Boron Nitride (h-BN) and Silicon Nitride (Si3N4) are both advanced ceramics known for their unique properties and applications in various industries. Both materials are non-oxide engineering ceramics, which means they do not contain oxygen in their chemical structure, but they possess distinct properties that make them suitable for different applications. Here’s
Here’s a comprehensive comparison of Boron Nitride (BN) ceramics and Silicon Nitride (Si₃N₄) ceramics, covering cost, properties, applications, manufacturing, and future developments:
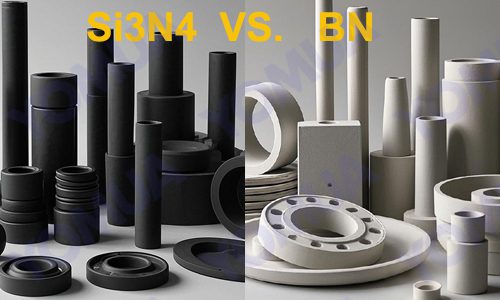
Cost Comparison:
- BN:is generally more expensive than Si₃N₄ due to the higher cost of raw materials and more complex manufacturing processes, especially for high-purity grades and c-BN.The cost of BN can vary significantly depending on the grade, purity, and form (h-BN or c-BN).
- Si₃N₄:is more cost-effective, making it a popular choice for a wider range of applications.
Property Comparison:
1. Structure and Composition:
- BN: Composed of boron and nitrogen, BN exists in several forms. Hexagonal BN (h-BN) has a layered structure similar to graphite, giving it lubricity. Cubic BN (c-BN) has a diamond-like structure, making it extremely hard.
- Si₃N₄: Consists of silicon and nitrogen, featuring strong covalent bonds in its crystalline structure (α and β phases).
2. Mechanical Properties:When comparing mechanical properties such as strength, hardness, toughness, and elastic modulus.
- BN: Generally softer and less strong than Si₃N₄. h-BN is brittle, limiting its use in high-stress applications. c-BN is exceptionally hard, second only to diamond.
- Si₃N₄: Exhibits superior mechanical strength, hardness, and toughness. It’s well-suited for applications requiring wear and impact resistance.
3. Thermal Properties: include thermal conductivity, thermal expansion, and temperature stability
- BN: Excellent thermal conductivity and high-temperature stability. h-BN can withstand very high temperatures in inert atmospheres.
- Si₃N₄: Good thermal stability, but lower thermal conductivity than BN. It can handle thermal gradients well.
4. Electrical Properties: such as volume resistivity and dielectric constant are crucial for electronic applications
- BN: Excellent electrical insulator with low dielectric loss, ideal for electronic insulation.
- Si₃N₄: Also an insulator, but with a higher dielectric constant than BN.
5. Tribological Properties: involve sliding wear resistance and friction.
- BN: Low friction, making h-BN a good lubricant.
- Si₃N₄: Better wear resistance due to its hardness, but potentially higher friction.
6. Chemical Properties:include chemical stability, is resistant to corrosion.
- BN: Chemically inert and resistant to most acids and bases, though strong acids/bases can affect it.
- Si₃N₄: More resistant to oxidation, performing well in high-temperature oxidizing environments.
Property Table :Boron Nitride (h-BN) VS. Silicon Nitride (Si3N4)
Property | Boron Nitride (BN) | Silicon Nitride (Si₃N₄) |
---|---|---|
Structure | Layered (h-BN), Diamond-like (c-BN) | Crystalline |
Hardness | Lower (h-BN), Extremely High (c-BN) | Very High |
Strength | Lower (h-BN), High (c-BN) | Very High |
Thermal Cond. | High | Lower |
Thermal Stability | Very High | High |
Electrical Ins. | Excellent | Good |
Lubricity | Excellent (h-BN) | Lower |
Wear Resistance | Lower (h-BN), High (c-BN) | Very High |
Oxidation Res. | Good | Excellent |
Applications:
- BN:
- High-temperature insulation
- Lubricants
- Coatings for metal processing
- Filler material
- Semiconductor industry (h-BN)
- Cutting tools (c-BN)
- Si₃N₄:
- Bearings
- Cutting tools
- Turbine blades
- Engine components (e.g., cylinder liners, piston rings)
- High-voltage insulators
- Biomedical applications (e.g., artificial bones)
Manufacturing Processes:
- BN: h-BN is typically produced by powder pressing and sintering or hot pressing. c-BN is synthesized under high-pressure, high-temperature conditions, similar to the process for creating synthetic diamonds.
- Si₃N₄: Common manufacturing methods include powder pressing and sintering, reaction bonding, and hot pressing.
Future Developments:
- BN: Research is focused on developing new BN forms with enhanced properties, such as improved mechanical strength and oxidation resistance. There is also a strong emphasis on developing cost-effective manufacturing methods to make BN more accessible for wider applications. The exploration of BN in advanced electronics and thermal management is a key area of focus.
- Si₃N₄: Future developments in Si₃N₄ technology aim to further improve its toughness and reliability. Researchers are also working on developing new Si₃N₄ composites with tailored properties for specific applications. The expansion of Si₃N₄ applications in demanding fields like aerospace and biomedical is expected.
Boron Nitride (BN) vs. Silicon Nitride (Si₃N₄) Ceramics: A Detailed Comparison
Feature | Boron Nitride (BN) | Silicon Nitride (Si₃N₄) |
---|---|---|
Composition | Boron and Nitrogen | Silicon and Nitrogen |
Structure | Hexagonal (h-BN, layered, like graphite), Cubic (c-BN, diamond-like) | Crystalline (α and β phases) |
Key Properties | * High thermal conductivity
* Excellent electrical insulation * Low friction (h-BN) * Extreme hardness (c-BN) * High-temperature stability |
* High strength and toughness
* High hardness and wear resistance * Good thermal shock resistance * High-temperature strength * Chemical resistance |
Cost | Generally more expensive than Si₃N₄, especially for high-purity grades and c-BN | More cost-effective than BN, with a wider range of grades available |
Manufacturing | * h-BN: Powder pressing and sintering, hot pressing
* c-BN: High-pressure, high-temperature synthesis |
Powder pressing and sintering, reaction bonding, hot pressing |
Applications | * h-BN: High-temperature insulation, lubricants, coatings, mold release agents, crucibles, electronics (substrates)
* c-BN: Cutting tools, grinding wheels |
* Cutting tools, wear parts, bearings, seals, engine components (turbine blades, valves), high-performance structural components, electronics (insulators) |
Advantages | * Superior thermal conductivity
* Excellent lubricity (h-BN) * Extreme hardness (c-BN) * High-temperature stability |
* High strength and toughness
* Good wear resistance * More cost-effective |
Disadvantages | * Lower mechanical strength (h-BN)
* High cost * Can be challenging to machine |
* Lower thermal conductivity than BN
* Can be brittle |
Future Developments | * Research on new BN forms with enhanced properties
* Development of cost-effective manufacturing methods * Exploration of BN in advanced electronics and thermal management |
* Improving toughness and reliability
* Developing new Si₃N₄ composites with tailored properties * Expanding applications in aerospace and biomedical fields |
Conclusion:
- BN and Si₃N₄ are both important advanced ceramics with unique strengths.
- BN is superior in thermal conductivity, lubricity (h-BN), and hardness (c-BN), making it ideal for specialized applications.
- Si₃N₄ excels in strength, toughness, and wear resistance, offering a cost-effective solution for a wide range of demanding applications.
- Continued research and development are driving advancements in both materials, leading to new applications and improved performance.