Producing advanced ceramic components presents several challenges due to the unique properties and requirements of these materials. Here are some of the key challenges:
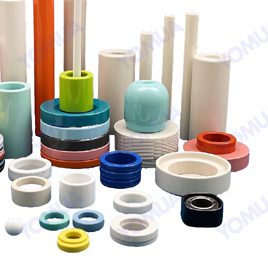
1. Material Properties:
- Brittleness: Ceramics are inherently brittle, making them prone to cracking and fracture under mechanical stress.
- Hardness: While hardness is an advantage for wear resistance, it makes machining and shaping difficult.
- Thermal Shock Resistance: Sudden temperature changes can cause cracking due to thermal expansion and contraction.
2. Manufacturing Processes:
- Complex Shaping: Advanced ceramics often require precise and complex shapes, which are difficult to achieve with traditional machining methods.
- Sintering: The sintering process, which involves heating the material to high temperatures to achieve densification, must be carefully controlled to avoid defects such as warping, cracking, or incomplete densification.
- Dimensional Tolerances: Achieving tight dimensional tolerances is challenging due to shrinkage and warping during sintering.
3. Quality Control:
- Defect Detection: Internal defects such as voids, cracks, or inclusions are difficult to detect and can significantly affect the performance of the component.
- Consistency: Ensuring consistent material properties and performance across batches is challenging due to variations in raw materials and processing conditions.
4. Cost:
- Raw Materials: High-purity raw materials required for advanced ceramics can be expensive.
- Processing Costs: The specialized equipment and processes needed for manufacturing advanced ceramics, such as hot pressing or hot isostatic pressing, are costly.
- Machining and Finishing: Post-sintering machining and finishing processes are time-consuming and expensive due to the hardness of ceramics.
5. Joining and Integration:
- Joining Techniques: Joining ceramics to other materials (e.g., metals) is challenging due to differences in thermal expansion coefficients and bonding issues.
- Integration: Integrating ceramic components into larger systems can be difficult due to their brittleness and the need for precise alignment and fitting.
6. Design and Engineering:
- Design Limitations: The brittleness and lack of ductility of ceramics limit design options and require careful consideration of stress concentrations and load paths.
- Simulation and Modeling: Accurate simulation and modeling of ceramic components are challenging due to their complex failure mechanisms and anisotropic properties.
7. Environmental and Operational Factors:
- Wear and Corrosion: While ceramics are generally wear and corrosion-resistant, certain environments can still cause degradation.
- Thermal Management: Managing thermal stresses and ensuring thermal stability in high-temperature applications is critical.
8. Research and Development:
- Material Development: Developing new ceramic materials with improved properties (e.g., higher toughness, better thermal shock resistance) requires significant R&D efforts.
- Process Innovation: Innovating new manufacturing processes to reduce costs and improve quality is an ongoing challenge.
9. Regulatory and Standards Compliance:
- Certification: Meeting industry standards and regulatory requirements for critical applications (e.g., medical, aerospace) can be demanding.
- Testing and Validation: Extensive testing and validation are required to ensure reliability and performance under operational conditions.
Addressing these challenges requires a multidisciplinary approach, combining expertise in materials science, engineering, manufacturing, and quality control. Advances in technology and process innovation continue to push the boundaries of what is possible with advanced ceramic components.