When diffusion bonding advanced ceramics to metals, intermediate layers are often added for the following reasons:

- Reducing Interfacial Stress
The significant difference in thermal expansion coefficients between ceramics and metals can lead to residual stresses during cooling after welding, causing cracks. Intermediate layers can alleviate these stresses and reduce the risk of cracking. - Improving Wettability
The poor wettability between ceramics and metals makes it difficult to form a strong bond during direct welding. Intermediate layers can enhance wettability and improve interfacial bonding strength. - Promoting Diffusion
Intermediate layers can act as diffusion mediators, accelerating atomic migration and enhancing the quality of interfacial bonding. - Preventing Harmful Reactions
Certain ceramics and metals may undergo harmful reactions at high temperatures. Intermediate layers can prevent these reactions, preserving material properties. - Optimizing Welding Processes
Intermediate layers can lower welding temperatures or shorten welding times, simplifying the process and reducing costs.
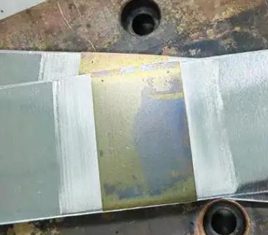
Common intermediate layer materials include active metals (such as titanium and zirconium) and metal composites (such as copper-titanium and nickel-titanium). When selecting an intermediate layer, compatibility with both ceramics and metals, thermal expansion coefficients, and welding process requirements must be considered.
Here are some examples of intermediate layers used in diffusion bonding of ceramics to metals:
- Titanium (Ti)
- Often used as an intermediate layer due to its high reactivity with both ceramics and metals, improving bonding strength.
- Zirconium (Zr)
- Similar to titanium, zirconium is highly reactive and promotes strong interfacial bonding.
- Copper-Titanium (Cu-Ti)
- A composite layer that combines the ductility of copper with the reactivity of titanium, enhancing bonding performance.
- Nickel-Titanium (Ni-Ti)
- A composite layer that leverages the unique properties of shape memory alloys to improve bonding under thermal cycling conditions.
- Silver (Ag)
- Used for its excellent wettability and ability to form strong bonds at relatively low temperatures.
- Aluminum (Al)
- Often used in bonding ceramics to aluminum-based metals due to its compatibility and ability to form a strong interface.
- Niobium (Nb)
- Known for its good thermal and mechanical properties, making it suitable for high-temperature applications.
- Vanadium (V)
- Used in specific applications where its reactivity and thermal properties are advantageous.
These intermediate layers are chosen based on the specific ceramic-metal combination, the desired bonding properties, and the operating conditions of the final product.
In summary, adding intermediate layers effectively addresses issues such as interfacial stress, wettability, diffusion, and harmful reactions in ceramic-metal diffusion bonding, thereby improving welding quality.