Porous zirconia (ZrO2) ceramics are advanced ceramics materials that have gained significant attention in various applications, particularly in the field of biomedical engineering and bone tissue regeneration. The synthesis and characterization of these ceramics involve several key processes and properties that contribute to their functionality.
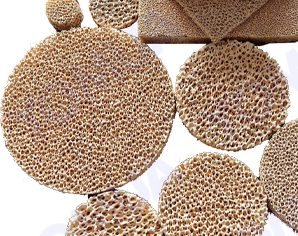
1. Introduction
We need better thermal insulation. Modern insulation should be high-quality, eco-friendly, and efficient. Porous zirconium oxide (ZrO2) ceramics are promising because they combine the good qualities of ceramics with the advantages of having pores. They resist high temperatures and corrosion, don’t conduct much heat, and are chemically stable. They are also light, strong for their weight, and can withstand sudden temperature changes. These properties make them useful for thermal insulation.
A porous ceramic’s performance depends on both its material and its pore structure. Things like the percentage of open and closed pores, the size and distribution of pores, how the pores are arranged, and the connections between pores all matter. How we make the ceramic is key to controlling these features. Different manufacturing methods create different pore structures.
A big challenge is making porous ceramics that are both good insulators and strong. Good insulation usually means lots of pores (high porosity), but high porosity can weaken the material. Also, when used for insulation, these ceramics face tough conditions: repeated heating and cooling, and sometimes exposure to moisture or salt. These conditions can degrade the material’s strength and insulation ability over time.
This article reviews how we design strong and insulating porous ZrO2 ceramics. It also explains how different manufacturing methods affect the material’s structure and performance.
2. Understanding the Basics
A. How Pores Affect Strength
A material’s strength, especially its ability to withstand compression, is directly related to its inner structure. This includes how many pores there are (porosity), the shape and size of the pores, how they’re distributed, and the properties of the solid material itself. Scientists have developed formulas to describe how strength relates to pore structure, especially porosity.
Early research mostly focused on the relationship between porosity and strength. The “minimum contact area model” suggests that strength decreases exponentially as porosity increases. However, this model is only accurate for materials with low porosity (less than 40%). Later models considered pore shape and other factors. Ashby and Gibson, for example, created different models for closed pores, open pores, and honeycomb-shaped pores. Research has shown that at high porosity levels, the way the pores are connected becomes more important than their specific shape.
In short, a material’s strength depends on its porosity, pore shape, and the strength of the solid material making up the pore walls. Smaller, more uniform pores, a strong base material, and closed pores can all contribute to a strong, highly porous ceramic.
B. How Pores Affect Thermal Conductivity
Air is a good insulator. Adding pores to a ceramic reduces its density and makes it a better insulator. Scientists use models to predict how much heat will travel through a porous material. These models often simplify the material into a solid part and a gas-filled pore part.
Different models work better for different pore structures. The Maxwell-Eucken model is good for closed pores. The effective medium model (EMT) can predict the relationship between porosity and thermal conductivity. More pores mean lower thermal conductivity. Other models, like the Landauer model, are better suited for open-pore structures. The accuracy of these models depends on how well they represent the real structure of the porous ceramic. However, even the best models simplify the structure, making it hard to precisely analyze how pore size and shape affect heat flow.
3. Making Porous ZrO2 Ceramics: Different Methods
There are four main methods to make these Porous ZrO2 Ceramics:

a. Particle Accumulation
This is the simplest method. ZrO2 particles are mixed with other ingredients, formed into a shape (a “green body”), and then heated (sintered). During heating, the particles bond together, but some empty spaces remain, creating the pores. The size and number of pores depend on the original particle size and the heating process. Usually, this method results in materials with less than 50% porosity, and the pores are 2-5 times larger than the starting particles.
Researchers have tried to improve this method. One approach involves adding zirconia particles to a zirconia felt framework. This method can increase strength, but it still has limitations in achieving very high porosity. 3D printing, a type of particle accumulation, is a newer technique that can create complex shapes and control pore structure better.
b. Template Replication
This method uses a “template” with a desired pore structure. A ZrO2 slurry or precursor is applied to the template, filling its pores. The template is then removed, leaving behind a ceramic with pores that match the template. This method allows for good control over pore size and shape. Materials with over 70% porosity can be made this way. Many different templates can be used, including synthetic materials like foam and natural materials like wood.
c. Sacrificial Template
This method mixes ZrO2 with a “sacrificial” material that will later be removed. The mixture is formed into a shape, and then the sacrificial material is eliminated, leaving behind pores. This method is good for making lightweight, strong, and insulating ceramics. There are several variations:
- Adding Pore-Forming Agents: Particles of a material (organic or inorganic) are mixed with the ZrO2. These particles are later burned away or dissolved, leaving pores.
- Emulsion Pore-Forming: An oil-in-water mixture (emulsion) is created with the ZrO2. The continuous part of the emulsion is solidified, and then the oil is removed, creating pores.
- Solvent Pore-Forming: The solvent in a ZrO2 slurry or gel is used to create pores as it evaporates. This includes methods like sol-gel (where a gel forms the structure), using tert-butyl alcohol (which evaporates easily), and freeze-drying (where the solvent is frozen and then sublimated).
d. Direct Foaming
This method creates pores by introducing gas bubbles directly into the ZrO2 slurry. The bubbles are stabilized, the slurry is solidified, and then the material is heated. The stability of the foam is crucial. Different things can stabilize the foam, including surfactants (like soap), proteins (like egg white), and even small particles.
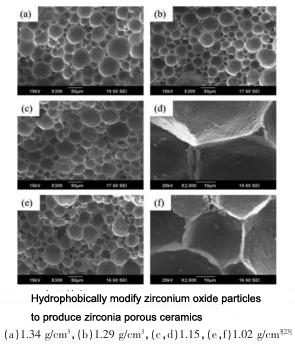
The long-chain anionic surfactant triethanolamine dodecyl sulfate (TLS) was used to hydrophobically modify zirconium oxide particles to produce zirconia porous ceramics with a volume density of 1.02-1.34 g/cm 3 , a pore size of less than 100 μm, and a complete pore wall structure.
4. Conclusion and Future Directions
ZrO2 is a great material for high-temperature insulation because it has a high melting point, is wear-resistant, naturally resists oxidation, is heat-resistant, and chemically stable. It also has low thermal conductivity. By carefully controlling how we make porous ZrO2, we can create materials that are light, strong, and excellent insulators. This will improve their use in high-temperature protection and other industrial applications.
Beyond insulation, porous ZrO2 has other uses. It can be used as a catalyst or catalyst support because of its unique chemical properties. It can also be used in oxygen sensors and fuel cells due to its ability to conduct oxygen ions. Further research will likely lead to even more advanced ways to make and use porous ZrO2 ceramics.