Zirconia (ZrO₂) ceramics, prized for their strength, toughness, and wear resistance, face several challenges hindering their full potential. Here’s a breakdown of thirteen issues and potential solutions.
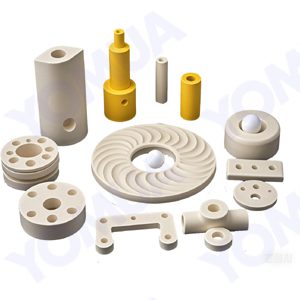
Tthirteen issues and potential solutions
1. Phase Instability & Low-Temperature Degradation (LTD):
- Issue: Zirconia’s phase transformations (tetragonal to monoclinic) can cause cracking and weakening, especially in humid environments (LTD).
- Solution: Stabilizing the tetragonal phase with additives like yttria (Y₂O₃) is common practice (Y-TZP). Further research focuses on optimizing stabilizer content and distribution, along with surface treatments, to combat LTD.
2. Brittleness:
- Issue: Despite high toughness compared to other ceramics, zirconia remains brittle compared to metals.
- Solution: Microstructure optimization (grain size control, etc.) and exploring composite materials (e.g., zirconia with alumina) are key strategies to improve toughness.
3. Thermal Conductivity:
- Issue: Zirconia’s low thermal conductivity limits its use in applications requiring heat dissipation.
- Solution: Developing zirconia-based composites with higher thermal conductivity components is an ongoing research area.
4. Machinability:
- Issue: Zirconia’s hardness makes machining difficult and costly, especially for complex shapes.
- Solution: Advanced techniques like laser machining, ultrasonic machining, and near-net-shape manufacturing (additive manufacturing) are being developed to improve machinability and reduce material waste.
5. Cost:
- Issue: High-quality zirconia powders and processing are expensive.
- Solution: Research into cost-effective production methods and alternative zirconia sources is crucial for wider adoption.
6. Joining:
- Issue: Joining zirconia to other materials is challenging.
- Solution: Developing reliable brazing, adhesive techniques, and mechanical interlocking designs are essential for integration with other components.
7. Property Variability:
- Issue: Properties can vary depending on manufacturing processes and raw materials.
- Solution: Strict quality control and standardized manufacturing are necessary to ensure consistent performance.
8. Environmental Concerns:
- Issue: Zirconia production can have environmental impacts.
- Solution: Sustainable production methods and recycling strategies are crucial for minimizing environmental footprint.
9. Limited Functionality:
- Issue: Basic zirconia may lack specific functionalities for advanced applications.
- Solution: Surface modification and combining zirconia with other materials to create multifunctional composites can expand its applications.
10. Long-Term Reliability:
- Issue: Long-term performance in harsh environments requires further investigation.
- Solution: Extensive testing, field trials, and predictive models are needed to ensure long-term reliability.
11. Sintering and Processing:
- Issue: Achieving high density and uniform microstructure during sintering is challenging, especially for complex shapes.
- Solution: Advanced sintering techniques like spark plasma sintering (SPS) and microwave sintering offer improved density and reduced processing time.
12. Biocompatibility and Medical Applications:
- Issue: While generally biocompatible, long-term performance in medical implants needs further study.
- Solution: Surface modifications and coatings can enhance biointegration and reduce wear in biomedical applications.
13. Wear Resistance:
- Issue: Zirconia can experience wear in certain applications.
- Solution: Surface treatments and coatings can improve wear resistance.
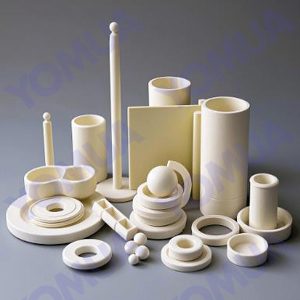
The Summary Table:
Thirteen issues and potential solutions
Issue | Description | Solution(s) |
---|---|---|
Phase Instability/LTD | Phase transformations (tetragonal to monoclinic) cause cracking, especially in humid environments (LTD). | Stabilize tetragonal phase with additives (e.g., Y₂O₃), optimize stabilizer content/distribution, surface treatments. |
Brittleness | Brittle compared to metals, limiting certain applications. | Microstructure optimization (grain size control), composite materials (e.g., ZrO₂/Al₂O₃). |
Thermal Conductivity | Low thermal conductivity restricts use in heat dissipation applications. | Develop ZrO₂-based composites with higher thermal conductivity components. |
Machinability | Hardness makes machining difficult and costly. | Advanced techniques (laser, ultrasonic machining), near-net-shape manufacturing (additive manufacturing). |
Cost | High-quality powders and processing are expensive. | Research cost-effective production methods, explore alternative ZrO₂ sources. |
Joining | Joining to other materials is challenging. | Reliable brazing, adhesive techniques, mechanical interlocking designs. |
Property Variability | Properties vary depending on manufacturing and raw materials. | Strict quality control, standardized manufacturing processes. |
Environmental Concerns | ZrO₂ production can have environmental impacts. | Sustainable production methods, recycling strategies. |
Limited Functionality | Basic ZrO₂ may lack specific functionalities. | Surface modification, multifunctional composites. |
Long-Term Reliability | Performance in harsh environments needs further investigation. | Extensive testing, field trials, predictive models. |
Sintering/Processing | Achieving high density and uniform microstructure is challenging. | Advanced sintering (SPS, microwave sintering). |
Biocompatibility (Medical) | Long-term performance in medical implants requires further study. | Surface modifications, coatings for enhanced biointegration. |
Wear Resistance | Can experience wear in certain applications. | Surface treatments, coatings. |
Addressing these challenges requires a multidisciplinary approach, combining materials science, engineering, and chemistry to optimize zirconia for various applications.
Conclusion:
Zirconia ceramics stand out for their exceptional blend of strength, toughness, and wear resistance, positioning them as promising materials for a broad spectrum of applications. However, their widespread adoption and full utilization are hampered by several inherent limitations. These challenges range from fundamental material properties like phase instability and brittleness to practical considerations such as machinability, cost, and ensuring long-term reliability in diverse environments. Overcoming these hurdles is essential to unlock the true potential of zirconia.
Significant strides have been made in addressing these challenges. Material design strategies, including stabilizing the tetragonal phase with yttria additions and meticulously controlling the microstructure, have yielded substantial improvements in performance. The development of zirconia-based composite materials, combining zirconia with other phases, offers further avenues for tailoring properties and enhancing performance in specific applications. These advancements have broadened the range of potential uses and pushed the boundaries of what zirconia ceramics can achieve.
Beyond material composition, advancements in processing techniques are playing a critical role. Novel sintering methods, like spark plasma sintering and microwave sintering, enable greater control over densification and microstructure development, leading to improved material properties. The emergence of additive manufacturing, or 3D printing, for ceramics offers exciting possibilities for near-net-shape fabrication, reducing machining needs and enabling the production of complex geometries with greater efficiency. These processing innovations are not only enhancing performance but also contributing to cost-effectiveness and scalability.
Despite these advancements, ongoing research and development remain crucial. Focus areas include surface modification techniques to enhance specific functionalities, the development of robust joining methods for integrating zirconia with other materials, and a deeper understanding of long-term behavior in challenging environments. A comprehensive approach that considers both material properties and processing techniques is necessary to fully realize the potential of zirconia ceramics.
In conclusion, while challenges remain, the future of zirconia ceramics is bright. By continuing to address the existing limitations through focused research and development efforts, zirconia ceramics are poised to play an increasingly important role in a wide array of applications. From structural components and cutting tools to advanced thermal management systems and biomedical implants, the versatility and performance of zirconia ceramics position them for continued growth and innovation across diverse industries.