Advanced ceramics and metal alloys are both classes of high-performance materials with unique properties that make them suitable for demanding applications. However, they exhibit significant differences in their characteristics and applications.
Composition:
- Advanced Ceramics: Inorganic, non-metallic materials composed of elements such as silicon, aluminum, oxygen, nitrogen, and carbon. Examples include alumina (Al₂O₃), zirconia (ZrO₂), silicon carbide (SiC), silicon nitride (Si₃N₄), and boron nitride (BN).
- Metal Alloys: Combinations of two or more metallic elements, often with minor additions of other elements to enhance specific properties. Examples include steel (iron and carbon), aluminum alloys, titanium alloys, and nickel-based superalloys.
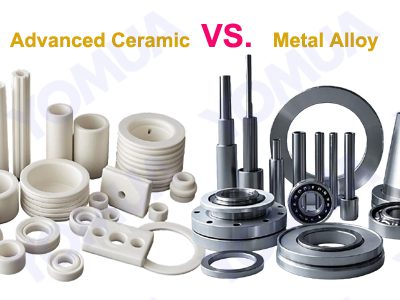
Key Properties:
-
Density:measured by Young’s modulus, represents a material’s resistance to elastic deformation under stress.
- Ceramics: due to their atomic structures, generally exhibit lower densities compared to most metals. This lower density can be advantageous in applications where weight reduction is critical, such as in aerospace and automotive industries.
- Metals Alloys: exhibit a wide range of densities depending on their composition. Some alloys, such as aluminum alloys, are relatively lightweight, while others, such as steel and many high-performance alloys, are denser.
-
Stiffness:measured by Young’s modulus, represents a material’s resistance to elastic deformation under stress.
- Ceramics: owing to their strong atomic bonds, exhibit exceptionally high stiffness. This rigidity is critical in applications demanding dimensional stability and resistance to deflection, such as precision engineering and aerospace components.
- Metals Alloys: such as steel, also exhibit high stiffness, they generally fall short of the stiffness levels attainable with advanced ceramics.
-
Strength:
- Ceramics: excel in compressive strength, demonstrating a remarkable ability to withstand significant forces pushing them together. However, their inherent brittleness limits their tensile strength and ductility.
- Metals Alloys: particularly those designed for structural applications, exhibit excellent tensile strength, allowing them to withstand significant pulling forces without fracturing. This ductility, the ability to deform without failing, is a crucial advantage of metals in applications where components are subjected to tensile stresses.
-
Hardness:
- Ceramics: due to their strong, rigid, and tightly bonded atomic structures, generally possess significantly higher hardness than most metals. This translates to superior resistance to scratching, indentation, and abrasion.
- Metals Alloys: such as high-strength steels, can achieve impressive hardness levels, they typically do not surpass the exceptional hardness of ceramics like alumina or silicon carbide.
-
Thermal Conductivity:
- Ceramics: Thermal conductivity varies significantly among ceramics. Some, like alumina and zirconia, exhibit moderate thermal conductivity. Others, like silicon carbide, demonstrate high thermal conductivity.
- Metals Alloys: Metals, in general, are excellent thermal conductors due to the presence of free electrons that readily transport heat energy. This property is crucial in applications requiring efficient heat dissipation, such as heat sinks and engine components.
Thermal Expansion:
- Ceramics: Many advanced ceramics exhibit low coefficients of thermal expansion. This means they undergo minimal dimensional changes with fluctuations in temperature. This property is critical in applications where dimensional stability is paramount, such as in precision instruments and high-temperature environments.
- Metals Alloys: The thermal expansion behavior of metal alloys varies significantly depending on their composition. Some alloys, such as stainless steel, exhibit relatively low thermal expansion, while others may undergo considerable dimensional changes with temperature fluctuations.
Corrosion Resistance:
- Ceramics: Many advanced ceramics exhibit excellent corrosion resistance, resisting attack from acids, bases, and other corrosive chemicals. This makes them suitable for applications in harsh environments, such as chemical processing plants and marine environments.
- Metals Alloys: The corrosion resistance of metal alloys varies widely depending on the specific alloy composition and the environment. Stainless steels, for example, are renowned for their corrosion resistance due to the presence of chromium, which forms a protective oxide layer. Other alloys may require protective coatings to enhance their corrosion resistance.
High-Temperature Stability:
- Ceramics: Advanced ceramics, due to their strong chemical bonds and high melting points, typically exhibit superior high-temperature stability and oxidation resistance compared to many metals. This makes them ideal for applications in extreme environments, such as in aerospace and high-temperature industrial processes.
- Metal Alloys: While some metal alloys, such as superalloys (nickel-based alloys), exhibit excellent high-temperature strength and creep resistance, they may not match the overall high-temperature stability and oxidation resistance of advanced ceramics.
Electrical Conductivity:
- Ceramics: Advanced ceramics are generally good electrical insulators, meaning they have very low electrical conductivity. This property is crucial in applications where electrical insulation is required, such as in electrical components and high-voltage equipment.
- Metals: Metals are excellent conductors of electricity due to the presence of free electrons. This property is fundamental to their use in electrical wiring, electronics, and many other applications.
Key Properties:
Property | Advanced Ceramics | Metal Alloys |
---|---|---|
Hardness | Generally higher | Generally lower, but can be very high in some cases (e.g., high-strength steels) |
Strength | High compressive strength, but often brittle | High tensile strength and ductility in many cases |
Stiffness | High stiffness (Young’s modulus) | High stiffness in some cases (e.g., steel), but generally lower than some ceramics |
Density | Generally lower density than metals | Can vary widely depending on the alloy composition |
Thermal Conductivity | Can vary widely, but often lower than metals | Generally high thermal conductivity |
Thermal Expansion | Low thermal expansion coefficients in many cases | Can vary significantly depending on the alloy |
Corrosion Resistance | Excellent corrosion resistance in many environments | Corrosion resistance varies widely depending on the alloy composition (e.g., stainless steel, titanium alloys) |
High-Temperature Stability | Superior high-temperature stability and oxidation resistance | High-temperature strength and creep resistance can be achieved in some alloys (e.g., superalloys) |
Electrical Conductivity | Generally good electrical insulators | Excellent electrical and thermal conductivity in many metals |
Processing & Fabrication:
-
Advanced Ceramics:
-
Challenges:
- Brittleness: The inherent brittleness of ceramics makes them challenging to shape and machine. Traditional metalworking techniques like machining and forging are often unsuitable.
- High Processing Temperatures: Many ceramic processing techniques involve high temperatures (e.g., sintering), requiring specialized equipment and energy.
- Complex Microstructures: Achieving the desired microstructure (grain size, porosity, etc.) often requires precise control of processing parameters, which can be complex to achieve.
-
Common Processing Techniques:
- Powder Metallurgy: Involves shaping ceramic powders into the desired form (e.g., pressing, slip casting, extrusion) followed by high-temperature sintering.
- Chemical Vapor Deposition (CVD): Used to deposit thin ceramic films or coatings.
- Physical Vapor Deposition (PVD): Techniques like sputtering and evaporation are used to deposit thin ceramic films.
- Spark Plasma Sintering (SPS): A relatively new technique that uses pulsed electric current to rapidly heat and densify ceramic powders.
Metal Alloys:
-
Advantages:
- Versatility: Metals are generally more amenable to a wider range of processing techniques, such as:
- Casting: Molten metal is poured into molds to create complex shapes.
- Forging: Shaping metal by hammering or pressing.
- Machining: Using tools to remove material and create precise shapes.
- Welding: Joining metal parts together.
- Additive Manufacturing (3D Printing): Building parts layer by layer from a digital design.
- Established Technologies: Many metal processing techniques are well-established and cost-effective.
- Versatility: Metals are generally more amenable to a wider range of processing techniques, such as:
-
Challenges:
- High-performance alloys: Some alloys, such as superalloys, may require specialized processing techniques and equipment.
-
Applications:
- Advanced Ceramics:
- Aerospace (thermal protection, engine components)
- Automotive (engine components, wear-resistant parts)
- Electronics (substrates, sensors)
- Medical implants (dental implants, bone replacements)
- Cutting tools and abrasives
- Chemical processing equipment
- Metal Alloys:
- Aerospace (aircraft structures, engine components)
- Automotive (body panels, engine blocks, transmission components)
- Construction (steel structures, bridges)
- Medical implants (surgical instruments, orthopedic implants)
- Energy generation (turbine blades, nuclear reactors)
Cost Comparison:
- Ceramics:
- Generally more expensive: Production processes for advanced ceramics are often more complex and energy-intensive than those for many metals.
- Raw material costs: Some ceramic raw materials can be relatively expensive.
- Processing challenges: The brittleness of ceramics necessitates specialized processing techniques and tooling, increasing manufacturing costs.
- Metals:
- Often more cost-effective: Many metals and their alloys are readily available and can be processed using well-established, relatively inexpensive techniques.
- Exceptions: Some high-performance alloys (e.g., titanium alloys, superalloys) can be quite expensive to produce and process.
Future Development:
-
Advanced Ceramics:
- Focus on improving processability: Research is ongoing to develop more cost-effective and efficient manufacturing techniques for ceramics, such as advanced sintering methods (e.g., microwave sintering, spark plasma sintering) and novel forming techniques.
- Developing new ceramic composites: Combining ceramics with other materials (e.g., ceramic matrix composites, ceramic-metal composites) can enhance toughness and tailor properties for specific applications.
- Exploring new applications: Research is expanding into areas like bioceramics, energy storage, and advanced electronics, where the unique properties of ceramics offer significant advantages.
-
Metal Alloys:
- Development of high-performance alloys: Ongoing research focuses on developing alloys with improved strength-to-weight ratios, enhanced corrosion resistance, and better high-temperature performance.
- Additive manufacturing (3D printing): This technology is revolutionizing metal processing, enabling the production of complex shapes with improved properties and reduced material waste.
- Advanced surface treatments: Techniques like thermal spraying, laser cladding, and ion implantation are being used to enhance the surface properties of metal alloys, improving wear resistance, corrosion resistance, and fatigue life.
Conclusion
In conclusion, advanced ceramics and metal alloys offer distinct advantages and disadvantages. The choice of material depends heavily on the specific application requirements, including performance needs (strength, hardness, corrosion resistance, etc.), cost considerations, and processing limitations.