Aluminum Nitride (AlN) ceramics are highly valued for their excellent thermal conductivity, electrical insulation, and mechanical properties. However, several challenges need to be addressed to optimize their performance and broaden their applications. Below are the key issues and potential solutions:
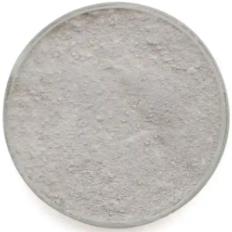
1. High Cost of Raw Materials and Processing
Issue: The production of high-purity AlN powder and the sintering process are expensive, limiting its widespread use.
Solutions:
- Develop cost-effective synthesis methods for AlN powder, such as carbothermal reduction or direct nitridation of aluminum.
- Optimize sintering techniques (e.g., pressureless sintering or spark plasma sintering) to reduce energy consumption and processing time.
- Explore the use of additives to lower sintering temperatures while maintaining material properties.
2. Sensitivity to Moisture
Issue: AlN is prone to hydrolysis in the presence of moisture, forming aluminum hydroxide and ammonia, which degrades its properties.
Solutions:
- Coat AlN surfaces with moisture-resistant materials (e.g., thin films of SiO₂ or Al₂O₃).
- Store and handle AlN in dry environments or under inert atmospheres.
- Develop AlN composites with hydrophobic additives to reduce moisture absorption.
3. Difficulty in Achieving High Density
Issue: Achieving fully dense AlN ceramics without defects is challenging due to its high sintering temperature and low self-diffusion coefficient.
Solutions:
- Use sintering aids like Y₂O₃ or CaO to promote densification at lower temperatures.
- Employ advanced sintering techniques such as hot pressing or spark plasma sintering to achieve high density.
- Optimize particle size distribution and powder processing to improve green body density.
4. Thermal Conductivity Degradation
Issue: Impurities, oxygen content, and lattice defects can significantly reduce the thermal conductivity of AlN.
Solutions:
- Use high-purity raw materials and minimize oxygen contamination during processing.
- Optimize sintering conditions to reduce oxygen content and enhance grain boundary purity.
- Post-process treatments (e.g., annealing) to improve crystallinity and reduce defects.
5. Mechanical Brittleness
Issue: AlN ceramics are inherently brittle, which limits their use in applications requiring high fracture toughness.
Solutions:
- Develop AlN-based composites by incorporating reinforcing phases (e.g., SiC, TiC, or graphene) to improve toughness.
- Use grain boundary engineering to enhance crack resistance.
- Explore nanostructured AlN materials for improved mechanical properties.
6. Joining and Integration Challenges
Issue: Joining AlN ceramics to other materials (e.g., metals or polymers) is difficult due to differences in thermal expansion coefficients and chemical compatibility.
Solutions:
- Develop compatible interlayers or brazing materials for joining AlN to metals.
- Use advanced bonding techniques such as diffusion bonding or laser welding.
- Design graded interfaces to mitigate thermal stress during joining.
7. Limited Scalability for Industrial Applications
Issue: Scaling up the production of high-quality AlN ceramics while maintaining consistency is challenging.
Solutions:
- Standardize manufacturing processes and quality control measures.
- Invest in automation and advanced manufacturing technologies to improve scalability.
- Collaborate with industry partners to optimize production workflows.
8. Environmental and Health Concerns
Issue: The production and processing of AlN involve hazardous chemicals and high energy consumption, raising environmental and health concerns.
Solutions:
- Develop greener synthesis methods with lower environmental impact.
- Implement waste recycling and energy recovery systems in production facilities.
- Ensure proper handling and disposal of AlN powders to minimize health risks.
9. Limited High-Temperature Stability
Issue: While AlN has good thermal stability, its performance can degrade at very high temperatures (above 1300°C) due to oxidation and decomposition.
Solutions:
- Develop protective coatings (e.g., SiC or Al₂O₃) to prevent oxidation at elevated temperatures.
- Use AlN in composite forms with other high-temperature materials (e.g., Si₃N₄ or ZrO₂) to enhance stability.
- Optimize the microstructure to minimize grain boundary oxidation.
10. Challenges in Machining and Shaping
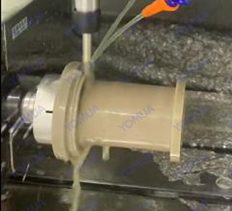
Issue: AlN ceramics are hard and brittle, making them difficult to machine or shape into complex geometries without causing cracks or defects.
Solutions:
- Use advanced machining techniques such as laser cutting, ultrasonic machining, or electrical discharge machining (EDM).
- Employ near-net-shape manufacturing methods like gel casting or injection molding to reduce the need for extensive machining.
- Develop diamond-based tools specifically designed for machining AlN ceramics.
11. Inconsistent Thermal Conductivity
Issue: The thermal conductivity of AlN can vary significantly depending on the purity, grain size, and processing conditions.
Solutions:
- Standardize the synthesis and sintering processes to ensure consistent material properties.
- Use advanced characterization techniques (e.g., TEM, XRD) to monitor and control microstructural features that affect thermal conductivity.
- Optimize the grain size and orientation to maximize phonon transport.
12. Compatibility with Thin-Film Technologies
Issue: Integrating AlN ceramics into thin-film applications (e.g., MEMS, sensors) is challenging due to stress and adhesion issues.
Solutions:
- Develop stress-relief layers or buffer layers to improve adhesion and reduce thermal mismatch.
- Use advanced deposition techniques like atomic layer deposition (ALD) or magnetron sputtering for precise control of thin-film properties.
- Optimize surface treatments (e.g., plasma etching) to enhance bonding with thin films.
13. Limited Electrical Conductivity Control
Issue: While AlN is an excellent electrical insulator, controlling its electrical properties for specific applications (e.g., semiconductors) is difficult.
Solutions:
- Dope AlN with specific elements (e.g., Si, Mg, or rare earth metals) to tailor its electrical properties.
- Explore AlN-based heterostructures or multilayers for advanced electronic applications.
- Investigate the use of AlN in combination with other materials (e.g., GaN) for hybrid devices.
14. Challenges in Large-Scale Production of Single Crystals
Issue: Producing high-quality single-crystal AlN for optoelectronic and piezoelectric applications is complex and costly.
Solutions:
- Develop advanced crystal growth techniques such as physical vapor transport (PVT) or hydride vapor phase epitaxy (HVPE).
- Optimize growth conditions (e.g., temperature, pressure, and precursor purity) to minimize defects.
- Collaborate with research institutions to scale up single-crystal production.
15. Limited Awareness and Adoption in Emerging Applications
Issue: Despite its excellent properties, AlN is underutilized in emerging fields like 5G, IoT, and renewable energy due to limited awareness and high costs.
Solutions:
- Increase awareness through industry conferences, publications, and collaborations.
- Demonstrate the cost-effectiveness and performance benefits of AlN in specific applications.
- Partner with end-users to develop tailored solutions for emerging technologies.
16. Environmental Degradation in Harsh Conditions
Issue: AlN ceramics can degrade in harsh environments, such as acidic or alkaline conditions, limiting their use in chemical processing or marine applications.
Solutions:
- Develop chemically resistant coatings or surface modifications to protect AlN in corrosive environments.
- Use AlN in composite forms with chemically stable materials (e.g., SiC or Al₂O₃).
- Optimize the microstructure to reduce susceptibility to chemical attack.
17. Challenges in Recycling and Reuse
Issue: Recycling AlN ceramics is difficult due to their chemical stability and high processing temperatures.
Solutions:
- Develop methods to recover and reuse AlN powder from waste materials.
- Explore chemical recycling techniques to break down AlN into reusable precursors.
- Design AlN components for easier disassembly and recycling at the end of their lifecycle.
18. Limited Data on Long-Term Performance
Issue: There is insufficient data on the long-term performance of AlN ceramics in real-world applications, which hinders their adoption in critical industries.
Solutions:
- Conduct extensive reliability testing under simulated operating conditions.
- Collaborate with industry partners to gather field data on AlN performance.
- Develop predictive models to assess long-term behavior based on accelerated aging tests.
19. Challenges in Additive Manufacturing
Issue: Additive manufacturing (3D printing) of AlN ceramics is still in its infancy, with issues related to powder flowability, binder systems, and sintering.
Solutions:
- Develop specialized AlN powders with optimized particle size and morphology for additive manufacturing.
- Use advanced binder systems and debinding techniques to minimize defects.
- Explore new 3D printing technologies (e.g., stereolithography or selective laser sintering) for AlN ceramics.
20. Regulatory and Standardization Gaps
Issue: The lack of standardized testing methods and regulatory guidelines for AlN ceramics can hinder their adoption in regulated industries (e.g., medical or aerospace).
Solutions:
- Work with standardization organizations to develop testing protocols and material specifications for AlN.
- Collaborate with regulatory bodies to establish guidelines for AlN use in critical applications.
- Promote industry-wide adoption of best practices for AlN processing and quality control.
Comprehensive Table
Here’s a comprehensive table summarizing all the issues related to Aluminum Nitride (AlN) ceramics and their corresponding solutions:
Issue | Solutions |
---|---|
1. High Cost of Raw Materials and Processing | – Develop cost-effective synthesis methods (e.g., carbothermal reduction). – Optimize sintering techniques (e.g., pressureless sintering). – Use sintering aids to lower processing temperatures. |
2. Sensitivity to Moisture | – Apply moisture-resistant coatings (e.g., SiO₂ or Al₂O₃). – Store and handle AlN in dry environments. – Develop hydrophobic AlN composites. |
3. Difficulty in Achieving High Density | – Use sintering aids (e.g., Y₂O₃ or CaO). – Employ advanced sintering techniques (e.g., hot pressing or spark plasma sintering). – Optimize powder processing for better green body density. |
4. Thermal Conductivity Degradation | – Use high-purity raw materials. – Optimize sintering to reduce oxygen content. – Post-process treatments (e.g., annealing) to improve crystallinity. |
5. Mechanical Brittleness | – Develop AlN composites with reinforcing phases (e.g., SiC or graphene). – Use grain boundary engineering. – Explore nanostructured AlN materials. |
6. Joining and Integration Challenges | – Develop compatible interlayers or brazing materials. – Use advanced bonding techniques (e.g., diffusion bonding). – Design graded interfaces to reduce thermal stress. |
7. Limited Scalability for Industrial Applications | – Standardize manufacturing processes. – Invest in automation and advanced manufacturing technologies. – Collaborate with industry partners. |
8. Environmental and Health Concerns | – Develop greener synthesis methods. – Implement waste recycling and energy recovery systems. – Ensure proper handling and disposal of AlN powders. |
9. Limited High-Temperature Stability | – Apply protective coatings (e.g., SiC or Al₂O₃). – Use AlN in composite forms with high-temperature materials. – Optimize microstructure to minimize oxidation. |
10. Challenges in Machining and Shaping | – Use advanced machining techniques (e.g., laser cutting or ultrasonic machining). – Employ near-net-shape manufacturing methods. – Develop diamond-based tools for machining. |
11. Inconsistent Thermal Conductivity | – Standardize synthesis and sintering processes. – Use advanced characterization techniques to monitor microstructure. – Optimize grain size and orientation. |
12. Compatibility with Thin-Film Technologies | – Develop stress-relief or buffer layers. – Use advanced deposition techniques (e.g., ALD or sputtering). – Optimize surface treatments for better adhesion. |
13. Limited Electrical Conductivity Control | – Dope AlN with specific elements (e.g., Si or Mg). – Explore AlN-based heterostructures. – Investigate hybrid materials (e.g., AlN-GaN). |
14. Challenges in Large-Scale Production of Single Crystals | – Develop advanced crystal growth techniques (e.g., PVT or HVPE). – Optimize growth conditions. – Collaborate with research institutions for scaling up production. |
15. Limited Awareness and Adoption in Emerging Applications | – Increase awareness through conferences and publications. – Demonstrate cost-effectiveness and performance benefits. – Partner with end-users for tailored solutions. |
16. Environmental Degradation in Harsh Conditions | – Develop chemically resistant coatings. – Use AlN in composite forms with chemically stable materials. – Optimize microstructure to reduce susceptibility to chemical attack. |
17. Challenges in Recycling and Reuse | – Develop methods to recover and reuse AlN powder. – Explore chemical recycling techniques. – Design AlN components for easier disassembly and recycling. |
18. Limited Data on Long-Term Performance | – Conduct extensive reliability testing. – Collaborate with industry partners for field data. – Develop predictive models for long-term behavior. |
19. Challenges in Additive Manufacturing | – Develop specialized AlN powders for 3D printing. – Use advanced binder systems and debinding techniques. – Explore new 3D printing technologies (e.g., stereolithography). |
20. Regulatory and Standardization Gaps | – Work with standardization organizations to develop testing protocols. – Collaborate with regulatory bodies for guidelines. – Promote industry-wide adoption of best practices. |
Conclusion
Aluminum Nitride (AlN) ceramics are a highly promising material due to their exceptional thermal conductivity, electrical insulation, mechanical strength, and stability at high temperatures. These properties make them ideal for a wide range of applications, including electronics, aerospace, automotive, and renewable energy. However, several challenges must be addressed to fully realize their potential and enable broader adoption.
The key issues include:
- High production costs and processing difficulties.
- Sensitivity to moisture and environmental degradation.
- Challenges in achieving high density and consistent thermal conductivity.
- Mechanical brittleness and machining difficulties.
- Limited scalability and integration with other materials.
- Lack of long-term performance data and regulatory standardization.
To overcome these challenges, a combination of advanced material synthesis techniques, innovative processing methods, and collaborative research efforts is essential. Solutions such as:
- Developing cost-effective production methods.
- Using sintering aids and protective coatings.
- Optimizing microstructure and grain boundary engineering.
- Exploring composite materials and additive manufacturing.
- Establishing industry standards and reliability testing protocols.
will play a critical role in advancing AlN ceramics.
By addressing these issues, AlN ceramics can be further optimized for emerging technologies like 5G, IoT, and renewable energy, as well as traditional applications in electronics and thermal management. Continued innovation, collaboration, and investment in research will ensure that AlN ceramics remain at the forefront of advanced materials, enabling new possibilities for high-performance applications in the future.