Zirconia (ZrO₂) ceramics can exhibit different colors due to variations in their composition, microstructure, and processing methods. The color of zirconia is influenced by several factors, including the addition of stabilizers, dopants, impurities, and the presence of defects in the crystal structure. Here’s a detailed explanation of why zirconia ceramics have different colors:
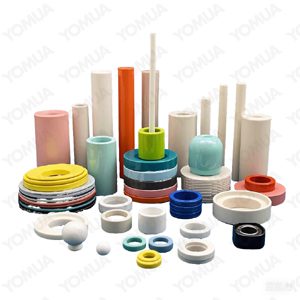
1. Stabilizers and Dopants
Zirconia is often stabilized with additives like yttria (Y₂O₃), ceria (CeO₂), or magnesia (MgO) to prevent phase transformations and improve its mechanical properties. These stabilizers can also affect the color:
- Yttria-Stabilized Zirconia (YSZ):
- Typically appears white or off-white due to the high reflectivity of the material.
- Small amounts of yttria do not significantly alter the color.
- Ceria-Stabilized Zirconia:
- May have a yellowish or beige tint due to the presence of cerium ions (Ce³⁺/Ce⁴⁺).
- Magnesia-Stabilized Zirconia:
- Usually white or grayish, depending on the amount of magnesia and processing conditions.
2. Impurities
Trace impurities in the raw materials or during processing can introduce color variations:
- Iron (Fe): Can cause a yellowish or brownish tint.
- Titanium (Ti): May lead to a grayish or bluish color.
- Other Transition Metals: Elements like chromium (Cr), manganese (Mn), or copper (Cu) can introduce green, pink, or blue hues.
3. Defects in the Crystal Structure
Color in zirconia can also arise from defects in the crystal lattice, such as oxygen vacancies or interstitial atoms:
- Oxygen Vacancies: These defects can cause light absorption in the visible spectrum, leading to darker or grayish tones.
- Reducing Atmosphere: Firing zirconia in a reducing atmosphere can create oxygen vacancies, resulting in a black or dark gray color (e.g., black zirconia).
4. Sintering Conditions
The temperature, atmosphere, and duration of sintering can influence the color:
- High-Temperature Sintering: Can cause grain growth and changes in light scattering, affecting the material’s opacity and color.
- Reducing Atmosphere: As mentioned, can produce black zirconia by creating oxygen vacancies.
- Oxidizing Atmosphere: Typically results in white or light-colored zirconia.
5. Additives for Aesthetic Purposes
In some applications, such as dental ceramics, colorants are intentionally added to match natural teeth:
- Pigments: Small amounts of metal oxides (e.g., iron oxide, erbium oxide) are added to create shades of white, yellow, or brown.
- Multilayer Zirconia: Dental zirconia often uses layered structures with graded colors to mimic the appearance of natural teeth.
6. Phase Composition
Zirconia exists in different phases (monoclinic, tetragonal, cubic), and the phase composition can affect color:
- Monoclinic Zirconia: Often appears white or off-white.
- Tetragonal Zirconia: Typically white or translucent.
- Cubic Zirconia: Can be transparent or translucent, often used in jewelry.
7. Translucency and Light Scattering
The translucency of zirconia depends on its grain size, density, and phase composition:
- Fine-Grained Zirconia: Appears more translucent and white.
- Coarse-Grained Zirconia: May appear more opaque and grayish.
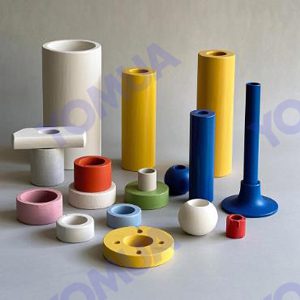
Common Colors of Zirconia and Their Causes
Color | Cause |
---|---|
White | Pure zirconia with no impurities or additives. |
Black | Oxygen vacancies created by sintering in a reducing atmosphere. |
Yellow/Brown | Presence of iron impurities or ceria stabilizers. |
Gray | Titanium impurities or coarse grain structure. |
Pink/Blue | Addition of transition metal oxides (e.g., chromium, copper). |
Translucent | High-density, fine-grained tetragonal or cubic zirconia. |
Applications of Colored Zirconia
- Dental Restorations: Multilayer and pigmented zirconia for crowns and bridges.
- Jewelry: Cubic zirconia gemstones in various colors.
- Industrial Components: Black zirconia for wear-resistant parts.
- Aesthetic Ceramics: Colored zirconia for decorative or functional purposes.
Conclusion
The color of zirconia ceramics is influenced by stabilizers, impurities, crystal defects, sintering conditions, and intentional additives. By controlling these factors, manufacturers can produce zirconia in a wide range of colors to meet specific application requirements, from industrial components to dental restorations and jewelry.