Advanced ceramics, also known as technical ceramics, are engineered materials with exceptional mechanical, thermal, electrical, and chemical properties. Below is an overview of the three most widely used advanced ceramics: Alumina (Aluminum Oxide – Al₂O₃), Silicon Carbide (SiC), and Zirconia (Zirconium Oxide – ZrO₂). Each is discussed in terms of properties, crystal structure, applications, advantages, disadvantages, manufacturing processes, cost, and future developments.
1. Alumina Ceramics (Aluminum Oxide – Al₂O₃)
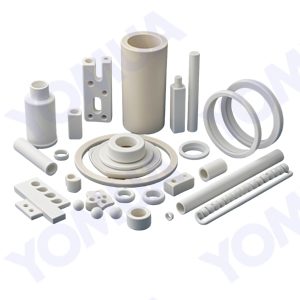
- Properties: Alumina is known for its high hardness and wear resistance, excellent electrical insulation, good thermal conductivity (for a ceramic), high melting point (~2072°C), and chemical inertness and biocompatibility.
- Crystal Structure: It has a hexagonal close-packed (HCP) crystal structure.
- Applications: Alumina finds use in electrical insulators, substrates, and spark plugs; cutting tools and wear-resistant components; biomedical implants (dental and joint replacements); and high-temperature furnace components.
- Advantages: Alumina is cost-effective compared to other advanced ceramics and available in a wide range of purity levels (85%-99.9%). It also boasts excellent mechanical and thermal properties.
- Disadvantages: Its brittleness and susceptibility to cracking under stress, along with lower fracture toughness compared to Zirconia, are key drawbacks.
- Manufacturing: Alumina is typically manufactured through powder pressing (dry or wet) followed by sintering at high temperatures. Additive manufacturing (3D printing) is an emerging technique.
- Cost: Alumina is relatively low cost, especially for lower purity grades.
- Future Development: Research focuses on improving fracture toughness through composite materials and enhancing manufacturing techniques like additive manufacturing for complex geometries.
2. Silicon Carbide Ceramics (SiC)

- Properties: Silicon Carbide exhibits extremely high hardness (Mohs hardness of 9.5), excellent thermal conductivity (better than most metals), high thermal shock resistance, a low thermal expansion coefficient, and superior chemical resistance.
- Crystal Structure: It exists in hexagonal (α-SiC) or cubic (β-SiC) crystal structures.
- Applications: SiC is used in high-temperature applications (furnace components, heat exchangers), the semiconductor industry (wafer substrates, power electronics), armor and ballistic protection, and automotive components (brake discs, turbocharger rotors).
- Advantages: SiC offers exceptional thermal and mechanical properties, is lightweight and durable, and resists oxidation and corrosion.
- Disadvantages: It is expensive to manufacture and difficult to machine due to its extreme hardness.
- Manufacturing: Manufacturing methods include hot pressing, sintering, or chemical vapor deposition (CVD), and reaction bonding for complex shapes.
- Cost: SiC is high cost due to complex manufacturing processes.
- Future Development: Increased use in electric vehicles (EVs) for power electronics and development of SiC-based composites for enhanced properties are key areas of focus.
3. Zirconia Ceramics (Zirconium Oxide – ZrO₂)

- Properties: Zirconia is characterized by high fracture toughness (due to transformation toughening), excellent wear resistance, high strength and hardness, low thermal conductivity, and biocompatibility and chemical inertness.
- Crystal Structure: It exists in monoclinic (at room temperature), tetragonal, and cubic phases. Transformation toughening occurs between phases under stress.
- Applications: Zirconia is used in biomedical implants (dental crowns, hip replacements), cutting tools and wear-resistant components, oxygen sensors and fuel cell membranes, and jewelry (synthetic gemstones).
- Advantages: High fracture toughness compared to other ceramics, aesthetic appeal (can be made in white or translucent forms), and excellent biocompatibility.
- Disadvantages: Susceptibility to low-temperature degradation (aging) in humid environments and higher cost than Alumina are limitations.
- Manufacturing: Manufacturing typically involves powder pressing and sintering, and additive manufacturing for custom biomedical implants.
- Cost: Zirconia’s cost is moderate to high, depending on the application.
- Future Development: Research aims to improve resistance to low-temperature degradation and expand the use of additive manufacturing for customized medical devices.
Summary Table:
Here’s a table summarizing the three advanced ceramics:
Property/Feature | Alumina (Al₂O₃) | Silicon Carbide (SiC) | Zirconia (ZrO₂) |
---|---|---|---|
Properties | High hardness, wear resistant, excellent electrical insulation, good thermal conductivity, high melting point, chemically inert, biocompatible | Extremely high hardness, excellent thermal conductivity, high thermal shock resistance, low thermal expansion, superior chemical resistance | High fracture toughness, excellent wear resistance, high strength & hardness, low thermal conductivity, biocompatible, chemically inert |
Crystal Structure | Hexagonal close-packed (HCP) | Hexagonal (α-SiC) or Cubic (β-SiC) | Monoclinic, Tetragonal, Cubic |
Applications | Electrical insulators, cutting tools, wear parts, biomedical implants, furnace components | High-temperature components, semiconductors, armor, automotive components | Biomedical implants, cutting tools, wear parts, oxygen sensors, fuel cells, jewelry |
Advantages | Cost-effective, wide range of purity, excellent mechanical & thermal properties | Exceptional thermal & mechanical properties, lightweight, durable, oxidation & corrosion resistant | High fracture toughness, aesthetic appeal, excellent biocompatibility |
Disadvantages | Brittle, low fracture toughness | Expensive, difficult to machine | Susceptible to low-temperature degradation, higher cost than Alumina |
Manufacturing | Powder pressing & sintering, additive manufacturing | Hot pressing, sintering, CVD, reaction bonding | Powder pressing & sintering, additive manufacturing |
Cost | Relatively low | High | Moderate to high |
Future Developments | Improved fracture toughness, enhanced additive manufacturing | Increased use in EVs, SiC-based composites | Improved low-temperature degradation resistance, expanded additive manufacturing use |
Conclusion
Advanced ceramics represent a class of materials engineered for exceptional performance in demanding applications. As we’ve explored, alumina, silicon carbide, and zirconia each offer a unique combination of properties that make them indispensable in various industries.
- Alumina stands out for its versatility and cost-effectiveness, making it a workhorse in applications ranging from electrical insulation to biomedical implants.
- Silicon carbide shines in extreme environments, where its exceptional hardness, thermal conductivity, and high-temperature strength are crucial, such as in cutting tools, power electronics, and aerospace components.
- Zirconia offers a compelling balance of strength, toughness, and biocompatibility, making it a preferred material for dental and orthopedic implants, as well as high-performance wear parts.
While each material has its limitations, ongoing research and development are constantly pushing the boundaries of their performance. Innovations in manufacturing techniques, such as additive manufacturing, are enabling the production of complex shapes and customized solutions. Moreover, the development of new ceramic composites is opening up possibilities for even greater enhancements in properties like fracture toughness and high-temperature strength.
Looking ahead, advanced ceramics are poised to play an increasingly important role in addressing global challenges. Their unique attributes position them as key enablers in areas like sustainable energy, advanced healthcare, and efficient transportation. As technology continues to advance, we can expect to see even more innovative applications emerge, solidifying the importance of advanced ceramics in shaping our future.