While advanced ceramics offer a unique combination of properties, they aren’t always the best or only choice. Here are some materials that can replace advanced ceramics in certain applications, along with the reasons why they might be considered:
1. Metals and Alloys:
-
- Examples: Stainless steel, aluminum, titanium alloys
- Applications: Structural components, heat sinks, where toughness is critical
- Why they might replace ceramics: Metals generally have higher toughness and ductility, making them less brittle than ceramics. They often have good thermal conductivity and can be easier to machine.
- Limitations: Metals may not withstand high temperatures or corrosive environments as well as ceramics. They can also be heavier.
2. Polymers (Plastics):
- Why they might replace ceramics: Polymers are lightweight, can be easily molded into complex shapes, and often have good chemical resistance.
- Examples: High-performance polymers like PEEK, PTFE, polyimides
- Applications: Seals, gaskets, electrical insulation, where flexibility and ease of processing are important
- Limitations: Polymers typically have lower strength, hardness, and temperature resistance compared to ceramics.
3. Composites:
-
- Examples: Carbon fiber reinforced polymers (CFRP), ceramic matrix composites (CMCs)
- Applications: Aerospace, automotive, where high strength-to-weight ratio and toughness are needed
- Why they might replace ceramics: Composites combine the desirable properties of two or more materials, potentially overcoming some limitations of ceramics.
- Limitations: Composites can be more expensive and complex to manufacture than ceramics.
4. Glass and Glass-Ceramics:
-
- Examples: Fused silica, machinable glass-ceramics (like Macor)
- Applications: Optics, high-temperature windows, electrical insulators
- Why they might replace ceramics: Glass and glass-ceramics offer a balance of properties, including good thermal stability, chemical resistance, and can be optically transparent.
- Limitations: Glass and glass-ceramics can be brittle and may not have the same high-temperature strength as some advanced ceramics.
5. Refractories:
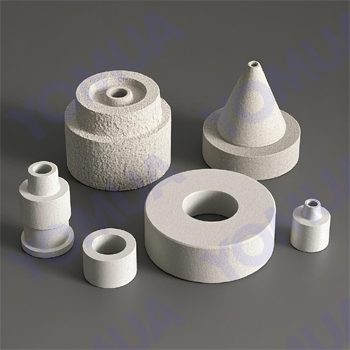
-
- Examples: Firebrick, alumina-silicate materials
- Applications: Furnace linings, kilns, where extreme temperature resistance is paramount
- Why they might replace ceramics: Refractories are designed to withstand extremely high temperatures and harsh environments.
- Limitations: Refractories may not have the same combination of properties (like wear resistance or electrical insulation) as some advanced ceramics.
here’s a table summarizing the materials that can replace advanced ceramics in certain applications, along with their key properties and limitations:
Material Category | Specific Examples | Key Properties | Limitations | Typical Applications Where They Might Replace Ceramics |
---|---|---|---|---|
Metals & Alloys | Stainless Steel, Aluminum, Titanium Alloys | High toughness, ductility, good thermal conductivity (often), relatively easy to machine | Lower high-temperature strength, may not be as chemically resistant, can be heavier | Structural components, heat sinks, where toughness and ease of fabrication are critical |
Polymers (Plastics) | PEEK, PTFE, Polyimides, High-Performance Thermoplastics | Lightweight, easily molded, good chemical resistance (some) | Lower strength, hardness, and temperature resistance compared to ceramics | Seals, gaskets, electrical insulation, where flexibility and ease of processing are important |
Composites | Carbon Fiber Reinforced Polymers (CFRP), Ceramic Matrix Composites (CMCs) | High strength-to-weight ratio, tailored properties | Can be more expensive and complex to manufacture | Aerospace, automotive, where high performance and specific property combinations are needed |
Glass & Glass-Ceramics | Fused Silica, Macor (Machinable Glass-Ceramic) | Good thermal stability, chemical resistance, can be optically transparent | Brittle, may not have the same high-temperature strength as some advanced ceramics | Optics, high-temperature windows, electrical insulators, where transparency or specific thermal properties are important |
Refractories | Firebrick, Alumina-Silicate Materials | Withstand extremely high temperatures and harsh environments | May not have the same combination of other properties (e.g., wear resistance, electrical insulation) as advanced ceramics | Furnace linings, kilns, where extreme temperature resistance is paramount |
Conclusion:
Factors to Consider When Choosing a Replacement:
- Application requirements: What are the critical properties needed (strength, temperature resistance, wear resistance, etc.)?
- Cost: How much does the material cost, and what are the manufacturing costs?
- Performance: How will the material perform in the intended application?
- Availability: Is the material readily available in the required form and quantity?
- Machinability: Can the material be easily shaped and machined?
It’s important to carefully evaluate the specific needs of the application and consider the trade-offs between different materials before making a decision. Sometimes, a combination of materials or a hybrid approach might be the best solution.