This section provides a comprehensive examination of oxide, non-oxide, and composite ceramics, focusing on their production processes and applications. Here’s a breakdown:
Classification and Composition
Advanced ceramics are classified based on their chemical composition, with oxide ceramics consisting of metal oxides such as alumina, zirconia, and silica, non-oxide ceramics including carbides, nitrides, and borides like silicon carbide and silicon nitride, and composite ceramics combining different materials, often fibers within a matrix, to enhance properties.
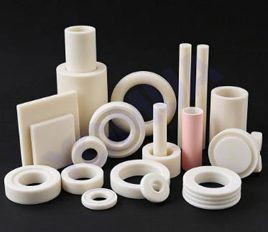
-
- Oxide Ceramics: Examples include alumina (Al2O3), zirconia (ZrO2), and silica (SiO2), known for their oxygen-containing structures. These are non-metallic, inorganic compounds, with properties adjusted through microstructure design.
-
- Non-Oxide Ceramics: Include aluminium nitrides (AlN), silicon nitrides (Si3N4), and various carbides like silicon carbide (SiC), characterized by the absence of oxygen, often containing nitrogen or carbon.
-
- Composite Ceramics: Defined as materials integrating ceramics with reinforcing constituents like fibers, whiskers, or particles, such as ceramic matrix composites (CMCs) like oxide-oxide (Ox-Ox) or silicon carbide-silicon carbide (SiC-SiC).
Production Processes
The production methods vary significantly, reflecting the chemical and structural differences:
-
- Oxide Ceramics Production:
-
- Raw materials are sourced from minerals like bauxite for alumina and zircon for zirconia. These are crushed, ground, and purified to form high-purity powders.
-
- The process involves mixing with binders (e.g., water, wax, or plastic resin) for shaping via pressing, casting, or extrusion, followed by sintering at high temperatures to achieve densification. For instance, alumina is sintered to enhance hardness and thermal stability.
-
- Additional steps may include specialized post-firing machining for precision, often under controlled atmospheres to maintain purity.
-
- Oxide Ceramics Production:
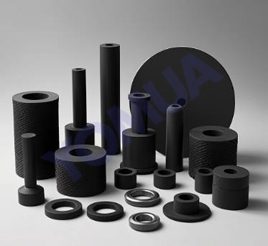
-
- Non-Oxide Ceramics Production:
-
- Production relies on specific chemical reactions or high-temperature processes. For example, silicon nitride is produced by nitriding silicon powder in a nitrogen atmosphere at high temperatures, or through reaction-bonded silicon nitride where silicon reacts with nitrogen.
-
- Silicon carbide is typically made via the Acheson process, heating a mixture of sand and carbon in an electric furnace. Other methods include hot pressing or HIP (Hot Isostatic Pressing) for densification, requiring temperatures often exceeding 2000°C for borides like B4C.
-
- These processes are more complex due to the need to exclude oxygen, often involving vacuum or inert atmospheres to prevent oxidation.
-
- Non-Oxide Ceramics Production:
-
- Composite Ceramics Production:
-
- Involves creating ceramic fibers (e.g., alumina or silicon carbide fibers) and preparing a matrix material, which can be oxide or non-oxide based. Fibers are then infiltrated with the matrix, often using techniques like chemical vapor infiltration (CVI), liquid silicon infiltration, or polymer infiltration and pyrolysis (PIP).
-
- Consolidation is achieved through sintering, hot pressing, or HIP, ensuring the fibers are bonded within the matrix. For example, oxide-oxide CMCs use alumina fibers in an alumina matrix, processed to maintain fiber integrity during high-temperature treatment.
-
- The process is more intricate, aiming to balance fiber-matrix interaction for optimal mechanical properties, often requiring specialized equipment to avoid fiber damage.
-
- Composite Ceramics Production:
Applications and Properties
The applications are driven by the unique properties each type offers, catering to diverse industrial needs:
-
- Oxide Ceramics Applications:
-
- Properties: High-temperature stability, electrical insulation, corrosion resistance, and good thermal shock resistance. For instance, alumina has high hardness (9 on Mohs scale) and thermal conductivity, while zirconia offers high fracture toughness.
-
- Applications: Widely used in electrical insulators for electronics, refractory materials for furnace linings, dental implants due to biocompatibility, and thermal barrier coatings in engines. Silica is crucial in glass and refractory applications, and yttria in high-temperature sensors.
-
- Oxide Ceramics Applications:
-
- Non-Oxide Ceramics Applications:
-
- Properties: High strength, hardness, resistance to oxidation at high temperatures, and excellent wear resistance. Silicon nitride, for example, has high compressive strength and thermal shock resistance, while silicon carbide is known for its abrasive properties and semiconductor capabilities.
-
- Applications: Found in cutting tools for machining, turbine blades in jet engines, bearings for high-speed applications, abrasives for grinding wheels, and semiconductor substrates like aluminium nitride for heat sinks in electronics.
-
- Non-Oxide Ceramics Applications:
-
- Composite Ceramics Applications:
-
- Properties: Improved fracture toughness, damage tolerance, high strength, and resistance to thermal shock, achieved by combining fibers (e.g., carbon or SiC) with a ceramic matrix. This addresses the brittleness of monolithic ceramics, with CMCs showing enhanced performance under cyclic loads.
-
- Applications: Predominantly in aerospace for turbine blades, exhaust components, and re-entry shields due to lightweight and high-temperature resistance. Also used in nuclear applications for structural components, and in automotive for brake disks, offering weight savings and durability under extreme conditions.
-
- Composite Ceramics Applications:
Comparative Table
To summarize the key differences, the following table compares the production and application aspects:
Category | Production Method | Key Properties | Primary Applications |
---|---|---|---|
Oxide Ceramics | Sintering high-purity metal oxide powders, shaping, firing | High-temperature stability, electrical insulation | Electrical insulators, refractories, dental implants |
Non-Oxide Ceramics | Specific reactions, high-temperature processes, e.g., nitriding | High strength, hardness, oxidation resistance | Cutting tools, turbine blades, abrasives |
Composite Ceramics | Fiber-matrix infiltration, consolidation via sintering/HIP | Improved toughness, damage tolerance, thermal shock resistance | Aerospace components, nuclear structures, brake disks |
This table highlights the distinct approaches and uses, reflecting the tailored nature of each ceramic type for specific industrial demands.
Additional Insights
An interesting observation is the evolution of composite ceramics, particularly CMCs, which are increasingly adopted in aerospace for their ability to withstand extreme conditions while reducing weight, a significant shift from traditional ceramic applications. For example, oxide-oxide CMCs are gaining traction for their cost-effectiveness and performance in high-temperature environments, as noted in recent industry reports.
Non-oxide ceramics, while challenging to produce due to oxygen exclusion, offer superior performance in reducing environments, making them critical for advanced engineering applications. Oxide ceramics, on the other hand, remain staples in electrical and thermal insulation, benefiting from their stability and ease of processing.
The comparison also reveals that while oxide ceramics are more common and easier to handle, non-oxide and composite ceramics push the boundaries of material science, addressing limitations like brittleness through innovative composite designs.
Conclusion
In summary, oxide, non-oxide, and composite ceramics each serve unique roles, driven by their production methods and property profiles. Oxide ceramics excel in stability and insulation, non-oxides in strength and hardness, and composites in toughness and damage tolerance, catering to a wide range of high-tech applications from electronics to aerospace.