Silicon Nitride (Si3N4) Ceramic Components
Top Quality Manufacturer
- High-Quality Manufacturing Solutions
- Four Decades of Industry Expertise
- Stringent Quality and Environmental Standards
- Fast Turnaround, Global Delivery
Get a Quote Today
Trusted Silicon Nitride (Si3N4) Ceramic Ceramic Components Manufacturer
WHy Yomua Silicon Nitride (Si3N4) Ceramic
- Precision Manufacturing: Our advanced machinery and equipment deliver exceptional accuracy and precision.Yomua utilize the latest technology to optimize production processes and enhance quality.
- Transparent Pricing: Our competitive pricing and upfront costs ensure budget certainty, backed by over 40 years of manufacturing experience.
- End-to-End Solutions: From design to mass production, we’ve got you covered. Our tailored solutions ensure that your project meets your specific needs and requirements.
- Quality Guaranteed: Our dedicated QC team and skilled technicians are committed to ensuring every project meets the highest standards.
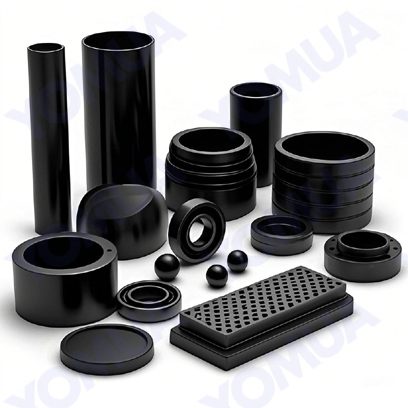
Custom Silicon Nitride (Si₃N₄) Ceramic Parts
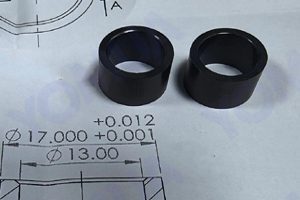
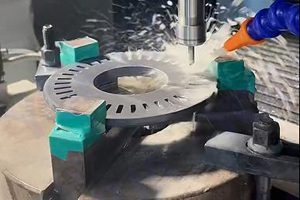
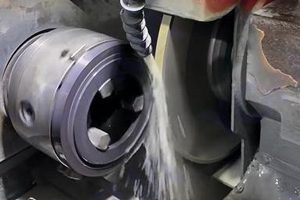
- Not Only Your Partner, But Your Dedicated Team:Our dedicated team at YOMUA is committed to your success. We collaborate closely with you to provide the high-performance zirconia solutions that meet your unique needs.
Silicon Nitride (Si3N4) Properties
Property Item | Units | Typical Values |
Material characteristics | ||
Density | g/cm3 | >3.2 |
Physical Property | ||
Hardness | HRA | 90 |
Vickers Hardness (Hv50) | HV0.5 | >1550 |
Modulus of Elasticity | Gpa | 290 |
Flexural Strength | Mpa | >600 |
Compressive Strength | Mpa | 2500 |
Fracture toughness | MPam 1/2 | >6.0 |
Thermodynamic Property | ||
Maximum Use Temperature | °C | 1200 |
Thermal Conductivity | W/(m.K) | 15-20 |
Thermal Expansion Coefficient | 10-6/°C | >3.1 |
Thermal Shock Resistance | ΔT°C | 500 |
Specific Heat Capacity | KJ/kg.K | 700 |
Electrical Property | ||
Dielectric Strength | KV/mm | 1 |
Dielectric Constant | εr | |
Volume Resistivity at 20°C | Ω.cm | 1.0×10^12 |
Note: The data provided is for general design reference purposes only. Actual material properties may exhibit variation depending on specific products. For precise and accurate information, please contact Yomua.
Silicon Nitride (Si3N4) Ceramic Products
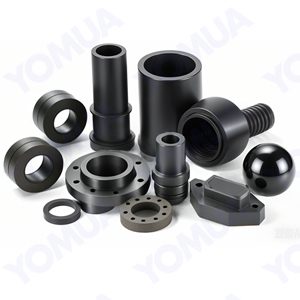
Customized Silicon Nitride (Si3N4) Ceramic Parts
Engineered components with tailored shapes and properties, designed to meet specific performance requirements in demanding applications.
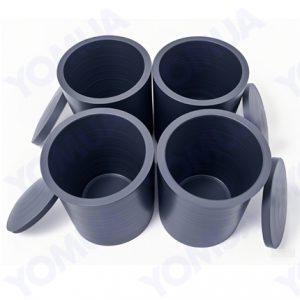
Silicon Nitride (Si3N4) Ceramic Crucible
Silicon Nitride (Si3N4) Ceramic Crucibles find extensive use in Melting and casting of high-temperature alloys ,Semiconductor Industry and Chemical Analysis.
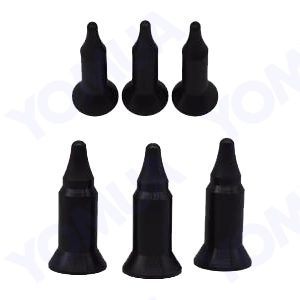
Silicon Nitride (Si3N4) Welding Pin
Silicon nitride (Si3N4) welding pins are precision-engineered components used in advanced manufacturing processes, particularly used for precise alignment and positioning.
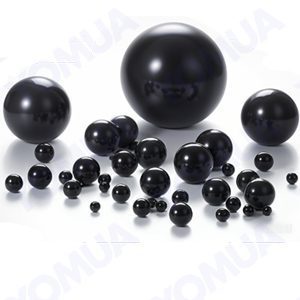
Silicon Nitride Si3N4 Ceramic Ball
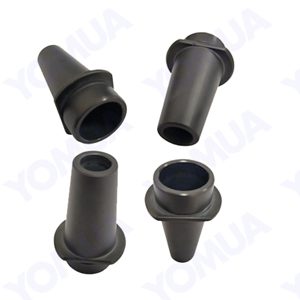
Silicon Nitride Si3N4 Ceramic nozzle
Silicon nitride (Si3N4 ) ceramic nozzles offer a significant advantage over traditional materials due to their exceptional properties,offering exceptional wear resistance, thermal stability, and corrosion resistance.
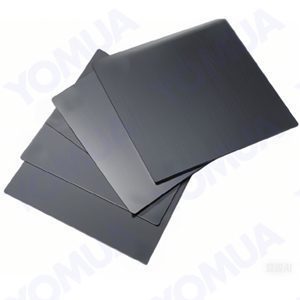
Silicon Nitride Si3N4 Ceramic Plate
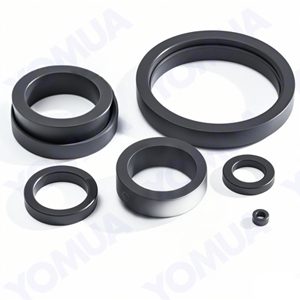
Silicon Nitride (Si3N4) Seal Ring
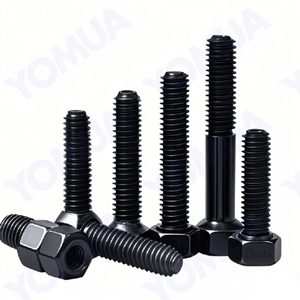
Silicon Nitride Si3n4 Ceramic Screw Bolt Nut
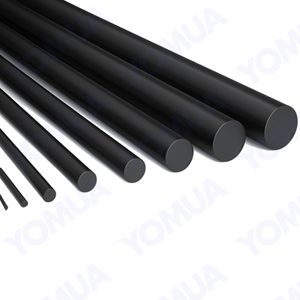
Silicon Nitride Si3N4 Ceramic Rod
Highly precise and stable, offering excellent heat resistance and chemical inertness that make them ideal for various industries: electronics, aerospace, and medical devices etc.,
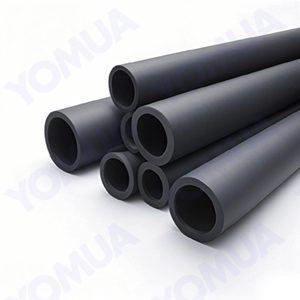
Silicon Nitride Si3N4 Ceramic Tube
Silicon Nitride Si3N4 Ceramic Tubes are utilized in high-temperature applications, such as thermocouple protection sheaths and components in molten metal handling.
Customer Testimonials for Yomua Silicon Nitride Ceramic...

Customer Satisfaction, Yomua's Top Priority



Silicon Nitride (Si₃N₄) Ceramic Related Products
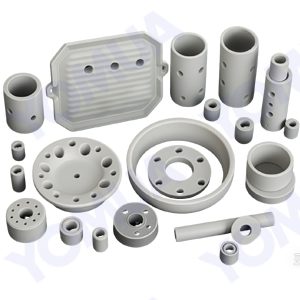
Boron Nitride(BN) Ceramics
High thermal conductivity, electrical resistance, and stability at extreme temperatures.
Silicon Nitride (Si3N4) Ceramic Components Guide
Frequently Asked Questions
What is Silicon Nitride or Si3N4 ?
Silicon nitride is a chemical compound with the formula Si3N4. It consists of silicon (Si) and nitrogen (N) atoms, specifically in a ratio of three silicon atoms to four nitrogen atoms. It exhibits exceptional strength, hardness, and resistance to thermal shock and chemical attack. These attributes make it a valuable material in a wide range of applications across various industries.
- Chemical Formula: Si3N4
- CAS Registry Number: 12033-89-5
- PubChem Compound ID: 3084099
- SMILES Identifier: N12[Si]34N5[Si]16N3[Si]25N46
- Appearance: White powder crystals, often appearing gray due to impurities or excess silicon.
- Density: Approximately 3.44 g/cm³ at room temperature.
- Melting Point: Decomposes at around 1900°C under normal pressure. The melting point can vary under different pressures.
- Crystal Structure: Silicon nitride exists in three primary crystal structures: α, β, and γ. The α and β phases are the most common forms found under normal conditions. The γ phase, which is significantly harder, can only be synthesized under high pressure and temperature.
What is Silicon Nitride Ceramic or Si3N4 Ceramic?
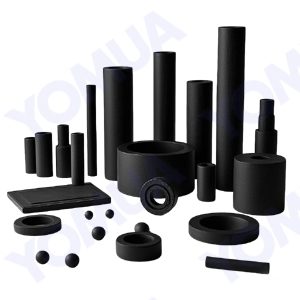
Silicon Nitride Ceramics, Represented by the Chemical Formula si3n4, Are Advanced Ceramic Materials Composed of Silicon and Nitrogic Ratio. It is a new type of inorganic non -metallic ceramic material with silicon nitride (si₃n₄).his unique structure grants Si3N4Ceramic a remarkable combination of characteristics.Si₃N₄ ceramics is a covalent -key compound, and the basic structural unit is (SIN4) all sides. The silicon atom is located in the center of the tetraonal body. There are four nitrogen atoms around them, which are located in the four vertices of the tetraonal body, and then form a continuous and solid network structure in the three -dimensional space in the form of one atom in three dimensions. This structure makes silicon nitride ceramics have high hardness, strength and stability.
What are the Properties of Silicon Nitride Ceramic or Si3N4 Ceramic?
Silicon nitride (Si3N4) ceramics are a class of materials renowned for their exceptional properties, making them suitable for a wide range of demanding applications.
Key Properties of Silicon Nitride Ceramics:
Mechanical Properties:
- High Strength: Si3N4 ceramics exhibit remarkable mechanical strength, maintaining high levels even at elevated temperatures. This property is crucial for applications involving significant mechanical stress.
- High Hardness: With a high degree of hardness, Si3N4 ceramics are highly resistant to wear and abrasion. This makes them ideal for components that experience friction and contact stresses.
- High Fracture Toughness: This property enables Si3N4 ceramics to withstand significant impact loads without cracking or breaking, making them suitable for applications where sudden impacts or stress concentrations are present.
Thermal Properties:
- High Thermal Stability: Si3N4 ceramics possess excellent thermal stability, with a high melting point of around 1900°C. This allows them to withstand extreme temperatures without degradation.
- Low Coefficient of Thermal Expansion: This property minimizes thermal expansion and contraction, reducing the risk of thermal stress-induced cracking, especially during rapid temperature changes.
- Resistance to Thermal Shock: Si3N4 ceramics can endure rapid temperature fluctuations without fracturing, making them suitable for applications involving frequent thermal cycling, such as cutting tools and engine components.
Chemical Properties:
- Chemical Inertness: Si3N4 ceramics are highly resistant to chemical attack from most acids and bases, making them suitable for use in corrosive environments.
- Oxidation Resistance: Si₃N₄ ceramics exhibit excellent oxidation resistance, protecting them from degradation at high temperatures.
Physical Properties:
- Low Density: Si3N4 ceramics have a relatively low density compared to other ceramic materials, making them lightweight and energy-efficient. This is particularly advantageous in aerospace and automotive applications.
- Good Electrical Insulation: Si3N4 ceramics are good electrical insulators, making them suitable for electronic components and applications where electrical conductivity must be minimized.
In Conclusion:
In conclusion, silicon nitride ceramics offer a unique blend of properties that make them valuable materials for a wide range of demanding applications. Their exceptional mechanical, thermal, and chemical properties, combined with their low density and good electrical insulation, contribute to their widespread use in industries.
What are The Crystalline Structures of Silicon Nitride ?
Silicon nitride (Si3N4 ) is a versatile ceramic material that crystallizes into different structures, each with unique properties. The two primary stable polymorphs under ambient conditions are α-Si₃N₄ and β-Si₃N₄.
1. α-Si₃N₄
- Crystal System: Trigonal
- Space Group: P31c (159)
- Lattice Parameters: a = 775.193 pm, c = 561.949 pm
- Structure: The α-phase consists of a network of corner-sharing SiN₄ tetrahedra arranged in hexagonal rings, stacked in an ABCDABCD… sequence.
2. β-Si₃N₄
- Crystal System: Hexagonal
- Space Group: P6₃/m (176)
- Lattice Parameters: a = 760.8 pm, c = 291.1 pm
- Structure: Similar to the α-phase, the β-phase also comprises corner-sharing SiN₄ tetrahedra, but with a different stacking sequence of ABAB….
3. High-Pressure Phase (γ-Si3N4 )
- Crystal System: Cubic
- Structure: Spinel structure
- Stability: Stable only under high-pressure and high-temperature conditions.
Silicon nitride (Si₃N₄) exists in several crystalline forms, each with distinct properties. Here’s a table summarizing the key characteristics of the primary phases:
Phase | Crystal System | Space Group | Lattice Parameters | Structure |
---|---|---|---|---|
α-Si3N4 | Trigonal | P31c (159) | a = 775.193 pm, c = 561.949 pm | Network of corner-sharing SiN₄ tetrahedra in hexagonal rings, stacked in an ABCDABCD… sequence. |
β-Si₃N₄ | Hexagonal | P6₃/m (176) | a = 760.8 pm, c = 291.1 pm | Similar to α-phase, but with ABAB… stacking sequence of SiN₄ tetrahedra. |
γ-Si₃N₄ | Cubic | – | – | Spinel structure, stable only under high pressure and temperature. |
Note: The γ-phase is a high-pressure phase and is not typically encountered in standard conditions.
Impact of Crystalline Structure on Properties
The distinct crystalline structures of silicon nitride significantly influence its mechanical properties, such as:
- Hardness: The strong Si-N bonds within the crystal lattice contribute to the high hardness of Si3N4 ceramics.
- Strength: The interconnected network of tetrahedra provides excellent strength and resistance to deformation.
- Fracture Toughness: The presence of different crystallographic planes and the ability to deflect cracks can enhance fracture toughness.
- Thermal Shock Resistance: The low thermal expansion coefficient and high thermal conductivity of Si3N4 help to mitigate thermal stress and prevent cracking.
By understanding the crystallographic structures of silicon nitride, researchers and engineers can tailor its properties for specific applications and develop advanced materials with enhanced performance.
What are The Types of Nitride Ceramic (Si3N4 ) Ceramics?
Silicon nitride ceramics are a class of materials with exceptional properties, making them suitable for a wide range of applications. Here’s a breakdown of the primary types, incorporating additional details:
1. Reaction-Bonded Silicon Nitride (RBSN)
- Manufacturing Process: Silicon powder is compacted and then heated to around 1450°C in a nitrogen-rich atmosphere. A reaction occurs, converting silicon to silicon nitride.
- Properties: RBSN is relatively porous, typically around 30%, which can limit its strength and toughness. However, it offers good thermal shock resistance and is cost-effective to produce.
- Applications: Refractory materials, wear components in low-stress environments, kiln furniture.
2. Hot-Pressed Silicon Nitride (HPSN)
- Manufacturing Process: Silicon nitride powder, along with additives like magnesium oxide, is pressed under high pressure (around 40 MPa) and high temperature (around 1800°C).
- Properties: HPSN is a dense material with excellent mechanical properties, including high strength, hardness, and wear resistance.
- Applications: Cutting tools, engine components, and high-performance bearings.
3. Sintered Reaction-Bonded Silicon Nitride (SRBSN)
- Manufacturing Process: RBSN is further sintered at high temperatures to reduce porosity and improve mechanical properties.
- Properties: SRBSN has lower porosity compared to RBSN, resulting in enhanced strength and toughness.
- Applications: Cutting tools, wear components, and structural components.
4. Gas Pressure Sintered Silicon Nitride (GPSN)
- Manufacturing Process: Silicon nitride powder is sintered under high nitrogen pressure (1-10 MPa) at temperatures around 2000°C.
- Properties: GPSN is a highly dense material (over 99% density) with excellent mechanical properties, including high strength, toughness, and wear resistance.
- Applications: High-performance engine components, cutting tools, and structural components.
5. Sintered Silicon Nitride (SSN)
- Manufacturing Process: Silicon nitride powder, with or without additives like yttrium oxide or magnesium oxide, is sintered at high temperatures (around 1750°C) without pressure.
- Properties: Sintered silicon nitride offers superior mechanical properties compared to other types, including high strength, toughness, and wear resistance.
- Applications: High-performance engine components, cutting tools, and structural components.
Here’s a table summarizing the key characteristics of different types of silicon nitride ceramics:
Type | Manufacturing Process | Key Properties | Applications |
---|---|---|---|
Reaction-Bonded Silicon Nitride (RBSN) | Nitrogenation of silicon powder | Porous, low cost, good thermal shock resistance | Refractory materials, low-stress wear components |
Hot-Pressed Silicon Nitride (HPSN) | High-pressure, high-temperature sintering | Dense, high strength, high hardness, high wear resistance | Cutting tools, engine components, high-performance bearings |
Sintered Reaction-Bonded Silicon Nitride (SRBSN) | Sintering of RBSN | Lower porosity than RBSN, improved strength and toughness | Cutting tools, wear components, structural components |
Gas Pressure Sintered Silicon Nitride (GPSN) | High-pressure, high-temperature sintering in nitrogen atmosphere | Very dense, excellent mechanical properties | High-performance engine components, cutting tools, structural components |
Sintered Silicon Nitride (SSN) | High-temperature sintering without pressure | High strength, toughness, and wear resistance | High-performance engine components, cutting tools, structural components |
The choice of SiC ceramic type depends on the specific application requirements, such as temperature, mechanical load, chemical environment, and cost. By understanding the different types of SiC ceramics and their properties, engineers can select the most suitable material for a given application.
What are The Advantages of Nitride Ceramic (Si3N4 ) Ceramics?
Silicon nitride ceramics (Si3N4 ) are a class of advanced materials renowned for their exceptional properties. These properties make them ideal for a wide range of applications across various industries. Here are the key advantages of silicon nitride ceramics:
Mechanical Properties:
- High Strength and Hardness: Si3N4 ceramics exhibit exceptional strength and hardness, making them highly resistant to wear and tear. This property is crucial in applications where components are subjected to high loads and abrasive conditions.
- Excellent Thermal Shock Resistance: They can withstand rapid temperature changes without fracturing, a crucial property for applications involving extreme temperature fluctuations. This makes them ideal for components exposed to thermal shock, such as those in gas turbines and diesel engines.
- High Fracture Toughness: Silicon nitride ceramics have relatively high fracture toughness, which means they can resist crack propagation and failure under stress. This property enhances their reliability and durability.
Thermal Properties:
- Low Thermal Expansion Coefficient: Si3N4 ceramics have a low coefficient of thermal expansion, which means they expand and contract minimally with temperature changes. This property helps to minimize thermal stress and prevent cracking.
- High-Temperature Stability: They can maintain their mechanical properties at elevated temperatures, making them suitable for high-temperature applications.
Chemical Properties:
- Excellent Chemical Resistance: Silicon nitride ceramics are highly resistant to corrosion and chemical attack, making them suitable for use in harsh environments. This property is particularly valuable in applications involving corrosive chemicals or high-temperature oxidation.
Electrical Properties:
- Good Electrical Insulation: They are excellent electrical insulators, making them suitable for applications in electrical and electronic devices.
Other Properties:
- Low Density: Si3N4 ceramics have a relatively low density, making them lightweight and energy-efficient. This property is beneficial in applications where weight reduction is a critical factor, such as in aerospace and automotive industries.
Property | Advantage |
---|---|
Mechanical | High strength and hardness, excellent thermal shock resistance, high fracture toughness |
Thermal | Low thermal expansion coefficient, high-temperature stability |
Chemical | Excellent chemical resistance |
Electrical | Good electrical insulation |
Other | Low density |
Conclusion
Silicon nitride ceramics have emerged as a valuable material in various industries due to their exceptional properties. Their high strength, hardness, thermal shock resistance, and chemical resistance make them ideal for demanding applications where performance and reliability are critical. As technology continues to advance, the demand for high-performance materials like silicon nitride ceramics is expected to grow, driving further innovation and development in this field.
What are The Disadvantages of Nitride Ceramic (Si3N4) Ceramics?
Silicon nitride ceramics, while offering numerous advantages, exhibit some limitations that can restrict their application in certain contexts:
Mechanical Properties:
- Low Fracture Toughness: This makes them susceptible to cracking under stress, reducing their reliability in high-stress environments.
- Medium Mechanical Strength: While strong, their strength is lower compared to other advanced ceramics like alumina and aluminum nitride.
- Brittleness: This inherent brittleness makes them vulnerable to sudden impacts or thermal shock, leading to catastrophic failure.
Thermal Properties:
- Lower Thermal Conductivity: This can hinder heat dissipation, limiting their use in applications requiring efficient heat transfer.
Manufacturing and Cost:
- Difficulties in Machining: Their hardness and brittleness make machining challenging, increasing manufacturing costs and lead times.
- Higher Production Costs: The complex manufacturing processes involved, including high-temperature sintering, can increase the overall cost of silicon nitride components.
Availability:
- Limited Availability: While demand is growing, the availability of high-quality silicon nitride components may still be limited compared to other ceramic materials.
Additional Considerations:
- Density Variations: Variations in density can affect the mechanical and thermal properties of silicon nitride components, leading to inconsistencies in performance.
- Surface Finish Limitations: Achieving precise surface finishes can be challenging, limiting their use in applications requiring smooth surfaces or tight tolerances.
Disadvantages of Silicon Nitride Ceramics
Property | Disadvantage |
---|---|
Mechanical Properties | * Low fracture toughness: Susceptible to cracking under stress. * Medium mechanical strength: Lower strength compared to other advanced ceramics. * Brittleness: Vulnerable to sudden impacts and thermal shock. |
Thermal Properties | * Lower thermal conductivity: Hinders heat dissipation. |
Manufacturing and Cost | * Difficult to machine: Hardness and brittleness make machining challenging. * High production costs: Complex manufacturing processes increase costs. |
Availability | * Limited availability: Supply may not meet demand in certain applications. |
Additional Considerations | * Density variations: Can affect mechanical and thermal properties. * Surface finish limitations: Difficult to achieve precise surface finishes. |
While silicon nitride ceramics offer exceptional properties like high wear resistance, oxidation resistance, and thermal shock resistance, these limitations must be carefully considered when selecting materials for specific applications.
What are The Applications of Nitride Ceramic (Si3N4) Ceramics?
Silicon nitride ceramics (Si3N4) are a class of advanced materials renowned for their exceptional mechanical, thermal, and chemical properties. These properties make them ideal for a wide range of applications across various industries.Given their exceptional properties, silicon nitride ceramics find applications in a multitude of industries and sectors:
1. Automotive Industry
- Engine Components: Pistons, piston rings, valves, and turbocharger rotors.
- Ball Bearings: High-performance, low-friction bearings.
- Exhaust Gas Sensors: Durable and heat-resistant sensors.
- Brake Discs: High-temperature, wear-resistant discs.
- Turbocharger Components: Impellers and turbine wheels.
2. Aerospace Industry
- Turbine Blades: High-temperature, corrosion-resistant blades.
- Heat Exchangers: Efficient heat transfer components.
- Structural Components: Lightweight and strong structural parts.
- Rocket Engine Components: High-temperature, high-stress components.
- Aircraft Engine Components: Durable and reliable components.
3. Electronics Industry
- Semiconductor Manufacturing Equipment: Wear-resistant components.
- Electronic Packaging: Heat sinks and substrates.
- MEMS Devices: Microelectromechanical systems.
- Optical Components: Lenses and mirrors.
4. Industrial Machinery
- Cutting Tools: High-speed, high-temperature cutting tools.
- Bearings: High-precision, low-friction bearings.
- Pumps and Valves: Wear-resistant and corrosion-resistant components.
- Dies and Molds: Durable and high-temperature-resistant molds.
- Gas Turbine Components: High-temperature, high-stress components.
5. Medical Industry
- Dental Implants: Biocompatible and durable implants.
- Orthopedic Implants: Strong and lightweight implants.
- Surgical Instruments: Durable and heat-resistant instruments.
6. Other Applications
- Gas Turbines: High-temperature, high-pressure components.
- Diesel Engines: Wear-resistant components.
- Nuclear Reactors: High-temperature, radiation-resistant components.
- Chemical Processing Equipment: Corrosion-resistant components.
- Metallurgical Industry: High-temperature, wear-resistant components.
- Oil and Gas Industry: High-temperature, high-pressure components.
- Power Generation: High-temperature, high-pressure components.
- Steel Industry: High-temperature, wear-resistant components.
- Ceramic Armor: Bulletproof and stab-proof armor.
- Heat Shields: High-temperature, thermal-shock-resistant shields.
- Gas Turbine Seals: High-temperature, high-pressure seals.
- Fuel Cells: Durable and high-temperature-resistant components.
- Solar Cells: High-temperature, corrosion-resistant components.
- Wear-Resistant Coatings: Protective coatings for metal surfaces.
- High-Temperature Insulation: Thermal insulation for furnaces and kilns.
- High-Voltage Insulators: Electrical insulators for power transmission.
- Sensor Housings: Protective housings for sensors.
- High-Temperature Filters: Filtration of high-temperature gases and liquids.
- Cutting Inserts for Hard Materials: Cutting inserts specifically designed for hard materials like titanium alloys.
- Ceramic Forming Tools: Tools used specifically for forming other ceramics.
- Precision Gears: Gears made from this material offer reduced weight while maintaining strength under load conditions.
- Sensors in Harsh Environments: Sensors deployed in harsh environmental conditions leverage the durability offered by Si₃N₄ against chemical attack or physical abrasion.
- Microelectromechanical Systems (MEMS): MEMS devices utilize thin films or structures made from Si₃N₄ due to their mechanical properties combined with electrical insulation capabilities.
In conclusion, silicon nitride ceramics have a wide range of applications.Silicon nitride ceramics offer a versatile solution for various industries. Their exceptional properties, including high strength, hardness, and thermal shock resistance, make them ideal for demanding applications like automotive, aerospace, electronics, medical, and industrial sectors.
What are the Difficulties in Machining Silicon Nitride (Si3N4) Ceramics?
Machining silicon nitride ceramics presents several challenges due to the material’s unique properties. These difficulties primarily stem from its mechanical characteristics, which are both advantageous for applications but problematic during processing. Here’s a detailed breakdown of the key issues encountered when machining Si₃N₄:
High Hardness and Wear Resistance:
- Tool Wear: The extreme hardness of silicon nitride leads to rapid wear of cutting tools, reducing tool life and increasing machining costs.
- Chip Formation: The brittle nature of the material can result in the formation of sharp, brittle chips that can damage the cutting tool and the workpiece surface.
Brittleness and Fracture Risk:
- Despite its toughness, silicon nitride exhibits brittle behavior under certain conditions. When subjected to machining forces, there is a significant risk of microcracking and spalling. These defects can compromise the integrity of the component being machined, leading to failures in service. The challenge lies in balancing the cutting parameters to minimize these risks while achieving acceptable surface finishes.
Difficulties with Ductile-Brittle Transition:
- The machining process can induce a transition between ductile and brittle behavior in silicon nitride depending on the conditions used (e.g., cutting speed, feed rate). While ductile mode machining can reduce damage by allowing material removal without cracking, achieving this state consistently is difficult due to variations in material properties and environmental factors during processing.
Low Material Removal Rate (MRR):
- Research has shown that while it is possible to grind sintered Si3N4 without inducing surface damage if material is removed entirely under ductile flow, the forces required for such conditions are minimal. This results in impractical material removal rates during conventional grinding processes, making it challenging to achieve efficient production cycles.
Laser-Assisted Machining Challenges:
- Some researchers have explored laser-assisted machining as a solution to improve MRR by inducing thermal gradients that weaken the material before grinding. However, this method disrupts the microstructure of Si₃N₄ significantly, complicating predictions of crack propagation during subsequent grinding operations. The irregular morphology created by laser ablation makes it difficult to maintain control over the quality of the finished part.
Tooling Limitations:
- The tools used for machining silicon nitride must be made from materials that can withstand extreme hardness and thermal conditions without degrading quickly. Diamond tools are often employed due to their superior hardness; however, they are expensive and require precise handling techniques to avoid damage during use.
In summary, while silicon nitride ceramics offer numerous advantages for high-performance applications due to their mechanical properties, these same characteristics create significant challenges during machining processes that must be carefully managed through advanced techniques and tooling strategies.
What is the Difference of Silicon Nitride Ceramics and Silicon Carbide Ceramics?
Silicon carbide (SiC) and silicon nitride (Si₃N₄) are two high-performance ceramic materials renowned for their exceptional properties. While both offer significant advantages, they differ in various aspects. Here’s a detailed comparison:
Mechanical Properties
Strength:
- SiC: Exhibits excellent high-temperature strength, maintaining its structural integrity up to 1600°C.
- Si3N4: Offers high strength and impact resistance at lower temperatures, but its strength decreases above 1200°C.
- SiC: Exhibits excellent high-temperature strength, maintaining its structural integrity up to 1600°C.
Toughness:
- Si3N4: Generally possesses superior toughness, making it more resistant to crack propagation and fracture.
- SiC: While strong, it is more brittle and prone to catastrophic failure.
Thermal Properties
Thermal Shock Resistance:
- Si3N4: Exhibits excellent thermal shock resistance due to its low thermal expansion coefficient.
- SiC: Has a higher thermal expansion coefficient, making it more susceptible to thermal shock.
Thermal Conductivity:
- SiC: Offers significantly higher thermal conductivity, making it ideal for heat dissipation applications.
- Si3N4: Has good thermal conductivity, but lower than SiC.
Chemical Properties
- Corrosion Resistance:
- Both materials exhibit excellent corrosion resistance to most acids and alkalis.
- Si3N4: Slightly more resistant to oxidation than SiC.
Wear Resistance
- SiC: Renowned for its exceptional hardness and wear resistance, making it ideal for applications requiring high durability.
- Si3N4: Offers good wear resistance, but not as high as SiC.
Production Process and Cost
SiC: Typically produced through processes like hot pressing, pressureless sintering, and reaction sintering.
Si3N4: Commonly produced through reaction sintering, hot pressing, and gas pressure sintering.
Cost:
- SiC: Generally less expensive to produce.
- Si3N4: More complex manufacturing processes can make it more costly.
Key Considerations for Application Selection
- High-temperature applications: SiC’s superior high-temperature strength makes it ideal for environments with extreme heat.
- Thermal shock resistance: Si₃N₄’s excellent thermal shock resistance is beneficial for applications involving rapid temperature changes.
- Toughness and impact resistance: Si₃N₄’s superior toughness makes it suitable for applications where impact resistance is critical.
- Wear resistance: SiC’s exceptional hardness and wear resistance make it ideal for applications requiring high durability.
- Cost: SiC is generally less expensive to produce, making it a more cost-effective option for certain applications.
Comparison of Silicon Carbide (SiC) and Silicon Nitride (Si₃N₄)
Property | Silicon Carbide (SiC) | Silicon Nitride (Si₃N₄) |
---|---|---|
Mechanical Properties | ||
Strength | Excellent high-temperature strength | High strength and impact resistance at lower temperatures |
Toughness | Brittle | Superior toughness |
Thermal Properties | ||
Thermal Shock Resistance | Susceptible to thermal shock | Excellent thermal shock resistance |
Thermal Conductivity | High thermal conductivity | Good thermal conductivity |
Chemical Properties | ||
Chemical Formula | SiC | Si₃N₄ |
Bond Type | Covalent | Covalent |
Natural Occurrence | Rare | Rare |
Chemical Stability | High | Good |
Oxidation Resistance | Excellent | Slightly lower than SiC |
Acid Resistance | Resistant to many acids | Resistant to most inorganic acids |
Alkali Resistance | Resistant to many alkalis | Resistant to caustic soda solutions below 30% |
Wear Resistance | ||
Wear Resistance | Exceptional | Good |
Production and Cost | ||
Production Processes | Hot pressing, pressureless sintering, reaction sintering | Reaction sintering, hot pressing, gas pressure sintering |
Cost | Lower cost | Higher cost |
In conclusion, both SiC and Si₃N₄ are valuable materials with unique properties. The optimal choice depends on the specific requirements of the application. By carefully considering their strengths and weaknesses, engineers can select the most suitable material for a given task.
What is the Production Process of Silicon Nitride (Si₃N₄)?
Here’s a detailed breakdown of the primary methods used to produce silicon nitride:
1. High-Temperature Nitridation of Silicon
- Chemical Reaction:
3Si + 2N₂ → Si₃N₄
- Process:
- High-purity silicon powder is heated to temperatures between 1300°C and 1400°C in a nitrogen atmosphere.
- Nitrogen gas reacts with the silicon, forming silicon nitride.
- Advantages:
- Relatively simple process.
- Produces high-purity silicon nitride.
- Disadvantages:
- Energy-intensive due to high temperatures.
2. Diimide Route
- Chemical Reactions:
SiCl₄ + 6NH₃ → Si(NH)₂ + 4NH₄Cl
3Si(NH)₂ → Si₃N₄ + N₂ + 3H₂
- Process:
- Silicon tetrachloride reacts with ammonia at low temperatures to form diimide.
- The diimide is then heated to high temperatures to form silicon nitride.
- Advantages:
- Better control over the reaction conditions.
- Produces high-purity silicon nitride.
- Disadvantages:
- Complex process involving multiple steps.
- Requires careful handling of reactive chemicals.
3. Carbothermal Reduction
- Chemical Reaction:
3SiO2 + 6C + 2N2 → Si3N4 + 6CO
- Process:
- Silicon dioxide, carbon, and nitrogen are mixed and heated to temperatures between 1400°C and 1450°C.
- The carbon reduces the silicon dioxide, and the nitrogen reacts with the silicon to form silicon nitride.
- Advantages:
- Cost-effective process.
- Can use low-cost starting materials.
- Disadvantages:
- Complex reaction involving multiple phases.
- Potential for impurities in the final product.
4. Chemical Vapor Deposition (CVD)
- Chemical Reaction (using silane):
3SiH4 + 4NH3 → Si3N4 + 12H2
- Process:
- Gaseous precursors like silane or silicon tetrachloride are reacted with ammonia at elevated temperatures.
- Silicon nitride is deposited on a substrate in the form of a thin film.
- Advantages:
- Precise control over film thickness, composition, and microstructure.
- Versatile for depositing silicon nitride on various substrates.
- Disadvantages:
- Complex equipment and processes.
- High cost.
Production Processes for Silicon Nitride (Si3N4)
Process | Chemical Reaction | Advantages | Disadvantages |
---|---|---|---|
High-Temperature Nitridation | 3Si + 2N₂ → Si₃N₄ | Simple process, high-purity product | Energy-intensive |
Diimide Route | SiCl4 + 6NH3 → Si(NH)2 + 4NH4Cl 3Si(NH)2 → Si₃N₄ + N₂ + 3H₂ | Better control, high-purity product | Complex process, requires careful handling of chemicals |
Carbothermal Reduction | 3SiO2 + 6C + 2N2 → Si3N4 + 6CO | Cost-effective, can use low-cost materials | Complex reaction, potential for impurities |
Chemical Vapor Deposition (CVD) | 3SiH4 + 4NH3 → Si3N4 + 12H2 | Precise control, versatile | Complex equipment, high cost |
Conclusion
Silicon nitride (Si3N4) is a versatile ceramic material with exceptional properties, making it suitable for a wide range of applications in various industries. The production of silicon nitride involves several methods, each with its own advantages and disadvantages.
High-temperature nitridation is a straightforward method that produces high-purity silicon nitride but requires high temperatures and energy. The diimide route offers better control over the reaction conditions but involves complex steps and requires careful handling of chemicals. Carbothermal reduction is a cost-effective method but can introduce impurities into the final product. Chemical vapor deposition (CVD) is a versatile technique for producing high-quality silicon nitride films but requires complex equipment and processes.
The choice of production method depends on factors such as the desired purity, product form, cost considerations, and environmental impact. By carefully considering these factors, manufacturers can select the most appropriate method to produce silicon nitride that meets specific application requirements.
How is Silicon Nitride (Si3N4) Ceramic Manufactured?
Silicon nitride (Si3N4) ceramics are renowned for their exceptional properties, including high strength, excellent thermal shock resistance, and exceptional wear resistance. These characteristics make them ideal for demanding applications in various industries, such as aerospace, automotive, and industrial machinery.
The production of silicon nitride ceramics involves a multi-step process that requires careful control of various parameters to achieve the desired properties. Here’s a detailed breakdown of the process:
1. Raw Material Preparation
- Silicon Powder: High-purity silicon powder is the primary raw material. It is typically obtained through the reduction of silica (SiO2) with carbon.
- Nitrogen Gas: High-purity nitrogen gas is used as the nitrogen source for the nitridation process.
- Additives (Optional): Additives such as yttrium oxide (Y2O3), magnesium oxide (MgO), or aluminum oxide (Al2O3) may be added to enhance specific properties like densification, strength, or toughness.
2. Synthesis of Silicon Nitride Powder
The synthesis of silicon nitride powder is typically carried out through one of the following methods:
- Direct Nitridation: Silicon powder is heated in a nitrogen atmosphere at high temperatures (around 1400°C) to directly form silicon nitride. The reaction can be represented as:
3Si + 2N2 → Si3N4
- Carbothermal Reduction and Nitridation (CRN): A mixture of silica, carbon, and nitrogen is heated to high temperatures (around 1400°C). Carbon reduces silica to silicon, which then reacts with nitrogen to form silicon nitride. The reaction can be represented as:
3SiO2 + 6C + 2N2 → Si3N4 + 6CO
3. Powder Processing
The synthesized silicon nitride powder is processed to obtain a homogeneous powder with the desired particle size distribution. This may involve milling, sieving, and mixing with additives.
4. Shaping
The processed powder is shaped into the desired form using various techniques:
- Pressing: The powder is compacted under high pressure to form the desired shape.
- Injection Molding: The powder is mixed with a binder and injected into a mold to form complex shapes.
- Slip Casting: The powder is dispersed in a liquid suspension and cast into a mold.
5. Sintering
Sintering is a critical step in the production process, where the shaped green body is heated to high temperatures to densify and strengthen the material. The sintering process can be classified into several types:
- Pressureless Sintering: The green body is heated without external pressure to high temperatures (around 1750°C) to densify.
- Hot Pressing: The green body is heated under high pressure (around 40 MPa) to high temperatures (around 1800°C) to achieve high density and fine microstructure.
- Gas Pressure Sintering: The green body is sintered under high nitrogen pressure (1-10 MPa) and high temperatures (around 2000°C) to achieve very high density and excellent mechanical properties.
- Reaction Bonded Silicon Nitride (RBSN): A mixture of silicon powder and a nitride-forming agent (e.g., silicon nitride powder) is compacted and heated to temperatures around 1450°C. Silicon reacts with the nitride-forming agent to form silicon nitride, resulting in a porous structure with good mechanical properties.
6. Machining and Finishing
After sintering, the ceramic components may undergo machining and finishing operations to achieve the desired final shape and surface finish. Techniques such as grinding, polishing, and diamond cutting can be used.
7. Quality Control and Testing
The final products are subjected to rigorous quality control testing to ensure they meet the required specifications. This may include testing for mechanical properties (strength, toughness, hardness), thermal properties (thermal shock resistance, thermal conductivity), and chemical resistance.
Production Process of Silicon Nitride Ceramic
Step | Description |
1. Raw Material Preparation | |
* Silicon Powder | High-purity silicon powder, obtained from silica reduction. |
* Nitrogen Gas | High-purity nitrogen gas for nitridation. |
* Additives (Optional) | Yttrium oxide, magnesium oxide, or aluminum oxide to enhance properties. |
2. Synthesis of Silicon Nitride Powder | |
* Direct Nitridation | Silicon powder is heated in nitrogen to form Si3N4. |
* Carbothermal Reduction and Nitridation (CRN) | Silica, carbon, and nitrogen react to form Si3N4. |
3. Powder Processing | * Milling, sieving, and mixing for homogeneous powder. |
4. Shaping | |
* Pressing | Compacting powder under high pressure. |
* Injection Molding | Mixing powder with a binder and injecting into a mold. |
* Slip Casting | Dispersing powder in a liquid suspension and casting into a mold. |
5. Sintering | |
* Pressureless Sintering | Heating without external pressure to densify. |
* Hot Pressing | Heating under high pressure to achieve high density. |
* Gas Pressure Sintering | Sintering under high nitrogen pressure for very high density. |
* Reaction Bonded Silicon Nitride (RBSN) | Silicon reacts with a nitride-forming agent to form a porous structure. |
6. Machining and Finishing | * Grinding, polishing, and diamond cutting to achieve desired shape and surface finish. |
7. Quality Control and Testing | * Testing for mechanical, thermal, and chemical properties to ensure quality. |
Note :The Role of Additives and Sintering Mechanisms
Additives: A Key Ingredient
Additives play a pivotal role in the sintering process of silicon nitride ceramics. These substances, such as yttrium oxide (Y2O3) and magnesium oxide (MgO), can significantly influence the final properties of the ceramic. Here’s how:
- Lowering Sintering Temperature: By forming low-melting-point liquid phases at relatively low temperatures, additives can reduce the energy required for densification. This can lead to faster sintering times and lower energy consumption.
- Enhancing Mechanical Properties: Additives can improve the strength, toughness, and fracture resistance of silicon nitride ceramics. They can act as grain growth inhibitors, reducing the size of grains and increasing the number of grain boundaries, which can enhance toughness.
- Controlling Microstructure: Additives can influence the microstructure of the ceramic, including grain size, porosity, and phase composition. By controlling the type and amount of additives, it is possible to tailor the microstructure to achieve specific properties.
Sintering Mechanisms: The Driving Force
The sintering process involves several mechanisms that contribute to densification and microstructure development. Understanding these mechanisms is crucial for optimizing the sintering process:
- Solid-State Sintering: This mechanism involves the diffusion of atoms through solid-state diffusion. It is typically dominant at lower temperatures and can lead to slower densification rates.
- Liquid-Phase Sintering: In this mechanism, a liquid phase forms at the grain boundaries, which can accelerate mass transport and densification. Liquid-phase sintering is often used to achieve high-density ceramics at lower temperatures.
Post-Sintering Treatments: Fine-Tuning the Properties
Post-sintering treatments can further enhance the properties of silicon nitride ceramics. Some common post-sintering treatments include:
- Heat Treatment: Heat treatment can improve the microstructure and mechanical properties of the ceramic. It can also be used to relieve residual stresses and enhance the stability of the material.
- Chemical Vapor Deposition (CVD): CVD can be used to deposit thin films on the surface of the ceramic to improve its surface properties, such as wear resistance, corrosion resistance, and oxidation resistance.
- Physical Vapor Deposition (PVD): PVD can be used to deposit coatings on the surface of the ceramic to improve its surface properties, such as hardness, toughness, and electrical conductivity.
By carefully controlling the raw materials, additives, sintering process, and post-sintering treatments, it is possible to produce high-quality silicon nitride ceramics with tailored properties for a wide range of applications.
How do Silicon Nitride Ceramics Compare to Common Metal Materials?
Silicon nitride ceramics offer unique properties that distinguish them from common metal materials. Let’s delve deeper into the key differences:
Mechanical Properties
Hardness:
- Silicon Nitride: Exceptionally hard, second only to diamond and cubic boron nitride. Vickers hardness: 1400-2200 HV.
- Common Metals: Significantly lower hardness. High-speed steel: 600-900 HV. Cemented carbide: 800-1000 HV.
- Implication: Superior wear and scratch resistance, ideal for bearings, tools, and other high-wear applications.
Bending Strength:
- Silicon Nitride: High bending strength of 700-1000 MPa, excellent resistance to bending stress.
- Common Metals: Varies depending on the material, but generally lower than silicon nitride. Some alloy steels may have comparable or higher strength after special treatment.
Toughness:
- Common Metals: Typically exhibit good toughness, allowing for deformation without breaking.
- Silicon Nitride: While tougher than most ceramics, it is still less tough than metals and can fracture under impact loads.
Physical Properties
Density:
- Silicon Nitride: Relatively low density of 3.2 g/cm³, advantageous for weight-sensitive applications like aerospace.
- Common Metals: Higher density. Iron: 7.86 g/cm³. Copper: 8.96 g/cm³. Aluminum: 2.7 g/cm³.
Thermal Expansion Coefficient:
- Silicon Nitride: Low thermal expansion coefficient, minimal dimensional change with temperature fluctuations.
- Common Metals: Higher thermal expansion coefficients, prone to expansion and deformation at high temperatures.
Thermal Conductivity:
- Common Metals: Generally good thermal conductors (e.g., copper, aluminum).
- Silicon Nitride: Lower thermal conductivity, but can be improved with additives or special processing.
Chemical Properties
Corrosion Resistance:
- Silicon Nitride: Excellent chemical stability, resistant to acids, alkalis, and salts.
- Common Metals: Prone to corrosion, especially in acidic or alkaline environments. Require protective coatings or treatments.
Oxidation Resistance:
- Silicon Nitride: High oxidation resistance at high temperatures, maintains stability in oxygen-rich environments.
- Common Metals: Oxidize readily at high temperatures, leading to performance degradation.
Processing and Cost
Processing Difficulty:
- Silicon Nitride: High hardness makes processing challenging, requiring specialized tools and techniques.
- Common Metals: Relatively easy to process using conventional methods like casting, forging, and machining.
Cost:
- Silicon Nitride: Complex production process, high-cost raw materials, and difficult processing result in higher costs.
- Common Metals: Simpler production, lower raw material costs, and easier processing lead to lower costs.
Silicon Nitride Ceramics vs. Common Metal Materials
Property | Silicon Nitride Ceramics | Common Metal Materials |
---|---|---|
Mechanical Properties | ||
Hardness | Very high, second only to diamond and cubic boron nitride | Significantly lower |
Bending Strength | High, 700-1000 MPa | Varies, but generally lower |
Toughness | Lower than metals, but higher than most ceramics | Typically good |
Physical Properties | ||
Density | Low, 3.2 g/cm³ | Higher, e.g., iron: 7.86 g/cm³, copper: 8.96 g/cm³ |
Thermal Expansion Coefficient | Low | Higher |
Thermal Conductivity | Lower | Generally good, especially copper and aluminum |
Chemical Properties | ||
Corrosion Resistance | Excellent, resistant to acids, alkalis, and salts | Prone to corrosion, especially in harsh environments |
Oxidation Resistance | High, stable at high temperatures | Oxidize readily at high temperatures |
Processing and Cost | ||
Processing Difficulty | High, requires specialized tools and techniques | Relatively easy, conventional methods |
Cost | High, complex production and high-cost raw materials | Lower, simpler production and lower-cost materials |
In conclusion, while silicon nitride ceramics offer superior properties in terms of hardness, wear resistance, and thermal stability, they also present challenges in terms of toughness, thermal conductivity, and processing complexity. The choice between silicon nitride and metal materials depends on the specific requirements of the application.
What is the Challenges in Manufacturing Silicon Nitride Ceramics ?
The production of silicon nitride ceramics, while offering numerous advantages, presents several significant challenges that manufacturers must overcome to achieve high-quality, cost-effective products.
1. Raw Material Quality and Consistency
- Purity and Particle Size:
- Silicon powder purity should be at least 99.9% to minimize impurities that can degrade the final product’s properties.
- Particle size distribution should be tightly controlled within a specific range (e.g., 1-10 µm) to ensure uniform densification and microstructure.
- Additives:
- The amount and type of additives (e.g., Y2O3, MgO) must be precisely controlled to optimize sintering behavior and final properties.
- Inconsistent additive distribution can lead to variations in microstructure and mechanical properties.
2. Processing Techniques
- Powder Metallurgy:
- Mixing: Ball milling or high-energy milling is often used to achieve homogeneous mixing of powders and additives. However, excessive milling can lead to particle size reduction and increased surface area, which can affect sintering behavior.
- Green Body Formation: Pressing techniques, such as cold isostatic pressing (CIP) or hot pressing, can be used to form green bodies with desired density and microstructure. However, these techniques require precise control of pressure and temperature to avoid defects.
- Hot Pressing:
- Temperature and Pressure Profiles: Temperature should be carefully controlled to prevent excessive grain growth and phase transformations. Pressure should be sufficient to achieve desired density without causing cracking or deformation.
- Die Wear: Diamond or tungsten carbide dies are often used, but they can still experience significant wear, especially at high temperatures and pressures.
- Sintering:
- Temperature Gradients: Temperature gradients within the furnace should be minimized to prevent thermal stresses and non-uniform densification.
- Atmosphere Control: Precise control of nitrogen and oxygen partial pressures is crucial to avoid oxidation and maintain a reducing atmosphere.
3. High Processing Temperatures
- Energy Consumption: High-temperature sintering processes can consume significant amounts of energy, increasing production costs and environmental impact.
- Equipment Limitations: Specialized furnaces capable of reaching and maintaining high temperatures are expensive and require frequent maintenance.
- Thermal Stresses: Rapid temperature changes can induce thermal shock, leading to cracking and deformation, especially in complex shapes.
4. Tool Wear and Equipment Durability
- Diamond Tooling: Diamond tools are often used for machining and grinding silicon nitride ceramics due to their exceptional hardness. However, diamond tools can be expensive and prone to wear, especially when machining complex shapes or hard materials.
- Equipment Maintenance: Frequent maintenance and calibration of equipment, such as furnaces, presses, and machining tools, are necessary to ensure consistent product quality and minimize downtime.
5. Scale-Up Challenges
- Uniformity and Reproducibility: Scaling up production can introduce variations in material properties and product quality due to factors such as heat transfer, mass transport, and stress distribution.
- Process Control: Maintaining precise control over process parameters becomes more challenging at larger scales, requiring advanced monitoring and control systems.
6. Environmental Considerations
- Waste Generation: The production process can generate hazardous waste, such as spent tooling, chemical residues, and dust.
- Energy Consumption and Emissions: High-temperature processes contribute to greenhouse gas emissions and energy consumption.
7. Market Competition and Cost Pressures
- Price Competition: Intense competition can drive down prices, forcing manufacturers to optimize production processes and reduce costs.
- Product Differentiation: To remain competitive, manufacturers must develop innovative products with superior performance and unique features.
Challenge | Description |
Raw Material Quality and Consistency | |
Purity and Particle Size | Requires high-purity silicon and nitrogen powders with controlled particle size distribution. |
Additives | Precise control over the type, amount, and distribution of additives is essential. |
Processing Techniques | |
Powder Metallurgy | Homogeneous mixing and green body formation are critical. |
Hot Pressing | Precise control of temperature and pressure to avoid defects. |
Sintering | Careful control of temperature gradients and atmosphere to ensure uniform densification. |
High Processing Temperatures | |
Energy Consumption | High-temperature processes are energy-intensive. |
Equipment Limitations | Specialized furnaces are required, which can be expensive and complex. |
Thermal Stresses | Rapid temperature changes can induce thermal shock. |
Tool Wear and Equipment Durability | |
Diamond Tooling | Expensive and prone to wear, especially for complex shapes. |
Equipment Maintenance | Frequent maintenance is necessary to ensure consistent product quality. |
Scale-Up Challenges | |
Uniformity and Reproducibility | Maintaining consistency at larger scales can be challenging. |
Process Control | Precise control over process parameters becomes more difficult at larger scales. |
Environmental Considerations | |
Waste Generation | The production process can generate hazardous waste. |
By addressing these challenges through careful process design, advanced materials engineering, and innovative manufacturing techniques, the production of high-quality silicon nitride ceramics can be optimized, leading to improved performance and reduced costs.
What is the Differences Between Silicon Nitride Ceramics and Zirconia Ceramics?
Silicon nitride (Si3N4) and zirconia (ZrO2) are two high-performance engineering ceramics, each with distinct properties and applications.
1. Thermal Expansion Coefficient
- Silicon Nitride: Low coefficient of thermal expansion, making it suitable for applications requiring dimensional stability under varying temperatures.
- Zirconia: Higher coefficient of thermal expansion, which can lead to thermal stresses and potential cracking if not managed properly.
2. Mechanical Properties
- Strength and Toughness:
- Silicon Nitride: High strength and toughness, making it ideal for high-stress applications.
- Zirconia: High toughness due to phase transformations that absorb energy during crack propagation, but lower strength compared to Si₃N₄.
- Fracture Toughness:
- Silicon Nitride: Lower fracture toughness, making it more susceptible to brittle failure.
- Zirconia: Higher fracture toughness, making it more resistant to crack propagation.
3. Chemical Resistance
- Silicon Nitride: Excellent resistance to acidic environments.
- Zirconia: Good resistance to alkaline environments.
4. Applications
- Silicon Nitride:
- Aerospace: Engine components, turbine blades, and heat shields
- Automotive: Engine components, turbochargers, and brake discs
- Electronics: Semiconductors and substrates
- Zirconia:
- Dental Implants: Crowns, bridges, and implants
- Cutting Tools: High-performance cutting tools
- Thermal Barrier Coatings: Protecting components from high-temperature environments
- Sensors and Actuators: Electronic components
Silicon Nitride Ceramics vs. Zirconia Ceramics
Property | Silicon Nitride (Si3N4) | Zirconia (ZrO2) |
---|---|---|
Thermal Expansion Coefficient | Low (around 3.0 x 10^-6/K) | Higher (around 10.5 x 10^-6/K) |
Mechanical Strength | High strength and toughness | Moderate strength, good ductility |
Brittleness | More brittle, prone to cracking under impact | Less brittle, more resistant to fracture |
Corrosion Resistance | Excellent in acidic environments | Excellent in alkaline environments |
Applications | Aerospace components, high-precision bearings | Cutting tools, dental applications, marine uses |
Conclusion
The choice between silicon nitride and zirconia depends on the specific application requirements. While silicon nitride offers superior mechanical properties and thermal shock resistance, zirconia’s toughness and biocompatibility make it suitable for a wide range of applications, including biomedical and dental.
How to Judge the Quality of Silicon Nitride Ceramics?
Silicon nitride ceramics are renowned for their exceptional mechanical, thermal, and chemical properties. To ensure the quality of these ceramics, several factors must be considered:
1. Visual Inspection:
- Surface Finish: The surface should be smooth, free of defects like cracks, pits, or bubbles.
- Color Uniformity: A consistent color indicates uniform material composition and processing.
- Edge and Corner Quality: Clean, sharp edges and corners suggest precise manufacturing.
2. Mechanical Properties:
- Hardness: High hardness is essential for wear resistance. Vickers or Knoop hardness tests can quantify this property.
- Strength: Both flexural and compressive strength are crucial. Higher values indicate superior strength.
- Toughness: This measures the material’s resistance to crack propagation. It can be assessed through impact tests or fracture toughness measurements.
3. Thermal Properties:
- Thermal Shock Resistance: The ability to withstand rapid temperature changes without fracturing.
- Thermal Conductivity: The material’s ability to conduct heat.
4. Chemical Properties:
- Corrosion Resistance: The ability to resist degradation when exposed to chemicals.
- Oxidation Resistance: The ability to withstand high-temperature oxidation.
5. Microstructural Analysis:
- Grain Size and Distribution: Smaller, uniformly distributed grains often lead to better mechanical properties.
- Porosity: Lower porosity correlates with higher strength and density.
6. Manufacturing Process:
- Sintering Process: The sintering technique used can significantly impact the final properties.
- Processing Accuracy: Precise machining and finishing are essential for complex shapes and tight tolerances.
Additional Considerations:
- Certification and Standards: Adherence to industry standards and certifications (e.g., ISO 9001) ensures quality control.
- Manufacturer’s Reputation: A reputable manufacturer with a proven track record is more likely to produce high-quality products.
- Specific Application Requirements: Different applications may have specific requirements, such as thermal conductivity for heat sinks or corrosion resistance for chemical environments.
By carefully evaluating these factors, you can select high-quality silicon nitride ceramics that meet the demands of your specific application.
What is Testing Standards for Hardness and Strength of Silicon Nitride Ceramics ?
Silicon nitride (Si3N4) ceramics are renowned for their exceptional mechanical properties, including high hardness, strength, and thermal stability. These characteristics make them ideal for demanding applications such as cutting tools, bearings, and structural components in high-temperature environments. To ensure the reliability and performance of silicon nitride ceramics in these applications, specific testing standards have been established to evaluate their hardness and strength.
Hardness Testing Standards
- Vickers Hardness Test (ASTM E92): This standard method involves applying a diamond pyramid indenter under a specific load onto the material’s surface. The size of the resulting indentation is measured to calculate the Vickers hardness number (HV), providing a quantitative measure of the material’s resistance to indentation.
- Knoop Hardness Test (ASTM E384): Similar to the Vickers test, the Knoop test uses a diamond indenter but with a specific elongated shape to produce a longer, narrower indentation. This method is particularly useful for brittle materials like ceramics, as it minimizes the risk of cracking.
- Mohs Hardness Scale: While not a standardized testing method, the Mohs scale provides a qualitative measure of hardness based on scratch resistance. Silicon nitride typically ranks around 8-9 on this scale, indicating its high resistance to scratching.
Strength Testing Standards
- Flexural Strength Test (ASTM C1161): This standard outlines procedures for determining the flexural strength of ceramic materials through a three-point or four-point bending test. The material is subjected to increasing load until fracture, and the flexural strength is calculated based on the maximum load and sample dimensions.
- Compressive Strength Test (ASTM C773): This standard specifies methods for measuring compressive strength by applying axial loads to cylindrical or rectangular specimens until failure. Compressive strength is crucial for applications where silicon nitride components will experience significant compressive forces.
- Fracture Toughness Testing (ASTM C1421): Fracture toughness is a critical property for assessing a material’s resistance to crack propagation. This standard describes methods such as single-edge notched beam tests or compact tension tests to determine fracture toughness values (KIC) for silicon nitride ceramics.
- Dynamic Mechanical Analysis (DMA): While not explicitly included in traditional standards, DMA can provide valuable insights into the mechanical behavior of silicon nitride under varying temperatures and frequencies, aiding in understanding its performance in real-world conditions.
By adhering to these standardized testing methods, manufacturers and researchers can reliably evaluate the hardness and strength of silicon nitride ceramics, ensuring their suitability for a wide range of demanding applications.
Can Yomua Meet the Special Requirements of Silicon Nitride Ceramic Surface?
Yes,Yomua is a leading manufacturer of advanced ceramic components, can certainly meet the special requirements of silicon nitride ceramic surfaces. They offer a range of products and services that can help achieve the desired surface quality.
Key Surface Quality Parameters for the customers:
- Surface Roughness: A smooth surface minimizes friction and wear, particularly crucial in applications like bearings and seals.
- Defect-Free Surfaces: The absence of cracks, pores, or inclusions is essential to prevent premature failure under stress.
- Dimensional Tolerance: Precise control over dimensions ensures accurate fit and function within assemblies.
Manufacturing Techniques for Superior Surface Quality
- Sintering Process Optimization: Careful control of sintering parameters, such as temperature and time, minimizes grain growth and porosity. The addition of sintering aids can enhance densification and reduce defects.
- Advanced Finishing Techniques:
Polishing:
- Mechanical Polishing: Uses abrasive materials to physically remove material from the surface.
- Precision Machining: Advanced machining techniques like diamond grinding and polishing can achieve very fine surface finishes.
- Chemical-Mechanical Polishing (CMP): Combines mechanical action with chemical etching to achieve a high-quality finish.
- Laser Surface Treatment: Lasers can be used to smooth surfaces, remove defects, or create specific surface textures.
Grinding:
- Removes material using abrasive wheels or belts to shape the component and achieve precise tolerances.
Coating Technologies:
- Thin Film Coatings:
- Diamond-like Carbon (DLC): Extremely hard and wear-resistant coating, often used in high-stress applications.
- Ceramic Coatings: Improve hardness, wear resistance, and corrosion resistance.
- Polymer Coatings:
- Reduce friction and wear, protect the surface from damage, and enhance lubrication.
Post-Processing Techniques
- Heat Treatment: Heat treatment can modify the surface properties of silicon nitride, such as hardness and residual stress.
- Surface Modification: Techniques like ion implantation and plasma treatment can alter the surface chemistry and microstructure.
Characterization Techniques for Surface Quality Assessment
- Atomic Force Microscopy (AFM): Provides high-resolution topographical images to measure surface roughness at the nanoscale.
- Scanning Electron Microscopy (SEM): Enables detailed inspection of surface morphology, including defects and microstructure.
- X-ray Diffraction (XRD): Analyzes the crystal structure and phase composition, which can influence surface properties.
Key Considerations
- Desired Surface Finish: The specific requirements for surface roughness, waviness, and other parameters will determine the appropriate manufacturing and finishing techniques.
- Component Geometry: Complex shapes may require specialized machining or finishing processes.
- Cost: The cost of achieving a specific surface finish will vary depending on the complexity of the process and the desired level of precision.
Collaboration with Customers
Yomua works closely with customers to understand their specific needs and develop tailored solutions to meet their requirements. We can provide guidance on suitable manufacturing processes, finishing techniques, and surface treatments to meet application needs.
By leveraging our expertise, advanced manufacturing capabilities, and quality control processes, Yomua can help you achieve the desired surface quality for your silicon nitride ceramic components.
What are the Typical Tolerance of Silicon Nitride Ceramics?
Silicon nitride (Si3N4) ceramics, renowned for their exceptional mechanical, thermal, and chemical properties, are widely used in various industries. When manufacturing custom Si3N4 components, achieving precise tolerances is paramount to ensure optimal performance. This article delves into the key tolerance considerations for Si3N4 ceramics.
Dimensional Tolerances
- General Tolerance Range: ±0.1 mm to ±0.5 mm, depending on the component size and complexity.
- Smaller components (e.g., <10 mm) can achieve tighter tolerances: ±0.05 mm.
- Larger components may have looser tolerances due to processing challenges.
Geometric Tolerances
- Flatness: Typically within 0.05 mm over 100 mm.
- Roundness: Often within 0.02 mm for critical circular features.
- Parallelism: Generally within 0.1 mm over 100 mm.
Surface Finish
- Ra (Average Roughness):
- Precision applications: 0.2-0.4 µm after grinding.
- Low-friction applications (e.g., bearings): 0.1 µm.
Feature | Tolerance Range |
---|---|
Dimensional Tolerance | ±0.1 mm to ±0.5 mm |
Geometric Tolerances | |
* Flatness | Within 0.05 mm over 100 mm |
* Roundness | Within 0.02 mm for critical circular features |
* Parallelism | Within 0.1 mm over 100 mm |
Surface Finish (Ra) | 0.2-0.4 µm for precision applications, 0.1 µm for low-friction applications |
Note: These are general guidelines, and actual tolerances may vary based on specific application requirements, manufacturing process, and material properties.
Factors Influencing Tolerances
- Manufacturing Process:
- Hot pressing and reaction bonding often yield tighter tolerances than traditional sintering.
- Design Complexity:
- Complex geometries require stricter tolerance control due to processing challenges.
- Application-Specific Requirements:
- Load-bearing capacity, thermal expansion, and other performance factors influence tolerance needs.
- Quality Control Standards:
- Adherence to industry standards (ISO, ASTM) dictates specific tolerance requirements.
Achieving Tight Tolerances
To achieve stringent tolerances in Si3N4 ceramics, manufacturers employ various techniques:
- Precise Mold Design and Manufacturing: Ensures accurate component geometry.
- Optimized Sintering Processes: Minimizes dimensional changes and warpage.
- Advanced Machining Techniques: Enables precise shaping and finishing.
- Rigorous Quality Control: Implements stringent inspection and testing procedures.
By understanding these factors and employing advanced manufacturing techniques, it is possible to produce custom Si3N4 ceramic components that meet exacting tolerance requirements, ensuring their reliability and performance in demanding applications.
What is the Service Life of Silicon Nitride Ceramics in Acidic and Alkaline Environments?
Silicon nitride (Si3N4) ceramics are renowned for their exceptional mechanical, thermal, and chemical properties, making them suitable for various applications, including those involving exposure to acidic and alkaline environments. However, the specific service life of these ceramics in such environments can vary significantly based on several factors.
Factors Influencing Service Life:
- Acid or Alkali Concentration: Higher concentrations generally accelerate degradation.
- Temperature: Elevated temperatures can exacerbate chemical reactions.
- Specific Chemical: Different acids and alkalis have varying degrees of reactivity with Si3N4.
- Mechanical Stress: Stress can amplify the effects of chemical attack.
- Material Quality and Manufacturing Process: The quality and manufacturing process influence the ceramic’s resistance to corrosion.
General Service Life Trends:
- Acidic Environments:
- Si3N4 exhibits good stability in dilute acids, often lasting for several years.
- In concentrated acids or at elevated temperatures, the service life may decrease to months or even weeks.
- Alkaline Environments:
- Si3N4 is less stable in alkaline environments due to hydrolysis reactions.
- Strong alkaline solutions can lead to significant degradation within months.
- Milder alkaline conditions may allow for longer service life, but still shorter than in acidic environments.
Practical Considerations:
- Protective Coatings: Applying protective coatings can enhance corrosion resistance.
- Regular Inspection and Maintenance: Monitoring the component’s condition and performing regular maintenance can extend its service life.
- Consulting Experts: Consulting with materials engineers or manufacturers can provide tailored advice for specific applications and environments.
Conclusion:
While silicon nitride ceramics offer excellent corrosion resistance, their service life in acidic and alkaline environments depends on various factors. It’s crucial to carefully consider the specific conditions of the application to ensure optimal performance and longevity. By understanding these factors and taking appropriate measures, engineers can effectively utilize Si3N4 ceramics in demanding environments.
Can Silicon Nitride Ceramics be Customized by Yomua ?
Yes, silicon nitride ceramics can indeed be customized by Yomua. Yomua is committed to working closely with its customers to achieve custom fabrication of unique materials and geometries tailored to specific needs. This includes the custom formulation of ceramic materials and the development of specialized manufacturing methods.
These customizations can involve:
- Shape and Size: Components can be manufactured in various shapes and sizes, from simple to complex geometries.
- Material Composition: Different additives can be incorporated into the silicon nitride matrix to modify properties like strength, toughness, and thermal conductivity.
- Surface Finish: Surface finishes can be customized to meet specific requirements, such as polished, ground, or textured surfaces.
- Heat Treatment: Heat treatment processes can be applied to improve specific properties, such as strength and toughness.
- Coating: Coatings can be applied to enhance surface properties like wear resistance, corrosion resistance, or electrical conductivity.
When considering a custom silicon nitride component, it’s important to consult Yomua to discuss your specific needs and explore the available customization options. We can provide guidance on material selection, design optimization, and manufacturing processes to ensure that the final product meets your requirements.
Is the Procurement Cost of Silicon Nitride Ceramics High?
Yes, the procurement cost of silicon nitride ceramics is generally higher compared to traditional materials like metals or plastics.
Several factors contribute to this higher cost:
Complex Manufacturing Processes:
- Silicon nitride requires specialized manufacturing techniques like hot pressing or pressureless sintering, which are more complex and energy-intensive than traditional ceramic processing methods.
High-Purity Raw Materials:
- The production of high-quality silicon nitride necessitates the use of high-purity raw materials, which can be expensive to source and process.
Limited Supply and Demand:
- While the demand for high-performance ceramics is increasing, the supply of silicon nitride remains relatively limited, which can drive up prices.
Superior Performance and Reliability:
- Silicon nitride’s exceptional mechanical, thermal, and chemical properties make it ideal for demanding applications. However, these superior characteristics come at a premium.
While the initial cost of silicon nitride ceramics may be higher, their long-term benefits, such as increased durability, reduced maintenance, and improved energy efficiency, often outweigh the upfront investment. For instance, silicon nitride bearings can last significantly longer than traditional steel bearings, leading to lower overall costs over their lifespan.
How are Silicon Nitride Ceramics Packaged?
Silicon nitride ceramics, renowned for their exceptional mechanical, thermal, and chemical properties, demand careful packaging to ensure their integrity during transportation and storage. Here’s a breakdown of key packaging considerations:
Material Selection
- Foam Inserts: These soft, shock-absorbing materials protect components from impact and vibration.
- Plastic or Metal Containers: Rigid containers provide sturdy protection, especially for larger or fragile components.
- Anti-static Packaging: For electronic applications, anti-static materials prevent electrostatic discharge damage.
Custom Packaging Solutions
- Tailored Foam Molds: These precision-cut molds provide a snug fit, minimizing movement and potential damage.
- Sealed Enclosures: For high-value or sensitive components, sealed enclosures protect against moisture, dust, and other contaminants.
Labeling and Documentation
- Clear Labeling: Product identification, handling instructions, and safety information should be prominently displayed.
- Safety Data Sheets (SDS): If applicable, SDS should be included to outline potential hazards and safety precautions.
Quality Control
- Component Inspection: Each ceramic component is visually inspected for defects before packaging.
- Packaging Integrity Testing: The packaging itself is tested to ensure it can withstand the rigors of transportation.
Shipping Considerations
- Transport Conditions: Temperature and humidity control may be necessary, especially for long-distance shipments.
- Carrier Selection: Choosing a reliable carrier with experience in handling fragile goods is crucial.
Additional Tips
- Desiccant Packs: These absorb moisture, preventing corrosion during storage.
- Vibration Dampening Materials: Additional layers of cushioning can further reduce the impact of vibration.
- Pallet Wrapping: For bulk shipments, pallet wrapping provides extra protection during transportation.
By following these guidelines and working with experienced packaging professionals, you can ensure that your silicon nitride ceramics arrive at their destination in perfect condition.
What are Zirconia Dispersion Strengthened Silicon Nitride Ceramics?
Zirconia dispersion strengthened silicon nitride (ZrO2-DS-Si3N4) ceramics are a class of advanced materials that combine the robust properties of silicon nitride with the transformative toughening effects of zirconia. This synergistic blend results in ceramics renowned for their exceptional mechanical performance, thermal stability, and chemical resistance, making them ideal for demanding applications in various industries.
Mechanical Properties
Strength and Toughness:
- Transformation Toughening: The incorporation of zirconia into the silicon nitride matrix significantly enhances fracture toughness. When subjected to stress, the zirconia particles undergo a phase transformation from tetragonal to monoclinic, absorbing energy and impeding crack propagation. This transformation toughening mechanism is crucial in preventing catastrophic failure.
- High Fracture Toughness Values: ZrO2-DS-Si3N4 ceramics can achieve fracture toughness values exceeding 10 MPa·m^(1/2), significantly surpassing conventional silicon nitride.
Flexural Strength:
- High Strength Levels: These ceramics exhibit excellent flexural strength, typically ranging from 600 to 900 MPa.
- Microstructure and Processing: The fine-grained microstructure, achieved through controlled sintering processes, and the uniform dispersion of zirconia particles within the silicon nitride matrix contribute to this high strength.
Hardness:
- Exceptional Hardness: ZrO2-DS-Si3N4 ceramics possess high hardness levels, often reaching 20 GPa or more, as measured by the Vickers hardness test.
- Wear Resistance: This exceptional hardness makes them suitable for applications requiring excellent wear resistance.
Thermal Properties
Thermal Stability:
- High-Temperature Performance: These ceramics exhibit outstanding thermal stability, retaining their mechanical properties even at temperatures exceeding 1200°C.
- Critical for High-Temperature Applications: This property is crucial for applications in high-temperature environments, such as those encountered in aerospace and energy generation.
Thermal Conductivity:
- Low Thermal Conductivity: While pure silicon nitride has relatively low thermal conductivity (around 30 W/m·K), the addition of zirconia has a minimal impact on this property.
- Thermal Barrier Applications: This low thermal conductivity makes ZrO2-DS-Si3N4 suitable for thermal barrier applications.
Coefficient of Thermal Expansion (CTE):
- Low CTE: The CTE of ZrO2-DS-Si3N4 is typically lower than that of many metals and other ceramics.
- Reduced Thermal Stresses: This low CTE helps to minimize thermal stresses during temperature fluctuations, enhancing the material’s durability.
Chemical Resistance
- Excellent Chemical Resistance: ZrO2-DS-Si3N4 ceramics exhibit excellent resistance to various corrosive environments, including acids and alkalis.
- Harsh Chemical Processing: This property makes them suitable for applications in harsh chemical processing environments where traditional materials may degrade.
Microstructural Characteristics
Grain Size Control:
- Fine-Grained Microstructure: Advanced sintering techniques, such as hot pressing or spark plasma sintering, are employed to achieve a fine-grained microstructure.
- Enhanced Mechanical Properties: A fine-grained microstructure contributes to improved mechanical properties, including strength and toughness.
Phase Distribution:
- Uniform Dispersion: The uniform dispersion of zirconia particles within the silicon nitride matrix plays a crucial role in enhancing toughness and strength.
- Crack Growth Inhibition: The dispersed zirconia particles inhibit crack growth and promote energy absorption during deformation.
Porosity Levels:
- Low Porosity: Low porosity levels are essential for optimal mechanical properties.
- Careful Fabrication Control: Careful control during fabrication ensures minimal defects and low porosity.
Applications
The exceptional properties of ZrO2-DS-Si3N4 ceramics have led to their widespread use in various industries:
Aerospace:
- Turbine Blades and Components: These ceramics are used in critical components like turbine blades, where high strength, toughness, and thermal stability are essential.
Biomedical:
- Implants and Prosthetics: Their biocompatibility and wear resistance make them suitable for biomedical applications, including dental implants and orthopedic devices.
Cutting Tools:
- Manufacturing Tools: The high hardness and wear resistance of these ceramics make them ideal for manufacturing cutting tools, enhancing tool life and improving machining efficiency.
Conclusion
Zirconia dispersion strengthened silicon nitride ceramics have emerged as a class of high-performance materials with a wide range of applications. Their unique combination of mechanical, thermal,
What is The Advanced Technologies in Silicon Nitride Ceramics?
This is a comprehensive and informative overview of silicon nitride ceramics, covering their advanced manufacturing technologies, enhanced material properties, innovative applications, and integration with other materials. Here are some key points highlighted from the text:
Advanced Manufacturing Technologies:
- Pressureless Sintering: Enables the production of complex-shaped silicon nitride ceramic parts with high precision and minimal defects.
- Hot Isostatic Pressing (HIP): Produces silicon nitride ceramic components with excellent mechanical properties, suitable for demanding applications like aerospace engines.
- Additive Manufacturing (3D Printing): Offers unprecedented design flexibility for manufacturing complex and customized silicon nitride ceramic components.
Enhanced Material Properties:
- Improved Toughness: Various techniques are employed to enhance the toughness of silicon nitride ceramics, making them more resistant to impact and dynamic loads.
- Customized Microstructure: Precise control of the microstructure allows for tailoring the properties of silicon nitride ceramics to specific applications.
Innovative Applications:
- Aerospace: Silicon nitride ceramics are crucial in aerospace components due to their high-temperature strength and thermal shock resistance.
- Automotive: They are used in turbochargers, engine components, and catalytic converters for improved efficiency and reduced emissions.
- Biomedical: Biocompatibility and wear resistance make silicon nitride ceramics suitable for dental implants and orthopedic devices.
- Electronics: High thermal conductivity and electrical insulation properties make them ideal for electronic packaging and semiconductor devices.
Integration with Other Materials:
- Ceramic-Metal Composites: Combining silicon nitride with metals enhances toughness and ductility while retaining high-temperature strength.
- Functional Coatings: Applying coatings to silicon nitride ceramics can further improve their performance in terms of wear resistance, corrosion resistance, and other specific properties.
The future of silicon nitride ceramics is promising, with ongoing research and development efforts aimed at further optimizing their properties and expanding their applications. This versatile material is poised to play a significant role in various industries, contributing to technological advancements and addressing critical challenges.
Silicon Nitride Ceramics Conclusion
Silicon nitride ceramics, renowned for their exceptional properties, have found wide-ranging applications. Advanced manufacturing techniques, such as pressureless sintering and hot isostatic pressing, enable the production of complex shapes and high-performance components. These ceramics are crucial in aerospace, automotive, biomedical, and electronics industries, offering superior strength, durability, and thermal stability. As research continues, silicon nitride ceramics are poised to revolutionize various fields, driving innovation and technological advancements.