder Preparation for Forming
Before forming, zirconia powder often requires specific preparation to improve its flowability and compactibility. This typically involves:
- Particle Size Reduction: Grinding the powder to a fine particle size.
- Surface Modification: Treating the powder surface with surfactants or other additives to improve its properties.
- Mixing and Blending: Homogenizing the powder with binders, lubricants, and other additives.
By carefully controlling these factors, manufacturers can produce high-quality zirconia ceramic components with desired properties.
3. Drying:
Drying is a crucial step in the production of zirconia ceramic powders, especially those prepared via liquid-phase methods. The goal of drying is to remove the moisture content from the powder, ensuring optimal powder properties for subsequent processing steps.
Here are some common drying techniques used for zirconia ceramic powders:
1). Hot Air Drying
- How it works: Hot air is circulated over the wet powder to evaporate the moisture.
- Advantages: Simple and cost-effective.
- Disadvantages: Can lead to particle agglomeration and potential damage to the powder structure, especially for heat-sensitive materials.
2). Infrared Drying
- How it works: Infrared radiation heats the powder directly, causing the moisture to evaporate.
- Advantages: Faster drying times and reduced risk of thermal damage compared to hot air drying.
- Disadvantages: Requires specialized infrared equipment.
3). Spray Drying
- How it works: A slurry of the ceramic powder is atomized into fine droplets and dried in a hot gas stream.
- Advantages: Produces spherical particles with uniform size distribution, excellent flowability, and high surface area.
- Disadvantages: High energy consumption and potential for particle agglomeration if not controlled properly.
4). Freeze Drying
- How it works: The wet powder is frozen and then subjected to vacuum conditions, causing the ice to sublime directly into vapor.
- Advantages: Preserves the delicate structure of the powder, minimizes particle agglomeration, and produces highly porous materials.
- Disadvantages: Slow and energy-intensive process.
Spray Drying for Zirconia Ceramic Powders Spray drying is a popular technique for drying zirconia powders, particularly for applications like mobile phone ceramic back panels. This method offers several advantages:
- Nano-scale Particles: Produces fine, nano-sized particles with high surface area.
- Improved Flowability: The spherical particles exhibit excellent flowability, making them suitable for various processing techniques.
- Enhanced Sintering: The high surface area promotes sintering and densification, leading to improved mechanical properties.
By carefully selecting the appropriate drying technique, manufacturers can optimize the properties of zirconia ceramic powders and ensure the production of high-quality ceramic components.
4. Sintering:
Sintering is a crucial step in the production of zirconia ceramics. It involves heating the green body, a porous ceramic compact, to a high temperature to densify the material and develop its desired properties.
Sintering Mechanisms
During sintering, several mechanisms contribute to densification:
Initial Stage:
- Particle Rearrangement: Particles rearrange themselves to minimize the total surface energy.
- Neck Growth: Neck formation between particles begins, reducing porosity.
Intermediate Stage:
- Grain Growth: Particles grow and coalesce, further reducing porosity.
- Pores Shrinkage: Pores become smaller and more spherical.
Final Stage:
- Densification: The material reaches near-theoretical density.
- Grain Growth: Grain boundaries migrate, leading to larger grains.
Types of Sintering
Conventional Sintering:
- Solid-State Sintering: The most common method, involving heating the green body in a furnace.
- Liquid-Phase Sintering: A sintering aid is added to form a liquid phase, which aids in densification.
Pressure-Assisted Sintering:
- Hot Pressing: The green body is heated and pressed simultaneously, accelerating densification.
- Hot Isostatic Pressing (HIP): The green body is heated and pressurized isostatically, resulting in high-density and uniform microstructures.
Microwave Sintering:
- Microwaves directly heat the ceramic material, leading to rapid heating and sintering.
Factors Affecting Sintering of Zirconia Ceramics
- Powder Characteristics: Particle size, shape, and purity influence sintering behavior.
- Additives: Sintering aids can enhance densification and control microstructure.
- Sintering Temperature and Time: Higher temperatures and longer times promote densification but can also lead to excessive grain growth.
- Atmosphere: The sintering atmosphere can affect the oxidation state of zirconia and the formation of secondary phases.
- Heating Rate: A controlled heating rate is essential to avoid thermal shock and cracking.
By carefully controlling these factors, manufacturers can produce high-quality zirconia ceramics with desired properties, such as high strength, toughness, and thermal shock resistance.
5. Machining :
- If necessary, the sintered components are machined to achieve precise dimensions and surface finishes.
6. Finishing :
Once the zirconia ceramic components have been sintered, they undergo a series of post-processing steps to achieve the desired final form and surface finish. These steps typically include:
- Cutting: Sintered components are cut into precise sizes and shapes using specialized cutting tools.
- Grinding: The surfaces of the cut components are ground to remove any sharp edges and irregularities.
- Polishing: A multi-step polishing process is employed to achieve the desired level of surface finish, ranging from matte to high-gloss. This involves using progressively finer abrasive particles and polishing compounds.
7.Quality Control
Rigorous quality control is essential throughout the entire manufacturing process of zirconia ceramics. The final products undergo a comprehensive inspection to ensure they meet specific performance and quality standards. Key inspection criteria include:
- Dimensional Accuracy: Verifying that the components conform to the specified dimensions and tolerances.
- Surface Quality: Assessing the surface finish for any defects, such as scratches, pits, or cracks.
- Mechanical Properties: Testing the hardness, strength, and toughness of the material to ensure it meets the required performance standards.
- Microstructural Analysis: Examining the microstructure of the ceramic to evaluate the grain size, porosity, and phase composition.
By implementing strict quality control measures, manufacturers can guarantee the reliability and durability of zirconia ceramic products for a wide range of applications.
By carefully controlling each step of the manufacturing process, it is possible to produce zirconia ceramic components with a wide range of properties and applications.
Why Does Zirconia Ceramics Turn Yellow After Sintering?
The yellowing of zirconia ceramics post-sintering can be attributed to several factors:
1. Contamination:
- Sagger or Layer Firing Plate: New, unfired saggers or plates can release impurities during the sintering process, leading to discoloration.
- Furnace Contamination: Internal contaminants within the furnace can affect the color of the ceramics.
2. Processing Conditions:
- High Temperature: Excessive temperatures can cause oxidation and discoloration.
- Poor Ventilation: Inadequate ventilation can lead to a reducing atmosphere, promoting the formation of color centers.
- Overcrowding: Overloading the furnace can hinder heat transfer and airflow, leading to uneven heating and discoloration.
3. Material Composition:
- Impurities: Impurities, particularly iron, can cause yellowing when oxidized.
- Yttria Doping: Excessive yttria doping can also contribute to color changes.
- Hafnium Oxide: The presence of hafnium oxide in zirconia powder can influence the color.
4. Sintering Atmosphere:
- Reducing Atmosphere: A reducing atmosphere can lead to the formation of color centers, causing the ceramics to appear yellow.
Treating Yellowed Zirconia Ceramics
While it’s challenging to reverse the yellowing after sintering, here are some tips for preventing it:
- Pre-fire Saggers and Plates: Ensure that these components are well-fired before use to minimize contamination.
- Optimize Sintering Conditions: Control the temperature, atmosphere, and heating rate to prevent excessive oxidation and color center formation.
- Use High-Purity Materials: Select zirconia powders with low impurity levels, especially iron.
- Control Yttria Doping: Avoid excessive doping to prevent color changes.
- Consider Alternative Sintering Techniques: Explore techniques like hot isostatic pressing (HIP) or microwave sintering to achieve better control over the sintering process.
By addressing these factors and implementing appropriate measures, it’s possible to produce high-quality, white zirconia ceramics.
Note: The specific causes of yellowing in a particular case may vary, and a thorough analysis of the process parameters and material composition is necessary to identify the root cause and implement corrective actions.
What are The Difficulties in Processing Zirconia Ceramics?
Zirconia ceramics, while offering exceptional properties, present unique challenges during manufacturing. Traditional mechanical processing techniques, such as turning, milling, and grinding, often result in surface damage and low efficiency. Additionally, methods like sandblasting and acid etching can contaminate the material or alter its physical and chemical properties.
Key Challenges and Potential Solutions:
Surface Damage and Finish:
- Diamond Grinding: A highly effective method for achieving precise surface finishes, but it can be costly and time-consuming.
- Chemical Mechanical Polishing (CMP): A promising technique for achieving mirror-like finishes, but it requires careful control of process parameters.
- Laser Polishing: A non-contact method that can produce high-quality surfaces, but it can be expensive.
High Processing Costs:
- Advanced Tooling: Developing advanced tooling materials and techniques can reduce tool wear and increase efficiency.
- Optimized Machining Parameters: Fine-tuning cutting parameters, such as feed rate and cutting speed, can improve efficiency and reduce costs.
- Alternative Processing Techniques: Exploring alternative processing methods, such as ultrasonic machining or electrochemical machining, can offer cost-effective solutions.
Complex Microstructure Control:
- Precise Sintering Control: Careful control of sintering parameters, such as temperature and time, is crucial for achieving the desired microstructure.
- Doping and Additives: Using dopants and additives can help to modify the microstructure and improve properties.
Large Machining Allowances:
- Advanced CAD/CAM: Utilizing advanced CAD/CAM software to optimize designs and reduce the need for excessive machining.
- Precision Manufacturing Techniques: Employing high-precision manufacturing techniques, such as diamond turning and grinding, to minimize machining allowances.
By addressing these challenges and implementing innovative solutions, manufacturers can produce high-quality zirconia ceramic components that meet the demands of various industries.
Yomua’s Commitment to Quality
Yomua leverages advanced equipment, precision machining techniques, and expert knowledge to overcome the challenges associated with zirconia ceramic processing. Our comprehensive approach, from design optimization to final finishing, ensures that our products meet the highest quality standards. By partnering with Yomua, you can benefit from:
- High-Quality, High-Efficiency Processing
- Precise Control Over Surface Finish and Dimensional Accuracy
- Cost-Effective Solutions
- Reliable and Timely Delivery
Let us be your trusted partner in achieving your zirconia ceramic goals.
How to Choose a Stable Zirconia Ceramic Manufacturer ?
When selecting a stable zirconia ceramic manufacturer, consider these key factors:
1. Experience and Expertise:
- Years of Operation: A longer track record often indicates a deeper understanding of the material and its applications.
- Technical Expertise: Look for a manufacturer with in-house research and development capabilities to ensure they can address specific needs and challenges.
- Industry Certifications: Certifications like ISO 9001 demonstrate a commitment to quality management systems.
2. Quality Assurance and Testing:
- Quality Control Procedures: A robust quality control process ensures consistent product quality.
- Testing Capabilities: In-house testing facilities allow for rigorous quality checks and material analysis.
- Compliance with Standards: Adherence to industry standards like ASTM and ISO guarantees product reliability.
3. Product Range and Customization:
- Diverse Product Offerings: A wide range of zirconia ceramic products caters to various applications.
- Customization Options: The ability to tailor products to specific requirements is essential.
- Material Consistency: Consistent material properties across different batches are crucial for reliable performance.
4. Manufacturing Capabilities:
- Advanced Manufacturing Techniques: Modern manufacturing processes, such as precision machining and sintering, ensure high-quality products.
- Production Capacity: Sufficient capacity to meet your production needs, especially for large-scale projects.
- Supply Chain Reliability: A reliable supply chain minimizes disruptions and ensures timely deliveries.
5. Reliability and After-Sales Support:
- On-Time Delivery: A consistent track record of meeting delivery deadlines is crucial.
- Technical Support: Accessible technical support for troubleshooting and product inquiries.
- Warranty and Return Policies: Clear warranty terms and efficient return processes provide peace of mind.
6. Cost-Effectiveness:
- Competitive Pricing: Competitive pricing without compromising quality.
- Value for Money: Consider the total cost of ownership, including factors like product lifespan and maintenance costs.
7. Environmental Responsibility:
- Sustainable Practices: A commitment to environmentally friendly manufacturing processes and waste reduction.
- Compliance with Regulations: Adherence to environmental regulations and standards.
Additional Tips:
- Request Samples: Obtain samples to evaluate product quality, performance, and compatibility with your specific application.
- Conduct Site Visits: If possible, visit the manufacturer’s facility to assess their operations and capabilities firsthand.
- Seek Recommendations: Consult with industry experts, engineers, or other customers to gather insights and recommendations.
- Review Customer Testimonials: Positive feedback from other customers can provide valuable information about a manufacturer’s reputation and service quality.
By carefully considering these factors, you can select a stable zirconia ceramic manufacturer that meets your specific needs and delivers high-quality products
What is The Surface Treatment Methods of Zirconia Ceramics?
Zirconia ceramics have gained significant popularity in dental restorations due to their exceptional mechanical properties, biocompatibility, and aesthetic appeal. However, their inert surface can hinder optimal bonding with dental adhesives. To address this challenge, various surface treatment methods have been developed to enhance the bond strength and long-term durability of zirconia restorations.
Mechanical Surface Treatments
- Sandblasting: A high-pressure stream of abrasive particles is directed at the zirconia surface to create micro-roughness, increasing the surface area for mechanical interlocking with the adhesive.
- Laser Etching: A laser beam is used to create precise micro-pits and grooves on the zirconia surface, improving the bonding surface.
Chemical Surface Treatments
- Silane Coupling Agents: These agents improve the wettability and adhesion of zirconia surfaces by forming a chemical bond between the ceramic and the adhesive.
Emerging Surface Treatment Techniques
- Plasma Treatment: Exposing the zirconia surface to a plasma modifies the surface chemistry, creating reactive sites for better bonding.
- Ion Beam Etching: A focused ion beam is used to etch the zirconia surface, creating precise microstructures.
Key Considerations for Surface Treatment
- Surface Roughness: Adequate surface roughness is crucial for mechanical interlocking.
- Surface Energy: A higher surface energy improves the wettability of the surface by the adhesive.
- Chemical Reactivity: The surface should be chemically reactive to form a strong bond with the adhesive.
- Preservation of Mechanical Properties: The surface treatment should not compromise the mechanical properties of the zirconia.
By carefully selecting and implementing appropriate surface treatment techniques, clinicians and researchers can optimize the bond strength and long-term performance of zirconia restorations, leading to improved patient outcomes.
How Are the Different Colors of Zirconia Ceramics Made?
Zirconia ceramics, renowned for their exceptional properties, can be produced in a variety of colors. The key to achieving these diverse hues lies in the careful selection and incorporation of colorants, as well as the precise control of the sintering process.
The Science Behind the Colors
The color of a material is determined by its interaction with light. When light strikes a material, it can be absorbed, reflected, or transmitted. The specific colors we perceive are a result of the wavelengths of light that are reflected or transmitted.
In the case of zirconia ceramics, the introduction of colorants can influence the material’s optical properties. However, the high-temperature sintering process can degrade or volatilize these colorants, limiting the range of achievable colors.
Coloration Techniques
To overcome these challenges, various techniques are employed:
Incorporation of Colorants:
- Metal Oxide Colorants: Metal oxides like chromium oxide, cobalt oxide, and iron oxide are commonly used to impart specific colors.
- Rare Earth Elements: These elements can produce vibrant colors when incorporated into the zirconia lattice.
Sintering Process Control:
- Temperature: The sintering temperature significantly impacts color development. Lower temperatures can help preserve colorants, while higher temperatures may lead to color fading or loss.
- Atmosphere: The atmosphere during sintering can influence the oxidation state of the colorants and, consequently, the final color.
Post-Sintering Treatments:
- Glazing: Applying a colored glaze can enhance the aesthetic appeal and color intensity.
- Polishing: Polishing the surface can improve the color depth and clarity.
Challenges and Future Directions
While significant advancements have been made in the coloration of zirconia ceramics, challenges remain:
- High-Temperature Stability: Maintaining color intensity and preventing color fading at high temperatures.
- Limited Color Palette: Expanding the range of achievable colors, especially vibrant hues.
- Uniform Color Distribution: Ensuring consistent coloration throughout the ceramic piece.
By addressing these challenges and continuing to explore innovative techniques, researchers and manufacturers can further enhance the aesthetic appeal and functional properties of zirconia ceramics, unlocking a wide range of possibilities for diverse applications.
What is The Difference Between Zirconia Ceramics and Metal ?
Zirconia ceramics and metals, while both serving as structural materials, exhibit distinct properties.
Mechanical Properties:
Strength:
- Metals: Metals generally possess good tensile strength, allowing them to withstand significant pulling forces.
- Zirconia Ceramics: While zirconia ceramics have high compressive strength, they are relatively brittle in tension.
- Metals: Metals generally possess good tensile strength, allowing them to withstand significant pulling forces.
Elasticity and Deformation:
- Metals: Metals typically exhibit both elastic and plastic deformation. Elastic deformation is reversible, while plastic deformation is permanent. This plasticity allows metals to be shaped and formed.
- Zirconia Ceramics: Zirconia ceramics primarily undergo elastic deformation. Beyond a certain point, they fracture rather than plastically deform. This brittle nature limits their formability.
- Metals: Metals typically exhibit both elastic and plastic deformation. Elastic deformation is reversible, while plastic deformation is permanent. This plasticity allows metals to be shaped and formed.
Creep Resistance:
- Metals: Metals can experience creep, a time-dependent deformation under constant stress, especially at elevated temperatures.
- Zirconia Ceramics: Zirconia ceramics exhibit excellent creep resistance, making them suitable for high-temperature applications.
- Metals: Metals can experience creep, a time-dependent deformation under constant stress, especially at elevated temperatures.
Other Properties:
- Thermal Expansion: Zirconia ceramics have a lower coefficient of thermal expansion compared to many metals, making them more resistant to thermal shock.
- Corrosion Resistance: Zirconia ceramics are highly resistant to corrosion, especially in acidic and alkaline environments.
- Biocompatibility: Zirconia ceramics are biocompatible and widely used in dental and medical implants.
Applications:
The unique properties of zirconia ceramics make them suitable for a variety of applications, including:
- Dental Implants: Zirconia crowns and bridges are popular due to their aesthetic appeal and biocompatibility.
- Engine Components: Zirconia ceramics are used in high-temperature engine components due to their excellent thermal shock resistance and wear resistance.
- Cutting Tools: Zirconia-based cutting tools are highly durable and can withstand high temperatures and pressures.
- Electronic Components: Zirconia ceramics are used in various electronic components due to their electrical insulating properties and high thermal conductivity.
In conclusion, while both zirconia ceramics and metals have their strengths and weaknesses, their distinct properties make them suitable for different applications. Understanding these differences is crucial for selecting the appropriate material for a specific task.
What are the Production Costs of Zirconia Ceramics?
he production cost of zirconia ceramics can vary significantly based on several factors, including:
Raw Material Costs:
- High-quality zirconia powder
- Stabilizers (e.g., yttria, ceria)
- Additives (e.g., sintering aids, coloring agents)
Manufacturing Process Costs:
- Powder processing (milling, drying, sieving)
- Forming (pressing, injection molding, 3D printing)
- Sintering (high-temperature densification)
- Machining and finishing (cutting, grinding, polishing)
Energy Consumption:
- High-temperature sintering requires significant energy input
- Machining and finishing processes also consume energy
Labor Costs:Skilled technicians and operators for production and quality control
Equipment and Tooling Costs:Kilns, presses, milling machines, and other specialized equipment
Research and Development Costs:Ongoing research to improve processes and develop new products
Market Demand and Competition:Market demand and competition can influence pricing and profitability.
While it’s difficult to provide a precise figure for the production cost of zirconia ceramics, it’s generally considered a premium material due to its complex manufacturing process and high-performance properties.
How to Judge the Quality of Zirconia Structural Ceramics?
To assess the quality of zirconia ceramics, a comprehensive approach involving multiple factors is necessary. Here are some key considerations:
Visual Inspection
- Surface Finish: The surface should be smooth, free from defects like cracks, pores, or discoloration.
- Dimensional Accuracy: The ceramic component should conform to the specified dimensions and tolerances.
Physical Properties
- Density: A higher density generally indicates better sintering and improved mechanical properties.
- Porosity: Low porosity is desirable as it enhances strength and durability.
- Hardness: A high hardness rating (e.g., Mohs or Vickers) indicates resistance to scratching and wear.
- Fracture Toughness: This property measures the material’s resistance to crack propagation.
- Flexural Strength: This measures the material’s ability to resist bending stress.
Microstructural Analysis
- Grain Size and Distribution: A fine, uniform grain size is preferred for optimal mechanical properties.
- Phase Composition: The phase composition, particularly the ratio of tetragonal to monoclinic phases, influences the material’s properties.
Chemical Composition
- Purity: High-purity zirconia powder is essential for achieving desired properties.
- Impurities: The presence of impurities can degrade the performance of the ceramic.
Performance Testing
- Thermal Shock Resistance: The ability to withstand rapid temperature changes.
- Corrosion Resistance: Resistance to chemical attack, especially in harsh environments.
- Wear Resistance: Resistance to abrasion and wear.
Certification and Standards
- ISO Certification: Adherence to international quality standards.
- Industry Standards: Compliance with relevant industry standards.
Additional Tips:
- Reliable Supplier: Choose a reputable supplier with a proven track record.
- Detailed Specifications: Clearly define your requirements in terms of dimensions, tolerances, and performance properties.
- Thorough Testing: Conduct rigorous testing to verify the quality of the received products.
By carefully considering these factors and conducting thorough testing, you can ensure that you’re purchasing high-quality zirconia ceramics that meet your specific needs.Yomua’s commitment to quality is evident in their rigorous inspection process. By ensuring that each product meets customer requirements, Yomua has built a strong reputation and gained the trust of customers over the years. This dedication to quality is a core value that drives Yomua’s continued development and success.
What is The Future Directions in Zirconia Ceramic Research?
Building upon the strong foundation of zirconia ceramics, researchers are exploring several promising avenues to further enhance their performance and expand their applications:
1. Advanced Composite Materials
- Hybrid Ceramics: Combining zirconia with other ceramics, such as silicon carbide or alumina, can create composite materials with superior mechanical properties, thermal shock resistance, and wear resistance.
- Ceramic-Polymer Composites: Incorporating zirconia particles into polymer matrices can yield lightweight, flexible, and tough composites with excellent thermal and electrical properties.
2. Innovative Processing Techniques
- Additive Manufacturing: 3D printing techniques enable the fabrication of complex zirconia components with intricate geometries, minimizing material waste and reducing production time.
- Field-Assisted Sintering: Applying external fields, such as electric or magnetic fields, during sintering can accelerate the process, reduce energy consumption, and refine the microstructure.
3. Functionalization and Surface Engineering
- Surface Modification: Modifying the surface properties of zirconia through techniques like coating or ion implantation can enhance its biocompatibility, corrosion resistance, and catalytic activity.
- Doping and Alloying: Introducing dopants or alloying elements into the zirconia lattice can tailor its electrical, optical, and magnetic properties for specific applications.
4. In-Situ Characterization
- Real-Time Monitoring: Employing advanced characterization techniques, such as in-situ X-ray diffraction and neutron scattering, allows researchers to study the microstructure evolution and phase transformations during processing and service conditions.
- Multiscale Modeling: Developing multiscale modeling approaches can provide insights into the relationship between microstructure, processing conditions, and macroscopic properties, enabling the design of optimized zirconia materials.
By pursuing these research directions, scientists and engineers aim to unlock the full potential of zirconia ceramics, leading to groundbreaking advancements in fields like aerospace, automotive, energy, and healthcare.
Zirconia ceramics Conclusion
Zirconia ceramics have emerged as a versatile material with exceptional properties, finding applications in diverse industries. Their high strength, durability, and resistance to extreme conditions make them ideal for demanding applications. Yomua, a leading manufacturer of zirconia ceramics, has been at the forefront of technological advancements in this field. By consistently delivering high-quality products and meeting customer requirements, Yomua has solidified its position as a trusted partner in the industry. As technology continues to evolve, zirconia ceramics are poised to play an even greater role in shaping the future of materials science.