Zirconia (ZrO₂) and magnesia (MgO) ceramics are both advanced ceramic materials with distinct properties, making them suitable for different applications. Here’s a detailed comparison of the two,including Material Properties, Thermal and Mechanical Properties, Applications, Advantages, Disadvantages, Manufacturing, Cost and Availability, Environmental and Health Considerations, and Future Developments:

1. Material Properties:
- Zirconia (ZrO₂):
- High Toughness: Zirconia is known for its exceptional fracture toughness, which is higher than most other ceramics. This is due to its transformation toughening mechanism.
- High Strength: It has high mechanical strength, making it suitable for structural applications.
- Wear Resistance: Zirconia exhibits excellent wear resistance, which is beneficial in applications like cutting tools and bearings.
- Thermal Insulation: It has relatively low thermal conductivity, making it a good thermal insulator.
- Biocompatibility: Zirconia is biocompatible, which makes it suitable for medical applications such as dental implants and prosthetics.
- Chemical Stability: It is chemically inert and resistant to corrosion in many environments.
- Magnesia (MgO):
- High Thermal Conductivity: MgO has higher thermal conductivity compared to zirconia, making it suitable for applications where heat dissipation is important.
- Refractory Properties: Magnesia has excellent refractory properties, with a high melting point (around 2852°C or 5166°F), making it ideal for high-temperature applications.
- Electrical Insulation: MgO is a good electrical insulator, which is useful in electrical and electronic applications.
- Chemical Stability: It is chemically stable in basic environments but can react with acids.
- Lower Toughness: MgO is generally more brittle and has lower fracture toughness compared to zirconia.
2. Applications:
- Zirconia (ZrO₂):
- Dental Implants and Prosthetics: Due to its biocompatibility and strength.
- Cutting Tools: Because of its wear resistance and toughness.
- Oxygen Sensors: Used in automotive and industrial applications due to its ionic conductivity.
- Biomedical Devices: Such as hip joint replacements.
- Thermal Barrier Coatings: In aerospace and gas turbine engines.
- Magnesia (MgO):
- Refractory Materials: Used in furnaces, kilns, and reactors due to its high melting point and thermal stability.
- Electrical Insulators: In electrical heating elements and other high-temperature electrical applications.
- Crucibles and Linings: For melting and processing metals and other materials.
- Chemical Industry: As a basic refractory material in chemical reactors.
3. Thermal and Mechanical Properties:
- Zirconia:
- Thermal Conductivity: Low (around 2-3 W/m·K).
- Fracture Toughness: High (6-15 MPa·m¹/²).
- Hardness: High (around 1200 HV).
- Magnesia:
- Thermal Conductivity: Higher than zirconia (around 30-40 W/m·K).
- Fracture Toughness: Lower than zirconia (around 1-2 MPa·m¹/²).
- Hardness: Lower than zirconia (around 500-600 HV).
4. Cost and Availability:
- Zirconia: Generally more expensive due to its advanced properties and processing requirements.
- Magnesia: Typically less expensive and more readily available, especially for refractory applications.
5. Environmental and Health Considerations:
- Zirconia: Generally considered safe and biocompatible, though the dust from machining can be hazardous if inhaled.
- Magnesia: Also generally safe, but MgO dust can be irritating to the respiratory system and eyes.
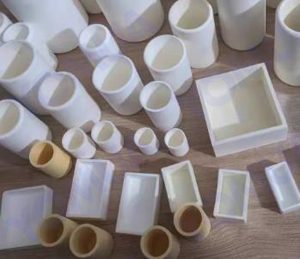
6. Advantages
Zirconia (ZrO₂):
- High Fracture Toughness: Resistant to crack propagation due to transformation toughening.
- High Strength: Suitable for load-bearing and structural applications.
- Wear Resistance: Excellent for high-wear applications like cutting tools and bearings.
- Biocompatibility: Safe for use in medical and dental implants.
- Thermal Insulation: Low thermal conductivity makes it ideal for thermal barrier coatings.
- Aesthetic Appeal: White color and translucency make it suitable for dental crowns and prosthetics.
Magnesia (MgO):
- High Thermal Stability: Ideal for high-temperature applications like furnaces and kilns.
- Thermal Conductivity: Better heat dissipation compared to zirconia.
- Electrical Insulation: Excellent for high-temperature electrical applications.
- Cost-Effective: Generally cheaper than zirconia, especially for large-scale refractory applications.
- Chemical Resistance: Resistant to alkaline environments and molten metals.
7. Disadvantages
Zirconia (ZrO₂):
- Cost: More expensive due to advanced properties and complex manufacturing.
- Low-Temperature Degradation (LTD): Can degrade in the presence of moisture over time.
- Brittleness at High Temperatures: May become brittle under extreme heat.
- Density: Heavier than some other ceramics, limiting use in weight-sensitive applications.
Magnesia (MgO):
- Low Fracture Toughness: More brittle and prone to cracking under mechanical stress.
- Reactivity with Acids: Not suitable for acidic environments.
- Moisture Sensitivity: Absorbs moisture, leading to hydration and degradation.
- Lower Wear Resistance: Not ideal for high-wear applications compared to zirconia.
8. Manufacturing Processes
Zirconia (ZrO₂):
- Powder Preparation: Synthesized from zirconium precursors (e.g., zirconium chloride or zircon sand).
- Shaping: Techniques include dry pressing, injection molding, and slip casting.
- Sintering: Sintered at high temperatures (1400–1600°C) for densification.
- Post-Processing: Machining, polishing, or surface treatments to achieve desired properties.
Magnesia (MgO):
- Powder Synthesis: Derived from magnesium carbonate or magnesium hydroxide through calcination.
- Shaping: Methods include dry pressing, isostatic pressing, and slip casting.
- Sintering: Sintered at very high temperatures (1600–2000°C).
- Post-Processing: Machining or surface treatments, though MgO is difficult to machine due to brittleness.
9. Future Developments
Zirconia (ZrO₂):
- Improved LTD Resistance: Enhancing resistance to low-temperature degradation.
- Nanostructured Zirconia: Using nanotechnology to improve mechanical properties.
- Additive Manufacturing: 3D printing for complex geometries in biomedical and industrial applications.
- Multifunctional Composites: Combining zirconia with other materials (e.g., alumina, graphene) for tailored properties.
Magnesia (MgO):
- Improved Toughness: Developing composites to enhance fracture toughness.
- Moisture Resistance: Coatings or additives to reduce sensitivity to moisture.
- Additive Manufacturing: 3D printing for complex refractory components.
- High-Temperature Applications: Advanced MgO-based composites for extreme environments like aerospace and energy sectors.
10.Comprehensive Table
Comparing Zirconia (ZrO₂) and Magnesia (MgO) Ceramics
Aspect | Zirconia (ZrO₂) | Magnesia (MgO) |
---|---|---|
Material Properties | – High fracture toughness (transformation toughening) – High strength – Wear-resistant – Biocompatible – Chemically stable |
– High thermal stability – High thermal conductivity – Electrical insulator – Chemically stable in alkaline environments |
Thermal and Mechanical Properties | – Thermal conductivity: 2-3 W/m·K – Fracture toughness: 6-15 MPa·m¹/² – Hardness: ~1200 HV – Density: ~6 g/cm³ |
– Thermal conductivity: 30-40 W/m·K – Fracture toughness: 1-2 MPa·m¹/² – Hardness: 500-600 HV – Density: ~3.6 g/cm³ |
Applications | – Dental implants and prosthetics – Cutting tools – Oxygen sensors – Biomedical devices – Thermal barrier coatings |
– Refractory materials (furnaces, kilns) – Electrical insulators – Crucibles and linings – Chemical reactors |
Advantages | – High toughness and strength – Excellent wear resistance – Biocompatible – Thermal insulation – Aesthetic appeal (dental) |
– High thermal stability – Good thermal conductivity – Cost-effective – Electrical insulation – Resistant to molten metals |
Disadvantages | – Expensive – Low-temperature degradation (LTD) – Brittle at high temperatures – Higher density |
– Brittle and low toughness – Reactive with acids – Moisture-sensitive – Lower wear resistance |
Manufacturing | – Powder synthesis from zirconium precursors – Shaping: dry pressing, injection molding, slip casting – Sintering at 1400–1600°C – Post-processing: machining, polishing |
– Powder synthesis from magnesium carbonate/hydroxide – Shaping: dry pressing, isostatic pressing, slip casting – Sintering at 1600–2000°C – Post-processing: machining (difficult due to brittleness) |
Cost and Availability | – Higher cost due to advanced properties and complex manufacturing – Readily available but expensive |
– Lower cost, especially for refractory applications – Widely available and cost-effective |
Environmental and Health Considerations | – Generally safe and biocompatible – Dust from machining can be hazardous if inhaled |
– Generally safe – Dust can irritate respiratory system and eyes – Moisture absorption can lead to degradation |
Future Developments | – Improved LTD resistance – Nanostructured zirconia for enhanced properties – Additive manufacturing (3D printing) – Multifunctional composites (e.g., ZrO₂-Al₂O₃, ZrO₂-graphene) |
– Enhanced toughness through composites (e.g., MgO-Al₂O₃) – Moisture-resistant coatings – Additive manufacturing for complex refractory components – High-temperature composites for aerospace and energy sectors |
Conclusion
- Key Takeaways:
- Zirconia (ZrO₂): Best suited for applications requiring high toughness, wear resistance, and biocompatibility, such as biomedical devices, cutting tools, and dental implants. Its future lies in additive manufacturing and nanostructured composites.
- Magnesia (MgO): Ideal for high-temperature, electrical insulation, and refractory applications due to its thermal stability and cost-effectiveness. Future advancements focus on improving toughness and moisture resistance.
Conclusion:
The choice between ZrO₂ and MgO depends on the specific application requirements, such as mechanical strength, thermal properties, and environmental conditions. Both materials are evolving with advancements in composite technology and additive manufacturing, expanding their potential in industries like aerospace, energy, healthcare, and electronics.