Silicon Carbide (SiC) ceramics are widely used in various industries due to their excellent properties, such as high thermal conductivity, hardness, and chemical resistance. However, there are still several challenges and issues that need to be addressed to further enhance their performance and expand their applications. Below are some of the key issues and potential solutions:
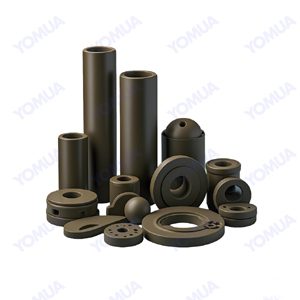
1. High Production Cost
- Issue: The manufacturing process of SiC ceramics is complex and energy-intensive, leading to high production costs.
- Solutions:
- Develop more cost-effective synthesis methods, such as using lower-cost raw materials or optimizing sintering techniques.
- Explore additive manufacturing (3D printing) to reduce material waste and production time.
- Scale up production to achieve economies of scale.
- Develop more cost-effective synthesis methods, such as using lower-cost raw materials or optimizing sintering techniques.
2. Brittleness and Low Fracture Toughness
- Issue: SiC ceramics are inherently brittle, which limits their use in applications requiring high toughness.
- Solutions:
- Introduce reinforcing phases, such as fibers, whiskers, or nanoparticles (e.g., carbon nanotubes or graphene), to improve toughness.
- Develop SiC-based composites, such as SiC-SiC or SiC-metal composites, to enhance fracture resistance.
- Optimize microstructure design to reduce crack propagation.
3. Difficulty in Machining and Shaping
- Issue: SiC ceramics are extremely hard and difficult to machine, making it challenging to produce complex shapes.
- Solutions:
- Use advanced machining techniques, such as laser machining or electrical discharge machining (EDM).
- Employ near-net-shape manufacturing methods, such as gel casting or injection molding, to reduce the need for extensive machining.
- Develop post-sintering machining tools with diamond or cubic boron nitride (CBN) coatings.
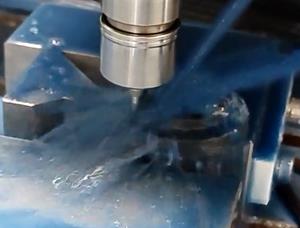
4. Thermal Shock Resistance
- Issue: While SiC has high thermal conductivity, its thermal shock resistance can be limited under rapid temperature changes.
- Solutions:
- Design graded or layered structures to reduce thermal stress.
- Incorporate additives or secondary phases to improve thermal shock resistance.
- Optimize the grain size and porosity of the material to enhance its ability to withstand thermal cycling.
5. Oxidation at High Temperatures
- Issue: SiC ceramics can oxidize at high temperatures, especially in environments containing oxygen or water vapor.
- Solutions:
- Apply protective coatings, such as silicon nitride or alumina, to prevent oxidation.
- Develop self-healing coatings that can repair surface damage during operation.
- Use additives to form a protective oxide layer on the surface.
6. Joining and Integration with Other Materials
- Issue: Joining SiC ceramics to metals or other ceramics is challenging due to differences in thermal expansion coefficients and chemical compatibility.
- Solutions:
- Use advanced joining techniques, such as brazing with active filler metals or diffusion bonding.
- Develop gradient interlayers to reduce thermal stress at the interface.
- Explore adhesive bonding with high-temperature-resistant adhesives.
7. Limited Electrical Conductivity Control
- Issue: SiC ceramics have limited tunability in electrical conductivity, which restricts their use in certain electronic applications.
- Solutions:
- Dope SiC with specific elements (e.g., boron or aluminum) to modify its electrical properties.
- Develop hybrid materials by combining SiC with conductive phases, such as metals or carbon-based materials.
- Optimize the sintering process to control grain boundary conductivity.
8. Environmental and Health Concerns
- Issue: The production and machining of SiC ceramics can generate fine particles, posing health and environmental risks.
- Solutions:
- Implement effective dust collection and filtration systems during manufacturing and machining.
- Develop safer handling protocols and protective equipment for workers.
- Explore eco-friendly production methods to reduce environmental impact.
9. Standardization and Quality Control
- Issue: Lack of standardized testing methods and quality control measures can lead to inconsistent material properties.
- Solutions:
- Establish industry-wide standards for SiC ceramic production and testing.
- Implement advanced quality control techniques, such as non-destructive testing (NDT) and real-time monitoring during manufacturing.
- Collaborate with research institutions and industry stakeholders to develop best practices.
10. Application-Specific Challenges
- Issue: SiC ceramics face unique challenges in specific applications, such as nuclear reactors, aerospace, or electronics.
- Solutions:
- Tailor material properties (e.g., radiation resistance for nuclear applications or thermal management for electronics) through advanced processing techniques.
- Conduct application-specific research to address performance gaps.
- Collaborate with end-users to develop customized solutions.
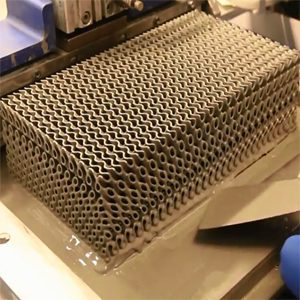
The Summary Table:
Here’s a table summarizing the issues SiC ceramics face and their corresponding solutions:
Issue | Solutions |
---|---|
High Production Cost | – Use cost-effective synthesis methods. – Explore additive manufacturing (3D printing). – Scale up production. |
Brittleness and Low Toughness | – Add reinforcing phases (fibers, whiskers, nanoparticles). – Develop SiC-based composites. – Optimize microstructure design. |
Difficulty in Machining | – Use advanced machining (laser, EDM). – Employ near-net-shape manufacturing. – Use diamond/CBN tools. |
Thermal Shock Resistance | – Design graded/layered structures. – Add secondary phases. – Optimize grain size and porosity. |
Oxidation at High Temperatures | – Apply protective coatings (e.g., silicon nitride, alumina). – Develop self-healing coatings. – Use oxidation-resistant additives. |
Joining with Other Materials | – Use brazing or diffusion bonding. – Develop gradient interlayers. – Explore high-temperature adhesives. |
Limited Electrical Conductivity | – Dope with elements (e.g., boron, aluminum). – Develop hybrid materials. – Optimize sintering for grain boundary control. |
Environmental and Health Risks | – Implement dust collection systems. – Develop safer handling protocols. – Explore eco-friendly production methods. |
Standardization and Quality Control | – Establish industry standards. – Use non-destructive testing (NDT). – Collaborate for best practices. |
Application-Specific Challenges | – Tailor material properties for specific uses. – Conduct application-specific research. – Collaborate with end-users. |
Conclusion:
In conclusion, Silicon Carbide (SiC) ceramics are advanced materials with exceptional properties, such as high thermal conductivity, hardness, and chemical resistance, making them ideal for demanding applications in industries like aerospace, electronics, energy, and nuclear. However, several challenges hinder their broader adoption and performance optimization. These include high production costs, brittleness, machining difficulties, oxidation at high temperatures, and application-specific limitations.
To address these issues, a combination of material innovation, advanced manufacturing techniques, and interdisciplinary research is essential. Solutions such as cost-effective synthesis methods, reinforcement with nanoparticles or fibers, protective coatings, and tailored material designs can significantly enhance the performance and applicability of SiC ceramics. Additionally, standardization, quality control, and eco-friendly production practices will ensure consistent quality and sustainability.
By overcoming these challenges, SiC ceramics can unlock their full potential, enabling their use in even more advanced and demanding applications. Collaboration between researchers, manufacturers, and end-users will be critical to driving innovation and expanding the role of SiC ceramics in cutting-edge technologies.