Joining Al2O3 (alumina) ceramics with metals is a common requirement in industries such as electronics, aerospace, and energy, where the combination of ceramic properties (e.g., electrical insulation, thermal stability) and metal properties (e.g., ductility, conductivity) is needed. However, the process is challenging due to differences in thermal expansion coefficients, bonding mechanisms, and mechanical properties. Below are the primary methods used to join Al₂O₃ ceramics with metals, along with their advantages, limitations, and applications:
1. Active Metal Brazing(AMB)
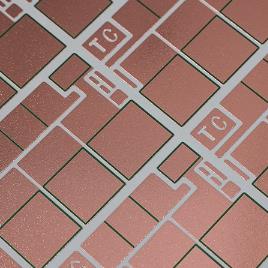
Active metal brazing is one of the most widely used methods for joining Al₂O₃ ceramics to metals.
Process:
- A filler metal (braze alloy) containing active elements like titanium, zirconium, or hafnium is used.
- The active elements react with the ceramic surface, forming a strong chemical bond.
- Common braze alloys include Ag-Cu-Ti or Cu-Ti.
Advantages:
- Strong and reliable joints.
- Suitable for high-temperature applications.
- Can join complex shapes.
Limitations:
- Requires precise control of temperature and atmosphere (often performed in a vacuum or inert gas).
- Surface preparation (e.g., cleaning, polishing) is critical.
Applications:
- Electronics: Joining Al₂O₃ substrates to metal heat sinks or packages.
- Aerospace: Ceramic-metal components for high-temperature environments.
- Energy: Fuel cells and power electronics.
2. Diffusion Bonding

Diffusion bonding involves joining Al₂O₃ ceramics and metals through atomic diffusion at high temperatures and pressures.
Process:
- The ceramic and metal surfaces are brought into close contact under high pressure and elevated temperature.
- An interlayer (e.g., titanium, nickel, or aluminum) is often used to improve bonding.
Advantages:
- Creates joints with high mechanical strength.
- No filler material is required, reducing contamination risks.
Limitations:
- Requires high temperatures and pressures, making it energy-intensive.
- Limited to simple geometries due to the need for uniform pressure.
Applications:
- High-strength components in aerospace and nuclear industries.
- Joining Al₂O₃ insulators to metal electrodes in sensors.
3. Adhesive Bonding
Adhesive bonding uses high-temperature adhesives to join Al₂O₃ ceramics and metals.
Process:
- A polymer-based adhesive (e.g., epoxy, silicone, or polyimide) is applied to the surfaces.
- The adhesive cures at room temperature or elevated temperatures, depending on the formulation.
Advantages:
- Simple and cost-effective.
- Suitable for low-stress applications and complex shapes.
Limitations:
- Limited thermal and mechanical performance.
- Not suitable for high-temperature or high-stress environments.
Applications:
- Electronics: Mounting Al₂O₃ substrates to metal housings.
- Medical devices: Joining ceramic components to metal frames.
4. Mechanical Fastening
Mechanical fastening uses screws, bolts, or clamps to join Al₂O₃ ceramics and metals.
Process:
- Holes are drilled or machined into the ceramic and metal parts.
- Fasteners are used to hold the components together, often with gaskets or spacers to reduce stress.
Advantages:
- No high temperatures or special equipment required.
- Easy to disassemble and reassemble.
Limitations:
- Stress concentrations at fastener points can lead to ceramic cracking.
- Limited to low-stress applications.
Applications:
- Industrial machinery: Joining ceramic insulators to metal frames.
- Laboratory equipment: Assembling ceramic and metal components.
5. Metallization and Soldering
Metallization involves coating the Al₂O₃ ceramic surface with a metal layer, followed by soldering to join it to a metal part.
Process:
- The ceramic surface is coated with a thin metal layer (e.g., molybdenum-manganese or tungsten) using techniques like screen printing or sputtering.
- The metallized ceramic is then soldered to the metal part using a low-melting-point solder (e.g., tin-lead or silver-based alloys).
Advantages:
- Provides good electrical and thermal conductivity.
- Suitable for moderate-temperature applications.
Limitations:
- Requires precise control of metallization and soldering processes.
- Limited to applications where high mechanical strength is not critical.
Applications:
- Electronics: Joining Al₂O₃ substrates to metal leads or connectors.
- Sensors: Integrating ceramic sensors with metal housings.
6. Direct Bonding (Glass Sealing)
Direct bonding uses a glass intermediate layer to join Al₂O₃ ceramics and metals.
Process:
- A glass powder or preform is placed between the ceramic and metal surfaces.
- The assembly is heated to melt the glass, which then bonds to both materials upon cooling.
Advantages:
- Provides hermetic seals.
- Suitable for high-temperature and vacuum applications.
Limitations:
- Limited by the thermal expansion mismatch between the glass, ceramic, and metal.
- Requires careful selection of glass composition.
Applications:
- Vacuum systems: Sealing ceramic windows to metal flanges.
- Lighting: Joining ceramic envelopes to metal bases in lamps.
Here’s a table summarizing the methods for joining Al₂O₃ ceramics with metals, along with their key characteristics, advantages, limitations, and applications:
Method | Process | Advantages | Limitations | Applications |
---|---|---|---|---|
Active Metal Brazing | Uses filler metals (e.g., Ag-Cu-Ti) with active elements to bond Al₂O₃ and metals. | Strong, reliable joints; suitable for high temperatures. | Requires vacuum/inert atmosphere; precise temperature control. | Electronics, aerospace, energy (e.g., heat sinks, fuel cells). |
Diffusion Bonding | Joins materials through atomic diffusion under high temperature and pressure. | High mechanical strength; no filler material. | Energy-intensive; limited to simple geometries. | Aerospace, nuclear, sensors. |
Adhesive Bonding | Uses high-temperature adhesives (e.g., epoxy, silicone) to bond materials. | Simple, cost-effective; suitable for complex shapes. | Limited thermal/mechanical performance; not for high-stress environments. | Electronics, medical devices. |
Mechanical Fastening | Uses screws, bolts, or clamps to join Al₂O₃ and metals. | Easy to disassemble; no high temperatures required. | Stress concentrations can crack ceramics; limited to low-stress applications. | Industrial machinery, laboratory equipment. |
Metallization + Soldering | Coats Al₂O₃ with a metal layer (e.g., Mo-Mn) and solders to metal. | Good electrical/thermal conductivity; moderate-temperature applications. | Requires precise metallization; limited mechanical strength. | Electronics, sensors. |
Direct Bonding (Glass Sealing) | Uses a glass intermediate layer to bond Al₂O₃ and metals. | Hermetic seals; suitable for high-temperature/vacuum applications. | Thermal expansion mismatch; careful glass selection required. | Vacuum systems, lighting (e.g., lamps). |
Key Takeaways
- Active Metal Brazing and Diffusion Bonding are ideal for high-strength, high-temperature applications.
- Adhesive Bonding and Mechanical Fastening are simpler and cost-effective but limited to low-stress environments.
- Metallization + Soldering and Glass Sealing are suitable for specific applications requiring electrical conductivity or hermetic seals.
This table provides a quick reference to help you choose the appropriate joining method based on your application requirements.
7. Challenges in Joining Al2O3 Ceramics with Metals
- Thermal Expansion Mismatch: Al₂O₃ and metals have different coefficients of thermal expansion, leading to stress and potential failure during thermal cycling.
- Brittleness of Ceramics: Al₂O₃ is brittle and prone to cracking under stress, requiring careful design of joints.
- Surface Preparation: Proper cleaning, polishing, and surface activation are critical for achieving strong bonds.
- High-Temperature Requirements: Many joining methods require high temperatures, which can limit material choices and increase costs.
Conclusion
In conclusion, joining Al2O3 (alumina) ceramics with metals is a critical process in many advanced industries, including electronics, aerospace, energy, and medical devices. While the inherent differences in thermal, mechanical, and chemical properties between ceramics and metals make the joining process challenging, several effective methods have been developed to address these challenges:
- Active Metal Brazing: Ideal for high-strength, high-temperature applications, offering reliable and durable joints.
- Diffusion Bonding: Provides excellent mechanical strength but requires high temperatures and pressures, making it suitable for specialized applications.
- Adhesive Bonding: A simple and cost-effective solution for low-stress applications, though limited by thermal and mechanical performance.
- Mechanical Fastening: Easy to implement and disassemble but limited to low-stress environments due to the risk of ceramic cracking.
- Metallization and Soldering: Offers good electrical and thermal conductivity, making it suitable for electronics and sensors.
- Direct Bonding (Glass Sealing): Provides hermetic seals and is ideal for high-temperature or vacuum applications.
Each method has its own advantages and limitations, and the choice depends on factors such as the application’s mechanical, thermal, and electrical requirements, as well as cost and production constraints. Proper surface preparation, joint design, and process control are essential to ensure strong, reliable, and durable bonds.
By carefully selecting the appropriate joining method and optimizing the process, Al₂O₃ ceramics can be effectively integrated with metals, enabling the development of advanced components and systems that leverage the unique properties of both materials. This integration is key to advancing technologies in fields ranging from renewable energy and aerospace to electronics and healthcare.