Silicon Nitride (Si3N4) ceramics are widely recognized for their excellent mechanical properties, thermal stability, and resistance to wear and corrosion. However, like any advanced material, they face several challenges that need to be addressed to optimize their performance and expand their applications. Below are the key issues and potential solutions:
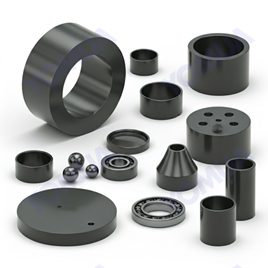
1. High Production Costs
Issue: The synthesis of high-purity Si₃N₄ powder and the sintering process are expensive, limiting its widespread use.
Solutions:
- Develop cost-effective synthesis methods, such as direct nitridation of silicon or carbothermal reduction.
- Optimize sintering techniques (e.g., pressureless sintering or spark plasma sintering) to reduce energy consumption.
- Use sintering aids (e.g., Y₂O₃, MgO, or Al₂O₃) to lower sintering temperatures.
2. Difficulty in Achieving Full Density
Issue: Achieving fully dense Si₃N₄ ceramics without defects is challenging due to its high sintering temperature and low self-diffusion coefficient.
Solutions:
- Use advanced sintering techniques like hot isostatic pressing (HIP) or gas pressure sintering.
- Optimize the particle size distribution and green body formation to improve densification.
- Incorporate sintering aids to promote liquid-phase sintering.
3. Mechanical Brittleness
Issue: Despite their high strength, Si₃N₄ ceramics are inherently brittle, which limits their use in applications requiring high fracture toughness.
Solutions:
- Develop Si₃N₄-based composites by adding reinforcing phases (e.g., SiC, TiC, or graphene).
- Use grain boundary engineering to enhance crack resistance.
- Explore nanostructured Si₃N₄ materials for improved toughness.
4. Limited High-Temperature Stability
Issue: Si₃N₄ ceramics can degrade at very high temperatures (above 1200°C) due to oxidation and decomposition.
Solutions:
- Apply protective coatings (e.g., SiC or Al₂O₃) to prevent oxidation.
- Use Si₃N₄ in composite forms with other high-temperature materials (e.g., ZrO₂ or AlN).
- Optimize the microstructure to minimize grain boundary oxidation.
5. Challenges in Machining and Shaping
Issue: Si₃N₄ ceramics are hard and brittle, making them difficult to machine or shape into complex geometries without causing cracks or defects.
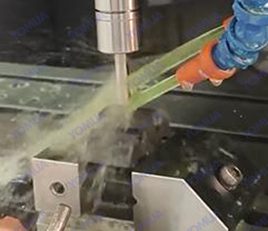
Solutions:
- Use advanced machining techniques such as laser cutting, ultrasonic machining, or electrical discharge machining (EDM).
- Employ near-net-shape manufacturing methods like gel casting or injection molding.
- Develop diamond-based tools specifically designed for machining Si₃N₄ ceramics.
6. Sensitivity to Thermal Shock
Issue: Si₃N₄ ceramics can experience thermal shock failure under rapid temperature changes due to their high thermal expansion coefficient.
Solutions:
- Design components with optimized geometries to reduce stress concentrations.
- Use Si₃N₄ composites with tailored thermal expansion properties.
- Develop graded materials to mitigate thermal stress.
7. Limited Electrical Conductivity Control
Issue: Si₃N₄ is an electrical insulator, which limits its use in applications requiring controlled electrical conductivity.
Solutions:
- Dope Si₃N₄ with specific elements (e.g., Al, O, or rare earth metals) to tailor its electrical properties.
- Explore Si₃N₄-based heterostructures or multilayers for advanced electronic applications.
- Investigate the use of Si₃N₄ in combination with conductive materials (e.g., metals or graphene).
8. Environmental Degradation in Harsh Conditions
Issue: Si₃N₄ ceramics can degrade in harsh environments, such as acidic or alkaline conditions, limiting their use in chemical processing or marine applications.
Solutions:
- Develop chemically resistant coatings or surface modifications.
- Use Si₃N₄ in composite forms with chemically stable materials (e.g., SiC or Al₂O₃).
- Optimize the microstructure to reduce susceptibility to chemical attack.
9. Challenges in Additive Manufacturing
Issue: Additive manufacturing (3D printing) of Si₃N₄ ceramics is still in its infancy, with issues related to powder flowability, binder systems, and sintering.
Solutions:
- Develop specialized Si₃N₄ powders with optimized particle size and morphology.
- Use advanced binder systems and debinding techniques to minimize defects.
- Explore new 3D printing technologies (e.g., stereolithography or selective laser sintering).
10. Limited Data on Long-Term Performance
Issue: There is insufficient data on the long-term performance of Si₃N₄ ceramics in real-world applications, which hinders their adoption in critical industries.
Solutions:
- Conduct extensive reliability testing under simulated operating conditions.
- Collaborate with industry partners to gather field data on Si₃N₄ performance.
- Develop predictive models to assess long-term behavior based on accelerated aging tests.
11. Joining and Integration Challenges
Issue: Joining Si₃N₄ ceramics to other materials (e.g., metals or polymers) is difficult due to differences in thermal expansion coefficients and chemical compatibility.
Solutions:
- Develop compatible interlayers or brazing materials for joining Si₃N₄ to metals.
- Use advanced bonding techniques such as diffusion bonding or laser welding.
- Design graded interfaces to mitigate thermal stress during joining.
12. Recycling and Reuse Challenges
Issue: Recycling Si₃N₄ ceramics is difficult due to their chemical stability and high processing temperatures.
Solutions:
- Develop methods to recover and reuse Si₃N₄ powder from waste materials.
- Explore chemical recycling techniques to break down Si₃N₄ into reusable precursors.
- Design Si₃N₄ components for easier disassembly and recycling at the end of their lifecycle.
13. Regulatory and Standardization Gaps
Issue: The lack of standardized testing methods and regulatory guidelines for Si₃N₄ ceramics can hinder their adoption in regulated industries (e.g., medical or aerospace).
Solutions:
- Work with standardization organizations to develop testing protocols and material specifications.
- Collaborate with regulatory bodies to establish guidelines for Si₃N₄ use in critical applications.
- Promote industry-wide adoption of best practices for Si₃N₄ processing and quality control.
14. Limited Awareness and Adoption in Emerging Applications
Issue: Despite its excellent properties, Si₃N₄ is underutilized in emerging fields like renewable energy, biomedical devices, and advanced electronics due to limited awareness and high costs.
Solutions:
- Increase awareness through industry conferences, publications, and collaborations.
- Demonstrate the cost-effectiveness and performance benefits of Si₃N₄ in specific applications.
- Partner with end-users to develop tailored solutions for emerging technologies.
15. Challenges in Large-Scale Production of Single Crystals
Issue: Producing high-quality single-crystal Si₃N₄ for specialized applications (e.g., optoelectronics) is complex and costly.
Solutions:
- Develop advanced crystal growth techniques such as chemical vapor deposition (CVD) or physical vapor transport (PVT).
- Optimize growth conditions (e.g., temperature, pressure, and precursor purity) to minimize defects.
- Collaborate with research institutions to scale up single-crystal production.
Comprehensive Table:
Here’s a comprehensive table summarizing the issues related to Silicon Nitride (Si₃N₄) ceramics and their corresponding solutions:
Table: Issues and Solutions for Silicon Nitride (Si3N4) Ceramics
Issue | Solutions |
---|---|
1. High Production Costs | – Develop cost-effective synthesis methods (e.g., direct nitridation or carbothermal reduction). – Optimize sintering techniques. – Use sintering aids to lower processing temperatures. |
2. Difficulty in Achieving Full Density | – Use advanced sintering techniques (e.g., hot isostatic pressing or gas pressure sintering). – Optimize particle size distribution and green body formation. – Incorporate sintering aids. |
3. Mechanical Brittleness | – Develop Si₃N₄-based composites with reinforcing phases (e.g., SiC or graphene). – Use grain boundary engineering. – Explore nanostructured Si₃N₄ materials. |
4. Limited High-Temperature Stability | – Apply protective coatings (e.g., SiC or Al₂O₃). – Use Si₃N₄ in composite forms with high-temperature materials. – Optimize microstructure to minimize oxidation. |
5. Challenges in Machining and Shaping | – Use advanced machining techniques (e.g., laser cutting or ultrasonic machining). – Employ near-net-shape manufacturing methods. – Develop diamond-based tools for machining. |
6. Sensitivity to Thermal Shock | – Design components with optimized geometries. – Use Si₃N₄ composites with tailored thermal expansion properties. – Develop graded materials to mitigate thermal stress. |
7. Limited Electrical Conductivity Control | – Dope Si₃N₄ with specific elements (e.g., Al or rare earth metals). – Explore Si₃N₄-based heterostructures. – Investigate hybrid materials (e.g., Si₃N₄ with conductive phases). |
8. Environmental Degradation in Harsh Conditions | – Develop chemically resistant coatings. – Use Si₃N₄ in composite forms with chemically stable materials. – Optimize microstructure to reduce susceptibility to chemical attack. |
9. Challenges in Additive Manufacturing | – Develop specialized Si₃N₄ powders for 3D printing. – Use advanced binder systems and debinding techniques. – Explore new 3D printing technologies (e.g., stereolithography). |
10. Limited Data on Long-Term Performance | – Conduct extensive reliability testing. – Collaborate with industry partners for field data. – Develop predictive models for long-term behavior. |
11. Joining and Integration Challenges | – Develop compatible interlayers or brazing materials. – Use advanced bonding techniques (e.g., diffusion bonding). – Design graded interfaces to reduce thermal stress. |
12. Recycling and Reuse Challenges | – Develop methods to recover and reuse Si₃N₄ powder. – Explore chemical recycling techniques. – Design Si₃N₄ components for easier disassembly and recycling. |
13. Regulatory and Standardization Gaps | – Work with standardization organizations to develop testing protocols. – Collaborate with regulatory bodies for guidelines. – Promote industry-wide adoption of best practices. |
14. Limited Awareness and Adoption in Emerging Applications | – Increase awareness through conferences and publications. – Demonstrate cost-effectiveness and performance benefits. – Partner with end-users for tailored solutions. |
15. Challenges in Large-Scale Production of Single Crystals | – Develop advanced crystal growth techniques (e.g., CVD or PVT). – Optimize growth conditions. – Collaborate with research institutions to scale up production. |
Conclusion
Silicon Nitride (Si3N4) ceramics are a highly versatile material with exceptional mechanical, thermal, and chemical properties, making them suitable for demanding applications in industries such as aerospace, automotive, electronics, and biomedical engineering. However, several challenges—including high production costs, brittleness, sensitivity to thermal shock, and difficulties in machining and integration—must be addressed to fully unlock their potential.
By leveraging advanced manufacturing techniques, material innovations, and collaborative research efforts, many of these challenges can be overcome. Solutions such as:
- Developing cost-effective synthesis and sintering methods.
- Enhancing toughness through composite materials and nanostructuring.
- Improving thermal and chemical stability with protective coatings.
- Advancing additive manufacturing and recycling technologies.
will play a critical role in expanding the use of Si₃N₄ ceramics.
Furthermore, addressing regulatory gaps, increasing awareness of Si₃N₄’s benefits, and gathering long-term performance data will help drive its adoption in emerging applications like renewable energy, 5G technology, and advanced electronics.
In conclusion, continued innovation and investment in Si₃N₄ ceramics will enable their widespread use in both traditional and cutting-edge applications, solidifying their position as a key material for the future of high-performance engineering.