Advanced ceramic seals and nylon seals differ significantly in terms of material properties, performance, applications, cost, and manufacturing processes. Below is a detailed comparison:
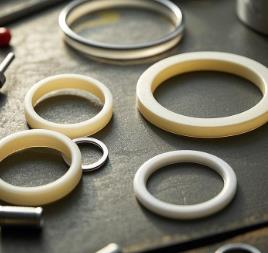
1. Material Properties
- Advanced Ceramic Seals:
- Materials: Typically made from advanced ceramics such as silicon nitride (Si₃N₄), silicon carbide (SiC), or alumina (Al₂O₃).
- Properties: High hardness, excellent wear resistance, superior high-temperature performance, and strong corrosion resistance.
- Nylon Seals:
- Materials: Made from polyamide (PA), commonly known as nylon.
- Properties: Good flexibility, strong impact resistance, and ease of processing, but lower hardness and wear resistance compared to ceramics.
2. Performance
- Advanced Ceramic Seals:
- High-Temperature Resistance: Can operate stably in environments exceeding 1000°C.
- Corrosion Resistance: Highly resistant to acids, alkalis, salts, and other corrosive media.
- Wear Resistance: Extremely high hardness and wear resistance, suitable for high-wear environments.
- Rigidity: High hardness but brittle, with poor impact resistance.
- Nylon Seals:
- Temperature Resistance: Typically suitable for temperatures ranging from -40°C to 120°C; prone to softening at high temperatures.
- Corrosion Resistance: Resistant to general chemical media but vulnerable to strong acids and alkalis.
- Wear Resistance: Good wear resistance but significantly lower than ceramics.
- Flexibility: Excellent elasticity and impact resistance, suitable for dynamic sealing.
3. Applications
- Advanced Ceramic Seals:
- High-Temperature Environments: Aerospace engines, gas turbines, etc.
- Highly Corrosive Environments: Chemical processing equipment, nuclear reactors, etc.
- High-Wear Environments: Pump and valve seals, mechanical seals, etc.
- Nylon Seals:
- General Industrial Environments: Hydraulic systems, pneumatic systems, etc.
- Low-Temperature Environments: Freezing equipment, refrigeration systems, etc.
- Dynamic Sealing: Rotary shaft seals, reciprocating motion seals, etc.
4. Cost and Manufacturing
- Advanced Ceramic Seals:
- Cost: High raw material and processing costs, making them expensive.
- Manufacturing: Complex processing requiring high-precision equipment.
- Nylon Seals:
- Cost: Low raw material and processing costs, making them more affordable.
- Manufacturing: Easy to process and suitable for mass production.
5. Advantages and Disadvantages
- Advanced Ceramic Seals:
- Advantages: High-temperature resistance, corrosion resistance, wear resistance, and long service life.
- Disadvantages: Brittle, poor impact resistance, and high cost.
- Nylon Seals:
- Advantages: Good flexibility, strong impact resistance, low cost, and ease of processing.
- Disadvantages: Limited temperature and corrosion resistance, lower wear resistance.
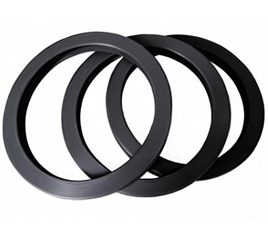
Summary Table:
Comparison of Advanced Ceramic Seals and Nylon Seals
Aspect | Advanced Ceramic Seals | Nylon Seals |
---|---|---|
Material | Silicon nitride (Si₃N₄), silicon carbide (SiC), alumina (Al₂O₃). | Polyamide (PA, nylon). |
Hardness | Very high. | Moderate. |
Wear Resistance | Excellent. | Good, but lower than ceramics. |
Temperature Resistance | Up to 1000°C or higher. | -40°C to 120°C. |
Corrosion Resistance | Resistant to acids, alkalis, and salts. | Resistant to general chemicals but vulnerable to strong acids and alkalis. |
Flexibility | Brittle, poor impact resistance. | Excellent flexibility and impact resistance. |
Cost | High raw material and processing costs. | Low raw material and processing costs. |
Manufacturing | Complex, requires high-precision equipment. | Easy to process, suitable for mass production. |
Applications | High-temperature, corrosive, and high-wear environments (e.g., aerospace, nuclear reactors). | General industrial and low-temperature environments (e.g., hydraulic systems). |
6. Selection Recommendations
- Choose Advanced Ceramic Seals:
- For extreme environments such as high temperatures, strong corrosion, and high wear.
- Applications requiring long-term stability and high reliability.
- Choose Nylon Seals:
- For general industrial environments, especially where flexibility and impact resistance are needed.
- Budget-sensitive applications or large-scale production.
Conclusion
Advanced ceramic seals and nylon seals each have unique advantages and suitable applications. The choice depends on the specific operating environment, performance requirements, and budget. For extreme conditions and high-performance needs, advanced ceramic seals are the better option, while nylon seals are more cost-effective and suitable for general industrial applications.