Silicon Carbide (SiC) vs. Tungsten Carbide (WC) are both exceptional hard materials, but their distinct properties make them suitable for different applications.Let’s delve into a comprehensive comparison of Silicon Carbide (SiC) and Tungsten Carbide (WC), covering composition, crystal structure, properties, applications, cost, manufacturing, future trends, and 3D printing.
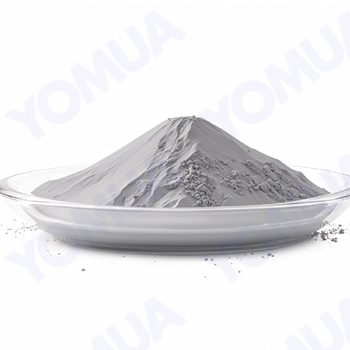
1. Composition
- Silicon Carbide (SiC):
- Composed of silicon (Si) and carbon (C) in a 1:1 ratio.
- Forms a covalent network structure.
- Tungsten Carbide (WC):
- Composed of tungsten (W) and carbon (C) in a 1:1 ratio.
- Typically used as a cemented carbide with a metallic binder (e.g., cobalt).
2. Crystal Structure
- SiC:
- Exists in multiple polytypes, including cubic (3C-SiC), hexagonal (4H-SiC, 6H-SiC), and rhombohedral (15R-SiC).
- The most common form is 6H-SiC (hexagonal).
- WC:
- Has a simple hexagonal crystal structure.
- Often combined with cobalt (Co) to form a composite material (cemented carbide).
3. Properties
Property | Silicon Carbide (SiC) | Tungsten Carbide (WC) |
---|---|---|
Hardness | Extremely hard (Mohs hardness 9~9.5) | Extremely hard (Mohs hardness ~9) |
Density | Lower density (~3.21 g/cm³) | Higher density (~15.6 g/cm³) |
Thermal Conductivity | High (~120-200 W/m·K) | Moderate (~80-100 W/m·K) |
Thermal Stability | Excellent (stable up to ~1600°C in air) | Good (stable up to ~500-600°C in air) |
Electrical Conductivity | Semiconductor (wide bandgap) | Conductive (metallic behavior) |
Oxidation Resistance | Excellent (forms protective SiO₂ layer) | Poor (oxidizes at high temperatures) |
Fracture Toughness | Moderate (~3-4 MPa·m¹/²) | High (~10-15 MPa·m¹/² with Co binder) |
4. Applications
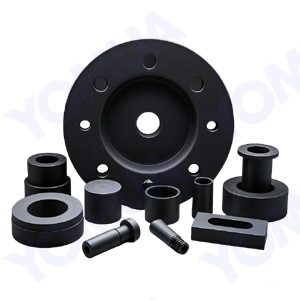
- SiC:
- Electronics: Power devices, LEDs, and sensors due to its wide bandgap.
- Aerospace: High-temperature components and thermal protection systems.
- Automotive: Brake discs, clutches, and engine components.
- Energy: Solar inverters and nuclear reactor components.
- Abrasive Tools: Grinding wheels and cutting tools.
- WC:
- Cutting Tools: Drills, end mills, and inserts for machining.
- Mining and Construction: Wear-resistant parts and drill bits.
- Industrial Machinery: Dies, punches, and wear plates.
- Jewelry: Used in high-end watches and rings for scratch resistance.
5. Cost and Availability
- SiC:
- Higher cost due to complex synthesis and processing.
- Limited availability of high-purity SiC for advanced applications.
- WC:
- Lower cost compared to SiC, but still expensive due to tungsten’s scarcity.
- Widely available as cemented carbide with cobalt binders.
6. Manufacturing Processes
- SiC:
- Synthesis: Acheson process, chemical vapor deposition (CVD), or sintering.
- Machining: Difficult due to hardness; typically requires diamond tools.
- Additive Manufacturing: Emerging techniques like binder jetting and SLA for SiC-based composites.
- WC:
- Synthesis: Powder metallurgy (sintering with cobalt binder).
- Machining: Easier than SiC due to cobalt binder, but still challenging.
- Additive Manufacturing: Binder jetting and selective laser melting (SLM) for WC-Co parts.
7. Future Development and Trends
- SiC:
- Wide-Bandgap Semiconductors: Growth in SiC-based power electronics for electric vehicles (EVs) and renewable energy.
- Thermal Management: Development of SiC composites for high-temperature applications.
- Quantum Technologies: Exploration of SiC for quantum computing and sensing.
- Sustainable Manufacturing: Recycling and reusing SiC waste materials.
- WC:
- Advanced Cutting Tools: Development of nano-grained WC for improved performance.
- Wear-Resistant Coatings: Use of WC in coatings for extreme environments.
- Cobalt-Free Alternatives: Research into alternative binders (e.g., nickel, iron) to reduce reliance on cobalt.
- Additive Manufacturing: Expansion of AM techniques for complex WC-Co parts.
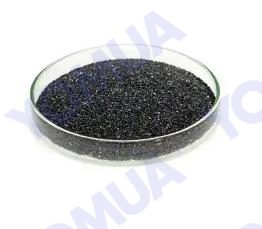
8. Additive Manufacturing (3D Printing) for SiC and WC
- SiC:
- Challenges: High melting point and brittleness make SiC difficult to print directly.
- Opportunities: Use of SiC-polymer composites or preceramic polymers for SLA or binder jetting.
- Applications: Lightweight, high-strength components for aerospace and electronics.
- WC:
- Challenges: High density and hardness require specialized AM techniques.
- Opportunities: Binder jetting and SLM for WC-Co parts with complex geometries.
- Applications: Custom cutting tools, wear-resistant parts, and industrial components.
9. Future Outlook
- SiC:
- Expected to dominate in power electronics, EVs, and renewable energy due to its superior thermal and electrical properties.
- Growth in AM for SiC-based composites and customized components.
- WC:
- Continued dominance in cutting tools and wear-resistant applications.
- Expansion into AM for customized industrial parts and cobalt-free alternatives.
Conclusion
- SiC excels in high-temperature, high-power, and semiconductor applications due to its thermal stability, wide bandgap, and lightweight properties. It is a key material for future technologies like EVs, renewable energy, and quantum computing.
- WC is unmatched in wear resistance and hardness, making it ideal for cutting tools, mining, and industrial applications. Its future lies in advanced AM techniques and cobalt-free alternatives.
Both materials have unique strengths and will continue to play critical roles in their respective domains. The choice between SiC and WC depends on the specific application requirements, such as thermal stability, electrical properties, wear resistance, and cost considerations. Advances in additive manufacturing and sustainable production methods will further enhance their capabilities and expand their applications.