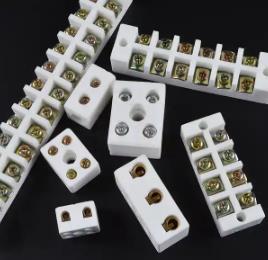
The Problem: Why Oxidation Occurs
- High-Temperature Processes: Ceramic-to-metal bonding often requires elevated temperatures, which can cause the metal to react with atmospheric oxygen, forming a brittle oxide layer at the interface.
- Consequences: The oxide layer is brittle and prone to crack propagation, leading to bond failure and reduced mechanical performance.
Potential Solutions to Minimize Interfacial Oxidation
Solution | Description | Key Benefits |
---|---|---|
Controlled Atmosphere | Conduct bonding in a vacuum or inert gas (e.g., argon, nitrogen) environment. | Prevents oxygen exposure, eliminating oxide formation. |
Surface Modification | Apply coatings (e.g., gold, platinum, silicon carbide) or pretreat surfaces (etching, sandblasting). | Protects metal surfaces and enhances reactivity for better adhesion. |
Bonding Technique Optimization | Use lower temperatures and shorter bonding times. | Reduces oxidation by minimizing high-temperature exposure. |
Interlayer Materials | Introduce reactive interlayers (e.g., titanium, zirconium) or active brazing alloys. | Reduces oxides and improves wetting at the interface. |
Anti-Oxidation Coatings | Apply coatings (e.g., nickel, chromium) to the metal surface. | Acts as a barrier against oxygen diffusion. |
Post-Bonding Treatments | Perform annealing or surface treatments after bonding. | Stabilizes the interface and reduces residual stresses. |
- Controlled Atmosphere
- Vacuum Bonding: Conduct the process in a vacuum to eliminate oxygen and prevent oxide formation.
- Inert Gases: Use argon or nitrogen to create a protective environment, reducing oxidation risks.
- Surface Modification
- Coatings: Apply oxidation-resistant materials (e.g., noble metals like gold or platinum, or carbides like silicon carbide) to protect the metal surface.
- Surface Pretreatments: Use techniques like chemical etching, plasma cleaning, or mechanical abrasion to remove existing oxides and enhance surface reactivity.
- Bonding Technique Optimization
- Lower Temperatures: Reduce bonding temperatures to minimize oxidation.
- Shorter Bonding Times: Limit high-temperature exposure to decrease oxide formation.
- Interlayer Materials
- Active Brazing Alloys: Use alloys containing reactive elements (e.g., titanium, zirconium) that reduce oxides and improve wetting at the interface.
- Anti-Oxidation Coatings
- Apply coatings (e.g., nickel, chromium) on the metal surface to act as a barrier against oxygen diffusion.
- Post-Bonding Treatments
- Perform annealing or surface treatments to stabilize the interface and reduce residual stresses that may promote oxidation.
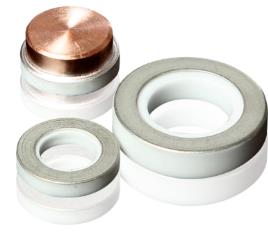
Choosing the Best Solution
The optimal approach depends on several factors:
- Materials: The types of ceramic and metal being bonded.
- Bonding Process: The specific technique used (e.g., brazing, diffusion bonding).More information ,please see this article:How Al2O3 Ceramics Join or Integrate with Metals?
- Performance Requirements: Desired bond strength, thermal stability, and operating environment.
Additional Considerations
- Consultation: Collaborate with materials scientists or engineers to optimize the bonding process for specific applications.
- Combination of Methods: Often, a combination of the above strategies is required to achieve the best results.
Key Takeaways
- Interfacial oxidation is a critical challenge in ceramic-to-metal bonding, but it can be mitigated through controlled atmospheres, surface modifications, optimized bonding parameters, and interlayer materials.
- The choice of solution depends on material compatibility, bonding techniques, and performance requirements.
- For complex applications, professional consultation is recommended to ensure reliable and durable bonds.
This version is concise, well-structured, and easy to follow, making it suitable for technical documentation or educational purposes. Let me know if further adjustments are needed!
Conclusion
Interfacial oxidation during ceramic-to-metal bonding is a significant challenge that can compromise the strength and reliability of the bond. However, by employing targeted strategies such as controlled atmospheres, surface modifications, optimized bonding parameters, and the use of interlayer materials or anti-oxidation coatings, this issue can be effectively mitigated. Each solution offers unique benefits, and the optimal approach depends on factors such as the materials involved, the bonding process, and the specific performance requirements.
For complex applications, a combination of these methods is often necessary to achieve the best results. Additionally, consulting with materials scientists or engineers can help tailor the bonding process to meet specific needs, ensuring durable and high-performance ceramic-to-metal bonds. By addressing interfacial oxidation proactively, industries can enhance the reliability and longevity of their bonded components, paving the way for advanced ceramics applications in electronics, aerospace, energy, and beyond.