LTCC (Low Temperature Co-fired Ceramic) technology is a specialized manufacturing process for producing multi-layered ceramic packages used in electronic devices. LTCC technology relies on a variety of advanced ceramic materials, each, for example alumina ceramic carefully, selected for its specific properties and role in the manufacturing process.
It’s notable for integrating passive components like capacitors, inductors, and resistors directly within the package, creating a highly compact and efficient design. A crucial aspect of LTCC is its ability to co-fire the ceramic and conductive materials at relatively low temperatures (under 1000°C), resulting in a strong, dense ceramic structure ideal for demanding electronic applications.
Manufacturing Process
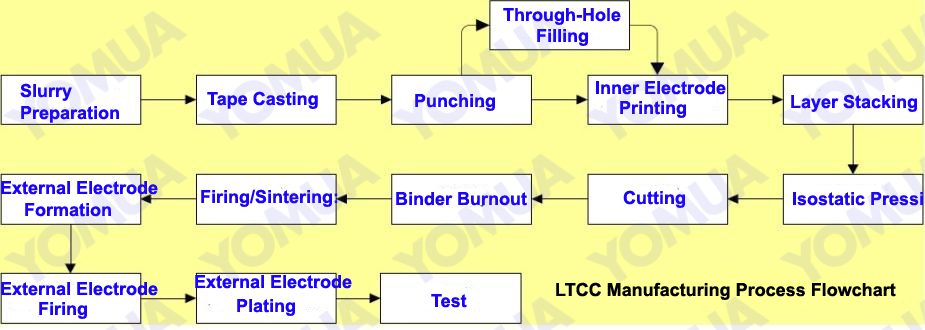
-
Slurry Preparation: The process begins with the preparation of the ceramic slurry, a mixture of ceramic powders, binders, solvents, and other additives. This slurry is carefully formulated to achieve the desired properties for the final LTCC substrate.
-
Tape Casting: The slurry is then cast into thin sheets or “tapes” using a precision tape casting machine. This process controls the thickness and uniformity of the ceramic layers.
-
Punching/Via Formation: Holes, or vias, are mechanically punched or laser-drilled into the green (unfired) ceramic tapes. These vias will provide electrical connections between different layers of the LTCC circuit.
-
Through-Hole Filling: After punching, some vias may require filling with conductive paste to create robust connections between layers. This is typically done using a screen printing or dispensing process.
-
Inner Electrode Printing: Conductive inks, typically containing metals like gold or silver, are screen-printed onto the ceramic tapes to form the inner conductor patterns of the circuit.
-
Layer Lamination/Stacking: The patterned and via-filled tapes are then precisely aligned and laminated together to form a multilayer structure. This stacking process creates the complex circuitry within the LTCC device.
-
External Electrode Formation: Conductive pastes are applied to the outer layers of the stacked structure to create the external electrodes or terminations.
-
Firing/Sintering: The laminated structure is fired in a furnace at a controlled temperature profile. This process removes the organic binders and densifies the ceramic material, resulting in a robust and hermetic structure.
-
Binder Burnout: Before the final high-temperature firing, a separate binder burnout step may be performed at a lower temperature to remove the organic materials from the structure more gradually.
-
Cutting/Dicing: The fired LTCC substrate is then cut or diced into individual components or circuits using a saw or laser.
-
Isostatic Pressing (Optional): In some cases, isostatic pressing may be used before firing to improve the density and uniformity of the LTCC structure.
-
External Electrode Firing: The external electrodes are fired to ensure good adhesion and electrical conductivity.
-
External Electrode Plating (Optional): The external electrodes may be plated with additional metals, such as nickel or gold, to enhance their solderability or corrosion resistance.
-
Testing: Finally, the individual LTCC components or circuits are tested to verify their electrical performance and functionality.
Fourteen Major Issues
However, it still faces some challenges that need to be addressed to improve its performance, reliability, and cost-effectiveness. The fourteen major issues that LTCC technology needs to solve are:
Here’s a table summarizing the challenges and limitations of LTCC technology, along with potential areas for improvement:
Challenge/Limitation | Description | Potential Improvements |
---|---|---|
Shrinkage Control & Dimensional Accuracy | Significant and often non-uniform shrinkage during firing leads to dimensional inaccuracies and misalignment. | Improved material processing, firing control, and shrinkage prediction models. |
Thermal Management Limitations | Lower thermal conductivity compared to alumina can cause heat buildup in high-power applications. | Development of LTCC materials with higher thermal conductivity, optimized heat sink integration, and thermal vias. |
Cavity & 3D Structure Fabrication | Creating complex 3D structures and cavities is challenging, requiring precise control and specialized techniques. | Improved tooling, processing techniques, and cavity filling methods. |
Large Area Processing Challenges | Scaling to larger substrate sizes introduces warpage and camber, impacting planarity and assembly. | Development of methods to maintain dimensional control over larger areas. |
Embedded Passive Component Integration | Achieving high precision and stability for embedded passives remains challenging due to material and process variations. | Improved material properties, processing control, and design/modeling tools for embedded passives. |
Material Compatibility & CTE Mismatch | Ensuring compatibility between different materials (conductors, dielectrics, adhesives) and managing CTE mismatch is crucial. | Careful material selection, CTE matching, and stress analysis. |
Manufacturing Cost & Throughput | The multi-step process contributes to high cost. | Process optimization, yield improvement, and waste reduction. |
Reliability & Long-Term Performance | Ensuring long-term reliability under various environmental conditions requires comprehensive testing. | More comprehensive reliability studies and accelerated aging tests. |
Design Tooling & Accessibility | Specialized design tools and expertise are required, limiting accessibility. | More user-friendly design tools and improved simulation capabilities. |
Standardization & Interoperability | Lack of standardization hinders adoption and interoperability. | Development of industry-wide standards for design, materials, and testing. |
High-Frequency Performance | Dielectric losses at high frequencies can impact signal integrity. | Research into LTCC materials with lower dielectric loss. |
Integration with Active Devices | Integrating active devices requires optimized die attachment and thermal management. | Optimized assembly techniques and thermal management solutions for active device integration. |
Environmental Considerations | Manufacturing can involve hazardous materials. | Development of more environmentally friendly processes and recyclable materials. |
Testing & Characterization | Testing and characterizing LTCC components, especially at high frequencies, can be complex. | Development of accurate and reliable testing methods. |
-
Shrinkage Control and Dimensional Accuracy: LTCC experiences significant shrinkage (typically several percent) during the firing process. Predictable and uniform shrinkage is crucial for achieving dimensional accuracy, especially in complex multilayer structures. Variations in shrinkage can lead to misalignment of layers, impacting electrical performance and the integration of surface-mounted components. Improved material processing and firing control are needed to minimize and manage shrinkage variations.
-
Thermal Management Limitations: LTCC materials generally have lower thermal conductivity compared to other ceramic substrates like alumina. This can lead to heat buildup in high-power applications, negatively affecting performance and reliability. While heat sinks and thermal vias can be incorporated, they add complexity and cost. Research into LTCC materials with higher thermal conductivity is essential.
-
Cavity and 3D Structure Fabrication: Creating cavities and other 3D structures within LTCC substrates adds significant manufacturing complexity. Precise control over the cavity dimensions and location is critical. Challenges include ensuring proper filling of cavities during lamination, preventing delamination during firing, and maintaining dimensional accuracy. Improved tooling and processing techniques are needed.
-
Large Area Processing Challenges: Scaling LTCC processing to larger substrate sizes is difficult due to the aforementioned shrinkage issues. Warpage and camber can become more pronounced in larger parts, impacting planarity and making subsequent assembly steps more challenging. Developing methods to maintain dimensional control over larger areas is crucial for expanding the applicability of LTCC.
-
Embedded Passive Component Integration: While LTCC allows for the integration of passive components (resistors, capacitors, inductors) within the multilayer structure, achieving high precision and stability remains a challenge. Variations in material properties and processing can affect component performance. Furthermore, the design and modeling of embedded passives require specialized tools and expertise.
-
Material Compatibility and CTE Mismatch: LTCC systems often involve the integration of various materials, including conductors (e.g., gold, silver), dielectrics, resistors, and adhesives. Ensuring compatibility between these materials, particularly in terms of their coefficients of thermal expansion (CTE), is critical. CTE mismatch can lead to stress buildup during thermal cycling, resulting in cracks, delamination, and device failure.
-
Manufacturing Cost and Throughput: LTCC processing involves multiple steps, including tape casting, screen printing, lamination, firing, and testing. Each of these steps contributes to the overall cost. Improving process yields, reducing material waste, and streamlining manufacturing processes are essential for making LTCC technology more cost-competitive.
-
Reliability and Long-Term Performance: Ensuring the long-term reliability of LTCC devices under various environmental conditions (temperature, humidity, vibration) is crucial. While accelerated aging tests are used, more comprehensive reliability studies are needed to fully understand the long-term performance of LTCC components, especially in harsh environments.
-
Design Tooling and Accessibility: Designing complex LTCC circuits requires specialized design tools and expertise. Making these tools more user-friendly and accessible to a wider range of engineers would facilitate broader adoption of the technology. Improved simulation capabilities for predicting performance and optimizing designs are also needed.
-
Standardization and Interoperability: The lack of standardization in design rules, material specifications, and testing protocols can hinder the adoption of LTCC technology. Developing industry-wide standards would improve interoperability between different vendors and simplify the design process. This would also facilitate the development of standardized components and modules.
-
High-Frequency Performance: As operating frequencies increase, the dielectric losses of LTCC materials become more significant. This can impact signal integrity and power efficiency. Research into LTCC materials with lower dielectric loss at high frequencies is crucial for applications such as 5G and microwave circuits.
-
Integration with Active Devices: Integrating active devices (e.g., transistors, ICs) with LTCC substrates can be challenging. Die attachment, wire bonding, and flip-chip assembly techniques need to be optimized for LTCC materials. Thermal management of the active devices also needs careful consideration.
-
Environmental Considerations: The manufacturing of LTCC components can involve the use of hazardous materials. Developing more environmentally friendly processes and materials is important for reducing the environmental impact of LTCC technology. This includes exploring recyclable and biodegradable LTCC materials.
-
Testing and Characterization: Testing and characterizing LTCC components and circuits can be complex, especially at high frequencies. Developing accurate and reliable testing methods is essential for ensuring product quality and performance. This includes techniques for measuring material properties, electrical performance, and thermal characteristics.