Joining advanced ceramics to plastics is a critical challenge in industries such as electronics, medical devices, aerospace, and automotive. Due to the significant differences in physical, chemical, and mechanical properties (e.g., thermal expansion coefficients, surface energy, and mechanical strength), achieving reliable bonds requires specialized techniques. Below is a comprehensive overview of advanced ceramic-to-plastic joining technologies, including methods, materials, and applications.
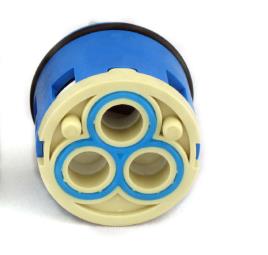
1. Adhesive Bonding
- Process: High-performance adhesives (e.g., epoxy, polyurethane, acrylic) are used to bond ceramics and plastics.
- Materials:
- Adhesives: Epoxy, polyurethane, acrylic.
- Ceramics: Alumina (Al₂O₃), silicon nitride (Si₃N₄), zirconia (ZrO₂).
- Plastics: Polycarbonate (PC), polyether ether ketone (PEEK), polyamide (PA).
- Applications:
- Electronics: Alumina ceramics bonded to polycarbonate for sensor housings.
- Medical devices: Silicon nitride ceramics bonded to PEEK for joint implants.
2. Laser Welding
- Process: A laser beam heats the plastic-ceramic interface, causing the plastic to melt and bond with the ceramic surface.
- Materials:
- Ceramics: Alumina (Al₂O₃), aluminum nitride (AlN).
- Plastics: Polycarbonate (PC), polymethyl methacrylate (PMMA).
- Applications:
- Optical devices: Alumina ceramics laser-welded to PMMA for laser encapsulations.
- Microelectronics: Aluminum nitride ceramics welded to polycarbonate for heat dissipation substrates.
3. Ultrasonic Welding
- Process: High-frequency ultrasonic vibrations locally melt the plastic, bonding it to the ceramic surface.
- Materials:
- Ceramics: Zirconia (ZrO₂), alumina (Al₂O₃).
- Plastics: Polypropylene (PP), polyamide (PA, nylon).
- Applications:
- Automotive: Zirconia ceramics ultrasonically welded to polypropylene for sensor housings.
- Consumer electronics: Alumina ceramics welded to nylon for connector components.
4. Hot Press Bonding
- Process: Heat and pressure are applied to soften the plastic and bond it to the ceramic surface.
- Materials:
- Ceramics: Silicon nitride (Si₃N₄), silicon carbide (SiC).
- Plastics: Polyether ether ketone (PEEK), polyphenylene sulfide (PPS).
- Applications:
- Sensors: Silicon nitride ceramics hot-pressed to PEEK for high-temperature sensors.
- Electronics: Silicon carbide ceramics bonded to PPS for high-power devices.
5. Chemical Bonding
- Process: Chemical treatments create active groups on the ceramic surface, enabling a reaction with the plastic.
- Materials:
- Ceramics: Alumina (Al₂O₃), zirconia (ZrO₂).
- Plastics: Polyimide (PI), polyether ether ketone (PEEK).
- Applications:
- Aerospace: Alumina ceramics chemically bonded to polyimide for high-temperature structural components.
- High-end electronics: Zirconia ceramics bonded to PEEK for high-frequency circuit boards.
6. Intermediate Layer Joining
- Process: An intermediate layer (e.g., metal or polymer film) is added to improve bonding performance.
- Materials:
- Intermediate Layers: Titanium (Ti), copper (Cu), nickel (Ni).
- Ceramics: Aluminum nitride (AlN), alumina (Al₂O₃).
- Plastics: Polyether ether ketone (PEEK), polytetrafluoroethylene (PTFE).
- Applications:
- High-reliability packaging: Aluminum nitride ceramics joined to PEEK via titanium interlayers for high-power LEDs.
- Optical devices: Alumina ceramics bonded to PTFE via copper interlayers for laser components.
7. 3D Printing Integrated Fabrication
- Process: Ceramic and plastic materials are deposited layer-by-layer using 3D printing technology.
- Materials:
- Ceramics: Zirconia (ZrO₂), hydroxyapatite (HA, bioceramics).
- Plastics: Polylactic acid (PLA), polyether ether ketone (PEEK).
- Applications:
- Medical devices: Hydroxyapatite ceramics integrated with PLA for bone repair implants.
- Aerospace: Zirconia ceramics integrated with PEEK for lightweight structural components.
8. Mechanical Joining
- Process: Mechanical structures (e.g., screws, clips, rivets) are used to join ceramics and plastics.
- Materials:
- Ceramics: Silicon carbide (SiC), alumina (Al₂O₃).
- Plastics: Polyamide (PA, nylon), polycarbonate (PC).
- Applications:
- Industrial equipment: Silicon carbide ceramics mechanically joined to nylon for wear-resistant parts.
- Household appliances: Alumina ceramics joined to polycarbonate via clips for heating element housings.
Comparison Table of Ceramic-to-Plastic Joining Technologies
Technology | Materials | Applications | Key Advantages |
---|---|---|---|
Adhesive Bonding | Epoxy, polyurethane, acrylic; Al₂O₃, Si₃N₄, ZrO₂; PC, PEEK, PA. | Electronics, medical devices. | Simple, low-cost, suitable for complex shapes. |
Laser Welding | Al₂O₃, AlN; PC, PMMA. | Optical devices, microelectronics. | High precision, small heat-affected zone. |
Ultrasonic Welding | ZrO₂, Al₂O₃; PP, PA. | Automotive, consumer electronics. | Fast, efficient, no additional materials required. |
Hot Press Bonding | Si₃N₄, SiC; PEEK, PPS. | Sensors, high-power electronics. | High bond strength, suitable for high-temperature applications. |
Chemical Bonding | Al₂O₃, ZrO₂; PI, PEEK. | Aerospace, high-end electronics. | High durability, excellent for high-performance applications. |
Intermediate Layer | Ti, Cu, Ni; AlN, Al₂O₃; PEEK, PTFE. | High-reliability packaging, optical devices. | Reduces thermal mismatch, improves bond strength. |
3D Printing | ZrO₂, HA; PLA, PEEK. | Medical devices, aerospace. | Design flexibility, integrated fabrication. |
Mechanical Joining | SiC, Al₂O₃; PA, PC. | Industrial equipment, household appliances. | No chemical bonding, suitable for high-temperature or corrosive environments. |
Conclusion
Advanced ceramic-to-plastic joining technologies offer diverse solutions for various industrial applications. The choice of method depends on material compatibility, performance requirements, and specific use cases. For example:
- Adhesive bonding and mechanical joining are cost-effective and versatile.
- Laser welding and ultrasonic welding are ideal for high-precision and mass production.
- Hot press bonding, chemical bonding, and intermediate layer joining are suitable for high-performance and high-temperature environments.
- 3D printing enables innovative designs and integrated fabrication.
By selecting the appropriate technology and materials, industries can achieve reliable and durable ceramic-to-plastic bonds, unlocking new possibilities in advanced manufacturing.