The performance of alumina ceramics (Al2O3 ceramics) can be improved by adding different additives, which can influence sintering behavior, microstructure, mechanical properties, thermal properties, and electrical properties. Below are common additives and their usage methods:
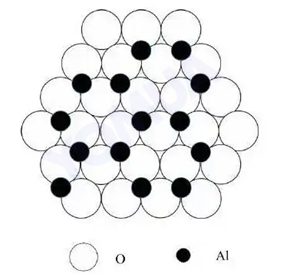
1. Sintering Aids
- Function: Reduce sintering temperature, promote densification, and decrease porosity.
- Common Additives:
- MgO (Magnesium Oxide): Inhibits grain growth and improves densification.
- SiO₂ (Silicon Dioxide): Forms a liquid phase with Al₂O₃ to promote sintering.
- TiO₂ (Titanium Dioxide): Lowers sintering temperature and enhances densification.
- Usage Method:
- Mix the additive in powder form uniformly with alumina powder (typically 0.1%-5% by weight).
- Ensure uniform distribution through ball milling or wet mixing.
- During sintering, the additives promote particle bonding by forming a liquid phase or solid solution.
2. Grain Growth Inhibitors
- Function: Suppress excessive grain growth to improve material strength and toughness.
- Common Additives:
- MgO (Magnesium Oxide): Most commonly used, inhibits grain growth by forming spinel (MgAl₂O₄).
- Y₂O₃ (Yttrium Oxide): Stabilizes grain boundaries at high temperatures.
- Usage Method:
- Typically added in amounts of 0.1%-1%.
- Uniformly mixed with alumina powder before sintering.
3. Toughening Agents
- Function: Enhance fracture toughness and thermal shock resistance of alumina ceramics.
- Common Additives:
- ZrO₂ (Zirconia): Improves toughness through phase transformation toughening.
- SiC (Silicon Carbide): Enhances strength and toughness as a second-phase particle.
- TiC (Titanium Carbide): Increases hardness and wear resistance.
- Usage Method:
- Typically added in amounts of 5%-20%.
- Uniformly dispersed in the matrix through mechanical mixing or chemical methods.
4. Conductive or Insulating Modifiers
- Function: Adjust the electrical properties of alumina ceramics.
- Common Additives:
- TiO₂ (Titanium Dioxide): Increases conductivity.
- SiO₂ (Silicon Dioxide): Enhances insulating properties.
- Usage Method:
- Adjust the amount based on target electrical properties (typically 1%-10%).
- Uniformly mixed and sintered.
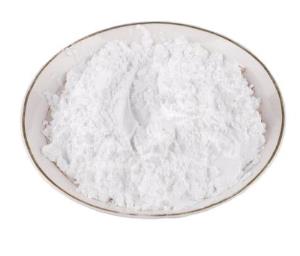
5. Thermal Property Modifiers
- Function: Improve thermal expansion coefficient, thermal conductivity, or thermal shock resistance.
- Common Additives:
- SiC (Silicon Carbide): Increases thermal conductivity.
- ZrO₂ (Zirconia): Reduces thermal expansion coefficient and improves thermal shock resistance.
- Usage Method:
- Adjust the amount based on specific requirements (typically 5%-30%).
- Achieve uniform distribution through mixing and sintering.
6. Color Modifiers
- Function: Change the color of alumina ceramics for decorative or identification purposes.
- Common Additives:
- Cr₂O₃ (Chromium Oxide): Green.
- Fe₂O₃ (Iron Oxide): Red or brown.
- CoO (Cobalt Oxide): Blue.
- Usage Method:
- Typically added in amounts of 0.1%-5%.
- Uniformly mixed and sintered.
7. Summary of Additive Usage Methods
- Powder Mixing:
- Mix additive powders with alumina powder in the desired ratio.
- Use ball milling or wet mixing to ensure uniformity.
- Forming:
- Shape the mixed powder into green bodies through dry pressing, isostatic pressing, or injection molding.
- Sintering:
- Sinter at the appropriate temperature (typically 1500-1700°C), where additives play their roles during sintering.
- Post-Processing:
- Perform grinding, polishing, or surface treatment as needed.
Precautions
- Uniformity: Additives must be uniformly dispersed to avoid uneven properties.
- Dosage: Excessive additives may introduce impurities or negatively affect performance.
- Sintering Process: Different additives may require adjustments to sintering temperature and time.
Summary Table:
Additives and Their Effects on Alumina Ceramics
Additive Type | Common Additives | Function | Usage Method | Typical Amount |
---|---|---|---|---|
Sintering Aids | MgO, SiO₂, TiO₂ | Reduce sintering temperature, promote densification, decrease porosity. | Mix uniformly with alumina powder (ball milling or wet mixing). Sinter to form liquid phase/solution. | 0.1%-5% |
Grain Growth Inhibitors | MgO, Y₂O₃ | Suppress excessive grain growth, improve strength and toughness. | Uniformly mix with alumina powder before sintering. | 0.1%-1% |
Toughening Agents | ZrO₂, SiC, TiC | Enhance fracture toughness and thermal shock resistance. | Disperse uniformly in the matrix (mechanical or chemical methods). | 5%-20% |
Electrical Modifiers | TiO₂ (conductive), SiO₂ (insulating) | Adjust electrical properties (conductivity or insulation). | Mix uniformly and sinter based on target electrical properties. | 1%-10% |
Thermal Modifiers | SiC, ZrO₂ | Improve thermal conductivity, reduce thermal expansion, enhance thermal shock resistance. | Adjust amount based on requirements. Mix and sinter uniformly. | 5%-30% |
Color Modifiers | Cr₂O₃ (green), Fe₂O₃ (red/brown), CoO (blue) | Change ceramic color for decorative or identification purposes. | Mix uniformly and sinter. | 0.1%-5% |
Conclusion
The performance of alumina ceramics (Al₂O₃ ceramics) can be significantly enhanced by incorporating various additives, which influence sintering behavior, microstructure, mechanical properties, thermal properties, and electrical properties. Key takeaways include:
- Sintering Aids like MgO, SiO₂, and TiO₂ reduce sintering temperatures and promote densification, while grain growth inhibitors such as MgO and Y₂O₃ refine the microstructure, improving strength and toughness.
- Toughening Agents like ZrO₂, SiC, and TiC enhance fracture toughness and thermal shock resistance, making the ceramics more durable.
- Electrical Modifiers (e.g., TiO₂ for conductivity, SiO₂ for insulation) and thermal modifiers (e.g., SiC, ZrO₂) allow tailoring of electrical and thermal properties for specific applications.
- Color Modifiers such as Cr₂O₃, Fe₂O₃, and CoO enable customization of ceramic appearance for decorative or functional purposes.
- Uniformity in additive distribution and proper dosage are critical to avoid adverse effects on performance. The sintering process must also be carefully controlled to optimize the effects of additives.
By carefully selecting and applying these additives, alumina ceramics can be engineered to meet the demanding requirements of diverse applications, including electronics, aerospace, automotive, and industrial components. The table above provides a concise summary of the roles, usage methods, and typical amounts of common additives, serving as a practical guide for optimizing alumina ceramic performance.