In the application of large-scale advanced ceramic components, ceramic joining technologies face numerous challenges, primarily due to the inherent properties of ceramic materials and the specific requirements of manufacturing and using large-scale parts. Below are the main challenges and their detailed analyses, followed by a summary table.
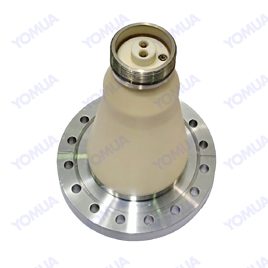
1. Mismatch in Thermal Expansion Coefficients
- Challenge: The significant difference in thermal expansion coefficients between ceramics and metals or other materials can lead to stress concentration in large-scale components during temperature changes, potentially causing cracks or joint failure.
- Solutions:
- Use intermediate layers (e.g., titanium, copper) to mitigate thermal stress.
- Optimize joining processes to control heating and cooling rates.
2. Residual Stress
- Challenge: Large-scale components are prone to residual stress during joining, especially during cooling after high-temperature processes (e.g., brazing, diffusion bonding), which can cause deformation or cracking.
- Solutions:
- Implement stepwise heating and cooling processes.
- Use stress-relief designs (e.g., flexible joint structures).
3. Joining Uniformity
- Challenge: The large joining area of big components makes it difficult to ensure uniformity at the interface, potentially leading to localized weak points or failure.
- Solutions:
- Use automated equipment (e.g., robotic welding) to ensure process consistency.
- Apply segmented joining or multi-point pressure techniques.
4. Process Complexity
- Challenge: The joining process for large-scale components is complex, requiring advanced equipment, tooling, and operations, which increases costs.
- Solutions:
- Develop specialized tooling and equipment to optimize the process.
- Adopt modular designs, breaking down large components into smaller parts for joining and subsequent assembly.
5. Material Cost and Processing Difficulty
- Challenge: The preparation and processing of large-scale ceramic components are costly, and defects (e.g., cracks, pores) are likely to occur during manufacturing.
- Solutions:
- Use near-net-shape technologies (e.g., gel casting, 3D printing) to reduce machining requirements.
- Optimize material formulations to improve ceramic toughness and machinability.
6. Interface Quality Control
- Challenge: It is difficult to comprehensively inspect the joining interface quality of large-scale components, and undetected defects (e.g., pores, incomplete fusion) may exist.
- Solutions:
- Employ non-destructive testing techniques (e.g., ultrasonic testing, X-ray inspection) to evaluate interface quality.
- Develop real-time monitoring systems to ensure process control.
7. Environmental Adaptability
- Challenge: Large-scale components may face complex environments (e.g., high temperature, corrosion, vibration) during service, posing higher reliability requirements for joining technologies.
- Solutions:
- Select joining materials resistant to high temperatures and corrosion (e.g., active brazing alloys, high-performance adhesives).
- Conduct environmental simulation tests to verify long-term reliability.
8. Size Effect
- Challenge: The size effect is significant in large-scale components, leading to differences in heat conduction, stress distribution, and other factors compared to small-scale parts, making traditional processes unsuitable.
- Solutions:
- Develop specialized joining processes for large-scale components.
- Use numerical simulations (e.g., finite element analysis) to optimize process parameters.
9. Cost and Efficiency
- Challenge: The joining process for large-scale components is often time-consuming and costly, making it difficult to meet mass production demands.
- Solutions:
- Optimize process parameters to improve efficiency.
- Develop low-cost, high-efficiency joining technologies (e.g., new brazing materials, fast-curing adhesives).
Summary Table: Challenges and Solutions for Large-Scale Ceramic Joining
Challenge | Description | Solutions |
---|---|---|
Thermal Expansion Mismatch | Differences in thermal expansion coefficients cause stress and cracks. | Use intermediate layers; optimize heating/cooling rates. |
Residual Stress | Stress during cooling leads to deformation or cracking. | Implement stepwise heating/cooling; use stress-relief designs. |
Joining Uniformity | Large joining areas result in inconsistent interface quality. | Use automated equipment; apply segmented joining or multi-point pressure. |
Process Complexity | Complex processes increase costs and require advanced equipment. | Develop specialized tooling; adopt modular designs. |
Material Cost and Processing | High costs and defects during manufacturing. | Use near-net-shape technologies; optimize material formulations. |
Interface Quality Control | Difficult to inspect large interfaces for defects. | Use non-destructive testing; develop real-time monitoring systems. |
Environmental Adaptability | Complex environments demand high reliability. | Select high-temperature/corrosion-resistant materials; conduct environmental simulations. |
Size Effect | Traditional processes are unsuitable for large-scale components. | Develop specialized processes; use numerical simulations. |
Cost and Efficiency | Time-consuming and costly processes hinder mass production. | Optimize process parameters; develop low-cost, high-efficiency technologies. |
Conclusion
Ceramic joining technologies for large-scale components face significant challenges, including thermal expansion mismatch, residual stress, joining uniformity, process complexity, material costs, interface quality control, environmental adaptability, size effects, and cost-efficiency. Addressing these challenges requires a combination of advanced materials, optimized processes, specialized equipment, and rigorous quality control. By leveraging technologies such as numerical simulations, non-destructive testing, and automation, it is possible to achieve high-quality and reliable joining of large-scale ceramic components.